आवश्यक प्लग गेज के निर्माण हेतु ‘ऐक्युरेट’ ने स्वयं ही लैपिंग मशीन बनाया। ऐक्युरेट द्वारा निर्मित गेज सुयोग्य होने का प्रमाणपत्र ‘किर्लोस्कर ऑइल इंजिन्स’ ने दिया और इस प्रकार भारत की पहली मैट्रोलॉजी कंपनी स्थापन हुई।
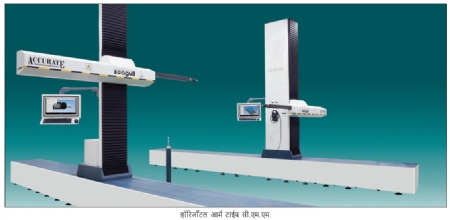
मापन उपकरणों का (मेजरिंग इंस्ट्रुमेंट) क्षेत्र चुनौतियों से भरा है। कारखाने में (यंत्रण की प्रक्रिया के दौरान) जिस अचूकता से कार्य होता है उस अचूकता की परीक्षा करने वाले उपकरण हमें बनाने होते हैं, यह इस क्षेत्र का सबसे बड़ा आहवान होता है। इसीलिए मापन उपकरणों का निर्माण अन्य उत्पादों की तुलना में अधिक मुश्किल तथा पेचीदा होता है। हमारे शुरुआती दिनों भारत में इस के काबिल कुशल कारीगर नहीं थे। महाविद्यालयों में भी यह चीजें सिखाई नहीं जा रही थी। इस वजह से इस व्यवसाय की शुरुआत करते वक्त हमें खुद नए लोग सिखा के तैयार करने पड़े। गेज के निर्माण में शामिल होनेवाली प्रक्रियाओं की रचना (डिजाइन) उस उत्पाद को ध्यान में रखते हुए, उसमें जो जटिल चीजें होती हैं उनका विचार कर के करना जरूरी होता है। बिल्कुल साधारण से प्लग गेज का निर्माण करना हो तो भी उस प्लग गेज की अचूकता लगभग 1 से 2 माइक्रॉन होना आवश्यक है। ग्राइंडिंग मशीन की मर्यादा में 10-15 माइक्रॉन की अचूकता हासिल की जा सकती है। लेकिन उसके आगे सिर्फ कुशल कारीगरों के जरिए, लैपिंग प्रक्रिया के इस्तेमाल से, अचूकता 15 माइक्रॉन से 2 माइक्रॉन तक लाई जा सकती है। यह हासिल करने के लिए लैपिंग मशीन भी हमें खुद बनाने पड़े। इसके सिवा एक ऐसे मशीन की जरूरत थी जिसमें गेज ग्राइंडिंग तथा लैपिंग के लिए एक ही सेटअप में ग्राइंडिंग और लैपिंग एकसाथ करना मुनासिब हो। यह मशीन खरीदना हमारे लिए संभव नहीं था। हमारी गेज निर्माण की कंपनी थी इसलिए हमें अधिक मशीनें जरूरी थी। मेरे पिताजी (विलासराव सालुंखे) ने इस मशीन के निर्माता ‘स्टूडर’ कंपनी के साथ बातचीत कर के इसका डिजाइन प्राप्त किया और उस हिसाब से हमने खुद इस मशीन का निर्माण किया।
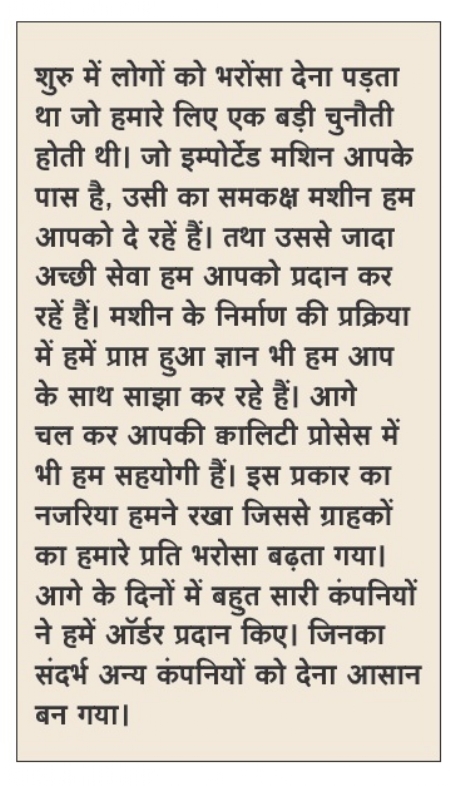
इस प्रक्रिया की चुनौतियाँ
