सेंटरलेस ग्राइंडर का विकसन, तेज गति से उत्पादन तथा उच्च अचूकता के लिए किया गया है। यह प्रक्रिया बड़ी बैच के लिए सर्वोत्तम है क्योंकि इसमें यंत्रण के लिए आवश्यक समय की तुलना में, सेटअप का समय कम रहता है। थ्रू-फीड तथा इन-फीड (प्लंज) ऐसे दोनों प्रकार के ग्राइंडिंग के लिए यह मशीन उपयुक्त है।
सेंटरलेस ग्राइंडिंग की संकल्पना
• स्थिर वर्करेस्ट (चित्र क्र. 2)
वर्करेस्ट तथा रेग्युलेटिंग वील स्थिर होते हैं, ग्राइंडिंग वील इन-फीड के लिए संचलन करता है। लंबे बार के ग्राइंडिंग के लिए उचित, ऑटो लोडिंग अैप्लिकेशन।
• स्थिर ग्राइंडिंग वील हेड (चित्र क्र. 3)
इन-फीड के लिए वर्करेस्ट तथा रेग्युलेटिंग वील संचलन करते हैं। उच्च यंत्रण पैरामीटर तथा उच्च विद्युतशक्ति वाली मशीन के लिए उपयुक्त। दर्जेदार अचूकता।
• स्थिर वर्क सेंटर (चित्र क्र. 4)
वर्करेस्ट स्थिर, ग्राइंडिंग के दौरान ग्राइंडिंग वील तथा रेग्युलेटिंग वील दोनों इन-फीडिंग के लिए संचलन करते हैं, इससे कार्यवस्तु सेंटर ब्लेड पर स्थिर रहती है। सी.एन. सी. नियंत्रण होने पर ही यह संभव होता है। अत्यंत उच्च ज्यामितीय अचूकता के लिए उपयुक्त।
सेंटरलेस में राउंडिंग प्रक्रिया
ग्राइंडिंग एवं रेग्युलेटिंग वील की केंद्ररेखा पर कार्यवस्तु की केंद्ररेखा सेट करने से गोलाकारिता तैयार नहीं होती। ऐसे सेटअप में कोई भी ऊंचाई (हाइ स्पॉट), व्यास के दूसरे सिरे पर (डाइमेट्रिकली ऑपोजिट), गड्ड़ा (लो स्पॉट) तैयार करती है। कुछ समय बाद, कार्यवस्तु चित्र क्र. 5 में दर्शाए गए विरूपित आकार के समान दिखाई देगी।
कार्यवस्तु पर गोलाई पाने हेतु सेंटरलेस ग्राइंडिंग प्रक्रिया करनी हो तो कार्यवस्तु वील की केंद्ररेखा से ऊपर (चित्र क्र. 6) रखना आवश्यक है। इस सेटअप में, ऊंचाई के कारण व्यास के दूसरे सिरे पर गड्ड़े तैयार नहीं होगे। बल्कि ऊंचाई का ग्राइंडिंग किया जाएगा, तथा कार्यवस्तु में धीरे धीरे गोलाई आ जाएगी। ब्लेड सपोर्ट पर होने वाला कोण इस प्रक्रिया में अधिक सहायता करता है।
सेटिंग पैरामीटर के असर
कार्यवस्तु की मध्यभाग में ऊं चाई (सेंटर हाइट)
एक इंच व्यास तक की कार्यवस्तु के लिए उचित ऊंचाई निश्चित करने का सामान्य नियम है, कार्यवस्तु का आधे व्यास जितना हिस्सा ग्राइंडिंग तथा रेग्युलेटिंग वील की केंद्ररेखा से उपर होना चाहिए। मिसाल के तौर पर, 20 मिमी. व्यास की कार्यवस्तु हो, तो उसकी 10 मिमी. ऊंचाई वील की केंद्ररेखा से उपर होनी चाहिए। 'अधिकांश सेंटरलेस ग्राइंडिंग सेटअप के लिए यह प्राथमिक आरंभ बिंदू होता है।' पुर्जे के विन्यास (कॉन्फिगरेशन) के अनुसार यानि ठोस/खोखला होना, कार्यवस्तु की बनावट तथा मटीरीयल आदि के अनुसार कार्यवस्तु के मध्यभाग की ऊंचाई बदलती है। मध्यभाग की ऊंचाई अधिकहो तो भी लोब की संख्या बढ़ने से गोलाई बढ़ती है, लेकिन उसकी अस्थिरता के कारण चैटरिंग होने की संभावना बढ़ती है। इसलिए हमें कार्यवस्तु के सेटिंग में मध्यमार्ग अपनाना पड़ता है।
