मशीन शॉप में और अन्य कई स्थानों पर, जहाँ उत्पादन किया जाता है, वहीं उत्पादों (प्रॉडक्ट) की जांच करना आवश्यक होता है। जांच हेतु हम विभिन्न जांच साधनों (मेजरिंग इंस्ट्रुमेंट) का इस्तेमाल करते हैं। लगातार इस्तेमाल करने से, कुछ समय बाद उनमें त्रुटियां (एरर) आती हैं। इन्हें दूर करना जरूरी होता है। त्रुटित साधनों के उपयोग से जांच और मापन अचूक नहीं होगा। फलस्वरूप ग्राहक को दोषरहित माल की आपूर्ति नहीं होगी। इससे बचने के लिए कैलिब्रेशन करना आवश्यक है।
कैलिब्रेशन का मतलब है, इस्तेमाल किए जाने वाले मापन उपकरणों की किसी मानक (स्टैंडर्ड) से तुलना करना और हमारे मापन उपकरणों में कितनी त्रुटियां हैं यह निश्चित करना। उपकरण की त्रुटि दूर करना भी कैलिब्रेशन का एक भाग है।
कैलिब्रेशन के मुख्य उद्देश्य1. मापन उपकरणों की अचूकता जांचना।
2. मापन पद्धति की खोजक्षमता (ट्रेसेबिलिटी) निश्चित करना।
3. उत्पाद की उत्तम जांच के लिए उपकरण में अचूकता बनाए रखना, ताकि ग्राहक को उचित आपूर्ति हो कर उसकी संतुष्टि हो जाए।
बाहरी माइक्रोमीटर स्क्रू गेजकैलिब्रेशन के संदर्भ में हम बाहरी माइक्रोमीटर स्क्रू गेज की मिसाल देखते हैं।
इस माइक्रोमीटर में मुख्य स्केल की अचूकता का कैलिब्रेशन करना है। इस उपकरण में शून्य त्रुटि है, यह जांचने के लिए माइक्रोमीटर शून्य रीडिंग पर लाया जाता है। उसकी समतलता (फ्लैटनेस) और समानांतरता उचित होने की पुष्टि की जाती है। माइक्रोमीटर की स्केल का कैलिब्रेशन करने हेतु स्लिप गेज का उपयोग किया जाता है। ये स्लिप गेज भी कैलिब्रेट किए होते हैं।
कैलिब्रेशन की आवश्यकता1. इस्तेमाल किए जाने के कारण मापन उपकरणों में घिसाव से त्रुटि हो सकती है।
2. इलेक्ट्रिक और मेकैनिकल शॉक के कारण मापन उपकरणों में त्रुटि हो सकती है।
3. जोखिम से भरे वातावरण, उनमें रखे गए मापन उपकरण में त्रुटि पैदा कर सकते हैं। जैसे कि अति उच्च तापमान, ऑईल, धातु की चिप आदि।
उपरोक्त सभी या उनमें से कोई भी गतिविधि के मामले में कैलिब्रेशन करना जरूरी है। कैलिब्रेशन के बारे में गलतफहमियांकैलिब्रेशन के बारे में कई गलतफहमियां है, उनमें से चुनिंदा पर हम नजर ड़ालते हैं। विभिन्न कंपनियों में ऑडिट करते समय आगे दी गई बातों के बारे में पता चलता है।
1. चूंकि हम अच्छे (स्टैंडर्ड) कंपनियों के ही उपकरण इस्तेमाल करते हैं, हमें कैलिब्रेशन की आवश्यकता नहीं।
तथ्य : मापन के लिए कितनी भी अच्छी कंपनी के उपकरण इस्तेमाल करने पर भी उसमें त्रुटि आती ही है इसलिए कैलिब्रेशन जरूरी है।
2. हमने नया उपकरण लाया है, जो पिछले 6 महीनों से इस्तेमाल में नहीं है। अब इस्तेमाल कर रहें हैं इसलिए हमें कैलिब्रेशन की जरूरत महसूस नहीं होती।
