उत्पादन की गुणवत्ता के मानकों का जहाँ बारीकी से पालन करना आवश्यक होता है ऐसी किसी भी औद्योगिक प्रणाली में संवेदक (सेन्सर) तथा स्मार्ट प्रणाली आज भी प्रासंगिक और महत्वपूर्ण है। स्मार्ट प्रणाली को किसी भी उत्पादन प्रणाली में आसानी से समा लेने के लिए नवीनतापूर्ण उपाय एवं योजनाओं की जरूरत होती है। मेट्रॉलॉजी एक ऐसा साधन है जो किसी भी नई प्रणाली को सुस्थापित करने में, बड़े पैमाने की उत्पादन प्रणाली के संनियंत्रण (मॉनिटरिंग) तथा उत्पादन की गुणवत्ता एवं सुरक्षितता सुनिश्चित करने हेतु आवश्यक विश्लेषण तथा प्रणाली के इष्टतमीकरण (ऑप्टिमाइज़ेशन) में मदद करता है। इससे उत्पादक अपनी प्रक्रियाओं पर कड़ा नियंत्रण रख सकते हैं।
गुणवत्ता तथा आवर्तन काल, दोनों ही औद्योगिक उत्पादन प्रणाली की लाभकारिता निश्चित करने वाले निर्णायक घटक होते हैं। इन दोनों को आसानी से हासिल करने में तेज़, स्वचालित तथा पूर्वसिध्द जांच प्रणाली के इस्तेमाल से प्राप्त किए गुणवत्ता आश्वासन का बहुत बड़ा योगदान होता है। शून्य त्रुटि दर आवश्यक बनने के कारण, उत्पादित पुर्जों की 100% जांच आजकल बहुत ही सामान्य जरूरत बन गई है। वस्तुओं के बड़े पैमाने पर एवं निरंतर उत्पादन के लिए, संपर्करहित मापन तंत्र वाली इनलाइन मेट्रॉलॉजी एक अच्छा विकल्प है। चूंकि मापन द्वारा प्राप्त परिणामों का फीडबैक सुधारात्मक उपायों के लिए उत्पादन प्रणाली में सीधा पहुंचता है, ऐसी जांच प्रणाली कार्यक्षम तथा स्पर्धात्मक उत्पादन प्रक्रिया का अविभाज्य हिस्सा मानी जाती है। रफ्तार, मापन की अचूकता, विश्वसनीयता तथा मापन के योग्य नियम इनलाइन ऑप्टिकल मापन प्रणाली की मुख्य विशेषताएं हैं।
इनलाइन मापन प्रणाली
वस्तुनिर्माण के परिवेश में, मेट्रॉलॉजी को मशीन के साथ एकात्म (इंटिग्रेट) किया जाता है। पारंपरिक उत्पादन में यंत्रभाग क्लैंप से बाहर निकाल कर जांच हेतु मशीन से दूर ले जाया जाता है। जांच के लिए स्वतंत्र कक्ष होता है। एकात्मिक परिवेश में वस्तु की इनलाइन जांच की जाती है।
ऑप्टिकल मेट्रॉलॉजी प्रणाली का डिज़ाइन, काफी हद तक अैप्लिकेशन पर निर्भर करता है। सभी तरह की ऑप्टिकल मेट्रॉलॉजी प्रणालियों में लेन्स, प्रतिमा संवेदक (इमेज सेन्सर) तथा कैमरा ये मुख्य अंग होते है। हर अंग का असर, प्रणाली की कार्यक्षमता के परिमाणात्मक (क्वांटिटेटिव) तथा गुणात्मक (क्वालिटेटिव) पहलुओं पर पड़ता है। मापन की अचूकता और कार्यवस्तु को प्रणाली में दर्ज करने के लिए आवश्यक समय को परिमाणात्मक पैरामीटर माना जाता है। इसके अलावा, कार्यवस्तु स्थिर है या गतिशील (जैसे, कन्वेयर पर घूम रही है या रोबो द्वारा संचालित है) इसका भी ध्यान रखना जरूरी होता है।