वर्करेस्ट ब्लेड का कोण
सेंटरलेस ग्राइंडिंग में वर्कब्लेड का कोण 0° से 45° तक होता है। देखा गया है कि कई सेंटरलेस ग्राइंडिंग अैप्लिकेशन के लिए 30° का शीर्ष ब्लेड कोण चुनने से उत्तम परिणाम मिलते हैं। यहाँ मूलाधारी नियम है कि ब्लेड का कोण जितना अधिक, उतनी गोलाई देने की क्रिया अधिक गतिशील होती है, लेकिन इस पर भी कई घटकों से मर्यादा आती है। बड़े व्यास की तथा लंबी कार्यवस्तु के लिए कम ब्लेड कोण सर्वोत्तम माना जाता है। सामान्यतः 30° का शीर्ष ब्लेड कोण चुनना एक उत्तम आरंभ बिंदु माना जाता है।
थ्रू-फीड ग्राइंडिंग
थ्रू-फीड सेंटरलेस ग्राइंडिंग (चित्र क्र. 7) में कार्यवस्तुएं ग्राइंडिंग वील से पूरी तरह आगे सरकाई (फीड) जाती हैं। एक ओर से कार्यवस्तु ग्राइंडर में प्रवेश कर के दूसरी ओर से बाहर निकलती है। थ्रू- फीड ग्राइंडिंग में रेग्युलेटिंग वील को, ग्राइंडिंग वील के प्लेन से ऐसे कोण में बाहर की ओर झुकाया जाता है कि, उससे मिलने वाले अक्षीय बल के हिस्से द्वारा कार्यवस्तु दो वील्स के बीच से सरकाई जाती है। थ्रू-फीड ग्राइंडिंग अधिक कार्यक्षम हो सकता है क्योंकि उसमें स्वतंत्र फीड प्रबंध की जरूरत नहीं होती। तथापि, जिनका बाहरी व्यास सीधा बेलनाकार हो ऐसे ही पुर्जों के लिए उसका इस्तेमाल किया जा सकता है।
थ्रू-फीड ग्राइंडिंग का इस्तेमाल प्रायः बड़े पैमाने पर निरंतर उत्पादन में किया जाता है। वील इस प्रकार ड् रेस किए जाते हैं कि कार्यवस्तु ग्राइंडिंग वील के फेस के सामने से, कटिंग झोन में से चलाई जाती है। कार्यवस्तु पूरी करने के लिए प्रायः 2-3 पास काफी होते हैं। आउटपुट की अचूकता तथा फिनिश की जरूरत के अनुसार पास की संख्या बढ़ाई जा सकती है। सापेक्ष संचलन से अत्यंत उच्च फिनिश (<0.1Ra), तथा ग्राइंडिंग करते समय स्लाइड का इन-फीड ना होने से आकार में अत्यंत उच्च दर्जे का टॉलरन्स (0.003-0.004 मिमी.) मिल सकता है। अंतिम उत्पादन की अचूकता, मुख्यतः स्पिंडल की अचूकता तथा मशीन की कुल दृढ़ता पर निर्भर होती है।
थ्रू-फीड ग्राइंडिंग में रेग्युलेटिंग वील तिरछा होता है जिससे, ग्राइंडिंग वील के सापेक्ष एक फीड कोण तैयार होता है। इस फीड कोण से रेग्युलेटिंग वील, कार्यवस्तु को ग्राइंडिंग वील की विपरित दिशा में गोल घुमाना तथा ग्राइंडिंग वील के फेस पर कार्यवस्तु चलाना ये दो काम कर सकता है।
ग्राइंडिंग वील के संदर्भ में रेग्युलेटिंग वील तिरछा (स्विवेल) किया जा सकता है। तथापि, उसका काम होने के लिए तथा ग्राइंडिंग वील की पूरी चौड़ाई इस्तेमाल करने हेतु कार्यवस्तु , ग्राइंडिंग वील तथा रेग्युलेटिंग वील के दौरान रेखीय संपर्क होना जरूरी है। इसीलिए रेग्युलेटिंग वील ट्रू करने का काम, खास उपसाधन पर स्थित डाइमंड ब्लॉक के इस्तेमाल से करना जरूरी होता है। डाइमंड ब्लॉक के जरिए डाइमंड का संपर्क, कार्यवस्तु की ऊंचाई की तुलना में ग्राइंडिंग तथा रेग्युलेटिंग वील की केंद्ररेखा के उपरी ओर समायोजित (अैडजस्ट) कर सकते हैं।
