फैक्टरी में काम करते हुए विभिन्न तरह की चुनौतियों का सामना करना पड़ता है। साथ ही उभर आई समस्याएं सुलझानी होती हैं। मशीन में खराबी, सही टूल की अनुपलब्धि जैसी समस्याओं के साथ, ग्राहक ने दिए जटिल पुर्जे का यंत्रण करते समय प्रत्याशित परिशुद्धता तथा पूर्वनिश्चित अवधि में उत्पादन पूरा करने की चुनौती भी उठानी पड़ती है। हमारे पास इस तरह के, मुश्किल यंत्रण वाले, पुर्जे उत्पादन के लिए आते रहते हैं। उपलब्ध साधन और सामग्री का सही एवं कल्पनाशील प्रयोग करते हुए, ग्राहक को इच्छित उत्पाद निश्चित अवधि में देने का हठ हम रखते हैं। ऐसे ही एक पुर्जे के संदर्भ में किए हुए सफल प्रयास की जानकारी इस लेख में दी गई है।
चित्र क्र. 1 में दर्शाई गई गोलाकार (स्फेरिकल) कार्यवस्तु का अंदर से एवं बाहर से यंत्रण तथा फिनिशिंग करना है। कार्यवस्तु का अंदरी व्यास 18.85 मिमी. और बाहरी व्यास 28.5 मिमी. (अंतिम नाप) है।
ग्राहक की अपेक्षाएं
1. अंदरी व्यास का Ra मूल्य बहुत ही कम यानि 0.1 Ra होना चाहिए।
2. बाहरी व्यास 15 से 17 माइक्रोन टॉलरन्स में होना चाहिए।
कार्यवस्तु बनाने के चरण
1. कच्ची सामग्री के तौर पर EN 31 का लंबा बार इस्तेमाल होता है।
2. इस (बार) में पहले अंदरी व्यास के नाप का ड्रिलिंग कर के बाद में उसका पार्टिंग करते हुए इच्छित लंबाई के टुकड़े बनाए जाते हैं।
3. पार्टिंग के पश्चात दोनों तरफ रफ यंत्रण किया जाता है।
4. रफ यंत्रण के बाद कार्यवस्तु हीट ट्रीटमेंट के लिए भेजी जाती है। फिर उसकी कठोरता 60 से 63 HRC तक होती है।
5. हीट ट्रीटमेंट के बाद कार्यवस्तु पकड़ कर उसके अंदरी व्यास का फिनिश यंत्रण होता है।
6. अंदरी व्यास के यंत्रण के बाद बाहरी पृष्ठ का यंत्रण एवं फिनिशिंग किया जाता है।
यंत्रण प्रक्रिया
कार्यवस्तु के अंदरी व्यास का यंत्रण शुरु करने से पहले उसे चक में ठीक से पकड़ना जरूरी है। इसके लिए, जैसे कि चित्र क्र. 1 में दर्शाया है, बाहरी पृष्ठ पर समतल हिस्सा बनाया जाता है। अंदरी पृष्ठ का प्रत्याशित Ra मूल्य पाने हेतु करीबन 0.8 मिमी. त्रिज्या का सी.बी.एन. इन्सर्ट (चित्र क्र. 2) इस्तेमाल किया है। यंत्रण के दौरान सरकने की गति (फीड) बहुत कम रखी, जिससे अंदरी व्यास का फिनिश 0.1 Ra से भी कम पाना मुमकिन हुआ। इस प्रकार ग्राहक की पहली मांग पूरी करने में हम सफल रहे।
ग्राहक की दूसरी माँग पूरी करने में हमें अधिक मुश्किलें आ रही थीं। ग्राहक इस कार्यवस्तु के बाहरी व्यास का टॉलरन्स 15 से 17 माइक्रोन की सीमा में चाहते थे। कार्यवस्तु एक तरफ से पकड़ कर उस पर यंत्रण करें तो प्रत्याशित परिशुद्धता नहीं मिल रही थी। इस हेतु हमने वी.एन.एम.जी. या वी.बी.एम.