औद्योगिक क्षेत्र में पुर्जे बनाते समय अलग अलग धातुओं और मशीनों पर, विविध कटिंग टूल की मदद से विभिन्न कार्यपध्दतियों का प्रयोग किया जाता है। परंतु जब तक उत्पादित पुर्जा योग्य जांच के स्वीकृति परीक्षणों से परख कर न निकले तब तक उसे पूर्णता प्राप्त नहीं होती। अक्सर देखा जाता है कि अपेक्षित पैरामीटर के मापन हेतु सुयोग्य उपकरण या कार्यपध्दति न चुनने के कारण जांच में तो पुर्जा स्वीकृत हो सकता है, परंतु असल में जोड़ते समय वह अस्वीकृत हो सकता है। इसलिए व्यापार में गुणवत्ता और लाभकारिता इन दो मानकों पर टिके रहने के लिए मापन उपकरण तथा मापन कार्यपध्दति, दोनों को यंत्रण की कार्यपध्दति जितनी ही सावधानी से चुनना जरूरी है।
हमारी 'अैक्युरेट' कंपनी ने पिछले लगभग 5 दशकों में, मापन के क्षेत्र में भारतीय उद्योगों के लिए कई आधुनिक उपकरणों का विकास कर के उन्हें बाजार में सफलतापूर्वक प्रस्थापित किया है। इस कालावधि में सामने आई चुनौतियों का सामना करते समय हमें मिले अनुभव तथा उस दौरान बने उपकरणों के निर्माण एवं विकास की यात्रा, इस लेख के माध्यम से पाठकों तक पहुंचाने का यह प्रयास है। इस अंक में हम वर्तमान काल से प्रासंगिक होने वाली कोऑर्डिनेट मेजरिंग मशीन (सी.एम.एम.) के बारे में जानेंगे। उससे पहले, सी.एम.एम. के निर्माण से पहले प्रचलित जांच पध्दतियों पर एक नजर डालेंगे।
स्टील की मापन पट्टी (स्केल) या उससे अचूक मापन करने वाले वर्नियर कैलिपर/डेप्थ डायल (चित्र क्र. 1) जैसे उपकरणों से सभी परिचित हैं। ये उपकरण एक अक्षरेखा में स्थित रेखीय परिमाणों का मापन करते हैं। यदि हम X,Y एवं Z इन तीनों अक्षों में मापन करने वाले उपकरण की कल्पना करें, तो सी.एम.एम. लगभग वैसी ही होगी।
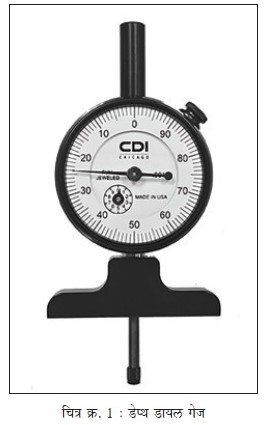
अधिकांश उपकरणों में मापन करते समय उपकरण का विशिष्ट पृष्ठ पुर्जे को स्पर्श करता है। इस पध्दति को 'कॉन्टैक्ट टाइप' मापन पध्दति कहते हैं। कभी कभी इस पध्दति से मिलने वाले परिणाम पूरी तरह अचूक और निरंतर नहीं होते हैं, उनकी भी कुछ मर्यादाएं हो सकती हैं। इसका मुख्य कारण है इसमें निहित मानवीय हस्तक्षेप। यह उपकरणों के डायल पर दिए गए दबाव में आने वाले फर्क के कारण आ सकता है या पुर्जों का संदर्भ लेते समय (रेफरन्स लेना या ट्रू करना) हो सकता है । इसके अलावा ऐसे उपकरणों में जोडे हुए पुर्जे एक दूसरे पर सरकते हैं या दांतों में घूमते हैं। ऐसे समुच्चनों में उपस्थित रिलेटिव बैकलैश के कारण भी रीडिंग में फर्क देखा जा सकता है। सुई (पॉइंटर) से रीडिंग दर्शाने वाले (अैनालॉग टाइप) उपकरणों में यह फर्क अधिक पाया जाता है। यह फर्क हटाने हेतु डिजिटल उपकरणों का विकास हुआ।