निर्माण के हिसाब से जरूरी प्रक्रियाओं के लिए कौशल विकास तथा उनके लिए आवश्यक सभी टूल एवं साधन बनाना यह इसमें प्रमुख चुनौती थी। इनके मापन हेतु जरूरी साधन भी उतने ही पेचीदा थे। मिसाल की तौर पर बताएँ तो जब हमने थ्रेड गेज का निर्माण शुरु किया तब, थ्रेड गेज नापने के लिए, फ्लोटिंग कैरेज माइक्रोमीटर नामक उपकरण जरूरी था। उसमें भी कठिनाइयाँ थी। कोई भी चीज आयात करने के लिए इंपोर्ट लाइसंस जरूरी था और उसे पाने में बहुत वक्त बरबाद होता था। इसलिए हमने ‘मैट्रिक्स’ कंपनी से बात चला कर उनके डिजाइन अपनाए। युरोप के उद्योग यह सारी चीजें 30-40 सालों से बनाते आने से अब उन्हें उनकी जरूरत नही थी। इसलिए हमें उनसे डिजाइन आसानी से प्राप्त होते गए। उस आधार पर हमनें फ्लोटिंग कैरेज माइक्रोमीटर का निर्माण किया। ऐसे विभिन्न उत्पाद तथा मापन उपकरण भी हमारे व्यवसाय के हिस्से के रूप में यहाँ बनते गए। इस तरह 1972 साल से ‘ऐक्युरेट’ का सफर शुरु हो गया।
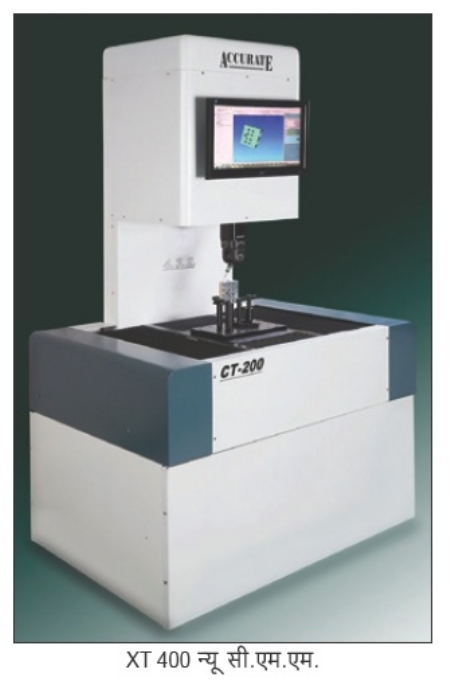
हर दफा एक नए उत्पाद के साथ उसके लिए जरूरी मशीन, सभी प्रक्रियाएँ तथा उनके लिए आवश्यक मापन साधन आदि सबकुछ तैयार होता गया। इनके प्रॉडक्ट डेवलपमेंट साइकिल बहुत लंबे होते थे। 1991 के बाद नीतीओं मे बदलाव होने से हमें कच्चे सामग्री की आपूर्ती आसानी से होने लगी। उत्पादों के उपउत्पाद हमें सहजता से उपलब्ध होते गए। इसलिए मशीनों का निर्माण और आसान बन गया।
सी.एम.एम. (कोऑर्डिनेट मेजरिंग मशिन) की यात्रा
सी.एम.एम. की रचना बहुत स्थिर और मजबूत होना जरूरी है। उसे जंग नही लगना चाहिए। उसकी उम्र लंबी होनी चाहिए और उस पर तापमान का असर अत्यल्प होना चाहिए। सी.एम.एम.में ‘एअर बेअरिंग तंत्र’ एवं ग्रेनाईट यह दो बहुत महत्वपूर्ण चीजें होती हैं। क्योंकि सी.एम.एम. के सभी चलित गाईड संपीडित वायु (कंप्रेस्ड एयर) बेअरिंग पर चलते हैं। इसलिए उसकी आयु अमर्याद बनती है। हमें गेजिंग का थोड़ा बहुत ज्ञान था जिसके आधार पर हमनें भारत में एयर बेअरिंग का तंत्र विकसित किया।
