धातु काटने की प्रक्रिया में हमेशा ही उष्मा पैदा होती है। जितना अधिक यंत्रण, उतनी उष्मा की मात्रा अधिक होती है। हेवी ड्यूटी मेटल कटिंग में अत्यधिक उष्मा पैदा होती है। इसके अलावा धातु के छोटे कण, धूल, आदि भी उत्पन्न होते हैं (जिन्हें साथ मिल कर 'स्वार्फ' कहते हैं)। अतिरिक्त उष्मा के साथ उन्हें भी दूर करना अनिवार्य होता है। माना कि कुछ खास कामों में सूखा यंत्रण करना संभव होता है, फिर भी धातु यंत्रण के अधिकांश कामों में, विशेषतः हेवी ड्यूटी धातु यंत्रण में, मेटल कटिंग फ्लुइड का उपयोग करना ना केवल आवश्यक बल्कि अनिवार्य होता है। सावधानीपूर्वक चुना गया कटिंग फ्लुइड, टूल तथा कार्यवस्तु के संपर्कक्षेत्र (इंटरफेस) के घर्षण का गुणांक (कोइफिशंट ऑफ फ्रिक्शन) घटाता है।
कटिंग फ्लुइड के मुख्य कार्य
- स्नेहक के रूप में काम कर के घर्षण कम करना ताकि जहाँ यंत्रण हो रहा हो, उस टूल के अग्र पर उत्पन्न उष्मा घटाई जा सके।
- शीतक के रूप में काम करना, क्योंकि घर्षण से उत्पन्न उष्मा पूरी तरह तो टाली नहीं जा सकती।
- कार्यवस्तु की धातु की छोर (बिल्ट अप एज), टूल पर तैयार होने से रोकने हेतु अँटी वेल्ड के रूप में काम करना।
- ठंड़ा रहने के कारण टूल की आयु अपनेआप ही बढ़ती है तथा उष्मीय विरूपण कम हो जाता है। घर्षण गुणांक कम होने के कारण यंत्रण बल तथा बिजली की खपत भी कम हो जाती है। इससे पृष्ठीय फिनिश भी काफी हद तक सुधरता है और छोटा मोटा विरूपण हो तो वह दूर हो जाता है।
चिप-टूल-वर्क जोन में उत्पन्न होने वाली उष्मा कुछ हद तक हटा कर, कटिंग ऑईल उस हिस्से को ठंड़ा रखता है। साथ ही चिप-टूल संपर्कक्षेत्र में कम शक्ति के संयुक्तन बनने से वहाँ का घर्षण गुणांक कम होता है। प्रवाह के साथ चिप दूर ले जाना बहुत जरूरी होता है।
आदर्श कटिंग फ्लुइड की विशेषताएं
1. कम विस्कॉसिटी तथा कम आण्विक आकार (ताकि चिप-टूल इंटरफेस में उसका जल्दी प्रवेश हो सके)
2. कार्यवस्तु, टूल तथा मशीन फिक्श्चर को जंग लगने से लंबे समय तक बचा कर रखे।
कटिंग फ्लुइड प्रायः दो प्रकार के होते हैं
अ. जलयुक्त कटिंग फ्लुइड
आ. नीट कटिंग फ्लुइड
नीट कटिंग ऑईल