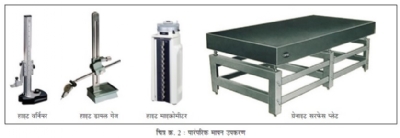
क्लिष्ट एवं जटिल पुर्जों के कुछ नाप, उस पुर्जे को मशीन से नीचे उतार कर, ग्रेनाइट की सरफेस प्लेट पर रख कर लेने पड़ते हैँ (चित्र क्र. 2)। उदाहरण के लिए अक्षों की समकेंद्रीयता (कॉन्सेंट्रिसिटी), अक्षों की कोणीय स्थिति (ऐंग्यूलर पोज़िशन), पृष्ठ की गोलाई (राउंडनेस) अथवा समतलता (फ्लैटनेस) आदि। इस प्रकार की जांच पध्दति को 'फर्स्ट प्रिन्सिपल' द्वारा जांच करना कहते हैं।
सरफेस प्लेट पर की जाने वाली मापन पध्दति में मुख्य रूप से दो तरह की मर्यादाएं देखी गई। पहली यह है कि जांच के दौरान पुर्जे का रेफरन्स लेने या उसे ट्रू करने में बहुत समय जाता था। इस प्रकार, कोई सेटिंग बदलने के बाद उत्पादित पुर्जा जांच कर वह ड्रॉइंग के अनुसार है या नहीं यह सुनिश्चित करने के लिए बहुत समय लगता था। यंत्रण के बाद पुर्जे की जांच और स्वीकृति होने तक, सी.एन.सी. जैसी महंगी मशीन बंद रखना स्पष्ट ही किफायती नहीं था। इसके अलावा मानवीय गलतियों के कारण भी जांच के नतीजों में निरंतरता नहीं मिलती थी।
शुरू में इस पर यह हल निकाला गया कि सी.एन.सी. मशीन पर पुर्जे का यंत्रण पूरा होने पर, उसी मशीन पर ही उसकी जांच की जाए। इस हेतु निश्चित स्वरूप की कुछ आज्ञावलियां भी बनाई गईं। परंतु इस हल में भी, सी.एन.सी. मशीन रोक कर जांच की व्यवस्था की होने के कारण अपेक्षित उत्पादकता नहीं मिल रही थी। साथ ही, मशीन के कुछ वर्षों के उपयोग के बाद, जांच का स्तर भी घटता जाता था।
सी.एम.एम. की जरूरत क्यों महसूस हुई यह जानने हेतु हम एक पुर्जे का उदाहरण विस्तार से देखेंगे। हमारे एक ग्राहक से प्राप्त इंजन सिलिंडर हेड के यंत्रचित्र के कुछ हिस्से चित्र क्र. 3 में दर्शाए हैं। इसमें दर्शाए गए कुछ महत्वपूर्ण मापदंड़ों पर जांच के लिए योग्य उपकरण वें हमसे चाहते थे। चित्र में दर्शाए वाल्व गाइड बोर तथा वाल्व सीट का यंत्रण, इस पुर्जे का सबसे अहम् हिस्सा है। इन दोनों का, अन्य पृष्ठभागों से होने वाला संबंध भी उतना ही सटीक एवं निर्दोष होना इंजन के कार्यप्रदर्शन में महत्वपूर्ण है। इसके मद्देनज़र कुछ जरूरी पैरामीटर नीचे दिए हैं तथा चित्र क्र. 3 में अलग रंग से दर्शाए हैं।
सिलिंडर हेड में नापे जाने वाले कुछ महत्वपूर्ण पैरामीटर
1. रेस्टिंग पृष्ठ की समतलता -C
2. वाल्व गाइड बोर तथा वाल्व सीट बोर की अलग अलग सिलिंड्रिसिटी, ओवेलिटी
3. वाल्व गाइड बोर तथा वाल्व सीट बोर के अक्षों की, रेस्टिंग पृष्ठ से होने वाली कोणीय स्थिति (अैंग्यूलर पोजिशन)