तथ्य : मापन उपकरण नया हो लेकिन उसे बिना इस्तेमाल कुछ समय के लिए रख देने पर भी उसमें त्रुटि हो सकती है। इसलिए मापन का कोई भी उपकरण इस्तेमाल करने से पहले वह कैलिब्रेटेड है या नहीं जरूर देखें।
3. हमारे उपकरणों की कीमत से उपकरणों के कैलिब्रेशन का खर्चा अधिक है।
तथ्य : यह बात कुछ हद तक सच है, लेकिन किसी भी स्थिति में उपकरण कैलिब्रेट करना अति आवश्यक है। इसका समाधान यह हो सकता है कि उपलब्ध उपकरण का कैलिब्रेशन करने के बजाय कैलिब्रेट किया हुआ नया उपकरण खरीदें।
4. कैलिब्रेशन, किसी बाहरी संस्था द्वारा किया जाना चाहिए।
तथ्य : यह एक बहुत बड़ी गलतफहमी है। हम हमारे मापन उपकरणों का खुद की कंपनी में कैलिब्रेशन कर सकते हैं। इसके लिए आगे दी गई बातों की पुष्टि/पूर्तता करनी पड़ती हैं।
· कर्मचारियों को कैलिब्रेशन की जानकारी होनी चाहिए। वें (विशेष रूप से प्रतिष्ठित प्रशिक्षण संस्था से) कैलिब्रेशन विषय में प्रशिक्षित होने चाहिए।
· जहाँ कैलिब्रेशन किया जाता है वहाँ ISO मानक के अनुसार तापमान और अन्य बातों का ध्यान रखा जाना चाहिए, जैसे कि कंपन (वाइब्रेशन)।
· कैलिब्रेशन के लिए जरूरी अंतर्राष्ट्रीय मानक (स्टैंडर्ड) उपलब्ध होने चाहिए।
· कैलिब्रेशन के काम से संबंधि मानक कार्यपद्धति (SOP) तैयार कर के वह उचित स्थान पर उपलब्ध करवाए।
· कैलिब्रेशन करने हेतु जिन उपकरणों का इस्तेमाल करना है उनकी अचूकता, मापन किए जाने वाले उपकरणों की अचूकता से दस गुना होनी चाहिए। कई स्थान पर अचूकता का 3:1 अनुपात भी स्वीकार्य है।
कैलिब्रेशन की बारंबारिता कैलिब्रेशन की बारंबारिता आगे दी गई बातों पर निर्भर होती है।
1. नापे जाने वाले आयाम की जटिलता देखें। अधिक अचूकता और कम टॉलरन्स अपेक्षित हो तब बारंबारिता अधिक होनी चाहिए।
2. रोज कितने उत्पादों की जांच होती है, इसे भी देखना जरूरी है। यह आंकड़ा अधिक हो तो बारंबारिता अधिक होना आवश्यक है। उपरोक्त मुद्दे अपने अनुभव पर आधारित
होते हैं।
3. अगर काम की जगह पर अति उच्च तापमान और कंपन हो तो ऐसी स्थिति में भी कैलिब्रेशन की बारंबारिता अधिक होनी चाहिए। कैलिब्रेशन की बारंबारिता नियत मात्रा से कम न रखें, अन्यथा दोषयुक्त उत्पाद ग्राहक तक पहुंचेंगे। कैलिब्रेशन की बारंबारिता नियत मात्रा से अधिक भी ना हो, अन्यथा हमारे श्रम और पैसे बेकार हो जाएंगे। कैलिब्रेशन करते समय इसका ध्यान रखें। कैलिब्रेशन की बारंबारिता तय करने के लिए ग्राहक से जरूर मार्गदर्शन लें।
मिसाल 1 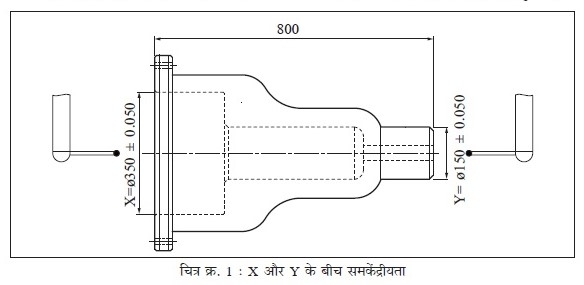
