फाऊंड्री में लोह द्रव में कितना प्रतिशत कार्बन है यह मापने के लिए एक विशेष रसायन का इस्तेमाल किया जाता है। यह रसायन काफी महँगा होता है लेकिन यह कम मात्रा में लगता है। इस रसायन को एक तापमान प्रतिरोधक (रिफ्रैक्टरी) सीमेंट में मिला कर (शेल मोल्डिंग प्रक्रिया से तैयार किए गए) एक कप के तले (बॉटम) रखा जाता है। इस लेख में आपको यह प्रक्रिया का स्वचालन कैसे किया इसकी जानकारी मिलेगी।
पुरानी पद्धति
हमारे ग्राहक की पुरानी पद्धति में सीमेंट और रसायन का मिश्रण तैयार किया जाता था। इस मिश्रण को कप के तले में एक छोटे चम्मच (लगभग 1.7 ग्राम) की मात्रा में लगाया जाता था। अपितु इसमें कठिनाइयों का सामना करना पड़ता था।
प्रक्रिया में आने वाली कठिनाइयाँ
• रसायन लेने की मात्रा पर बिल्कुल नियंत्रण नहीं था।
• प्रक्रिया में अधिक समय लगने से सीमेंट धीरे धीरे कड़ा हो जाता था।
• कड़ा हुआ मिश्रण फेंकना पड़ता था।
• कप के तले में मिश्रण पूरी तरह फैलता नहीं था। जिससे कप की गुणवत्ता नहीं मिलती थी।
• उत्पादकता नहीं मिलती थी।
• कंपनी निर्धारित समय पर माँग पूरी नहीं कर पाती थी।
इस समस्या से छुटकारा पाने के लिए हमने नई तकनीक ढूँढ़ निकाली। यह तय किया गया कि चालू प्रक्रिया में सुधार करने के लिए कौन से घटकों पर काम करना चाहिए
• कप हैंडलिंग - निरंतरता और लगने वाला समय
• अचूक वजन का मिश्रण छोड़ना
• कप के तले में हर जगह पर मिश्रण फैलना
उपरोक्त घटकों में अपेक्षित परिवर्तन करने वाली नई पद्धति लागू की गई है।
नई पद्धति
सब से पहले कप हैंडलिंग के लिए एक कन्वेअर तैयार किरा गरा। शेल मोल्डिंग प्रक्रिया से बाहर आने पर कप की फ्लैश रिमूविंग (कप के बाहर का अतिरिक्त भाग निकालना) प्रक्रिया की जाती है। इसके बाद कप कन्वेअर पर रखे जाते हैं। उत्पादन को बेहतर बनाने के लिए हमने चार स्टेशन वाली (दो बाएं ओर एवं दो दाएं ओर) डिस्पेन्सिंग मशीन का निर्माण किया। चार स्टेशन बनाने के बाद एक ही समय पर एक साथ चार कप में मिश्रण ड़ालने की व्यवस्था की। इसलिए दो तरफ दो अलग कन्वेअर बिठाए गए। यहाँ दोनों तरफ ऑपरेटर की जरूरत पड़ती है। शेल मोल्डिंग में एक समर में एक साथ 64 कप बाहर आते हैं। उसमें से 32 कप की फ्लैश रिमूविंग कर के एक ऑपरेटर उन्हें कन्वेअर पर रखता है। दूसरे ऑपरेटर की भी रही प्रक्रिरा शुरू रहती है। कन्वेअर में से एक के बाद एक कप आते हैं। कोटिंग स्टेशन के पास ‘सिंगलिंग’ रुनिट लगाया है। इस रुनिट में रे कप अलग अलग किए जाते हैं, और एक कतार में आगे छोड़े जाते हैं। ऐसे चार युनिट उस स्टेशन पर होते हैं। हर कप में 1.7 ग्राम मिश्रण ड़ालना जरूरी होता है। कप का वजन करने के लिए लोड सेल का इस्तेमाल किया गया है।
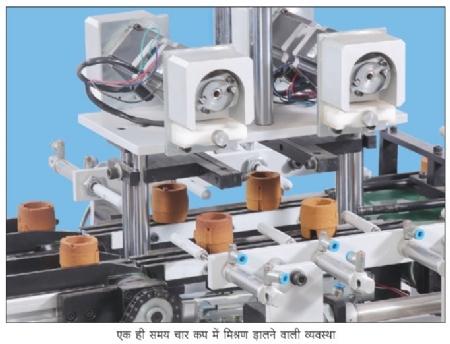
कप बारी बारी से मापन प्रणाली में लाने का यांत्रिक प्रबंध किया गया। इसके लिए न्रुमैटिक पुशर का इस्तेमाल किरा गया। लोड सेल पर आने के बाद स्वचालित प्रणाली से कप का वजन शून्य किया जाता है रानि लोड सेल से मिलने वाला मूल्य शून्य किया जाता है। यह संकेत (सिग्नल) इलेक्ट्रॉनिक कंट्रोलर के पास आने पर, कंट्रोलर पंप को ऐक्टिवेट करता है। इसलिए हमने नॉन कॉन्टैक्ट प्रकार के पेरिस्टाल्टिक पंप विकसित किए। रह पंप स्टेपर मोटर से ड्राईव होने के कारण से इसका नियंत्रण अपने हाथ में होता है। लोड सेल से संकेत प्राप्त करने के बाद पेरिस्टाल्टिक पंप शुरू किया जाता है। जैसे जैसे पेरिस्टाल्टिक पंप कप में मटिरिअल ड़ालता है, वैसे वैसे लोड सेल की तरफ से संकेत मिलते हैं, और 1.7 ग्राम मिश्रण आने पर पंप रोक दिरा जाता है। कंट्रोलर से संकेत मिलते ही पंप रोकने के बाद भी रदि वजन में कुछ वृद्धि हुई, तो अगली प्रक्रिया में स्टेपर मोटर के उतने स्टेप कम किए जाते हैं। इस प्रक्रिरा से औसत अचूकता अच्छी मिलने लगती है। एक साथ चार कप भरने के कारन सीमेंट का मिश्रण कड़ा होने से पहले ही सीमेंट का वह बैच खत्म हो जाता है और एक नया बैच गिराया जा सकता है। ऐसा करने से सीमेंट कड़ा होने से जो बर्बादी होती थी उसमें कमी आई। लोड सेल से बाहर निकलने वाले कप फिर से एक आऊटपुट कन्वेअर पर लाए जाते हैं। बाहर जाने वाले कन्वेअर पर हमने एक एयर नोजल बिठाया। जिस समय कप उसके नीचे से गुजरता है, उसी समर वायु के दबाव से कप में रसायन फैलाने की प्रक्रिरा शुरू होती है। इससे कप के तले में अपेक्षित पतली परत मिलने लगी। स्वचालन पूरा करने के बाद यह देखा गया कि सिर्फ दो ऑपरेटरों से लगभग चार गुना उत्पादन मिल सकता है। इस तरह स्वचालन के लिए किए खर्चे का प्रतिफल एक साल के पहले आना शुरू हो गया।
फायदे
• सीमेंट और रसायन की बर्बादी की मात्रा पहले से 10% कम हुई।
• कप का रिजेक्शन 4% से घट कर 1% से भी कम हो गया।
• ग्राहक की माँग सही समय पर पूरी होने से अधिक काम मिलने लगा।
• दो ऑपरेटर से होनेवाला उत्पादन चार गुना बढ़ गया।
प्रसन्न अक्कलकोटकरजी यांत्रिक अभियंता हैं। आपको स्वचालन क्षेत्र का 25 साल से अधिक अनुभव है।