मिलिंग की सहायता से किसी भी आकार की कार्यवस्तु तैयार की जा सकती है। इसी के कारण यंत्रण की सभी प्रक्रियाओं में सबसे अधिक उपयुक्त प्रक्रिया मिलिंग होती है। टर्निंग की तुलना में मिलिंग प्रक्रिया की सफलता विभिन्न घटकों पर निर्भर करती है। यह घटक एक दूसरे पर प्रभाव ड़ालते हैं इसलिए मिलिंग की प्रक्रिया थोड़ी सी जटिल होती है।
मिलिंग में बार बार उपयोग की जानेवाली संज्ञाएँ (टर्मिनॉलॉजी)
मिलिंग मूलतः खंडित चक्रीय (साइक्लिक) प्रक्रिया है। मिलिंग करते समय एक से अधिक कटिंग एज कार्यवस्तु के संपर्क में आते हैं, जब कि टर्निंग करते समय एक ही एज कार्यवस्तु के संपर्क में आती है। इसलिए मिलिंग संबंधी कुछ प्राथमिक बातें ठीक से समझना जरूरी है।
मिलिंग की संज्ञाएँ
• Vc : कटाव की गति (कटिंग स्पीड) - मी/मिनट
• N : RPM - प्रति मिनट फेरे
N = Vc X 1000 / (Dc X π)
• Dc : कटर का व्यास - मिमी.
• Fz : सरकने की गति (फीड) - मिमी./दाँत (टूथ)
• Vf : सरकने की गति (फीड) - मिमी./मिनट
• Ae : प्रतिशत संपर्क कमान (पर्सेन्टेज आर्क ऑफ एंगेजमेंट)-मिमी.
• Ap : काट की गहराई - मिमी.
कटिंग टूल के उत्पादक कार्यवस्तु के मटिरिअल के अनुसार मिलिंग कटर के बारे में मार्गदर्शक सूचनाएँ देते हैं, लेकिन मिलिंग करते समय वास्तविक रूप से जो विभिन्न समस्याएँ आती हैं उन के बारे में कोई निर्देश नहीं मिलते हैं। इसलिए मिलिंग करते समय दिए हुए कटर की सूचनाओं के बारे में पहले जानकारी लेकर, कार्यवस्तु के अनुरूप, बदलाव लाने पड़ते हैं। यह करते समय टूल उत्पादक को बुला कर, आई हुई समस्याएँ दूर करने के लिए, उन की मदद ली जाती है। फिर भी समस्या दूर नहीं हुई तो दूसरे उत्पादक को बुलाना पड़ता है। दोनों उत्पादकों में से जिसका उत्पादन योग्य होता है उसका चयन किया जाता है। इसमें समय और धन दोनों का अपव्यय होता है। यहाँ ऑप्टिमाइजेशन (इष्टतमीकरण) का उपयोग होता है।
उदाहरण के लिए अगर कार्यवस्तु की खोखली जगह (कैविटी) में मिलिंग करनी हो तो इसके लिए, कटर उत्पादक के कैटलॉग के अनुसार, कटर का चयन किया जाता है। उस में दिए हुए निर्देशों के अनुसार सारे मापदंड़ (पैरामीटर) निर्धारित किए जाते हैं। फिर भी कभी कभी अपेक्षित परिणाम नहीं मिलते हैं। ऐसे समय में खोखले स्थान की ज्यामिति का बार बार अध्ययन कर के टूल के मार्ग में सुधार लाने पड़ते हैं। कटर अधिक समय तक टिकने केलिए कोने के काट के साथ ही इंटरपोलेशन समीकरण बदलने हेतु प्रोग्राम में योग्य बदलाव लाने पड़ते हैं।