टी. न्यूट्रल टूल द्वारा यंत्रण किया, फिर भी कार्यवस्तु पकड़ने के मामले में परेशानियां थी। शुरुआत में हम इस कार्यवस्तु का यंत्रण करते समय उसका अंदरी व्यास 20 माइक्रोन की सीमा में रखते थे। इसके अनुसार टेपर मैंड्रेल बना कर वह कार्यवस्तु आगे की ओर से क्लैंप करते थे। लेकिन अंदरी व्यास के 20 माइक्रोन टॉलरन्स के कारण कार्यवस्तु थोड़ी आगे पीछे हिल रही थी, जिससे उसका अपेक्षित आकार मिलने के बजाय वह अंड़ाकार बन रही थी। फलस्वरूप कार्यवस्तु के नाप परिशुद्ध नहीं पाए जा रहे थे। हमने सोचा कि उस पर फैलने वाले (एक्स्पांडिंग) मैंड्रेल का प्रयोग करें। फैलने वाले मैंड्रेल के कई प्रकार बाजार में मिलते हैं। हमें इस यंत्रण के लिए फिक्स्ड स्टॉप वाले, (फिक्स्ड स्टॉप यानि कार्यवस्तु एक निश्चित स्थान से सट कर रुकती है।) फैलने वाले मैंड्रेल की जरूरत थी, जो बाजार में मिलना बहुत मुश्किल था। इस फिक्स्ड स्टॉप के कारण ऑपरेटर जो ऑफसेट लेगा के वल उतनी ही जगह में टूल घूमता है, वह आसपास कहीं नहीं जाता है। वरना हर बार टेपर मैंड्रेल पर कार्यवस्तु का स्थानांतरण हो जाता है। हालांकि सी.एन. सी. पर हर बार ऑफसेट लेना संभव है, यह काम कष्टप्रद होता है और उसमें समय बरबाद होता है। इन सब चीजों को टालने हेतु हमने सोचा कि फिक्स्ड स्टॉप वाला मैंड्रेल होना चाहिए।
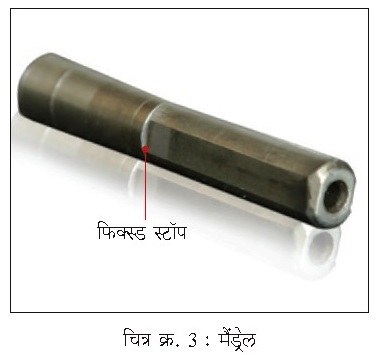
यह मैंड्रेल (चित्र क्र. 3) हमने खुद ही बनाया। शुरुआत में यह पूरी लंबाई पर गोलाकार किया था। उस पर 2 समतल पृष्ठ बना कर ग्रब स्क्रू लगाने की सुविधा की। परंतु कुछ समय बाद नजर आया कि हर कार्यवस्तु पर काम करते समय मैंड्रेल हर बार बाहर निकालना पड़ेगा और यदि ऑपरेटर ग्रब स्क्रू कस कर लगाना भूल गया तो सी.बी.एन. इन्सर्ट टूटने की संभावना रहेगी। यह इन्सर्ट काफी महंगे होते हैं। इस पर इलाज करने के लिए हमने बहुत अनुसंधान किया, तो समझ आया कि मैंड्रेल चक में पकड़ा जाने पर वह खड़ी या आड़ी किसी भी दिशा में घूमना नहीं चाहिए। उसका आड़ा और डाइमेट्रिकल प्ले कम से कम होना चाहिए। इसके लिए हमने मैंड्रेल की दोनों बाजुओं को समतल बनाया क्योंकि प्ले डबल हो तो कार्यवस्तु उस हिस्से पर आती है। अगर इसका नियंत्रण 5 माइक्रोन की सीमा में कर सके तो कार्यवस्तु की ओवैलिटी 10 माइक्रोन की सीमा तक पाना मुमकिन है।
मैंड्रेल की रेडियल और समतल दोनों पृष्ठों पर आयाम (डाइमेन्शन) अचूक होने चाहिए। मैंड्रेल पर हमने जो टेपर दिया है वहीं टेपर हब (चित्र क्र. 4) की अंदरी बाजू पर है।
मैंड्रेल की लंबाई पर तथा हब में दो समतल पृष्ठ बनाए जाने से शाफ्ट एवं हब के बीच की हलचल बंद हो गई। चक में मैंड्रेल पकड़ने के बाद डायल लगा कर ट्रू कर सकते हैं; वह भी परिशुद्ध होना जरूरी है। इसके बाद मैंड्रेल पर कॉलेट (चित्र क्र. 5) लगाया जाता है और उस पर कार्यवस्तु बिठाई जाती है। यहाँ फिक्स्ड स्टॉप होने के कारण कार्यवस्तु किसी भी दिशा में हिलती नहीं है, बल्कि पक्की बैठजाती है। दूसरी तरफ से इस पूरे हिस्से पर टेलस्टॉक द्वारा दबाव दिया जाता है। इस दबाव से मैंड्रेल पर रहा कॉलेट फैल जाता है, जिससे कार्यवस्तु मैंड्रेल पर और भी कस कर (चित्र क्र. 6) बिठाई जाती है। इस सुविधा के कारण कार्यवस्तु का यंत्रण करना आसान होता है और कार्यवस्तु पर न्यूट्रल टूल से निरंतर यंत्रण किया जा सकता है।
यंत्रण करते हुए बरतने की सावधानी