मापन प्रणाली की विश्वसनीयता है गुणात्मक पैरामीटर। बदलते तापमान और प्रकाश जैसी बदलती परिवेशी परिस्थितियों में भी मापन के नतीजे संगत तथा पुनरावृत्तिक्षम होना जरूरी है। हर औद्योगिक समस्या एक अलग ही चुनौती होती है। समस्या का पूरा निदान करने की कोई मानक कार्यप्रणाली न होने के कारण हर समस्या का स्वतंत्र रूप से विचार करना पड़ता है।
· उचित हार्डवेयर
· प्रकाश व्यवस्था
· पुर्जों के संचलन की प्रणाली
· योग्य प्रीप्रोसेसिंग और पोस्टप्रोसेसिंग अल्गोरिदम चुनने से आरंभ कर के, हर अैप्लिकेशन के लिए सुयोग्य जांच प्रणाली की रचना करनी होती है।
हर पहलू का महत्व अधोरेखांकित करने हेतु आगे कुछ उदाहरण दिए हैं। ये प्रणालियां सेंट्रल मैन्युफैक्चरिंग टेक्नॉलॉजी इन्स्टिट्यूट (CMTI) में, उद्योगों की जरूरतें ध्यान में रखते हुए विकसित की गई हैं।
गुणवत्ता के लिए त्रुटि जांच प्रणाली
रिटेनिंग बुश
उद्देश्य : वाहन उद्योग में, सुरक्षा की दृष्टि से महत्त्वपूर्ण होने वाले, प्लैस्टिक इंजेक्शन मोल्डिंग पध्दति से उत्पादित 'रिटेनिंग बुश' (चित्र क्र. 1) में त्रुटियाँ खोज कर उनका वर्गीकरण करना जरूरी था। साथ ही, जरूरी तथा महत्वपूर्ण परिमाणों का स्वचालित मापन नमूने के आधार पर करना और उसे जांच में सम्मिलित करना भी आवश्यक था।
चुनौती : पुर्जे का स्थान स्थिर न होने के कारण उसका संचलन चुनौतिपूर्ण था।
उपाय : पुर्जे को जांचस्थानक तक निश्चित अभिमुखता (ओरिएंटेशन) से भेजने हेतु, लीनियर फीडर के बाद एक योग्य वायब्रेटरी फीडर (चित्र क्र. 2) लगाया। साथ ही दो कैमरों का प्रयोग कर के जांच प्रणाली विकसित की। पहला कैमरा ऊपरी पृष्ठ की त्रुटियां (उदाहरण के लिए, भरे हुए छिद्र, अत्यधिक फ्लैश, उड़ा हुआ रंग, आदि) परखने के लिए तथा दूसरा कैमरा साइड व्यू में दिखने वाली त्रुटियों को (टूटा या गायब पैर आदि) खोजने के लिए लगाया। दोनों कैमरे 200 fps फ्रेम प्रति सेकंड) दर के और 0.3 MP रिजोल्यूशन के हैं। जांच में कुछ महत्वपूर्ण परिमाणों का मापन भी समाविष्ट था।
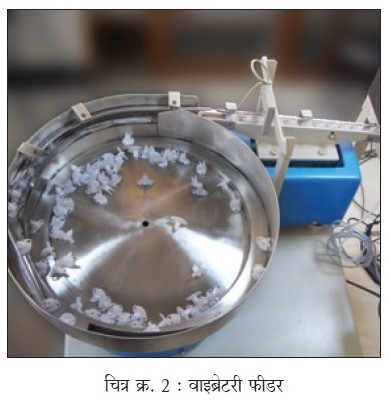
उपरोक्त उपायों के कारण (चित्र क्र. 3) प्रति सेकंड 3 पुर्जों की जांच (चित्र क्र. 4) करना संभव हो पाया। जांच दर, जांच प्रणाली द्वारा नहीं बल्कि यांत्रिकी फीडर के कारण मर्यादित हुआ था। पुर्जा स्थिर स्थिति में जकड़ने (लॉक किया जाने) के बाद उसे प्रॉक्सिमिटी सेन्सर द्वारा संवेदित किया जाता है और तुरंत ही कैमरा उसकी टॉप व्यू तथा साइड व्यू तस्वीरें दर्ज कर लेता है। विजन कंट्रोलर से प्राप्त संकेत के अनुसार सोलेनॉइड चलित न्यूमैटिक वॉल्व द्वारा पुर्जे को स्वीकृत अथवा अस्वीकृत कर के, तदनुसार दो भिन्न बिन में ड़ाला जाता है।
ड्रिपर
उद्देश्य : ड्रिपर (चित्र क्र. 5) के उत्पादन दर से मिलती जुलती स्वचालित जांच प्रणाली विकसित करना।