4. वाल्व गाइड बोर तथा वाल्व सीट बोर की एक दूसरे से होने वाली समकेंद्रीयता (कॉन्सेंट्रिसिटी)। यह पैरामीटर इतना महत्वपूर्ण है कि सिलिंडर पर वाल्व की असेंब्ली करने के बाद, कुछ सेकंड के लिए, डीजल का प्रयोग कर के रिसाव की जांच (लीकेज टेस्टिंग) की जाती है।
सरफेस प्लेट पर ये पैरामीटर, फर्स्ट प्रिन्सिपल द्वारा जांचने में समय तो ज्यादा लगता ही था, पर इसमें होने वाली संभाव्य मानवीय गलतियों के कारण विश्वसनीय विवरण मिलने की संभावना भी कम थी। इसी मर्यादा के चलते, सी.एम.एम. जैसी जांच मशीन का कदम दर कदम विकास होता गया।
सी.एम.एम. की वर्तमान रचना की विशेषताएं
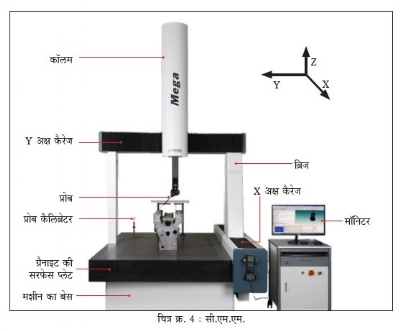
चित्र क्र. 4 में साधारणतया 500 से 800 मिमि. लंबाई, चौड़ाई तथा ऊंचाई होने वाले पुर्जों की जांच के लिए प्रयुक्त सी.एम.एम. की रचना दिखाई गई है। जांच के लिए प्रस्तुत पुर्जा स्थिर रखने के लिए ग्रेनाइट की सरफेस प्लेट मजबूत नीव (बेस) पर रखी जाती है। X अक्ष पर अत्यंत सुलभ तथा बिना कंपन संचलन पाने हेतु एयर बेरिंग पर चलने वाला एक ब्रिज लगाया जाता है। मशीन के हिलते हिस्से घिस कर हुई क्षति का असर, उसकी अचूकता पर ना हो इसलिए ऐसे हिस्सों तथा ग्रेनाइट गाइडवे के बीच निश्चित दबाव से वायु का निरंतर बहाव बनाया रखा जाता है। इससे मशीन की आयु बढ़ती है। Y अक्ष में संचलन के लिए ब्रिज पर एक कैरेज बिठाया होता है। खड़े अक्ष में ऊपर नीचे संचलन हेतु कॉलम दिया होता है। कॉन्टैक्ट टाइप मापन के लिए कॉलम के रैम पर एक प्रोब स्थित होता है। ये प्रोब X, Y एवं Z तीनों अक्षों में आवश्यकतानुसार आगे पीछे हिलाया जा सकता है। यह संचलन जॉयस्टिक की मदद से हाथों से अथवा स्वचालित रूप से भी किया जा सकता है। यदि बार बार एक ही तरह के पुर्जों की जांच करनी हो, तो मशीन में पहले से ही आज्ञावली शामिल कर के, यह प्रक्रिया स्वचालित बनाई जा सकती है।
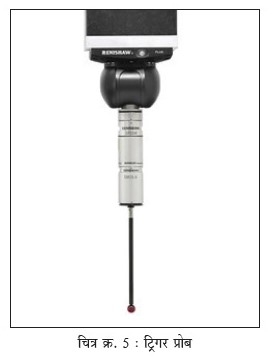
अधिकांश प्रोब, टच ट्रिगर तरह के होते हैं। ये प्रोब (चित्र क्र. 5) जब पुर्जे के अपेक्षित पृष्ठ को स्पर्श करते हैं, तब पूर्वनिश्चित दबाव के अनुसार सेन्सर द्वारा यह नाप प्रोसेसर में दर्ज किया जाता है। परंतु जब पुर्जे के कुछ पृष्ठ का आकार नापना होता है, (जैसे, इंपेलर के वेन की प्रोफाइल) तब स्कैनिंग प्रोब (चित्र क्र. 6 एवं 7) का प्रयोग होता है। ये प्रोब आज्ञानुसार दी गई दिशा में पुर्जे से संपर्क बना कर अनगिनत निरीक्षण दर्ज करते हैं और उस प्रोफाइल का निश्चित आकार अचूकता से दर्शाते हैं।
