उद्योग जगत के विस्तृत क्षेत्र में सामान्यतः उपयोग किए जानेवाले हल्के धातुओं में से ऐल्युमिनिअम सबसे अधिक इस्तेमाल होनेवाली धातु होगी। धातुशास्त्र और धातु को आकार देने की प्रक्रिया में हो रहे विकास के कारण ऐल्युमिनिअम का प्रयोग हर क्षेत्र में हो रहा है। इसका सबसे उपयोगी और आमतौर पर दिखने वाला रूप है खाद्यवस्तु को लपेटी जानेवाली ऐल्युमिनिअम फॉइल, और सबसे उच्च कोटि का तांत्रिक उपयोग हवाई जहाज के ढ़ाँचे में होता है। तुलनात्मक दृष्टि से मानव ने इस्तेमाल में लाई हुई यह सबसे नई धातु है। 1825 में इसकी खोज हुई और उद्योग जगत में इसकी गुणवत्ता जानकर इसका इस्तेमाल प्रारंभ हुआ।
कास्टिंग, फोर्जिंग, एक्स्ट्रूजन तथा रोलिंग जैसी विभिन्न प्रारंभिक प्रक्रियाओं द्वारा ऐल्युमिनिअम को आकार दिए जाते हैं। इन प्रक्रियाओं के द्वारा हमें यंत्रण करने के लिए कास्टिंग एवं फोर्जिंग, शीट, विशेष सेक्शन, ट्यूब, बार और वायर रॉड प्राप्त होते हैं।
ऐल्युमिनिअम से बननेवाले मिश्रधातु (ऐलॉइ) श्रेष्ठ यंत्रण क्षमतावाले धातु माने जाते हैं। धातु की कटाई के लिए आवश्यक ताकत, टूल की आयु, श्रेष्ठ पृष्ठीय फिनिश निर्माण करने की क्षमता, चिप आसानी से दूर करने की क्षमता और तेज गति से धातु को काटने की क्रिया इन सभी के लिए यंत्रण क्षमतालिका क्र. 1 में दिखाया गया है।
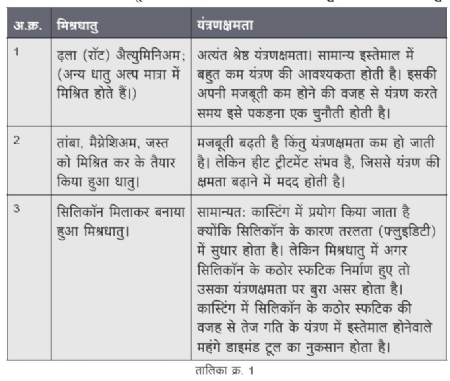
ऐल्युमिनिअम के जिस मिश्रधातु पर यंत्रण की प्रक्रिया करनी होती है उसके रासायनिक घटक तथा उनकी मात्रा और साथ ही भौतिक गुणधर्म जानना जरूरी होता है। मिश्रधातु की धातुशास्त्रीय विशेषताएँ और उपलब्ध मशीनरी की क्षमता इन दोनों का खयाल रख कर ही टूल का प्रकार एवं ज्यामिति, फिक्श्चर, कार्यवस्तु पकड़ने की व्यवस्था, कटाई के पैरामीटर, शीतक आदि का चयन करना चाहिए। ऐल्युमिनिअम की कठोरता कम होने के कारण उसे काटने के लिए वाइट बिट टूल से पॉलिक्रिस्टलाइन डाइमंड (पी.सी.डी.) तक विभिन्न प्रकार के टूल इस्तेमाल कर सकते हैं। जब मशीन की स्पिंडल की आर.पी.एम. पर मर्यादा होती है, तब एच.एस.