चुनौती : उत्पादन दर से मेल रखने हेतु, 600 पुर्जे प्रति मिनट का जांच दर जरूरी था।
उपाय : एरिया स्कैन कैमरा का प्रयोग कर के तेजी से हिलती कार्यवस्तु की स्थिर तथा परिशुध्द तस्वीर पाने हेतु हमें अल्प एक्स्पोजर काल, उच्चगति शटरिंग, प्रकाश का शक्तिशाली स्रोत, सिंक्रोनाइजिंग में स्ट्रोब इग्नाइटिंग आदि पहलुओं पर काम करना होता है। इन सब की वजह से प्रणाली और जटिल बनती है और अच्छी तस्वीर ले पाना प्रायः मुश्किल और महंगा मामला हो जाता है।
इसके विपरीत, उत्पाद से समानांतर स्थित लाइन स्कैन कैमरे, उच्च गति से संचलित कार्यवस्तु के चित्रांकन में बहुत ही कारगर होते हैं। उदाहरण के लिए कपड़े की जांच, वेब जांच, प्रिंटेड सर्किट बोर्ड की जांच, खाद्यवस्तुओं की गुणवत्ता जांच, विशिष्ट गठन (टेक्श्चर) वाले पृष्ठभागों में त्रुटियाँ खोजना आदि।
प्रस्तावित उपायों में, लाइन स्कैन कैमरा का प्रयोग कर के उच्च गति जांच प्रणाली (चित्र क्र. 6) दी गई है। इससे 600 भाग प्रति मिनट के दर से ड्रिपर की परिधी पर मौजूद विभिन्न त्रुटियों की जांच की जाती है। आवश्यक जांच दर पाने के लिए समान सेटअप में एक ही समय 2 ड्रिपर, प्रणाली में ड़ाल कर जांच की जाती है।
मापन प्रणाली
बोन स्क्रू
उद्देश्य : शल्यचिकित्सा में प्रयुक्त स्क्रू (चित्र क्र. 7) की अनेक महत्वपूर्ण मितीय विशेषताएं नापने के लिए स्वचालित विजन आधारित जांच प्रणाली विकसित करना।
चुनौती : जिस स्क्रू की जांच करनी हो उसकी विविधता। आवश्यक पैरामीटर की जांच करने के लिए हड्डियों के स्क्रू की हर तरफ से तस्वीरें खींचना आवश्यक था। साथ ही टॉप व्यू में अलग अलग प्रतलों में स्थित विशेषताएं होने की वजह से विभिन्न फोकस पोजिशन की आवश्यकता थी। जांच में अचूकता अत्यावश्यक थी।
उपाय : इसके लिए दो कैमरा सेटअप (चित्र क्र. 8 और 9) का प्रयोग किया गया। एक में, थ्रेड प्रोफाइल पता करने के लिए, सटीकता से समानांतर किए गए बैकलाइट का प्रयोग किया, तो दूसरे में जूम लेन्स का उपयोग कर के टॉप व्यू की विभिन्न विशेषताएं (जैसे कि इनसर्कल, अलग अलग फ्लैट की चौड़ाई तथा बाहरी वृत्त आदि) का चित्रण किया गया।
विजन तकनीक द्वारा मशीन टूल में उष्मीय त्रुटि की भरपाई
उद्देश्य : उष्मा के कारण पैदा हुई त्रुटियां मशीन टूल में देखे जाने वाले दोषों का मुख्य स्रोत हैं, जिससे उत्पादित पुर्जों में भी त्रुटियां पैदा होती हैं। एक अनुसंधान में देखा गया है कि यंत्रण की त्रुटियों में से 70% त्रुटियों का कारण हो सकता है उष्मीय बदलाव। इसलिए, मशीन में उष्मीय त्रुटियों के कारण पैदा होने वाला मशीन टूल स्पिंडल ऑफसेट खोजने और उसे सुधारने की पध्दति तथा प्रणाली की आवश्यकता है। ये प्रणाली आसान, कम सेटअप समय वाली, निर्दोष, तथा बहुआयामी होना अपेक्षित है। उष्मीय बदलावों के कारण भले ही विरूपण होता रहे, फिर भी 'स्पिंडल' एवं 'टेबल' के बीच का स्थानविषयक विशेष संबंध बनाया रखने का हमारा उद्देश्य था।