जांच के समय प्रोब का स्पर्शबिंदु पुर्जे के कौनसे हिस्से से सटना जरूरी है, यह बात पुर्जे की रचना पर निर्भर रहती है। इसी लिए विभिन्न आकार एवं लंबाई के प्रोब (चित्र क्र. 8) मशीन के साथ उपलब्ध करवाए जाते हैं। प्रोब हेड पर, प्रोब हाथ से या स्वचालित रूप से बदला जा सकता है। बहुत नाजुक होने के कारण प्रोब का संचलन बहुत सावधानी से करना पड़ता है, इसलिए ग्रेनाइट प्लेट पर आवश्यकतानुसार प्रोब के पार्किंग की भी व्यवस्था की जाती है। यह व्यवस्था स्वचालित रूप से प्रोब बदलते समय (चित्र क्र. 9) काम आती है।
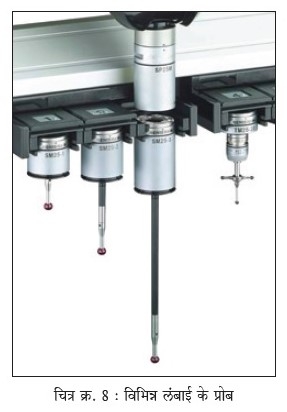
सी.एम.एम. पर जांचा जाने वाला पहला पुर्जा, X या Y अक्ष से समानांतर रखा जाता है। उसकी स्थिरता सुनिश्चित की जाती है। सी.एम.एम. में अलग अलग पैरामीटर नापने हेतु विभिन्न विकल्प (प्रोग्रैम) उपलब्ध होते हैं। जिस पैरामीटर का मापन करना हो, उसकी आज्ञावली चुन कर उसके अनुसार योग्य प्रोब का चयन करना होता है। शुरुआत में हाथ से नियंत्रित कर के प्रोब को पुर्जे के पृष्ठ के समीप लाया जाता है। अब आज्ञावली के अनुसार सावधानी से स्पर्श कर के हलका सा दबाव दिया जाता है। नियत दबाव के बाद निरीक्षण को सेन्स कर के प्रोसेसर में दर्ज किया जाता है। ऐसे अनेक अपेक्षित निरीक्षणों के संच के आधार पर हमें उस पैरामीटर का निश्चित नाप (वैल्यू) मिलता है। साथ ही ड्रॉइंग में दिए टॉलरन्स की तुलना में वह स्वीकृत है या अस्वीकृत यह भी पता चलता है। इसकी प्रिंट निकाल कर प्रतिवेदन संग्रहित किया जाता है। उदाहरण के तौर पर, सिलिंडर हेड का प्रतिवेदन चित्र क्र. 10 में दिया गया है।
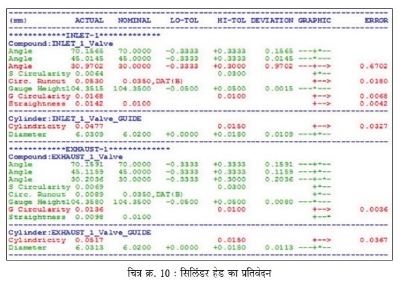
जांचे जाने वाले पुर्जे का आकार, उसके आयाम तथा जांच की क्लिष्टता के अनुसार हम हमारे सी.एम.एम. उत्पादनों को संशोधित करते गए। इस काम में हमारे साथ, प्रोबसंबंधी संशोधन में 'रेनिशॉ' कंपनी का योगदान अमूल्य रहा है। जटिल तथा अचूक पुर्जों के यंत्रण करने वाले लघु तथा मध्यम उद्योगों के पास भी आज सी.एम.एम. का होना एक जरूरत बन गई है। सी.एम.एम. की शृंखला में आज हमारे कई मॉडल बाजार में उपलब्ध हैं। उनमें से कुछ मॉडल चित्र क्र. 11, 12, 13 में दर्शाए गए हैं।
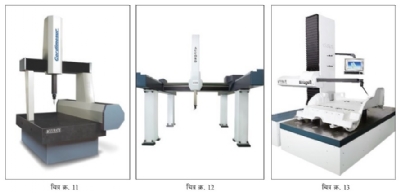