एस. जैसे टूल का इस्तेमाल करना चाहिए जो कार्बाईड से नर्म होते हैं। लेकिन इससे पृष्ठीय फिनिश पर मर्यादा आती है। कटाई की गति कम होने के मामले में ‘बिल्टअप रिज’ यह मुख्य समस्या होती है। इसके लिए रेक ऐंगल का ध्यान से चयन करना पड़ता है। सिलिकॉन मौजूद होने वाले मिश्रधातु में रेक ऐंगल अधिक और तांबे तथा मैग्नेशिअम मौजूद होने वाले मिश्रधातु में रेक ऐंगल कम रखने से काम बढ़िया होता है। एच.एस.एस. टूल का इस्तेमाल करते समय पानी में घुलनेवाले (सोल्युबल) कटिंग तेल या केरोसिन के प्रयोग से अच्छा काम होता है। लेकिन केरोसिन ज्वलनशील और खतरनाक होने के कारण उसका इस्तेमाल न करने की
सिफारिश की जाती है। कटाई की गति कम रहते समय चिप बाहर निकालने की समस्या गहरी होती है क्योंकि उससे निकलने वाली चिप अखंड़ित और लंबी होती है। कटाई की कम गति पर 6.3 Ra और विशेष परिस्थिति में 3.2 Ra पृष्ठीय खुरदरापन (रफनेस) मिल सकता है।
कोटिंग की हुई या सिवा कोटिंग की कार्बाईड टूल के इस्तेमाल से भी हम कटाई की गति बढ़ा सकते हैं। इससे ‘बिल्टअप रिज’ की समस्या दूर होने में मदद होती है। टर्निंग, मिलिंग और टैपिंग जैसी विभिन्न प्रक्रियाओं के लिए कटिंग टूल के उत्पादक कई सुझाव देते हैं। बेहतरीन परिणाम पाने के लिए उच्च गति के मशीन स्पिंडल आवश्यक होते हैं। पानी में घुलनेवाले सिंथेटिक और सेमी सिंथेटिक कटिंग तेल के विभिन्न विकल्प उपलब्ध हैं। कार्बाईड टूल के इस्तेमाल से कम लंबाई के चिप बनते हैं जिनको निकालना आसान होता है। कार्बाईड टूल इस्तेमाल करके प्रायः 3.2 Ra जितना पृष्ठीय खुरदरापन मिलता है। विशेष परिस्थिति में 1.6 Ra का पृष्ठीय खुरदरापन मिलने की संभावना होती है।
विकसित सी.एन.सी. मशीनिंग सेंटर में 20000 आर.पी.एम. तक की स्पिंडल गति मिल सकती है। इस जगह पी.सी.डी. से बनाई टूल का इस्तेमाल संभव है। ये टूल फिनिशिंग के लिए इस्तेमाल होते हैं। उससे सामान्यतः 0.8 Ra और विशेष परिस्थिति में 0.2 Ra तक पृष्ठीय खुरदरापन मिल सकता है। जहाँ बहुत ही चिकनी पृष्ठीय फिनिशिंग चाहिए हो और नाप का टॉलरंस (छूट) अत्यल्प हो ऐसे सूक्ष्म बोरिंग, मिलिंग तथा रीमिंग के काम में ही यह टूल इस्तेमाल किया जाता है। इस टूल का प्रयोग करते समय खास सिंथेटिक कटिंग तेल उपयुक्त होता है। उच्च आर.पी.एम. पर इस टूल का उपयोग करते समय उस आर.पी.एम. पर टूल का डाइनैमिक बैलंसिंग करवाना आवश्यक होता है। बैलंस न किए गए टूल का इस्तेमाल किया गया तो उसके महंगे टिप टूट सकते हैं। पी.