वस्त्र उद्योग में विभिन्न प्रकार की मशीनें इस्तेमाल की जाती हैं। इनके निर्माण में अलॉइ स्टील, स्टेनलेस स्टील, अैल्युमिनियम, फोर्ज्ड स्टील आदि अलग अलग मटीरीयल का उपयोग किया जाता है। ऐसी मशीन के अधिकतर सभी भाग निरंतर कार्यरत रहते हैं। इसलिए इस्तेमाल होने वाले मटीरीयल घिसाव प्रतिरोधी होना तथा उनकी आयु अधिक होना जरूरी होता है। चूंकि मशीन के अन्य स्थिर भाग मजबूत होना आवश्यक है, वे फोर्ज्ड स्टील या कास्टिंग से बनाए होते हैं।
हमारे एक ग्राहक वस्त्र उद्योग में जरूरी होने वाले पुर्जों के उत्पादक है। फिलहाल वाहन उद्योग के लिए होने वाले पुर्जों का उत्पादन कम मात्रा में लिया जा रहा है। लेकिन विक्रेता या आपूर्तिकर्ताओं को अपनी मशीनें चलाने की जरूरत होती है, इसलिए वे अब वाहन क्षेत्र के बजाय अन्य उद्योगों के बारे में सोच रहे हैं। वस्त्र उद्योग में भी मशीन की वृद्धि उल्लेखनीय है। आपूर्तिकर्ता, उद्योग के लिए लगने वाले एक ही प्रकार के पुर्जों पर निर्भर नहीं रहना चाहते। यह भाग निरंतर नहीं बनते, उन्हें विभिन्न बैच में बनाया जाता है।
हमारे ग्राहक वस्त्र उद्योग में आवश्यक हब, पिन, शाफ्ट तथा हाउसिंग जैसे पुर्जों के उत्पादक हैं। इन पुर्जों में से हब, फोर्ज्ड स्टील से बनाया जाता है। यह पुर्जा विभिन्न आकारों एवं रुप में बनाए जाने के कारण अतिरिक्त मटीरीयल निकालने (स्टॉक रीमूवल) की मात्रा भी अधिक होती है, क्योंकि अंतिम पुर्जा, बेलनाकार कच्चे माल का यंत्रण कर के बनाना होता है।
मांग तथा मात्रा में अचानक हुई वृद्धि के कारण ग्राहक को उत्पादन क्षमता बढ़ाने में कठिनाई हो रही थी। साथ में इस पुर्जे का यंत्रण वर्तमान सेटअप में ही करना पड़ रहा था। इस हेतु टर्निंग, ड्रिलिंग, मिलिंग, उष्मोपचार, ग्राइंडिंग इन प्रक्रियाओं का इस्तेमाल किया जा रहा था। हमने इन सारी प्रक्रियाओं का अध्ययन किया। तब पता चला कि चूंकि फ्लैंज की बाजू पर अधिक यंत्रण करना होता है, यंत्रण का सबसे अधिक समय मिलिंग मशीन पर जा रहा था। दोनों बाजू पर होने वाला अधिक यंत्रण, चित्र क्र. 1 में दर्शाया है। साथ ही, मौजूदा प्रक्रिया में जरूरी पास की संख्या भी अधिक थी। इस संदर्भ में हमने मिलिंग का वर्तमान टूलिंग भी जांचा।
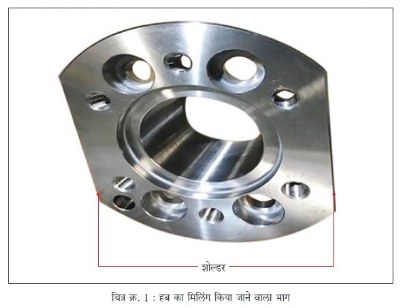
वर्तमान पद्धति में इस्तेमाल होने वाला इन्सर्ट, दो कोने वाला तथा 90° के कोण में प्रवेश करने वाला था। कटर का व्यास 32 मिमी. था और उसे 3 पॉकेट थे। काट की चौड़ाई 15 मिमी. थी। पैरामीटर और टूलिंग का विवरण तालिका क्र. 1 में दिया है। इसमें इन्सर्ट का तेजी से घिसाव हो रहा था और यंत्रण के दौरान वह टूटने की समस्या थी। यंत्रण के लिए समय भी अधिक लग रहा था। उत्पादन की मात्रा बढ़ने से, वर्तमान टूलिंग तथा प्रक्रिया पैरामीटर का उपयोग कर के ग्राहक जरूरी आपूर्ति नहीं कर पा रहे थे।