आजकल मिलिंग करने के लिए मुख्यत: मशीनिंग सेंटर का प्रयोग किया जाता है। मशीनिंग सेंटर में किए जाने वाले अत्याधुनिक मिलिंग तांत्रिकी का प्रयोग करते समय, जिन घटकों का परिणाम होता है उस की जानकारी प्रस्तुत लेख में दी गई है। टूल उत्पादक ने दी हुई मार्गदर्शक सूचनाएँ और इन घटकों के मेल से मिलिंग प्रक्रिया अधिक लाभदायक होती है। उत्पादकता और टूल की आरु बढ़कर संपूर्ण मिलिंग प्रक्रिया भी सुरक्षित तरीके से शुरू रहती है।
अधिकांश उत्पादकों को उन के उत्पादन से संबंधित मिलिंग के सभी घटकों की गहराई से जानकारी लेने मे दिलचस्पी होती है। क्योंकि यह घटक मिलिंग प्रक्रिरा पर प्रभाव ड़ालते हैं। जैसे कि कार्यवस्तु की विशिष्टताएँ, इन्सर्ट का आकार और ऐप्रोच ऐैंगल, मिलिंग टूल के इष्टतम मार्ग के लिए सर्वोत्तम प्रोग्रामिंग आदि।
मिलिंग प्रक्रिया सुधारने के लिए घटकों का ऑप्टिमाइजेशन
किसी भी प्रक्रिया का ऑप्टिमाइजेशन करने के लिए शून्य से प्रारंभ करना बेहतर होता है। नई कार्यवस्तु पर काम करने के लिए उस प्रक्रिया का फिर से पुनर्गठन (रीइंजिनिअरिंग) करना कालापव्यय होता है। इसलिए पूरी प्रक्रिया समझ लेने के बाद ही उसमें स्थित घटकों का सर्वोत्तम उपयोग मिलिंग प्रक्रिया में करने का विचार किरा जा सकता है। साथ में अब हम देखेंगे कि उपर दिए गए घटकों का अधिकतम उपयोग किस तरह कर सकते हैं और प्रक्रिया किस तरह अधिक लाभदायक हो सकती है।
1. मिलिंग करने की कार्यवस्तु की विशिष्टता को समझकर कटर का स्थान (पोजिशन) और उसके मार्ग (पाथ) का उचित चयन।
2. कार्यवस्तु, उसका मटिरिअल और मशीनिंग सेंटर ध्यान में लेते हुए सर्वोत्तम विधि एवं प्रोग्रामिंग।
3. उत्पादकता बढ़ाने के लिए ऐप्रोच ऐैंगल और चिप की मोटाई की आपसी संबद्धता का लाभ उठाकर वृद्धिंगत सरकती गति।
4. प्रभावी व्यास (इफेक्टिव डाइमीटर) संकल्पना का इस्तेमाल कर के बॉल नोज, और टोरॉईड कटर (केंद्रस्थान में एक दूसरे पर कटिंग एज आच्छादित होनेवाले कटर) की सहायता से किया हुआ प्रोफाइल मिलिंग।
5. खोखलों की मिलिंग करते समय उच्च अक्षीय गहराई (हाइ ऐक्सिअल डेप्थ) और कम त्रिज्यीय कटाई (रेडिअल कट) का प्रयोग किया हुआ प्रोग्रामिंग।
उपरी 5 मुद्दों में से पहले 3 मुद्दे ठीक से समझकर उपयोग में लाने से होने वाले लाभों के बारे में आप लेख में आगे पढ़ सकते हैं। ये सारे परिणाम वस्तुत: प्रयोग करने के बाद प्राप्त हुए हैं।
1) मिलिंग साइकिल पर कटर पोजिशनिंग का प्रभाव
गिअर बॉक्स का यंत्रण करते समय कटर का स्थान तथा संपर्क किस तरह प्रभाव ड़ालते हैं यह बात उदाहरण के द्वारा प्रस्तुत की गई है। (कटर व्यास :125 मिमी.)
