यंत्रण प्रक्रिया से अपेक्षित होने वाला उत्कृष्ट पृष्ठीय फिनिश किन पैरामीटर पर निर्भर रहता है तथा उस पर असर करने वाले घटकों का नियंत्रण कैसे किया जाता है आदि बातों की जानकारी आप इस लेख में पढ़ेंगे।
यंत्रण प्रक्रिया से प्राप्त उपलब्धियों में से बढ़िया पृष्ठीय फिनिश यह एक प्रमुख उपलब्धी है। यह कौन कौनसे पैरामीटर पर निर्भर है और उसे प्रभावित करने वाले कारकों को कैसे नियंत्रित करना है यह हम इस लेख में देखने वाले हैं।
जब हम ‘सुधार’ इस शब्द का इस्तेमाल करते हैं तब हमें केवल पृष्ठीय खुरदरेपन का मूल्य (रफनेस वैल्यू) अपेक्षित नहीं होता। सुधार में पृष्ठीय फिनिश के साथ साथ अपेक्षित गुणवत्ता का ओशासन, उत्पाद का खर्चा, उत्पाद सुयोग्य समय में पूरा करने की काबिलियत जैसे अन्य कारक भी शामिल होते हैं। इन तीन कारकों में से गुणवत्ता के बारे में कोई समझौता मुनासिब नही है। उत्पाद का डिजाइन उसकी अपेक्षित गुणवत्ता का निर्धारण करता है। आर्थिक/वास्तविक नजरिये को ध्यान रखते हुए यंत्रण करने वाला व्यक्ति अन्य दो कारकों को कम/ज्यादा प्राथमिकता दे सकता है।
सामान्यतः अधिकांश उत्पादनों के डिजाइन में पृष्ठीय खुरदरेपन के मूल्य की अपेक्षित परिसीमा (आउटर लिमिट) निर्देशित की गई होती है। जब हम पृष्ठीय खुरदरेपन का अपेक्षित मूल्य प्राप्त करने हेतु यंत्रण प्रक्रिया का सेटिंग करते हैं, तब निर्देशित गुणवत्ता के बाहरी परिसीमा मूल्य के 50 से 75% पृष्ठीय फिनिश प्राप्त करने का उद्देश रखना चाहिए। (अगर लक्ष्य 6.0 होगा तो 4.5 या 3.0 प्राप्त करने का प्रयास करना चाहिए)। यह एक सामान्य गलतफहमी है कि निर्दिष्ट किए गए पृष्ठीय खुरदरेपन मूल्य से बहुत कम मूल्य हासिल करने का प्रयास करना या स्वीकार करना अच्छा होता है। पृष्ठीय खुरदरेपन का मूल्य जितना कम उतनी पृष्ठ की चिकनाई अधिक होती है। कृपया ध्यान में रहे कि उत्कृष्ट पृष्ठीय फिनिश हासिल करने के लिए उत्पादकता कम होना और टूल के खर्चे में बढ़ोतरी, इस प्रकार दुगनी कीमत देनी पड़ती है।
पृष्ठीय खुरदरापन मूल्य कितना चाहिए यह तय करने के बाद अब देखते हैं कि प्रक्रिया के पैरामीटर क्या रहेंगे?