इन-फीड/प्लंज ग्राइंडिंग
इन-फीड (प्लंज) सेंटरलेस ग्राइंडिंग (चित्र क्र. 8) का इस्तेमाल, एक से अधिक व्यास अथवा प्रोफाइल होने वाली कार्यवस्तु के ग्राइंडिंग में किया जाता है। ग्राइंडिंग प्रक्रिया शुरु होने के पहले, कार्यवस्तु हाथ से अथवा दो वील के बीच से ग्राइंडिंग मशीन में लोड की जाती है तथा रेग्युलेटिंग वील उसके उचितस्थान पर हिलाया जाता है। कार्यवस्तु का बाह्यरूप (शेप) तथा ग्राइंडिंग वील का आकार इनके, अचूक ग्राइंडिंग के लिए बनाए विशेष प्रोफाइल के कारण, कार्यवस्तु को मशीन में अक्षीय दिशा में फीड नहीं कर सकते।
इन-फीड सेंटरलेस ग्राइंडिंग, किसी सेंटर टाइप मशीन पर प्लंज ग्राइंडिंग करने के समान है। कार्यवस्तु ब्लेड पर रखी जाती है और ग्राइंडिंग शुरु करने के लिए, रेग्युलेटिंग वील अपने प्रोग्रैम किए फीड में संचलन करता है। इस प्रकार के सेंटरलेस ग्राइंडिंग में कार्यवस्तु अक्षीय दिशा में आगे नहीं जाती। मशीन की दृढ़ता, ग्राइंडिंग के दौरान कार्यवस्तु को मिलने वाला अधिक उचित आधार तथा गतिमान लोडिंग/अनलोडिंग इनके जरिए सेंटरलेस ग्राइंडिंग में अचूकता तथा उत्पादकता सर्वोत्तम होती है।
इन दो प्रकारों में से, इन-फीड में सेटअप करना इतना मुश्किल नहीं है। कार्यवस्तु की ऊंचाई महत्वपूर्ण होते हुए भी, तैयार कार्यवस्तु के चरणों (स्टेप्स) में जरूरी संबंध प्राप्त करने के लिए उचित वर्कब्लेड तथा वील प्रोफाइल जरूरी है।
वील के बीच में कार्यवस्तु रखी जाती है और ग्राइंडिंग का आवर्तन शुरु होता है। स्पार्कआऊट के बाद, तैयार किया गया भाग बाहर निकाला जाता है तथा अगला भाग अंदर आता है।
कार्यवस्तु की कमाल लंबाई, ग्राइंडिंग वील की चौड़ाई तक सीमित होती है। जटिल प्रोफाइल तथा एक से अधिक चरणों वाले व्यास, एक सेटअप में ग्राइंड किए जा सकते हैं।
प्लंज ग्राइंडिंग में उत्पादन की अचूकता मशीन की सकल अचूकता पर यानि इन-फीड अक्ष, स्पिंडल, कुल दृढ़ता, प्रोफाइल वील पर ड्रेसकी जाने के कारण ड्रेसिंग सिस्टम प्रोफाइल, इन सब पर निर्भर करती है। इस मशीन पर, अनुत्पादक समय घटाने हेतु कार्यवस्तु शीघ्र संचलन करने वाली स्वचालित प्रणालियां अत्यंत जटिल होती हैं।
ग्राइंडिंग मशीन के क्षेत्र में माइक्रोमैटिक ग्राइंडिंग टेक्नॉलॉजीज् लि. (MGTL) कंपनी विख्यात है। इसकी शुरुआत 1973 में एक किराए के शेड में की गई। आज हमारी कंपनी का उत्पादन, गाजियाबाद में 3 तथा बंगलुरु में 1 ऐसे कुल चार कारखानों में लगभग 20,000 वर्गमीटर के क्षेत्र से हो रहा है। सिलिंड्रिकल, सेंटरलेस, युनिवर्सल जैसे सभी प्रकारों के सी.एन. सी. ग्राइंडिंग मशीन के साथ ही, विशेष पुर्जों के लिए होने वाले स्पेशल पर्पज मशीन भी यहाँ बनते हैं।