सी.डी. बोरिंग बार या रीमर के इस्तेमाल के पहले एक और सावधानी बरतना जरूरी होता है। ओशस्त करें कि पहले किए हुए काम में इस्तेमाल किए गए रफिंग टूल (ड्रिल) के टुकड़े अंदर अटके नहीं हैं। खास कर के ब्लाइंड छिद्र के मामले में ज्यादा सावधानी लेनी चाहिए। टूटे हुए टूल के टुकड़े अंदर ही रह जाने की संभावना होती है (चित्र क्र. 1) और स्वचालित आवर्तन (साइकिल) के अनुसार अगले चरण के काम में पी.सी.डी. टूल उनसे टकरा कर टूटता है। इससे महंगे टूल के इस्तेमाल का वित्तीय लाभ नष्ट हो जाता है।
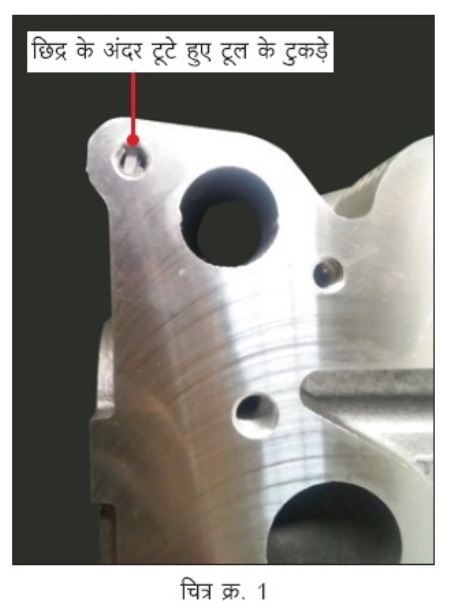
फिक्श्चर के डिजाइन में क्लैंप और लोकेटर का विशेष रूप से ध्यान रखना पड़ता है। यंत्रण किए हुए पृष्ठ पर क्लैंप का या लोकेशन के छिद्र में डावेल पिन का इस्तेमाल करते समय, फिक्श्चर के कठोर (हार्ड) किए हुए इन भागों के कारण, कार्यवस्तु के पृष्ठ पर निशान पैदा होते हैं। इसी प्रकार की अन्य समस्या से नुकसान हो सकता है। इस प्रकार की हानि टालने के लिए क्लैंप पर पीतल की टोपी/बटन लगाना चाहिए या पट्टी ब्रेज करनी चाहिए (चित्र क्र. 2)। संभव हो तो शंख के आकार की पीतल की टोपी लोकेशन पिन पर लगा दी जाए। लोकेशन पिन को बड़ा चैंफर दिया जाए। जिस स्थान पर यह चैंफर व्यास से मिलता है वहाँ त्रिज्या (रेडियस) दी जाए।
ऐल्युमिनिअम यंत्रण के फिक्श्चर में क्लैंपिंग का बल सतर्कता से नियंत्रित रखना बहुत महत्वपूर्ण होता है। यांत्रिकी फिक्श्चर के मामले में ऑपरेटर का झुकाव, रिंग स्पैनर का इस्तेमाल कर के कार्यवस्तु ज्यादा से ज्यादा कस कर पकड़ने की ओर होता है। यह बहुत ही खतरनाक है। इसके कारण पुर्जा टेढ़ामेढ़ा होकर अस्वीकृत (रिजेक्ट) होता है। इसलिए यांत्रिकी फिक्श्चर के मामले में ध्यानपूर्वक टार्क सेट करने के बाद, टार्क रेंच का इस्तेमाल करना अत्यावश्यक है। हैड्रोलिक फिक्श्चर के मामले में क्लैंपिंग का दबाव परीक्षण कर के सेट कर सकते हैं।