1. हमें किस धातु पर काम करना है यह ध्यान में रखते हुए इस्तेमाल किए जाने वाले कटिंग टूल की ग्रेड तथा कटिंग ऑइल तय करें।
धातु में घटकों का अनुपात, उसकी आंतरिक रचना, कठोरता (हार्डनेस) इन सब पर ध्यान देते हुए वह धातु, यंत्रण के दौरान किस प्रकार बर्ताव करेगी यह समझ लेना चाहिए। उसके मुताबिक हमें कटिंग ऑइल का इस्तेमाल करना है या नहीं, अगर करना है तो कौनसा कटिंग ऑइल इस्तेमाल करना है, यंत्रण के लिए कौनसे कटिंग टूल का प्रयोग करना है, उस पर कौनसा कोटिंग रहेगा, इन सब चीजों के बारे में फैसला करना होता है। टूल और कटिंग ऑइल के उत्पादकों से धातु के गुणधर्मों के बारे में जानकारी पर चर्चा कर के उनकी सलाह/सिफारिश लेना हमेशा हितकारी होता है।
2. कितनी धातु काटनी है इसका अंदाजा लगाके काट की संख्या तय करें।
यंत्रण के दौरान, उपलब्ध कच्चे माल के रूप के मुताबिक अलग अलग पृष्ठभागों से निकाली जाने वाली धातु का मूल्यांकन करना पड़ता है। इस दौरान कच्चे माल की अनियमितताएँ और अपेक्षित टॉलरन्स का भी खयाल करना चाहिए।
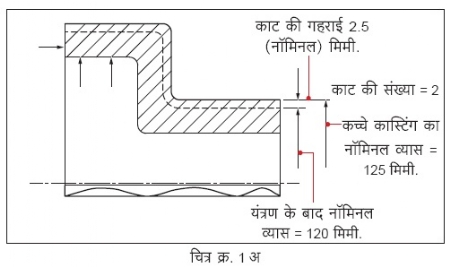
मिसाल की तौर पर मान लीजिए की 125 मिमी. के व्यास में से 120 मिमी. फिनिश व्यास की वस्तु बनानी है (चित्र क्र. 1अ, 1ब, 1क)। कास्टिंग के टॉलरन्स के मुताबिक अधिकतम व्यास 126.6 मिमी. होगा। उसके अलावा कोर में 0.8 का फर्क होने की अनुमती ध्यान में ली जाए तो किसी भी स्थान पर अधिकतम व्यास 128.2 मिमी. रहेगा, इसलिए वास्तव में कटिंग का अलाउंस (128.2 - 120) / 2 = 4.1 मिमी. रहेगा। (125 - 120) / 2 = 2.5 मिमी. इस अपेक्षित नाप से यह बहुत अधिक है। अभी कार्यवस्तु और टूल की जकड़ की दृढ़ता, कटिंग के लिए उपलब्ध बल आदि का खयाल रखते हुए काट की संख्या तय करनी पड़ेगी। अगर कार्यवस्तू में से 2.5 मिमी. मोटाई का मटीरीयल निकालना हो और पृष्ठीय फिनिश Ra 4 माइक्रॉन तक अपेक्षित हो, तो एक रफ कट और एक फिनिशिंग कट ले कर काम पूरा हो सकता है। लेकिन अगर कटिंग अलाउंस 4.1 मिमी. का है यह बात ध्यान में ली जाए, तो शायद दो रफ कट और एक फिनिशिंग कट लेना पड़ेगा। काट की संख्या न्यूनतम हो इस प्रकार की सर्वसामान्य नीति अपनाई जाए तो उत्पादकता एवं टूल के खर्चे पर नियंत्रण रखना मुमकिन होगा, फिर भी प्रत्यक्ष रूप से मशीन पर आने वाले कच्चे माल की अनियमितता का खयाल करना उतनाही महत्वपूर्ण है।
फिनिशिंग काट के लिए उपलब्ध यंत्रण अलाउंस एक महत्वपूर्ण कारक है। धातु के गुणधर्म, शीतक, फिनिशिंग टूल के नोज की त्रिज्या, टूल का टॉप रेक कोण, पहले रफ कट में प्राप्त पृष्ठीय खुरदरापन और प्रति फेरा फीड आदि बातें ध्यान में ले कर फिनिशिंग टूल के बारे में फैसला किया जा सकता है। फिनिशिंग टूल को उपलब्ध होने वाले यंत्रण अलाउंस पर अच्छा काबू रखने से ही प्राप्त होने वाले नाप के टॉलरन्स को परिसीमा में रखने में मदद हो सकती है।
3. रफ कट और फिनिश कट के लिए टूल की ज्यामिती नियत करें।
क्वालिटी, कॉस्ट, डिलिवरी (क्यू.सी.डी.) इन लक्ष्यों में इष्टतम नतीजे पाने का मूलमंत्र है रफिंग और फिनिशिंग के लिए भिन्न टूल का इस्तेमाल करना। ऑटोमैटिक टूल चेंजर (ए.टी.सी.)/टूल टरेट की मर्यादाओं की वजह से कभी कभी अभियंता को रफिंग और फिनिशिंग के लिए एक ही टूल का इस्तेमाल करने का प्रलोभन हो जाता है। लेकिन हमारा मशवरा होगा कि ऐसा ना कर के, किसी किस्म का विशेष संयुजित (काँबिनेशन) टूल का प्रयोग करें (चित्र क्र. 2)। अभी हम टूल की ज्यामिती के पैरामीटर के ओर ध्यान बढ़ाएंगे।
टॉप रेक कोण, धन या ऋण?