ग्रेनाईट यंत्रण की प्रक्रिया भी हमनें विकसित की। तीसरी महत्वपूर्ण चीज थी, सी.एम.एम. के लिए जरूरी डिजिटल तथा ऑप्टिकल स्केल। शुरु में, 80 के दशक में, हम मशीन टूल रेट्रोफिटिंग (पुनर्गठन) में एक जापानी कंपनी के साथ काम करते थे। वहाँ के मशीन टूल में जो इलेक्ट्रॉनिक तथा डिजिटल स्केल इस्तेमाल होते थे, वह देख कर हमें ध्यान आया कि सी.एम.एम. में यही तंत्र, थोड़े अलग तरीके से, इस्तेमाल किया जा रहा था। यह तीनों तंत्र साथ ला कर, उनके लिए जरूरी साफ्टवेयर का विकास कर के, 1988 में सी.एम.एम. बनाने का कार्य शुरु हो गया। 1991 साल की ‘VMTX’ प्रदर्शनी में यह मशीन पहली बार प्रदर्शित किया गया। उसके बाद हमें पहली ऑर्डर प्राप्त हो गई।
जब सी.एम.एम. की प्रक्रिया शुरु हो गई उस वक्त हम एक युरोपीय कंपनी के साथ काम कर रहे थे। भारत में मशीनों की बिक्री करना यह उस कंपनी का लक्ष्य था। इस वजह से हम समझ पाए कि इस किस्म के आधुनिक मशीन के लिए किन अन्य चीजों की जरूरत होती है। जैसे कि सी.एन.सी. नियंत्रक (कंट्रोलर), प्रोब प्रणाली आदि। उसकी इको सिस्टिम से भी हमारी पहचान हो गई जो भारत के बाहर थी। सी.एम.एम. में ग्रेनाईट महत्वपूर्ण हिस्सा था। भारत में हमारे जो प्रधान ग्रेनाईट डेवलपमेंट सप्लायर थे उनसे मैंने खुद बात की। उस वक्त हमारे ध्यान में आ गया कि ये आपूर्तिदार पारंपरिक रीति से काम कर रहे हैं। मैंने देखा था कि विदेश में ग्रेनाईट जैसी चीजों का यंत्रण पारंपरिक मशीनों पर किया जाता है। सी.एम.एम. मशीन के सभी गाईडवे ग्रेनाईट के बने हुए होते हैं।

मशीन टूल के स्लाईडवे ग्राइंडर पर ग्रेनाईट का यंत्रण होता है। अर्थात इसके लिए जरूरी टूल अलग किस्म के होते हैं। 1995-96 में एक कंपनी का स्लाईडवे ग्राइंडिंग मशिन हमें नीलामी में अल्प कीमत पर उपलब्ध हो गया। यह हमारा सबसे बड़ा पूँजी निवेश था। हमने यह मशीन खरीदा और उस पर ग्रेनाईट की पूरी डेवलपमेंट शुरु की। हमने यंत्रण और लैपिंग प्रक्रिया एकसाथ, एक ही सेटअप में करना शुरु किया। आगे चल कर, 2002 में, हमें और एक अच्छा मौका मिल गया। इटली में हमारे ही कार्यक्षेत्र में कार्यरत एक कंपनी थी। 50 सालों से चलती आई इस कंपनी की किसी वजह से नीलामी हो गई जिसमें उस कंपनी के सारे मशिन हमें मिल गए। 2002 में हमने वे सारी मशिनें भारत में लाई। उस दौरान वहाँ के कुछ डिजाइनरों को नौकरी की जरूरत थी। फिर उनका और हमारे लोगों का एक कार्यसमूह बनाया गया। उनका तजुर्बा और हमारे लोगों की ऊर्जा इकठ्ठा हो गई और वहाँ से सी.