मशीन टूल डिजाइन करते समय आगे दिेए गए पहलुओं पर विचार किया जाता है।
योग्य शीतक प्रणाली का प्रयोग कम घर्षण वाले बेरिंग के इस्तेमाल बेरिंग का प्रीलोड ,स्पिंडल बेरिंग के लिए एयर-ऑईल रोगन का इस्तेमाल , वैकल्पिक सामग्री उपयोग में ला कर डिजाइनर उष्मीय बदलावों का प्रभाव न्यूनतम रखने का प्रयास करना लेकिन उष्मा का प्रभाव अब भी काफी सुस्पष्ट है। दुनियाभर के विशेषज्ञों ने यह त्रुटि घटाने की तकनीक प्रस्तावित की हैं। सामान्यतया, उष्मीय त्रुटियों को सुधारने के दो मार्ग देखे गए हैं - निष्क्रिय दुरुस्ती अथवा सक्रिय दमन (सप्रेशन)। निष्क्रिय दुरुस्ती में उष्मीय त्रुटि को मशीन टूल के थर्मल एरर प्रेडिक्शन मॉडल द्वारा सुधारा जाता है और सक्रिय दमन में उष्मीय त्रुटि न्यूनतम रखने या नियंत्रित करने का प्रबंध मशीन टूल के डिजाइन में ही किया जाता है।
चुनौती : मशीन के कंपन के कारण कैमरा तथा ऑप्टिक्स के नापों में गलतियां होती हैं। साथ ही, यंत्रण के दौरान निर्मित प्रतिकूल परिवेश से उन्हें सुरक्षित रखना भी जरूरी होता है।
उपाय : मशीन के निरंतर चलने से पैदा होने वाली उष्मा की वजह से स्पिंडल की अक्षरेखा झुक जाती है। इसे दृश्य रूप में दर्ज करने के लिए, उष्मीय त्रुटि मापन की एक अपूर्व संपर्करहित एवं कैमेरा वाली पध्दति विकसित की गई।
चित्र क्र. 10 में दर्शाएनुसार कैमेरा, स्पिंडल हाउसिंग पर स्थित होता है। मशीन बेड पर दृढ़ता से स्थापित निश्चित आकृति वाली ठंड़ी वस्तु का प्रयोग, स्पिंडल की अक्षरेखा का संदर्भस्थान दर्ज करने हेतु किया जाता है। फिर मशीन को लगातार चलाया जाता है। हर 2 घंटे बाद मशीन रोक कर, उस वस्तु के संदर्भ में स्पिंडल की अक्षरेखा का विचलन कैमरा द्वारा नापा जाता है। मशीन नियंत्रक में टूल ऑफसेट सेटिंग का प्रयोग कर के स्वचालित रूप से थर्मल त्रुटियां सुधारने के लिए X और Y अक्ष में दर्ज किए हुए रेखीय ऑफसेट का उपयोग किया जाता है।
निष्कर्ष
स्मार्ट कारखानों की कल्पना भले नई ना हो, पर उसमें निरंतर उन्नति हो रही है। भविष्यलक्षी काम करने वाले कारखाने औद्योगिक क्रांति लाएंगे, इसमें कोई शक नहीं है। ऑप्टिकल मेट्रॉलॉजी प्रणाली तथा कारखानों में रोबो के बढ़ते प्रयोग के साथ, हाथों से किए जाने वाले पुनरावृत्त कामों का महत्व घटता जा रहा है। मेट्रॉलॉजी मार्केटसंबंधी विभिन्न औद्योगिक अैप्लिकेशन में स्वचालन ही मुख्य प्रेरणा होना अपेक्षित है। उपरोक्त सारे अनुसंधान कार्य में मेरी टीम के दीपा आर., मधुसूदन, वी. कविता, जे. प्रद्युम्न और एस. हर्ष इन सहकारियों ने सहयोग किया है।