नीट कटिंग ऑईल का निर्माण, रसायनशास्त्र के मानवनिर्मित आधारभूत संयुग एस्टर का उपयोग कर के विकसित किया गया है। इसके उपयोग से पर्यावरणीय तथा कार्यक्षमता संबंधि दोनों लाभ होते हैं।
नीट कटिंग ऑईल सामान्यतः खनिज तेलों से बनता है और, उसमें बिना कुछ और मिलाए, उत्पादक से प्राप्त स्थिति में ही काटने के लिए इस्तेमाल होता है। धातुकार्य में, उपयुक्तता के अनुसार फ्लुइड भिन्न होते हैं। जैसे कि, पेट्रोलियम आधारित कटिंग ऑईल का प्रयोग उनकी उच्चस्तरीय स्नेहन क्षमता के कारण ड्रिलिंग तथा टैपिंग में कई बार होता है। वही टर्निंग तथा मिलिंग के लिए आवश्यक ठंडक प्रदान करने का काम, पानी में सहजता से घुलने वाले फ्लुइड करते हैं। नीट कटिंग ऑईल में सामान्यतः खनिज तेल एवं अन्य पदार्थों का मिश्रण पाया जाता है। नीट ऑईल का प्रयोग हल्के मशीनिंग से ले कर हेवी ड्यूटी ऑपरेशन तक किया जा सकता है। उनका प्रयोग मुख्यतः उष्मा कम करने तथा स्नेहन के लिए किया जाता है। इससे टूल की लंबी आयु के साथ ही यंत्रित पृष्ठभाग का अच्छा फिनिश, दोनों मिलते हैं। कटिंग टूल जब धातु में घुसता है अथवा स्वार्फ के साथ उसका घर्षण होता है तब, घर्षण से उत्पन्न उष्मा कम करने में घुलनशील या सिंथेटिक कटिंग फ्लुइड की अपेक्षा नीट कटिंग ऑईल अधिक कारगर स्नेहक साबित होते हैं। नीट कटिंग ऑईल यंत्रण बल कम कर के ऊर्जा बचाते हैं।
यंत्रण की तीव्रता, धातुओं के प्रकार तथा कार्य की विशिष्ट आवश्यकतानुसार धातु यंत्रण के अलग अलग प्रकार होते हैं। उनमें हेवी ड्यूटी अर्थात ब्रोचिंग, टैपिंग, रीमिंग, गियर कटिंग आदि तथा लाइट ड्यूटी यानि होनिंग, लॅपिंग और धातु के सुपर फिनिशिंग संबंधि अन्य काम समाविष्ट होते हैं।
पिछले 200 वर्षों से धातु यंत्रण में कटिंग फ्लुइड का बड़े पैमाने पर प्रयोग हो रहा है। आरंभ में, मशीन टूल के स्नेहन हेतु ब्रश द्वारा सादा तेल लगाया जाता था। कभी कभी तेल की स्नेहन क्षमता बढ़ाने के लिए खाने में प्रयुक्त चरबी, जानवरों की चरबी या फिर वेल मछली का तेल उसमें मिलाया जाता था। जैसी ही यंत्रण कामों की तीव्रता बढ़ती गई, कटिंग फ्लुइड की मिश्रण प्रक्रिया (फॉर्म्युलेशन) अधिकाधिक जटिल होती गई। धातुकार्य के उद्योगक्षेत्र में अपेक्षित परिणाम पाने के लिए, आज कटिंग फ्लुइड में रासायनिक समावेशी (अैडिटिव), स्नेहक, इमल्सिफायर, डीफोमर, वेटिंग एजंट और नैफ्थिनिक एवं पैराफिन बेस तेल तथा बेस स्टॉक के विशेष मिश्र का प्रयोग होता है।