पुर्जा : हब
मटीरीयल : फोर्ज्ड स्टील
प्रक्रिया : फेस तथा शोल्डर मिलिंग
मशीन : वी.एम.सी. BT 40 टेपर
स्पिंडल की शक्ति : 12kW
मशीन का अधिकतम आर.पी.एम. : 4000
वर्तमान प्रक्रिया में समस्याएं
1. टूल की कम आयु : टूल का अधिक घिसाव
2. टूल की चिप निकलना
3. कम उत्पादन क्षमता
4. प्रति पुर्जा अधिक लागत
हमने प्रक्रिया तथा कार्यवस्तु का यंत्रण करने की पद्धति को जांचा। काट की चौड़ाई 15 मिमी. होने के कारण बड़े कटर का उपयोग करना आवश्यक नहीं था। समस्या यह थी कि इससे पुर्जे पर यंत्रण का भार पड़ रहा था। इसलिए हमने D32 कटर के बजाय D25 कटर के इस्तेमाल की सिफारिश की। साथ ही पहले इस्तेमाल किए 2 कोनों के इन्सर्ट के बजाय 6 कोनों के तथा अधिक सर्पिल (हेलिकल) इन्सर्ट के उपयोग का सुझाव दिया। इससे कंपन तथा यंत्रण का बल कम करने में हम कामयाब हुए। साथ ही 6 कोनों वाले इन्सर्ट की विशेष ज्यामिति से सरकन गति बढ़ा पाए। वर्तमान में पास की संख्या अधिक थी और काट की गहराई कम थी। लेकिन हमने देखा कि मशीन, काट की अधिक गहराई एवं अधिक सरकन गति सहने में सक्षम है। इसलिए काट की गहराई बढ़ा कर हमने पास की संख्या घटाई, जिससे आवर्तन समय कम करने और उत्पादन क्षमता बढ़ाने में मदद मिली।
हमने क्या सीखा? अ. मशीन की क्षमता जांचना और मशीन का इष्टतम इस्तेमाल करना।
ब. रफ मिलिंग में कम गति रख कर अधिक सरकन गति हासिल करने का प्रयास करना। इससे आवर्तन समय घटाने में मदद मिलेगी, टूल की आयु बढ़ेगी और उत्पादकता में सुधार होगा।
क. इन्सर्ट की श्रेणी का चयन (रफ मिलिंग के लिए अधिक टफ)
ड. टूल का मार्ग हमेशा फिक्श्चर क्लैंपिंग के बल की दिशा में होना चाहिए (डाउन मिलिंग)।
इ. अटकी चिप से बचने और बाधा विरहित यंत्रण हेतु उचित शीतक का इस्तेमाल करना।
सरकन गति और काट की गहराई बढ़ाने से हम उत्पादकता बढ़ाने में सफल हुए। आवर्तन समय लगभग 50% कम हुआ। साथ ही, पहले इस्तेमाल होने वाले 2 कोनों के इन्सर्ट के बजाय नए उपयोग किए इन्सर्ट में 6 कोने होने के कारण 4 अधिक कोनों का लाभ मिला। इससे हर शिफ्ट में इस्तेमाल किए जाने वाले इन्सर्ट की संख्या कम करने में मदद मिली।
पैरामीटर तथा टूलिंग में बदलाव से मिले लाभ
1. टूल की आयु 13% बढ़ी। (हर नग के लिए 100% से अधिक वृद्धी)
2. अतिरिक्त 4 कोने
3. उत्पादकता 50% बढ़ी।
4. प्रति पुर्जा लागत 56% कम हुई।
5. इन्सर्ट का इस्तेमाल कम हुआ।
6. D32 कटर और D25 कटर की कीमत में लगभग 15% फर्क है।
7. दो कोनों के इन्सर्ट की कीमत से, 6 कोनों के इन्सर्ट की कीमत दोगुनी है। यह कीमत अधिक होने पर भी हमने प्रति पुर्जे की लागत 4.6 रुपये कम की है। साथ ही इन्सर्ट का इस्तेमाल प्रति माह 675 से 260 तक घटा है, जिससे इन्सर्ट की इन्वेंटरी में उल्लेखनीय कटौती हुई है।