एम.एम. का सफर सही तरह से शुरु हो गया। फिलहाल हम छोटे से लेकर बड़े मशीनों तक, अधिक अचूकता होने वाली मशिनों से लेकर बॉडी इन्वाईट ऐप्लिकेशन तक, सालाना लगभग 125 मशीन निर्माण करते हैं। आज जर्मनी, अमरिका, मेक्सिको, थाइलैंड, चीन इन देशों में हमारी मशीनें भेजी जाती हैं।
हमनें लगभग 1 हजार मशीनें अपने ही देश में दी हैं, फिर भी भारत में यह मशीन बहुत कम पैमाने पर निर्माण होती हैं। ‘ऐक्युरेट’ और अत्यल्प संख्या में मौजूद कुछ अन्य कंपनियों के अलावा इस क्षेत्र में बहुत कम लोग हैं। इसकी दो वजहें हैं, एक तो हमारे यहाँ पहले जिस किस्म का माहौल था उसमें इस प्रकार की मशीनें किफायती संख्या (वॉल्युम) में निर्माण करना एक अहम् चुनौती थी। दूसरी बात यह है कि उद्योगों के नजरिये से भी मापन साधन की जरूरत किसी भी कारखाने में बहुत कम संख्या में होती है। एक उपकरण एक ही बार खरीदना है तो वह विदेशी ब्रांड का ही क्यों न खरीदा जाएँ? यह सोच बहुत दफा होती थी। क्योंकि इम्पोर्टेड मशिन होने से उन्हे उनके ग्राहकों को बताना आसान हो जाता था कि आप जो मशीन इस्तेमाल कर रहे हैं वही मेरे पास है।
उपकरण बनाते हुए सामने आई कठिनाईयाँ
वर्निअर जैसे उपकरणों के निर्माण में कुछ अलग किसम की कठिनाइयाँ होती हैं। सच कहा जाए तो हमने भारत में सब से पहले कैलिपर का निर्माण किया है। उस वक्त चुनौतियाँ भी बहुत थी। उसमें हमे एक अलग ही आहवान का सामना करना पड़ा। इस कैलिपर के लिए हमें अचुंबकीय फौलाद (नॉन मैग्नेटिक स्टील) आयात करना पड़ता था। उसके लिए हमें 410 और 420 ग्रेड के स्टेनलेस स्टील की जरूरत होती थी। लेकिन उस वक्त भारत सरकार ने सोचा कि स्टेनलेस स्टील की आयात, लघु उद्योगों में समाविष्ट बर्तन उद्योगों को खतरा है। इसलिए भारत सरकार ने बर्तन निर्माण उद्योग की रक्षा हेतु, उस प्रकार के स्टील पर 300% आयात शुल्क लगा दिया। हम इस विवाद में फँस गए, क्योंकि इन बर्तनों के लिए जरूरी 410 तथा 420 ग्रेड का स्टील हमारें टूल के लिए भी आवश्यक था। इसका हल करने हेतु हमने इसे अन्य स्टील कंपनीयों से बना के लिया लेकिन उससे कुछ लाभ न हो सका। बाद में चीन में स्टील का निर्माण बहुत बड़े पैमाने पर शुरु हो गया और वहाँ की विशिष्ट निर्माण पद्धति की वजह से उन्होंने बड़ी तादात में इन साधनों का उत्पादन शुरु किया जो एक सस्ते विकल्प के रूप में उपलब्ध हो गया।