नीट कटिंग ऑईल की जानकारी
नीट कटिंग ऑईल में सामान्यतः बेस ऑईल तथा समावेशी होते हैं। समावेशियों द्वारा कई तरह के गुणधर्म प्राप्त होते हैं। उदाहरण के लिए अत्यधिक दाब (एक्स्ट्रीम प्रेशर EP), स्नेहक, अैंटिऑक्सिडंट, अैंटिफोम आदि। EP समावेशी भी कई प्रकार के होते हैं। वें क्लोरीनयुक्त, सल्फरयुक्त या फॉस्फरसयुक्त हो सकते हैं। सल्फर समावेशी द्वारा कटिंग टूल और कार्यवस्तु के बीच रासायनिक बंध निर्माण कर के कटिंग ऑईल को घिसाव प्रतिरोधक क्षमता प्रदान की जाती है। इससे टूल, काटी जा रही कार्यवस्तु के सीधे संपर्क में नहीं आता। सल्फर समावेशी दो तरह के होते हैं; सक्रिय एवं निष्क्रिय। निष्क्रिय समावेशियों का प्रयोग माइल्ड (लो कार्बन) स्टील काटने हेतु किया जाता है तथा उससे नर्म धातुओं पर दाग नहीं पड़ते।
सक्रिय सल्फर समावेशी निष्क्रिय समावेशियों से ज्यादा मजबूत बंधों का निर्माण करता है, परंतु उससे नर्म धातुओं पर दाग पड़ जाते हैं। इसी लिए, सिर्फ कठोर स्टील के यंत्रण तथा ब्रोचिंग के लिए सक्रिय सल्फरयुक्त तेल की सिफारिश की जाती है। टूल की उम्र बढ़ाने तथा धातु कटाई के अधिकांश कार्यों में निर्माण होने वाले तीव्र तापमान की वजह से टूल को कार्यवस्तु की सतह पर वेल्ड होने से बचाने में यह रासायनिक बंध कारगर होता है। क्लोरीन समावेशी भी सल्फर समावेशी की तरह ही कार्य करता है और टूल के आसपास के रासायनिक बंध (फिल्म) को मजबूती दे कर सल्फर के लिए पूरक साबित हो सकता है। फैटी ऑईल तथा एस्टर का प्रयोग स्नेहन के लिए समावेशी के रूप में हो सकता है। फैटी ऑईल प्राकृतिक अथवा पशुजन्य चरबी से प्राप्त हो सकते हैं। फैटी ऑईल के समावेश से स्नेहन क्षमता बढ़ती है तथा वह तेल को अधिक 'गीलापन' प्रदान करता है। इससे, बिना समावेशी वाले तेल की तुलना में यह तेल बेहतर स्नेहन करता है तथा धातु को ठंड़ा रखता है। इससे अधिक अच्छी तथा सफाईदार कटाई की जा सकती है और टूल की उम्र भी बढ़ती है। फैटी ऑईल वेटिंग एजंट की तरह ही काम करने वाले मानवनिर्मित मेटल वेटिंग एजंट भी उपलब्ध हैं। उनसे दो अन्य लाभ हैं। मानवनिर्मित एजंट काफी समय तक पड़े रहने पर भी उनकी बासी बदबू नहीं आती और उनसे धातु पर जंगप्रतिरोधक परत तैयार हो जाती है। कभी कभी फॉर्म्युलेशन में अैंटीऑक्सिडंट भी इस्तेमाल होते हैं। ऑईल से आने वाली बदबू की समस्या टालने में इससे फायदा होता है। धातु पर प्रयुक्त तेल में झाग आना (फोमिंग) एक और समस्या है।