पुरानी रीती
जैसे कि चित्र क्र. 1 में दिखाया गया है 125 मिमी. व्यास का कटर, एक पास में, 68 मिमी. चौड़ाई के पूर्ण पृष्ठभाग का मिलिंग करता है। इस रीति में, कार्यवस्तु के आकार के कारण, कटिंग करते समय इन्सर्ट पर झटके लगने से इन्सर्ट बार बार टूट रहे थे। साथ में सम्पर्क कमान ज्यादा होने के कारण इन्सर्ट रगड़े जा रहे थे, जिस से घर्षण बढ़ता था।
नई रीती
जैसे कि चित्र क्र. 2 में दिखाया गया है, कटर एक पास में 36 मिमी. चौड़ाई के पृष्ठभाग का मिलिंग करता है और बचे हुए हिस्से के लिए दूसरा पास देने की व्यवस्था की गई है। इससे कटर को लगने वाले झटके कम हो गए और सम्पर्क कमान भी कम हो जाने से अधिक फीड का प्रयोग हो सका। इससे कुल प्रक्रिया को कम समय लगा और इन्सर्ट की आरु बढ़ गई। कटर का स्थान और संपर्क निश्चित करते समय टूल का मार्ग उचित रखना महत्वपूर्ण होता है। इस जगह डाउन मिलिंग उपयुक्त साबित होता है।
अप मिलिंग और डाउन मिलिंग
सामान्यत: उत्पादक अप मिलिंग करने के बजार डाउन मिलिंग करना पसंद करते हैं। डाउन मिलिंग में कटर कार्यवस्तु में प्रवेश करते समय चिप की मोटाई सर्वाधिक होती है जो, कट पूरा होते समय, कम होते जाती है। इसके कारण अच्छे दर्जे की कटाई होती है। इसके विपरीत अप मिलिंग करते समय, कटर जब कार्यवस्तु में प्रवेश करता है तब चिप की मोटाई सबसे कम अर्थात शून्य होती है और कटाई पूरी होते वक्त वह बढ़ जाती है। इससे कटिंग एज घिस जाती है और इसके कारण कटाई का दर्जा घट जाता है।
अप मिलिंग में होनेवाली रगड़ की प्रक्रिया के कारण जरूरत से ज्यादा उष्मा निर्माण हो कर टूल की आरु कम हो जाती है। साथ ही अक्षीय बल (ऐक्सिअल फोर्स) की ज्यादा आवश्यकता होती है। (चित्र क्र. 3)
मिलिंग एक चक्रीय प्रक्रिया होने के कारण कटिंग एज बार बार कार्यवस्तु में घुसती और बाहर निकलती है। कार्यवस्तु में कटर त्रिज्यीय दिशा में खिसकता/चक्कर लगाता है तब चिप की मोटाई सदा बदलती रहती है। कटर की कार्यवस्तु में प्रवेश करने की जगह और दिशा के अनुसार मिलिंग प्रक्रिया का कटिंग एज पर होनेवाला असर तीन बातों पर निर्भर करता है
1.1) काट लेने के लिए किया हुआ प्रवेश
मिलिंग प्रक्रिया के तीन भागों में से यह सब से कम संवेदनशील (सेन्सेटिव) होता है। प्रवेश करते समय होनेवाले आघातों के कारण उत्पन्न होने वाले कम्प्रेसिव स्ट्रेस का सामना कार्बाईड मोटे चिप बना कर करता है। इसके लिए
• मिलिंग निचली दिशा में किया जाए।
• सरकने की गति (फीड रेट) ज्यादा रखकर आसानी से प्रवेश करने के लिए सबसे अच्छे प्रवेश कोण (एन्टरिंग ऐैंगल) रखें। (चित्र क्र. 4)।
1.2) काट में स्थित संपर्क कमान