इन-फीड अथवा थ्रू-फीड ग्राइंडिंग अैप्लिकेशन के लिए MGT सेंटरलेस ग्राइंडर सुविधाजनक होते हैं। MGT तीन अक्ष की स्टैंडर्ड मशीन पेश करती है, तथापि अैप्लिकेशन के जरूरत के अनुसार इस मशीन को 8 अक्षों तक कॉन्फिगर किया जा सकता है।
स्टैंडर्ड 3 अक्षीय मशीन
• मुख्य इन-फीड X
• ग्राइंडिंग वील ड्रेसर ट्रैवर्स Y
• ड्रेसर फीड Z
वैकल्पिक अक्ष
थ्रू-फीड काम के लिए मुख्य इन-फीड X
वैकल्पिक 6 अक्ष(चित्र क्र. 9)
• मुख्य इन-फीड X
• ग्राइंडिंग वील ड्रेसर ट्रैवर्स Y
• ड्रेसर फीड Z
• इन-फीड हाउसिंग स्लाइड W
• रेग्युलेटिंग वील ड्रेसर ट्रैवर्स B
• इन-फीड A
इन-फीड अथवा थ्रू-फीड ग्राइंडिंग अैप्लिकेशन से उत्पादन की जरूरत पूरी करने के लिए MGT द्वारा, मशीन समेत इंटरफेस किए गए विभिन्न प्रकार के ऑटोलोडिंग तथा अनलोडिंग उपकरण दिए जाते हैं।
प्रोफाइल तथा अचूकता की जरूरत के अनुसार MGT निम्न विभिन्न ड्रेसिंग व्यवस्था देती है।
• ब्लेड प्रकार के डाइमंड से ड्रेसिंग
• डिस्क ड्रेसर के इस्तेमाल से ड्रेसिंग
• डाइमंड रोल के इस्तेमाल से ड्रेसिंग
सेंटरलेस ग्राइंडिंग के लिए बनाई गई CLG श्रेणी की मशीन की विशेषताएं
नीडल ग्राइंडिंग जैसे काम के लिए उचित सी.एन.सी. सेंटरलेस ग्राइंडर CLG 5020 (चित्र क्र. 10) की मुख्य विशेषताएं इस प्रकार हैं
• रिब की रचना वाले बेड के कारण उत्तम स्टैटिक तथा डाइनैमिक दृढ़ता मिलती है और कंपनों का दमन (डैंपनिंग) सुनिश्चित किया जाता है।
• रेग्युलेशन वील स्पिंडल के लिए हाइ प्रिसिजन बेरिंग वाला दृढ़ आउटबोर्ड सपोर्ट
• ग्राइंडिंग वील के लिए ऑटो डाइनैमिक सिस्टम (इनसाइड स्पिंडल प्रकार)
• ग्राइंडिंग वील तथा रेग्युलेटिंग वील स्पिंडल का, डाइनैमिक स्थिति में अधिकतम लोड के लिए, FEA विश्लेषण किया होता है।
• इन-फीड अक्ष के लिए (X अक्ष) हेवी ड्यूटी प्रीलोडेड उच्च प्रिसिजन रोलर गाइडवे
• अचूक प्रोफाइल ड्रेसिंग के लिए ग्राइंडिंग वील ड्रेसर समेत दो अक्षीय सी.एन.सी. रोटरी डिस्क ड्रेसर
• रेग्युलेटिंग वील के प्रोफाइल ड्रेसिंग के लिए 2 अक्षीय सी.एन.सी. ड्रेसर
• पुर्जे द्रुत गति से अनलोड करने के लिए तथा रेग्युलेटिंग वील ड्रेसिंग की क्षतिपूर्ति हेतु सर्वो नियंत्रित अपर स्लाइड
• घटकों के गतिमान लोडिंग के लिए इन-फीड स्लाइड पर बिठाई सर्वो गैन्ट्री
• लोडिंग के लिए रोबो, विजन कैमरा तथा वाइब्रेटरी बाउल फीडर एवं पोकायोके।
मिसाल
ग्राहकों को उनके पुर्जों के अचूक ग्राइंडिंग में हर प्रकार से सहायता करना, MGTL की संस्कृति का अहम् हिस्सा है। नाशिक में पैटको प्रिसिजन कंपोनंटस् कंपनी है। इन्हे सी.आर. नोजल ग्राइंडिंग के लिए CLG मशीन इस्तेमाल करते समय समस्या आ रही थी। जानते हैं कि, अंतिम ग्राहक डेल्फी-टीवीएस टेक्नॉलॉजीज् की सहायता से, बाद में उत्पन्न हुई समस्या का समाधान किस प्रकार किया गया।
एकसाथ काम करने से सफलता मिलती है !