ऐल्युमिनिअम के यांत्रिक भाग का डीबरिंग करना (बर हटाना) आसान होता है लेकिन उसमें भी एक बात की सावधानी लेनी पड़ती है। अगर मिलिंग से फिनिश किए हुए पृष्ठ के किनारों पर रोटरी बर टूल का इस्तेमाल किया गया तो डीबरिंग गन किनारे से फिसलने की संभावना होती है और पूरी तरह से फिनिशिंग किए हुए चिकने पृष्ठ पर डीबरिंग गन खराश बना सकती है (चित्र क्र. 3)। इससे पृष्ठ का स्थायी नुकसान होता है। बहुत ही सुंदरता से यंत्रण किए हुए ऐल्युमिनिअम के पुर्जे, विशेष रूप से कास्टिंग के पतले पुर्जे गलत डीबरिंग के कारण रिजेक्ट हो जाते हैं। इस खतरे से बचने के लिए योग्य ऊँचाई के वर्क बेंच और हो सके तो वर्क होल्डिंग फिक्श्चर का इस्तेमाल किया जाना चाहिए, जिससे ऑपरेटर के हाथ से डीबरिंग गन गलत दिशा में न फिसले। कार्यवस्तु के आकार के अनुसार योग्य प्रकार के रोटरी बर टूल का इस्तेमाल किया जाए। इसके अलावा ऑपरेटर की प्रशिक्षा महत्वपूर्ण है ही।
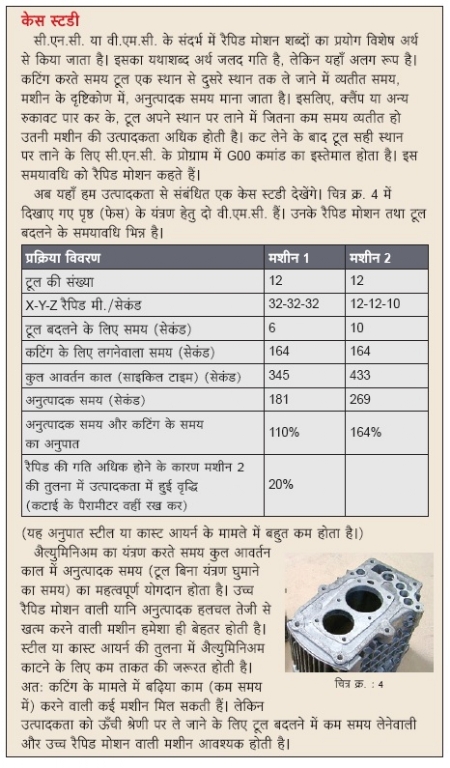
ऐल्युमिनिअम के उच्च सटीकता के पुर्जे को संभालकर पकड़ना चाहिए। ट्रोली और भण्डारण के बिन (BIN) प्लास्टिक के होने चाहिए या उनपर टेफ्लॉन का कोटिंग होना हितकर होगा। ऐल्युमिनिअम के यंत्रण के समय, विशेषकर सी.एन.सी. मशीन पर सर्वोत्कृष्ट क्षमता पाने के लिए, केवल कटाई का समय तथा बर्बाद अनुत्पादक समय इन दोनों का विश्लेषण करना महत्वपूर्ण है। अनुत्पादक समय में टूल के चलन (एयर कटिंग) के लिए लगनेवाला समय और टूल बदलने के लिए जरूरी समय समाविष्ट होते हैं। कटाई की गति उच्च होने के कारण कुल आवर्तन के समय में कटाई की गति का समय अल्प होता है। इसी वजह से मशीन का अनुत्पादक समय घटाने के लिए कई योजनाएँ बनानी पड़ती हैं। टूल बदलते समय बर्बाद होनेवाला समय कम करने के लिए कॉम्बिनेशन टूल का इस्तेमाल करना और कटाई का एक पास हो जाने पर दूसरे पास के लिए शीघ्रता से लौटना (फास्टर रैपिड मूवमेंट) आदि इलाजों का अधिकतम इस्तेमाल करना जरूरी है। सी.एन.सी. मशीन में हुई रैपिड संबंधित आधुनिक तंत्र ऐल्युमिनिअम के यंत्रण की उत्पादकता को एक वरदान साबित हुआ है।
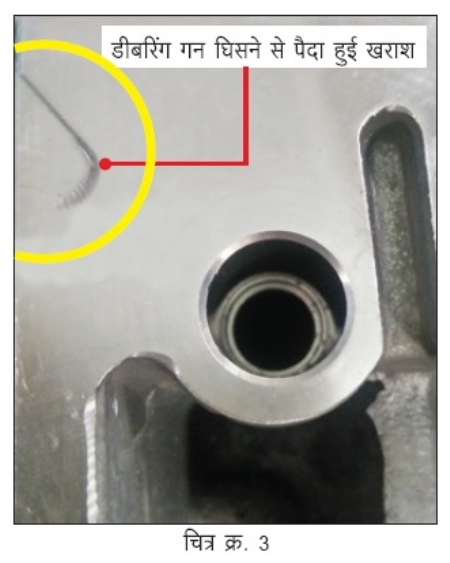
रैपिड मूवमेंट तथा टूल बदलने के समय का कुल उत्पादकता पर होनेवाला असर जानने हेतु दी हुई केस स्टडी का अध्ययन कीजिए।
0 9359104060
राजेश म्हारोळकरजी यांत्रिकी अभियंता है। आप ‘श्रीनिवास इंजिनिअरिंग ऑटो कंपोनंटस् प्रा. लि.’ के संचालक हैं। यह कंपनी ट्रैक्टर और ऑटोमोटिव उद्योगों को आयर्न कास्टिंग और प्रिसिजन मशीनिंग की सेवा प्रदान करती है।