चित्र क्र. 1 में भारी वाहन के पिछले पहिये का हब दर्शाया है। यह हब 800 मिमी. लंबा और वजन में 60 किग्रै. है। इसे कास्टिंग में बनाया है। इस हब का एक बाजू का अंदरी व्यास (ID) 350 मिमी. है, जिसे हम X कहेंगे। इस हब के दुसरी बाजू का बाहरी व्यास (OD) 150 मिमी. है, हम इसे Y कहेंगे। इन दोनों व्यासों में समकेंद्रीयता 50 माइक्रोन से कम होनी चाहिए। उत्पाद करने वाली ('अ') कंपनी में एक बैच में इस प्रकार की 60 कार्यवस्तुएं बनाई गई। उसके बाद कंपनी में उनकी जांच की। उस समय कार्यवस्तु की समकेंद्रीयता 30 माइक्रोन के आसपास पाई गई। हब की बैच को ग्राहक ('ब') के पास भेजा गया। उन्होने इनमें से एक हब की नमूना जांच (सैंपल टेस्टिंग) की। तब उस हब की समकेंद्रीयता 90 माइक्रोन देखी गई। 'ब' ने किए नमूना जांच में हब फेल हुआ। उन्होनें 60 हब की पूरी बैच फेल होने के बारे में 'अ' को बताया। 'अ' के लिए यह बड़ा धक्का था। बाद में 'अ' के उत्पादन विभाग के एक अभियंता और गुणवत्ता विभाग के एक अभियंता ने 'ब' से भेंट की और जांच के बारे में पूछा। तब पता चला कि जांच सी.एम.एम. पर की गई है। उनकी पद्धति के अनुसार, किसी बैच की दो पुर्जे, जांच में अस्वीकार (रिजेक्ट) होते हो तब वह पूरी बैच रिजेक्ट की जाती है। 'अ' के कर्मचारियों ने, जांचे गए हब का फिर से सी.एम.एम. पर परीक्षण करने की बिनती की। दोबारा जांचने पर हब में समकेंद्रीयता 80 से 90 माइक्रोन के आसपास देखी गई। एक ही हब 2 अलग सी.एम.एम. पर जांचने से इतना फर्क पड़ने की वजह जानने हेतु, दोनों सी.एम.एम. के कैलिब्रेशन रिपोर्ट देखने का तय किया गया।
'अ' की मशीन का रिपोर्ट मंगवाया गया। 'ब' ने भी उनकी सी.एम.एम. का कैलिब्रेशन जांचने की बात मानी। इस हब की ज्यामिति के अनुसार उसकी आगे की तथा पिछली बाजू जांची जानी चाहिए। इसलिए सी.एम.एम. का राइट अैंगल प्रोब 00 पर और 1800 पर जाना जरूरी था। 'ब' की सी.एम.एम. कैलिब्रेट करते समय वही प्रोब 00 और 1800 पर जांचा गया, तब उसमें लगभग 83 माइक्रोन का फर्क दिखाई दिया। सी.एम.एम. कैलिब्रेट करने के बाद, इसके पहले जांचे गए हब की फिर से जांच की गई, तब वही हब 35 माइक्रोन में दिखाई दिया। इसके बाद 'अ' के कर्मचारियों ने और दो हब जांचे। वे भी अपेक्षित मर्यादा में पाए जाने पर ग्राहक ने हब की पूरी बैच स्वीकार की।
सी.एम.एम. के साथ, संदर्भ के लिए एक घनाकार ठोस वस्तु (क्यूब) दी होती है। हर रोज मशीन शुरू करने के बाद, राइट अैंगल वाला रैम उस क्यूब के पास ले जा कर प्रोब 00 और 1800 के पृष्ठ से स्पर्श कर के उसका कैलिब्रेशन करना आवश्यक होता है। इसके अलावा सी.एम.एम. पर हर 25 कार्यवस्तुओं के बाद या हर शिफ्ट में एक बार समकेंद्रीयता जांचने का नियम है। लेकिन कई कंपनियों में इसका पालन नहीं किया जाता, जिससे कई समस्याओं का सामना करना पड़ता है।