उत्पादकता और टूल का खर्चा इन नजरियों से ऋण रेक कोण लाभकारी होते हैं क्योंकि इससे हमें प्रति टूल इन्सर्ट अधिक संख्या में कटिंग एज मिलते हैं। रफिंग के कार्य में उनका बड़े पैमाने पर इस्तेमाल किया जाना चाहिए। लेकिन फिनिशिंग कार्य के दौरान मौजूदा धातु के लिए अपेक्षित पृष्ठीय खुरदरेपन के मूल्य पर उसका इस्तेमाल निर्भर होता है। पृष्ठ की अच्छी चिकनाई के लिए धन रेक कोण वाले टूल अधिक अच्छा काम निभाते हैं। ऋण रेक कोण वाले टूलों के इस्तेमाल के दौरान कटिंग के लिए अधिक बल जरूरी होता है और कार्यवस्तु पकड़ने की और मजबूत सुविधा जरूरी होती है।
टूल की नोज त्रिज्या, छोटी या बड़ी?
इसका फैसला करने के लिए परिमाण/आकार/ज्यामिती के टॉलरन्स, डिजाईन में अनुज्ञेय फिलेट त्रिज्या जैसे मुद्दों के साथ में ही अपेक्षित पृष्ठीय खुरदरेपन के मूल्य का खयाल करना होगा। काट की एकसमान गहराई के लिए अगर टूल की नोज त्रिज्या बड़ी होगी तो, छोटी त्रिज्या की तुलना में, टूल की धार जादा समय बनी रहेगी। टूल की नोज त्रिज्या छोटी होने से नापों के नियंत्रण (डाइमेंशनल कंट्रोल) के अच्छे परिणाम हासिल हो सकते हैं। लेकिन टूल अधिक समय तक चलने तथा अच्छा पृष्ठीय फिनिश हासिल होने के लिए बड़ी त्रिज्या अधिक अच्छी साबित होती है।
4. फिनिशिंग काट की गहराई और फीड तय करना
क्यू.सी.डी. की परिभाषा में पृष्ठीय खुरदरापन नियंत्रित रखने में शायद यह दो सब से महत्वपूर्ण कारक हैं। टूल या कार्यवस्तु के गोलाकार घूमने के कारण काटे जाने वाले पृष्ठ पर सूक्ष्म आकार के उबड़ और गड्ढ़े पैदा होते हैं। सामान्यतः इन्हें फीड मार्क कहलाते हैं। यह थ्रेड जैसे दिखाई देते हैं और इन थ्रेड का पिच एवं गहराई ऊपरलिखित दो कारकों पर निर्भर होती हैं। इसलिए कह सकते हैं कि फीड जितना कम, उतनी अच्छी चिकनाई हासिल होगी। लेकिन कम फीड का मतलब है कम उत्पादकता। इसलिए इन दोनो में से बीच का मार्ग निकालना अभियंता के लिए एक कसौटी होती है। जैसे कि पहले बताया गया है, निर्देशित अधिकतम मूल्य के 50% से 75% पृष्ठीय खुरदरापन मूल्य प्राप्त करने का हमारा उद्देश होना चाहिए। इसकी एक मिसाल आगे दी गई है (चित्र क्र. 3)। इस मामले में बोल्ट, फ्लैंज को जहाँ स्पर्श करता है वहाँ का पृष्ठ थोड़ा खुरदरा होना जरूरी था क्योंकि उससे बोल्ट का फिसलना रूक जाता था। जहाँ जादा टार्क जरूरी है, वहाँ यह महत्वपूर्ण साबित होता है। इसलिए जब डिजाइनर 12 ठर पृष्ठीय फिनिश की अपेक्षा रखता है तब उत्पादक ने मशीन की सेटिंग इस प्रकार करनी चाहिए कि उससे 7 - 12.5 के बीच का ठर मूल्य प्राप्त होगा। इससे अधिक फिनिश देने में संसाधनों पर फिजूल खर्चा तो होगा ही, ऊपर से अपेक्षित परिणाम न मिलने की संभावना बढ़ेगी। इसलिए यह ना करें।