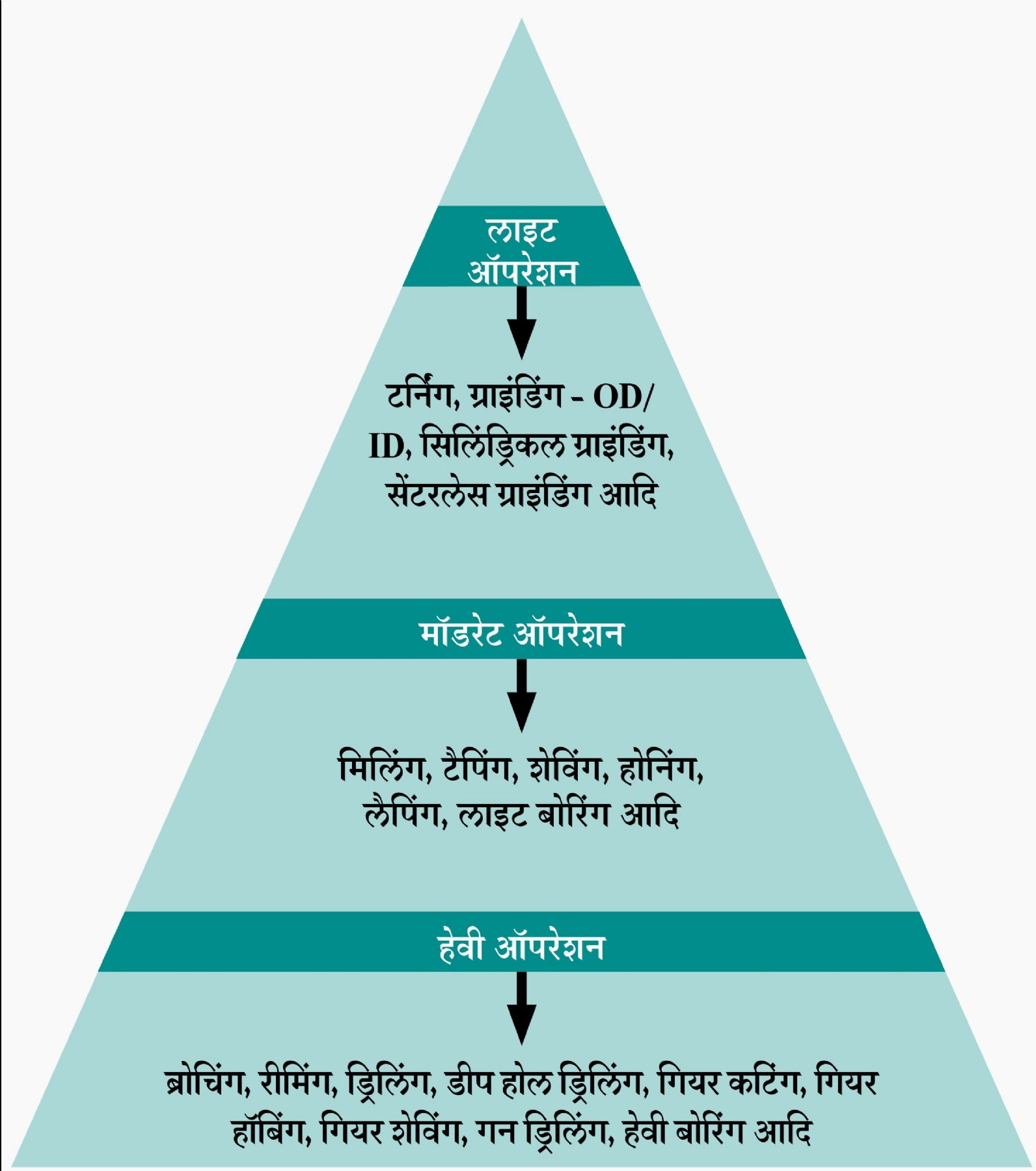
कटिंग ऑईल का फॉर्म्युलेशन करने के लिए विशेष ज्ञान आवश्यक होता है। धातु की कटाई, स्नेहक, EP गुणधर्म, यंत्रण की जा रही धातु के तथा कटिंग टूल के ठंडेपन की विशेषताएं आदि कई चीजों का संबंध कटिंग ऑईल से होता है और उनकी निर्भरता ऑईल पर होती है। धातु यंत्रण के सारे कार्यों के लिए एक ही प्रकार के तेल का इस्तेमाल संभव नहीं होता। कुछ समावेशी, तांबे जैसी पीली धातु के लिए क्षारक (कोरोजिव) हो सकते हैं।
वही समावेशी अन्य धातुओं के यंत्रण के लिए आवश्यक होते हैं, परंतु क्षारक नहीं होते। फिर भी दोनों धातुओं के यंत्रण में समावेशी की आवश्यकता हो सकती है। इसलिए, यंत्रण की जा रही धातु पर दाग लगाए बिना काम करने वाले समावेशी की मात्रा तथा गाढ़ापन (कॉन्सन्ट्रेशन) पता करने का तंत्र मालूम होना आवश्यक है। यंत्रण के लिए जरूरी गाढ़ा रसायन, योग्य मात्रा में पतला बनाना एक महत्त्वपूर्ण प्रक्रिया है। यंत्रण के बाद चिप हटाना (फ्लशिंग) भी जरूरी है, जिससे यंत्रित पृष्ठ और टूल जल्दी ठंड़े हो कर पृष्ठ की गुणवत्ता बढ़ती है।
यदि मशीन में कोई कटिंग/ब्रोचिंग ऑईल को छानने (फिल्टर) की प्रणाली ठीक से काम न कर रही हो, तो चिप अथवा धातुई कण शीतक में मिल कर उसमें बहने लगेंगे। इससे टूल की उम्र कम होना, बिल्ट अप एज, यंत्रभाग पर चॅटरिंग मार्क आदि समस्याएं पैदा होंगी। चिपयुक्त तेल बड़ी मात्रा में फेंका जाने के कारण प्रयुक्त शीतक/ऑईल की मात्रा भी बढ़ेगी। कभी कभी ऑईल का गाढ़ापन घटने का भी अनुभव किया गया है।
फोर बॉल वेल्ड लोड परीक्षण
सभी प्रकार के द्रवरूप स्नेहक, ग्रीज तथा अन्य उपयुक्त स्नेहकों के घिसाव प्रतिरोधक गुणधर्मों का मूल्यांकन करने के लिए फोर बॉल मशीन का उपयोग होता है।