मिसाल 2 ऑटोमोबाइल क्षेत्र से संबंधित पुर्जों का उत्पादन करने वाली एक कंपनी में एक पुर्जा कास्टिंग से बनाया गया था। उसका यंत्रण करते समय एक ही बोर में शुरुआत में अंदरूनी व्यास (चित्र क्र. 2) 20 मिमी. +0.015 मिमी. और 25±0.15 मिमी. था।
शुरुआत में अलग अलग प्लग गेज के इस्तेमाल से जांच की जाती थी। दोनों आकारों के लिए (Ø20 और Ø25) स्वतंत्र मापन साधन थे।
कंपनी ने जांच का समय घटाने हेतु एक ही स्टेप प्लग गेज तैयार कर के उसका इस्तेमाल आरंभ किया था। नए प्लग गेज का कैलिब्रेशन किया था। कंपनी ने उस गेज से जांच कर के, तैयार पुर्जे के दो लॉट ग्राहक को भेज दिए। ग्राहक ने सारे पुर्जे बेकार कह कर वापस भेज दिए। उसके बाद कंपनी ने वहीं पुर्जे अन्य मापन उपकरण से जांचे, तब वो पुर्जा बेकार होने की पुष्टि हुई। उसके बाद नए तैयार किए गेज को कैलिब्रेशन करने वाली अन्य एजेंसी द्वारा जांचा गया। उस जांच में शुरुआती कैलिब्रेशन में हुई गलती के बारे में पता चला। इसके पश्चात आगे दी हुई बातों पर गौर किया गया।
· कंपनी ने शुरुआत में जिस एजेंसी से कैलिब्रेशन करवाया था वहाँ दोनों आकारों के कैलिब्रेशन के लिए एक ही उपकरण का इस्तेमाल किया गया था।
· कंपनी ने इसके लिए कंपैरेटर और बेंच माइक्रोमीटर का इस्तेमाल किया था, जिनकी अचूकता 20 माइक्रोन थी।
· कैलिब्रेशन कंपनी ने दोनों आकारों का टॉलरन्स अलग होने के कारण (Ø20 हेतु 15 माइक्रोन और Ø25 हेतु 150 माइक्रोन), Ø20 के कैलिब्रेशन के लिए अधिक अचूकता वाला उपकरण इस्तेमाल करना जरूरी (कम से कम 5 माइक्रोन अचूकता का) था।
· 15 माइक्रोन और 150 माइक्रोन में कैलिब्रेशन करते समय, कैलिब्रेशन करने वाली कंपनी की गलती हुई।
· Ø20 आकार का गेज ओवरसाइज था, लेकिन कैलिब्रेशन एजेंसी ने उसे उचित आकार का बताने के कारण पुर्जों का आकार यानि अंदरूनी व्यास भी अधिक हो कर बेकार पुर्जों का निर्माण हुआ।
यह पता चला कि उपरोक्त बातें, गलत कैलिब्रेशन किए उपकरण के इस्तेमाल के कारण हुई। कैलिब्रेशन करने के बाद आगे दिए गए मुद्दों पर ध्यान दे कर उपकरण मापन के लिए योग्य होने की पुष्टि करें, बाद में ही उसे इस्तेमाल करना उचित होगा।
· जिस उपकरण से कैलिब्रेशन किया गया हो उसकी अचूकता
· कैलिब्रेशन करने हेतु जिस उपकरण का उपयोग किया हो उसकी कैलिब्रेशन वैधता
· सभी कैलिब्रेशन रिपोर्ट अधिकृत व्यक्ति से जांचे जाने की पुष्टि करना
· कैलिब्रेशन के लिए इस्तेमाल किए गए मानक (स्टैंडर्ड)
· कैलिब्रेशन एजेंसी के NABL या तत्सम प्रमाणपत्र की वैधता