आज के नए टूल को केवल दोनों तरफ से समतल पृष्ठ होते हैं। इस तरह की कार्यवस्तुओं का यंत्रण करने के लिए तीसरी तरफ से भी पृष्ठ समतल होना चाहिए। उस पर टूल कसना मुमकिन होना जरूरी है, ताकि टूल विस्थापन (डिफ्लेक्शन) पर रोक लगे।
लेकिन टेलस्टॉक से होने वाला दबाव बदलने से यंत्रण में समस्या आ सकती है। कार्यवस्तु एक ही जगह पर घूमी तो इन्सर्ट टूट भी सकता है। इसलिए टेलस्टॉक द्वारा दिया जाने वाला दबाव भी इस यंत्रण में महत्वपूर्ण है, तथा टेलस्टॉक का संचलन नियंत्रित होना भी जरूरी है। हमारे टेलस्टॉक का संचलन डिजिटल तरीके से किया जाता है। यह भी तय किया जाता है कि टेलस्टॉक द्वारा कितना दबाव देना है। इसका मतलब है टेलस्टॉक का स्थान, उससे दिया जाने वाला दबाव और उसका पुनरावर्तन (रिपीटैबिलिटी) यह तीनों बातें सेट करना महत्वपूर्ण है।
मैंड्रेल एवं कॉलेट बनाते समय पोकायोके के बारे में भी सोचा गया है। मैंड्रेल पर जहाँ कॉलेट लगाया जाता है, वहाँ टेपर बनाया गया है। यदि यह कॉलेट उल्टा ड़ाला जाए तो वह मैंड्रेल पर ठीक से बैठ नहीं पाता है। इसमें प्रधानता से आगे दिए बातों का विचार किया गया
1. ऑपरेटर कार्यवस्तु मैंड्रेल पर एक ही दिशा में लगा सकता है, कार्यवस्तु उल्टी नहीं ड़ाली जा सकती।
2. कॉलेट आगे से दबाने पर वह टूटना नहीं चाहिए।
3. अगर बिना कार्यवस्तु ड़ाले ही कॉलेट टेपर हिस्से पर सरकाया जाए तो, एक निश्चित व्यास पर वह अत्यधिक फैल कर टूट जाएगा। यह ना हो इसलिए वह कितनी मात्रा में आगे जाना चाहिए, उसकी लंबाई, चौड़ाई, टेपर आदि के बारे में सोचा। कॉलेट का अधिकतम 0.5 मिमी. तक फैलना ठीक है, लेकिन हम चाहते थे कि वह केवल 20 माइक्रोन तक ही फैले, क्योंकि इस कार्यवस्तु का अंदरी व्यास 20 माइक्रोन की सीमा में ही रखा जाता है।
लाभ
1. परिशुद्ध पुर्जे (चित्र क्र. 7) पाए जाने लगे।
2. बाहरी व्यास के संदर्भ में अच्छी संकेन्द्रिता (कॉन्सेन्ट्रिसिटी) मिलने लगी।
3. यंत्रण के दौरान कार्यवस्तु ना हिलने से उसके बेलनी आकार की निरंतरता बनाई रखी गई।
4. पुराने तरीके में कार्यवस्तु अस्वीकार होने की मात्रा भले ही कम थी, लेकिन उसे बनाने में अधिक समय लगता था। यदि कुछ समस्या आए तो पॉलिशिंग में 10-20 माइक्रोन में हम उसकी सीमा पाते थे। लेकिन इसमें फिर से काम करना (रीवर्क) अधिक होता था और समय भी बरबाद होता था। अब इस सुधार के बाद हमारा लगभग 20% समय बच गया।
5. पुराने तरीके में पॉलिशिंग करने वाले कुशल कर्मचारी की जरूरत थी, जो अब नहीं रही।
6. सुधार से पहले हर दिन 60-70 पुर्जे बनते थे। लेकिन सुधार के पश्चात अब यह संख्या प्रतिदिन 300-350 तक बढ़ी है। इन पुर्जों की परिशुद्धता माइक्रोमीटर से जांची जाए तो उनके आयाम बिल्कुल सही होने की सुनिश्चिति हम ग्राहक को आज दे सकते हैं।
प्रमोद जोशी
संचालक, फैब्युलस इंजीनीयरिंग
8830591172
प्रमोद जोशी यांत्रिकी अभियंता हैं और आपको देखभाल क्षेत्र का 13 साल एवं यंत्रण क्षेत्र का 27 सालों का अनुभव है। फैब्युलस इंजीनीयरिंग कंपनी के आप संचालक है।