फोर बॉल घिसाव परीक्षण (ASTMD2266) का प्रयोग परिसीमा स्नेहन प्रक्रिया (बाउंड्री लुब्रिकेशन कंडिशन) में कार्यरत धातु के सरकने वाले पृष्ठों पर स्नेहक के सापेक्ष घिसाव प्रतिरोधक गुणधर्म निश्चित करने हेतु किया जाता है। ये परीक्षण निर्दिष्ट गति, तापमान तथा भार (लोड) पर किया जाता है। निर्दिष्ट समय खत्म होने पर, नीचे स्थित तीन बॉल पर पड़े घिसाव के निशानों का औसत व्यास नापा जाता है।
स्नेहकों का चार बॉल परीक्षण
4 बॉल घिसाव संरचना (कॉन्फिगरेशन) का प्रयोग कर के स्नेहन के लिए प्रयुक्त ग्रीज के घिसाव निशान (वेयर स्कार) गुणधर्म तथा घर्षण गुणांक भी निश्चित किए जा सकते हैं। स्नेहक की घिसाव प्रतिरोधक विशेषताएं निश्चित करने हेतु इसका प्रयोग होता है। 4 बॉल घिसाव परीक्षण में स्टील का एक बॉल निर्दिष्ट भार, गति तथा तापमान पर निश्चित समय के लिए स्नेहक लगाए तीन स्थिर स्टील के बॉल पर घिस कर गोल घुमाया जाता है।
घिसाव रोकने में स्नेहक जितना प्रभावी होगा, उतना ही तीन बॉल पर घिसाव का निशान छोटा होगा। परीक्षण खत्म होने पर तीनों बॉल पर के घिसाव के निशान नाप कर उनका औसत मूल्य देखा जाता है। 60 मिनिट के परीक्षण द्वारा घर्षण गुणांक भी नाप कर परीक्षण के अंत में औसत मूल्य दर्ज किया जाता है।
भार वहन क्षमता, लोड बेरिंग, घिसाव से सुरक्षा तथा घर्षण कम करने की भिन्न क्षमताएं रखने वाले स्नेहकों के बीच का फर्क पहचानने में, चार बॉल परीक्षण से प्राप्त निरीक्षण उपयुक्त होते हैं। इन निरीक्षणों का भले ही काम से सीधा संबंध ना हो, तब भी EP, घिसाव तथा घर्षणसंबंधी कार्यक्षमता की तुलना करने के लिए यह पध्दति उद्योगजगत में मानक बन गई है।
नमूना परीक्षण प्रतिवेदन
नमूना स्रोत : टेक्निकल सर्विस
नमूने का विवरण : ब्रोचिंग ऑईल
नमूने का नाम : नमूना A तथा नमूना B
परिणाम
निष्कर्ष
1. PB अधिकतम पकड़ (सीजर) लोड है। इस मूल्य का अधिक होना ऑईल की सीमा स्नेहक प्रक्रिया अधिक होने का सूचक है। उपरोक्त परीक्षण परिणामों से स्पष्ट होता है कि नमूना A तथा नमूना B की स्नेहन प्रक्रिया समान है।
2. PD अर्थात सिन्टर लोड (N)। इस मूल्य का अधिक होना ऑईल में EP स्नेहन प्रक्रिया अधिक होने का सूचक है। उपरोक्त परीक्षण परिणामों से स्पष्ट होता है कि नमूना A की स्नेहन प्रक्रिया, नमूना B से बेहतर है।
विस्कॉसिटी बनाम ब्रोच तापमान