कम निवेश में एक नई सी.आर. नोजल असेंब्ली शुरु करने की चुनौती डेल्फी-टीवीएस टेक्नॉलॉजीज् लि. (डी.टी.वी.एस.) के सामने थी। इसी उद्देश्य से कंपनी ने 2018 की शुरुआत में सेंटरलेस ग्राउंड 'फ्युएल इंजेक्शन नीडल' (चित्र क्र. 11) ब्लैंक्स का वितरण करने के लिए नाशिक स्थित पैटको प्रिसिजन कंपोनंटस् को सप्लाइअर नियुक्त किया। यह पुर्जा हाइ स्पीड स्टील (HSS) के इस्तेमाल से बनाना था। स्लाइडिंग हेड सी.एन. सी. पर उसका टर्निंग करना था, 64+ HRC पर उसे निर्वात उष्मोपचार (वैक्युम हीट ट्रीटमेंट) देना था और बाद में प्लंजिंग पद्धती से उसका ग्राइंडिंग करना था।
अचूक यंत्रण के संदर्भ में पैटको का काम उत्कृष्ट था लेकिन उन्हे ग्राइंडिंग का ज्यादा अनुभव नहीं था। डी.टी. वी.एस. ने इस उत्पाद के लिए जिन विकल्पों के बारे में सोचा, उनमें से केवल एक भारतीय था। कंपनी ने ऐसे ही एक अैप्लिकेशन के लिए पहले आयात मशीन का इस्तेमाल किया था, भारतीय CLG मशीन कभी भी खरीदा नहीं था। फिर भी डी.टी.वी.एस. के उत्पादन अभियांत्रिकी विभाग ने (PED) अध्ययन कर के, MGTL की CLG 5020-4 सी.एन.सी. मशीन चुनने का निर्णय लिया।
MGTB में बनाई जा रही मशीन का इस्तेमाल 'जेट' इस अन्य पुर्जे के लिए किया जाने वाला था। उसमें प्रति लोड 2 नग की जरूरत थी। MGTB ने दो महीनों में प्री-ऑर्डर टेस्ट पूरी की। उसमें व्यासों के बारेमें ±2.5μm तथा गोलाई/ एकरेखीयता में 5μm टॉलरन्स पाया गया, जिससे डी.टी.वी.एस. का विश्वास बढ़ा।
मशीन का निर्माण 7 महीनों में पूरा हुआ। इसमें 4 अक्ष के लिए सी.एन. सी. नियंत्रण, ग्राइंडिंग वील पर फॉर्म तथा प्रोफाइल ड्रेसिंग के लिए डाइमंड रोलर ड्रेसर, बाउल फीडर, पिक अैंड प्लेस रोबो, पोकायोके कॉग्नेक्स कैमरा, कंट्रोल वील के पास बेल्ट कन्वेयर पर कार्यवस्तु के लोडिंग एवं अनलोडिंग के लिए एक अक्षीय सर्वो गैन्ट्री आदि के समेत स्वचालित लोड अनलोड सिस्टम (चित्र क्र. 12) का समावेश था।
डी.टी.वी.एस.एम.ई. तथा पैटको प्रोजेक्ट टीम के सक्रिय सहयोग से MGTB ने बारी बारी से 2 कार्यवस्तुओं के उत्पादन का प्रात्यक्षिक बार बार कर के, प्रणाली ऑपरेटर के लिए सुलभ होने का दावा सिद्ध किया। कारखाने में भी सभी परीक्षण सफल कर के, टिकाऊ होने के नमूने पूरे किए।
2018 के उत्तरार्ध में ग्राहक के पास शुरु रखने की मान्यता मिली। पूरी वैल्यू सिस्टम पर (अर्थात मटीरीयल, यंत्रण, एच.टी. (मुड़े हुए भाग) तथा ग्राइंडिंग) पकड़ पाने तथा उसके प्रबंधन के लिए उन्हें थोड़ा समय लगा। अगस्त 2019 के आखिर तक कई चुनौतियों का सामना करना पड़ा, जैसे कि लोड/अनलोड प्रणाली थम जाना, बाउल फीडर में नीडल अटकना, दर्जा एकसमान न होना आदि।
एक बार वॉट्सएप पर एक संदेश मिला; 'प्रॉडक्शन ऑटो मोड - असाधारण आवाज - मशीन इमर्जन्सी मोड- GW, CW तथा वर्करेस्ट ब्लेड का नुकसान हुआ है। क्षतिग्रस्त पुर्जा पिघल कर ब्लेड पर चिपक गया है।' कंपनी के उत्पादन में कोई भी रुकावट ना आए इसलिए हमने तुरंत पैटको में तंत्रज्ञों की एक टीम भेजी। इस टीम तथा पैटको के विशेषज्ञों ने इस समस्या पर गंभीरता से विचार किया। चर्चा के उपरांत इस समस्या की वजह का पता चला जो इस प्रकार थी; 'ग्राइंडिंग किया पुर्जा कन्वेयर पर अनलोड ना हो कर वर्करेस्ट ब्लेड के पास अटक जाने के कारण यह दुर्घटना हुई।' खोज का केंद्रबिंदु रहा कि क्या 28 अगस्त 2019 से किसी इनपुट में बदलाव आया है अथवा किसी नए इनपुट को प्रविष्ट किया गया है, जो मूल निर्देशों (स्पेसिफिकेशन) से अनुरुप नही है?