देखा जाए तो सी.एम.एम. तकनीक सबसे पहले 1965 के आसपास यूरप में विकसित हुई। आगे चल कर यूके, इटली, जर्मनी जैसे देशों ने इसमें निपुणता हासिल की। हमने सी.एम.एम. बनाने का विचार 1985 के आसपास पहली बार किया। प्रत्यक्ष उत्पादन 1991 के आसपास शुरू हुआ। मशीन बनने के शुरुआती दौर में ये महंगी होने की वजह से इनकी संख्या कम ही हुआ करती थी। इस स्थिति में मशीन का कवर खोल कर उसके अंदरूनी पुर्जों का बारीकी से निरीक्षण कर पाना मुश्किल ही था। ऐसे में इस तरह की मशीनें हमारी कंपनी में बनाने के लिए कई पुर्जों की कल्पना करना, या एयर बेरिंग जैसे पुर्जों के लिए, उनके बेकार हो चुके पुर्जों की रिवर्स इंजीनीयरिंग करने के अलावा हमारे पास कोई चारा नहीं था।
दूसरी चुनौती थी इलेक्ट्रॉनिक सेन्सर जैसे पुर्जों का विकास। उस जमाने में ऐसे पुर्जों पर 100% आयात शुल्क (इंपोर्ट ड्यूटी) होने के कारण हमें पहली मशीन बनाने में 10 लाख रुपये लागत आई। इस मशीन की अचूकता जांचने के लिए आवश्यक मशीन भी अत्यधिक महंगी होने के कारण हमने कुछ मशीन टूल उत्पादकों के पास पहले से उपलब्ध मशीनें इस्तेमाल कर के ये जरूरत पूरी की। भारत में संगणक का विकास बस शुरू ही हुआ था। हमने मशीन में प्रयुक्त गणितीय समीकरणों के लिए पहले संगणक आधारित माइक्रोप्रोसेसर प्रोग्राम का प्रयोग कर के इस चुनौती का बखूबी सामना किया। करीबन 3 वर्षों की कड़ी मेहनत से हमने पहली नमूना मशीन बनाई। बेंगलुरु की 'धातु निर्माण' कंपनी ने हम पर भरोसा दिखा कर पहली मशीन हमसे खरीदी और इस तरह हमारा सी.एम.एम. मशीन उत्पादन का सिलसिला 1991-92 में शुरू हुआ।
क्या सी.एम.एम. जैसी अत्याधुनिक तथा कीमती मशीन के रखरखाव का खर्चा उठाना संभव होगा? संभवतः यह डर भी कुछ उत्पादकों के मन में होता है। मशीन की कीमत ही जब इतनी ज्यादा थी, तब उसके पुर्जे (स्पेयर) भी उतने ही महंगे होंगे, ऐसा भी कई उद्यमियों ने हमसे कहा था। परंतु यह एक गलतफहमी थी। यह मशीन मुख्यतः एयर बेरिंग पर चलती है, जिस कारण इसमें एक दूसरे पर घिस कर क्षति होने वाले कोई भी पुर्जे नहीं हैं और इसलिए उन्हें बार बार बदलना भी नहीं पड़ता। परंतु समय समय पर मशीन का कैलिब्रेशन कर के उसकी अचूकता बनाई रखना जरूरी होता है। यदि ग्राहक हमारे साथ ए.एम.सी. (अैन्युअल मेंटेनन्स कॉन्ट्रैक्ट) बनाते हैं तो इस कैलिब्रेशन की सारी जिम्मेदारी हम उठाते हैं।
इस दौरान यदि इलेक्ट्रॉनिक भाग बदलने पड़ें तो उनका कुछ खर्चा होता है। पर वह परिस्थितिनुसार बदलता रहता है। उसी तरह इलेक्ट्रॉनिक प्रोब पर स्थित स्टाइलस भी कभी-कभी बदलना पड़ता है। परंतु उसका खर्चा दो से पांच हजार रुपयों के बीच होता है।
कई चुनौतियों का सामना करते हुए विदेशी उत्पादों के समकक्ष उपकरण हम उपलब्ध करवा रहे हैं। साथ ही हमारे उत्पाद विदेशी उत्पादों की तुलना में 20-40% सस्ते हैं। इन दोनों बातों पर हमें गर्व है।