कार्यवस्तु में खाँच (स्लॉट) बनाते समय संपर्क कमान सबसे अधिक, अर्थात 1800 होती है। प्रोफाइल मिलिंग करते समय वह सबसे कम होती है। संपर्क कमान जितनी बड़ी होगी, उतनी अधिक उष्मा कटिंग एज की ओर जाती है। इसके विपरीत संपर्क कमान जितनी छोटी होगी उतनी कम उष्मा निर्माण होती है और कर्तन दबाव भी कम होता है (चित्र क्र. 5)। इस्पात (स्टील) और ढ़ाले लोहे की (कास्ट आयर्न) कार्यवस्तु की मिलिंग करते समय Ae 70% रखने से सबसे अधिक उत्पादकता मिलती है और खर्चा भी कम होता है। Ae 50% हो तब कटर की मध्यरेखा (सेंटर लाइन) कार्यवस्तु की एज पर होती है। यह स्थिति प्रवेश के लिए सबसे कठिन होती है। ऐसे समय इन्सर्ट के टुकड़े उड़ते हैं और खर्चा भी बढ़ता है। मिलिंग के लिए कठोर स्टेनलेस स्टील, ड्यूप्लेक्स स्टेनलेस स्टील, इन्कोनेल जैसे धातु पर कार्य करते समय कर्तन बल कम करने हेतु Ae कम रखना चाहिए। इस से कटिंग एज का तापमान कम रह कर कार्यवस्तु सख्त होने की संभावना घटती है, साथ ही फीड की गति बढ़ाई जा सकती हैं।
1.3) काट से कटर बाहर निकलना (एक्जिट)
कटर काट से बाहर निकलते समय अगर चिप की मोटाई अधिक होगी तो कार्बाईड टूल बड़े पैमाने पर घिसता है जिस से टूल की आयु कम हो जाती है। काट के अंत पर तैयार होने वाली चिप को कोई आधार न होने के कारण चिप टूटने के बजाय सिर्फ मुड़ती (बेंड) है और उसकी दिशा बदलती है। कार्बाईड इन्सर्ट से मिलनेवाला बल (कम्प्रेसिव से टेन्साइल में परिवर्तित होनेवाला) इन्सर्ट के कोने के अंतिम एज से बाहर निकलने वाले चिप को तोड़ देता है। (चित्र क्र. 6)
इसलिए
• हमेशा डाउन मिलिंग करें।
• कटर ऑफ् सेंटर इस प्रकार रखें कि कटर के बाहर निकलते समय चिप की मोटाई अल्प रहे।
• कार्यवस्तु की कठिनाइयों को पहले सोचकर, प्रभावी प्रोग्राम स्थापित करना चाहिए। (अगर यह संभव न हो तो सरकन गति कम रखिए।)
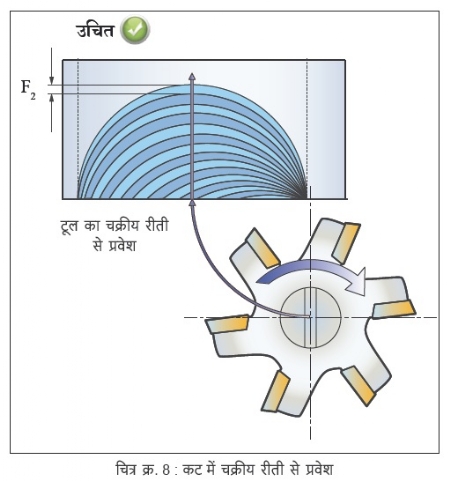
मिलिंग करते समय की सबसे कठिन स्थिति चित्र क्र. 7 में दिखाई है। यहाँ पूरा कटर कार्यवस्तु के संपर्क में है। देखते हैं कि इस स्थिति में टूल का सबसे बढ़िया मार्ग सी.एन.सी. प्रोग्रामिंग की सहायता से कैसे तय किया जा सकता है। इसके लिए चित्र क्र. 7 एवं 8 में दिखाए हुए टूल के मार्ग को देखिए। कटर काट से बाहर निकलते समय मोटे चिप निकल रहे हो तो टूल का तेजी से घर्षण होता है जिस से कटिंग एज टूटते हैं या उसके छोटें टुकड़े होते हैं। यदि कटर का कार्यवस्तु में सीधा प्रवेश होने के लिए प्रोग्राम दिया गया तो, कटर कार्यवस्तु में 100% प्रवेश करने तक बाहर निकलनेवाले चिप (एक्जिट चिप) मोटे होंगे। अर्थात हर बार कार्यवस्तु में प्रवेश करते समय इन्सर्ट पर अनावश्यक भार (लोड) आ सकता है। इससे टूल बहुत ज्यादा रगड़ जाने से उस की आयु कम हो सकती है। इस समस्या पर सबसे बढ़िया उपाय है प्रोग्रामिंग करते समय कुछ नई सोच लगाना! इसके लिए कार्यवस्तु में प्रवेश करने वाला कटर घड़ी की दिशा में घूमता होना जरूरी है। कटर घड़ी की विरुद्ध दिशा में घूमने वाला हो तो ज्यादा मोटी चिप की समस्या का समाधान नहीं मिलेगा। चित्र क्र. 8 में आप देख सकते हैं कि काट लेते समय घुमावदार प्रवेश करने के कारण, इन्सर्ट से बाहर निकलते समय चिप की मोटाई शून्य है। इससे फीड की गति तेज रखना संभव होने के साथ टूल की आयु भी बढ़ सकती है।
रवि नाईकजी को टूलिंग क्षेत्र में 40 से अधिक सालों का अनुभव है। टूलिंग और मशिनिंग ऐप्लिकेशन में आप ख्यातकीर्त सलाहगार हैं।