उसके बाद एक दिन के वर्कशॉप का आयोजन किया गया। इसमें मशीन और इनपुट, कार्यवस्तु आदि दोनों के संदर्भ में बदलाव किए गए। पैटको की टीम को समस्या निवारण का प्रशिक्षण दिया गया। इसके बाद तीन महीने कोई समस्या नहीं थी। तीन महीने बाद, 28 नवंबर 2019 पर डिफेन्स के लिए पुर्जे बनाने वाली उत्पादन लाइन बंद हो गई। वर्करेस्ट टेबल पर एक पुर्जा अटक जाने से यह हुआ था। असाधारण टॉर्क के बारे में चेतावनी देने वाला अलार्म 'रीसेट' हो गया था तथा वह पुर्जा उस स्थान से हटाया नहीं गया था। इससे ब्लेड खराब हुआ। मशीन में असाधारण टॉर्क की चेतावनी देने वाली सुविधा शामिल है। ऑपरेटर ने अलार्म रीसेट करने के बजाय, उसकी वजह जांची होती तो ब्लेड खराब ना होता। MGT ने डिफेन्स के लिए उत्पादन करने वाली दूसरी लाइन तुरंत शुरु कर दी और पुर्जा को तुरंत दूर करने के लिए एक और चेतावनी का समावेश किया।
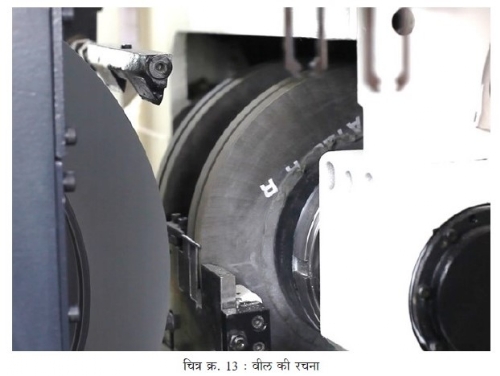
ग्राइंडिंग वील (चित्र क्र. 13, 14) तथा अक्षों को स्वाभाविक रुप से नियंत्रित करने वाला रीसेट बटन, 'होम' में रखा गया। आज हमेशा की तरह MGT ने सुनिश्चित किया है कि, ऑटोमेशन के हर उपप्रणाली सप्लाइअर द्वारा (इंटिग्रेटर-टेस्पा रोबोटिक्स) मूल्य प्रवाह का (वैल्यू स्ट्रीम) पुनर्मूल्यांकन करने के बाद प्रक्रिया पर पैटको का अधिकार रहेगा तथा उनका आत्मबल भी बढ़ेगा। इस दौरान पैटको के इनपुट गुणवत्ता का नियंत्रण डी.टी.वी.एस. करती है और पैटको का एक दिन का औसतन उत्पादन साडेतीन हजार से अधिक है।
महेश समारिया
डिजाइन अैंडअैप्लिकेशन हेड, माइक्रोमैटिक ग्राइंडिंग टेक्नॉलॉजीज लि.
9741300644
mahesh.samaria@ micromaticgrinding.com
महेश समारिया ने यांत्रिकी अभियांत्रिकी की शिक्षा ग्रहण की है। आपको सिलिंड्रिकल, सेंटरलेस, डबल डिस्क, एस.पी.एम. आदि विभिन्न ग्राइंडिंग मशीन पर काम का लंबा तजुर्बा है। वर्तमान में आप बंगलुरु की माइक्रोमैटिक ग्राइंडिंग टेक्नॉलॉजीज् लि. में डिजाइन तथा अैप्लिकेशन हेड हैं।