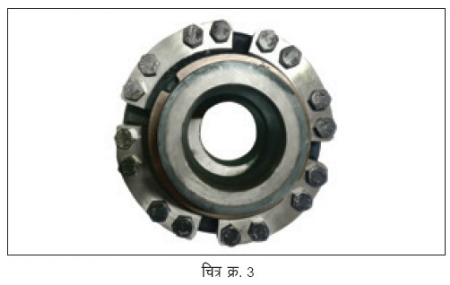
टर्निंग के दौरान टूल की नोज त्रिज्या और पृष्ठीय फिनिश
टर्निंग के दौरान टूल कार्यवस्तु के पृष्ठ पर एक सर्पिल (हेलिकल) खाँचा (थ्रेड के समरूप) तैयार करता है। इस खाँंचे की गहराई यानि खुरदरेपन की उँचाई R MAX होती है (चित्र क्र. 4)।
R MAX ∝ (फीड - F)1/2 तथा R MAX ∝ 1/नोज त्रिज्या (R)।
नीचे दिया हुआ सूत्र हमें ठर का अंदाजित मूल्य देता है। अर्थात अचूक मूल्य वास्तविक नापन से ही मिलता है।
R MAX = 1000X F2/ 8R
तालिका क्र. 1 में टूल की नोज त्रिज्या और फीड की विविध जोड़ों के लिए R MAX का मूल्य माइक्रॉन में दिया गया है।
यह गणित से प्राप्त मूल्य है। वास्तव में प्राप्त मूल्य टूल का घिसाव (वेयर), मशीन का दर्जा, कंपन (वाइब्रेशन) आदि पर निर्भर होता है। शुरुआत करने में यह मूल्य मददगार रहेंगे। पृष्ठीय फिनिश में सुधार लाने के लिए हम एक तो फीड रेट कम कर सकते हैं या नोज त्रिज्या बढ़ा सकते हैं। फीड आधा किया जाए तो पृष्ठीय फिनिश में चार गुना सुधार प्राप्त होगा (R MAX 75% से कम हो जाता है)। नोज त्रिज्या दुगनी की जाए तो पृष्ठीय फिनिश में दो गुना सुधार प्राप्त होगा (R MAX 50% से कम हो जाता है)।
5. टूल और कार्यवस्तु की जकड़ की दृढ़ता (रिजिडिटी)
इसमें कुछ भी दोष होगा तो कंपन निर्माण हो कर फलस्वरूप चैटर मार्क, खुरदरा पृष्ठ तथा परिमाण/ज्यामिति में अधिक फर्क जैसे नतीजे होंगे। चैटर मार्क का होना निर्देशित करता है कि टूल या कार्यवस्तु ठीक तरीके से नहीं पकड़ी गई है। प्रक्रिया में स्थित कंपन एक दोष है जिसे हमेशा काबू में रखना पड़ता है। दृढ़ता के लिए कोई भी सर्वसमावेशी समाधान नही हो सकता। जैसे ही समस्याएँ सामने आएगी, वैसे उस स्तर पर उचित समाधान ढूँढ़ना पड़ता है।
संक्षेप में कहा जाए तो यंत्रण प्रक्रिया का नियोजन करते वक्त ही हमारे सामने पृष्ठीय खुरदरेपन का सुस्पष्ट लक्ष्य होना चाहिए। हमारा यह मशवरा है कि यंत्रण प्रक्रिया का सेटिंग करते वक्त खुरदरापन नापने के साधन का प्रयोग करें। खुरदरेपन का अचूक मूल्य हासिल हो जाने पर अभियंता को गुणवत्ता पर ध्यान केंद्रित करने, प्रक्रिया की उत्पादकता बढ़ाने और उसे किफायती बनाने में मदद हो जाती है।
0 9359104060
राजेश म्हारोलकरजी यांत्रिकी अभियंता हैं। आप श्रीनिवास इंजीनीयरिंग ऑटो कंपोनंट्स प्रा.लि. के संचालक हैं और सलाहगार के रूप में भी काम करते हैं। यह कंपनी ट्रैक्टर और ऑटोमोटिव उद्योगों को आयर्न कास्टिंग और प्रिसिजन मशीनिंग की सेवा प्रदान करती है।