ब्रोचिंग का तापमान घटने से अधिकतम बल मिलता है, प्रक्रिया तथा ब्रोचिंग की टैपिंग कार्यक्षमता सुधरती है, ब्रोचिंग की अचूकता तथा पृष्ठीय गुणवत्ता सुनिश्चित की जा सकती है, कटिंग टूल की आयु बढ़ती है, खर्चा कम होता है तथा पर्यावरण सुरक्षासंबंधी जरूरतें भी संतोषजनक ढ़ंग से पूरी होती हैं।
काइनेमैटिक विस्कॉसिटी मध्यम (12-18 cst के बीच) हो तो ब्रोच का तापमान कम (37°C-44°C के बीच) रहता है और इसलिए पुर्जे का तापमान, ब्रोच के तापमान की तुलना में 2°-4° कम रहता है। उदाहरण 1 तथा उदाहरण 2 में दो विस्कॉसिटी (12 से 18 cst) के मिश्र का प्रयोग किया गया है, जिससे उच्च टैपिंग कार्यक्षमता की प्रतिशतता प्राप्त होती है।
ब्रोचिंग तथा नीट कटिंग ऑईल
ब्रोचिंग ऑपरेशन क्या है? ब्रोचिंग इस यंत्रण प्रक्रिया में मटीरीयल निकालने के लिए ब्रोच नामक दांतेदार उपकरण का प्रयोग होता है।
नीट कटिंग के सारे कामों में ब्रोचिंग, सर्वाधिक तीव्रता का धातु कटाई का काम है। समतल, गोलाकार अथवा कंटूर वाली कार्यवस्तु पर से धातु हटाने के लिए ब्रोचिंग किया जाता है। इसमें अनेक दांतों वाले कटिंग टूल का प्रयोग होता है। इसके पहले दांत से दूसरा दांत थोड़ा ऊंचा होता है और हर दांत, पहले दांत की तुलना में ज्यादा गहराई तक का मटीरीयल निकालता है।
जिस यंत्रण में प्रति मिनट (ग्रै./मिनट) अधिक धातुई चिप निकलती हो उसे यदि हेवी ड्यूटी यंत्रण कहा जाए, तो ब्रोचिंग को हेवी ड्यूटी नहीं मान सकते। मिलिंग तथा टर्निंग प्रक्रियाओं में बहुत बड़े पैमाने पर धातु निकाली जाती है। इसलिए इस काम में टंग्स्टन कार्बाइड, सिरैमिक्स तथा PCD जैसे कठोर कटिंग टूल मटीरीयल का प्रयोग करना संभव है। इन मटीरीयल पर लेपन (कोटिंग) कर के बहुत कड़ी स्थितियों में भी इनका प्रयोग किया जा सकता है, क्योंकि इससे घिसाव तथा उष्मा का अच्छा प्रतिरोध संभव होता है। इसलिए ऐसी स्थिति में कटिंग ऑईल पर ज्यादा निर्भर नहीं रहना पड़ता। किंतु ब्रोचिंग टूल में इन मटीरीयल का प्रयोग संभव नहीं है। इसमें HSS से से बने टूल का प्रयोग होता है, जो ऊपर लिखे गए मटीरीयल से वाकई कम सख्त (टफ) होते हैं। परंतु यह उपकरण बहुत बड़ा तथा महंगा होता है, कार्यवस्तु की अपेक्षित गुणवत्ता (फॉर्म, आकार, पृष्ठीय फिनिश आदी) बहुत उच्च दर्जे की होती है और चिप हटाने में कई समस्याएं आती हैं। इन सब कारणों से उच्च प्रभावशालि कटिंग ऑईल की आवश्यकता होती है और इसी लिए यहाँ नीट कटिंग ऑईल इस्तेमाल होता है।