इस प्रकार इन कंपनीयों ने पूरे विेश को मात दे दी। आगे चल कर इंडस्ट्री में लेसर का प्रयोग शुरु हुआ और वर्निअर जैसे उपकरणों के मार्किंग की रीतियाँ लेसर आधारित मशीनों में अपनाई गई (पहले फोटो मार्किंग का इस्तेमाल होता था)।
चीन के हर एक राज्य ने लेसर मशीन बिठा कर यह तंत्र उपयोग में लाया। इस वजह पूरी प्रक्रिया में उत्पाद खर्चे में बड़े परिवर्तन हो गए। वे विेश के बाजार में बहुत आगे निकल गए। इस वजह से आज ऐसी नौबत खड़ी हुई है कि बिक्री पश्चात सेवा की जरूरत न होने वाले उत्पादों के संदर्भ में चीन के साथ बराबरी करना सिर्फ भारत ही नहीं बल्कि दुनिया के किसी भी देश को सचमुच मुश्किल है। इस क्षेत्र की जिन कंपनीयों ने खुद का कोई विशेष उत्पाद पेश कर के उसमें विकास हासिल किया है वही आज जीवित हैं। हमें इस बात पर नाज है कि ‘ऐक्युरेट’ उनमें से एक है।
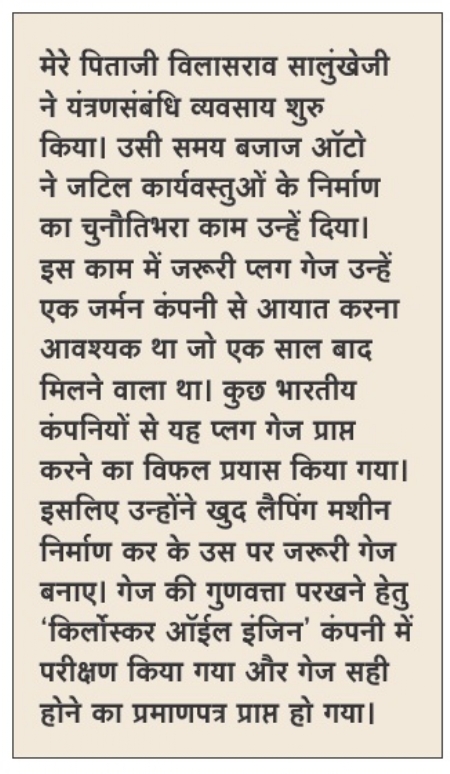
इन सब बातों में इलेक्ट्रॉनिक्स का भी बहुत बड़ा योगदान है। फिलहाल ‘इंडस्ट्री 4.0’ नाम का एक औद्योगिक मापदंड (स्टैंडर्ड) स्थापित हो रहा है जिसमें स्वचालित क्षतिपूर्ती (ऑटोमैटिक कॉम्पेन्सेशन) यानि कार्य के दौरान प्रक्रिया ठीक करने के उपायों (प्रोसेस करेक्शन) पर बल होगा। जहाँ विभिन्न साधनों के बीच संज्ञापन जरूरी है और इसके लिए नई कार्यपद्धति की स्थापना अनिवार्य है, वहाँ इलेक्ट्रॉनिक्स बहुत महत्वपूर्ण होगा। दुर्भाग्य से इस प्रकार के इलेक्ट्रॉनिक्स (हार्डवेयर) का निर्माण भारत में नहीं होता है। क्योंकि इलेक्ट्रॉनिक्स में होने वाले अलग अलग किस्म कें सेंसर भारत में नहीं बनते हैं। युरोप और चीन में इन का निर्माण किया जाता है।
विक्रय और विपणन की हमारी कुछ नीतियाँ थी। हमने तय किया था कि हम इस उद्योग के लिए जितना माल आयात कर रहे हैं उतनी तो हमारी निर्यात होना जरूरी है। इस साल हम कंपनी का 25% माल निर्यात कर रहें हैं और यह अनुपात 40% तक बढ़ाने की हमारी कोशिश है। अर्थात भारत का बाजार हमारे व्यवसाय के लिए सबसे बड़ा है। फिलहाल भारत के बाजार में ‘ऐक्युरेट’ का हिस्सा करीबन 40% है और बाकी 60% अन्य कंपनीयों में विभाजित है। इसलिए हमने हमारी मशीनें भारत के बाहर बेचने पर ध्यान केंद्रित किया है। सी.एम.एम. के साथ अन्य मापन उपकरण भी हम निर्यात करते हैं।