कटिंग ऑईल संबंधि कुछ जरूरी जानकारी
1. रचना : बेस ऑईल, सल्फर/फॉस्फेट आधारित EP समावेशी, इमल्सिफायर, अैंटिफोम आदि
2. ब्रोचिंग ऑईल में अपेक्षित गुणधर्म : सम्प में दीर्घ आयु। बिल्ट अप एज, ब्रोच के दांत टूटना तथा पुर्जे पर चैटर मार्क जैसी समस्याएं न होना। यदि पानी मिश्रित हो तो कटिंग ऑईल से बदबू न आना।
3. प्रयोगशाला में परीक्षण : प्रयोगशालेय स्थिति में केवल विस्कॉसिटी, विशिष्ट गुरुत्वाकर्षण और उच्च तथा हिमांक बिंदु पर उपलब्ध स्थिरता का मापन किया जा सकता है।
4. अच्छे ब्रोचिंग ऑईल के कार्यान्वयन के बाद अपेक्षित परिणाम : अच्छा पृष्ठीय फिनिश, पुर्जों पर बर्न मार्क का अभाव और पुर्जों के आयाम बरकरार रहना।
5. टंकी (सम्प) में आयु : कटिंग ऑईल के परीक्षणसंबंधि गाढ़ापन तथा pH जैसे मापदंड़ योग्य तरीके से बरते जाए, मिश्र/टॉप अप के लिए RO (रिवर्स ऑस्मॉसिस) या DM (डीमिनरलाइज्ड्) पानी का प्रयोग किया जाए और समय समय पर छाना जाए, तो जलमिश्रित ऑईल के लिए 9-12 महीने तक की आयु टंकी में प्राप्त हो सकती है। नीट कटिंग ऑईल को छानने हेतु अच्छी तकनीक का इस्तेमाल करने तथा समय समय पर ऑईल को सेंट्रीफ्यूज द्वारा साफ करने पर कटिंग ऑईल की आयु बढ़ सकती है।
सुरक्षासंबंधी महत्वपूर्ण जानकारी
स्वास्थ्य के लिए हानिकारक : यदि कम फ्लैशपॉइंट वाले स्नेहक या रसायनिक साल्वंट का उपयोग कर रहे हो तो 'ज्वलनशील - स्वास्थ्य के लिए हानिकारक हो सकता है' यह चेतावनी जरूर दें।
अग्निशामक माध्यम : CO2, सूखे रसायन, फोम अथवा पानी के तुषार (पानी की फुहार का सीधा प्रयोग ना करें।)
विशेष अग्निशमन पध्दति : स्वयंपूर्ण श्वसन उपकरण (NIOSH द्वारा प्रमाणित) पहनें। भांप का दाब बढ़ना रोकने के लिए, आग से तपे कंटेनर को पानी से ठंड़ा करना जरूरी है वरना कंटेनर फट सकता है।
यंत्रण प्रक्रिया अधिकतम प्रभावशालि बनाने हेतु इस्तेमाल किए जाने वाले नीट कटिंग ऑईल की विविध विशेषताओं की जानकारी इस लेख में संक्षेप में पेश करने का प्रयास किया गया है। आशा है कि आपके कारखाने में यह जानकारी उपयुक्त होगी।