अनुसंधान और विकास की स्थिति
हमारे जैसी कंपनियों ने अनुसंधान और विकास में अच्छा संतुलन हासिल किया है। हमारे अभियंता तथा बाहर से प्राप्त मार्गदर्शन में मेल होने के जरिए हम इसमें सफल हो गए हैं। इस क्षेत्र में काम करते वक्त अचूकता के नजरिये से कुछ चीजें महत्वपूर्ण हैं। आप जिसका इस्तेमाल कर रहें हैं वह उपकरण और उसके इस्तेमाल के दौरान होने वाला माहौल (तापमान, नमी आदि) यह बातें बहुत मायने रखती हैं। सही तापमान पर उस उपकरण का इस्तेमाल मुनासिब होना बहुत महत्वपूर्ण बात है। उपकरण का निर्माण करने के लिए सुयोग्य ऑपरेटर, उसकी हुनर, जटिल तथा पेचीदा प्रक्रिया की पूरी तथा योग्य जानकारी होनी जरूरी है।
‘ऐक्युरेट’ में इन तीनों का संतुलन करने का प्रयास किया गया है। ‘ऐक्युरेट’ न केवल एक कंपनी है बल्कि एक ऐसी ‘इंस्टिट्युशन’ है जहाँ हमारे सभी कारीगरों को ‘कुशल कारीगर’ बनाने पर हम ध्यान देते हैं। हर कारीगर को हर किस्म की जानकारी होना तथा उसके पास हर तरह का काम करने की काबिलियत होना हमारे लिए एक अहम् बात है। हमारा प्रयास है कि यांत्रिकी, इलेक्ट्रॉनिक्स, साफ्टवेयर इन सभी क्षेत्रों में हम सक्षम बन जाए।
अनुसंधान के लिए जरूरी अभियंता हमेंही तैयार करने होते हैं। इसलिए हम नए यानि अनुभवहीन अभियंता भर्ती कर के उनसे पहले उत्पादन क्षेत्र में काम करवा कर उन्हें तैयार करते हैं। उसके बाद ही वो डिजाइन में आते हैं। पहले एक उत्पाद विकसित तथा सुस्थापित करने हेतु हमें जितना समयावधि लगता था वह अभी बहुत कम हो गया है। नई प्रक्रियाएँ, उनकी खूबियाँ, समस्याएँ हल करने के तंत्र आदि मुद्दे हमारी समझ में आ जाने से अब सारी प्रक्रियाएँ सुलभ बन चुकी हैं।
020 - 66039000
[email protected]
विक्रम सालुंखेजी अभियांत्रिकी शिक्षा पूरी करने के बाद उनके पिताजी विलासराव सालुंखेजी ने 1963 में आरंभ की हुई ‘ऐक्युरेट सेल्स ऐंड सर्विसेस प्रा. लि. ’ कंपनी के पिछले 29 सालों से प्रबंधक संचालक रहे हैं।