छोटे व्यास वाले छिद्रों में अंदरी चूड़ी (थ्रेड) बनाने हेतु उपयोग की जाने वाली कट टैपिंग और फॉर्म टैपिंग प्रक्रिया की विस्तारपूर्वक जानकारी इस लेख में दी गई है। साथ ही, बनाई गई चूड़ी की गुणवत्ता, टूल की अधिकतम आयु, उत्पादकता, उत्तम फिनिश जैसे मापदंड़ों पर की गई तुलनाएं भी इस लेख में प्रस्तुत की गई हैं।
टैपिंग एक सरल प्रक्रिया है। छोटे व्यास के छिद्रों में अंतर्गत चूड़ी (थ्रेड) बनाने के लिए इस प्रक्रिया का उपयोग किया जाता है। कार्यवस्तु में चूड़ी का जो आकार अपेक्षित होता है, उसका प्रतिबिंब यानि 'मिरर इमेज' होने वाली चूड़ी टैपिंग टूल पर बनाई होती है। टैपिंग करने से पहले कार्यवस्तु (कंपोनंट) का मटीरीयल, मशीन का विवरण, छिद्र का प्रकार (एक बाजू बंद है या आर पार), स्नेहक का प्रकार आदि महत्वपूर्ण बातों पर गौर करना पड़ता है। इन सभी पर विचार करने के बाद टैप का चयन करना चाहिए। टैपिंग दो प्रकार से किया जाता है, एक मटीरीयल काट कर (कट) और दूसरा मटीरीयल को आवश्यक आकार (फॉर्म) दे कर। इन दोनों पद्धतियों से टैपिंग करते समय, अचूकता जरूरी होती ही है।
कट टैपिंग प्रक्रिया
कट टैपिंग
कट टैपिंग में अधिक टॉलरन्स की चूड़ी बनाई जाती है। इसलिए यह प्रक्रिया अधिक मुश्किल नहीं होती। सिर्फ सख्त मटीरीयल का टैपिंग करते समय कट टैपिंग में मुश्किलें आती हैं। स्टेनलेस स्टील तथा फोर्ज्ड् स्टील में क्रोमियम की मात्रा अधिक होने के कारण विशेष डिजाइन के टैप तैयार किए जाते हैं, जैसे ब्लाइंड होल, डीप टैपिंग। इसमें थ्रू कूलंट होल टैपिंग करने से, शीतलक (कूलंट) का उचित प्रवाह चिप बाहर निकालने में सहायक होता है। कटिंग टूल की कार्यक्षमता, चिप के संचलन पर निर्भर करती है। चिप संचलन करने के लिए विशेष प्रकार की ज्यामिति डिजाइन की जाती है। कुछ टैप में (ऑस्टेनिटिक स्टील, फोर्ज्ड् स्टील या स्टेनलेस स्टील) चिप ब्रेकर का प्रबंध किया होता है। इससे लंबी सर्पिल (स्पाइरल) चिप के बजाय लहरेदार (कर्ल) या टुकड़ों में (कट) चिप तैयार होती हैं।
छिद्र के प्रकार से या टैप के प्रवाह के अनुसार यह तय किया जाता है कि उस चिप को कितना और कहाँ काटना है। कटिंग टैप में मटीरीयल काटा जाता है और अपेक्षित आकार तैयार होता है। कटिंग टैप में ड्रिलिंग से प्राप्त माइनर व्यास वैसा ही रहता है और चूड़ी का बाह्य व्यास तैयार किया जाता है।
फॉर्म टैपिंग
फॉर्म चूड़ी में गुणवत्ता पाने के लिए, प्री टैपिंग ड्रिलिंग अचूक करना जरूरी होता है। जहाँ कंपन हो या अधिक इस्तेमाल किया जाता हो वहाँ फॉर्मिंग अधिक लाभदायक होता है। अधिक मजबूती (स्ट्रेंग्थ) जरूरी हो और मटीरीयल फॉर्मिंग करने के लिए अनुकूल हो, तो फॉर्म टैपिंग करना बेहतर होता है। जैसे, कनेक्टिंग रॉड या क्रैंकशाफ्ट। जिन जटिल पुर्जों में कंपन, उच्च दबाव जैसी चुनौतियां होती हैं वहाँ फॉर्मिंग टैप का इस्तेमाल किया जाता है।
फॉर्मिंग में, मटीरीयल का विस्थापन (डिस्प्लेसमेंट) हो कर चूड़ी तैयार होती है। फॉर्मिंग टैप में कार्यवस्तु पर ड्रिल किया हुआ व्यास (पिच डाइमीटर) बना रहता है लेकिन माइनर व्यास बदलता है। जहाँ तन्यता गुणांक (कोईफिशंट ऑफ डक्टिलिटी) न्यूनतम 10% होगा वहाँ फॉर्मिंग टैप का उपयोग करें। कास्ट आयरन के लिए फॉर्मिंग टैप का इस्तेमाल हरगिज नहीं किया जा सकता। धातु प्रवाही (फ्लूइड) हो, तब ही फॉर्मिंग किया जा सकता है। यह टैपिंग, चूड़ी की उत्तम गुणवत्ता देता है। कोई भी परिवर्तन के बिना, चूड़ी की पकड़ने की अपेक्षित शक्ति (स्ट्रिपिंग स्ट्रेंग्थ) फॉर्म टैपिंग से प्राप्त होती है।
चित्र क्र. 1 : चूड़ी की ज्यामिती में अंतर
फॉर्म टूल से तैयार हुई चूड़ी और कट टूल से बनाई चूड़ी, इनकी ज्यामिति में काफी अंतर (चित्र क्र. 1) देखा जा सकता है। फॉर्म टैपिंग और कट टैपिंग, इन दोनों प्रकारों में नोंक पर मिलने वाली ज्यामिति भिन्न होती है। कटिंग टैप की चूड़ी की छोर को तेज धार होती है, तो फॉर्मिंग टैप की चूड़ी की छोर पर एक छोटा गड्ढ़ा होता है। फॉर्मिंग करते समय, दोनों तरफ से बह कर आने वाला मटीरीयल, केंद्र में एक दूसरे के सामने आने पर उस जगह गड्ढ़ा बनता है।
टैप की रचना
कटिंग टैप को यंत्रण छोर (कटिंग एज) होती हैं। कटिंग टैप में, चैंफर की गई सामने की चूड़ी (चित्र क्र. 2) मुख्य यंत्रण छोर होती है, जो मटीरीयल काटती है और चूड़ी बनती है। फॉर्मिंग टैप में कोई यंत्रण छोर नहीं होती, इसमें कंटूर होते हैं। उसे नुकीले बिंदु होते हैं। यह वास्तव में कार्यवस्तु के संपर्क में आने वाला हिस्सा है जो मटीरीयल निचोड़ता (स्क्वीज) है जिससे मटीरीयल प्रवाहित हो कर चूड़ी तैयार होती हैं।
चित्र क्र. 2 : टैप की रचना
कटिंग पद्धति से टैपिंग करने के बाद ड्रिल किए छिद्र का माइनर व्यास वैसा ही रहता है। जैसे, M6 X 1 टैप के लिए प्री टैपिंग होल साइज की मिसाल आगे दी गई है।
व्यास-पिच = प्री टैपिंग होल साइज, यानि 6-1 = 5 मिमी. है। यहाँ 5 मिमी. माइनर व्यास, वैसा ही रहता है। यहाँ ओवरसाइज ड्रिल करना पड़ता है।
M6 X 1 के लिए छिद्र का व्यास 5.5 मिमी. होता है। फॉर्मिंग करते समय वह 5.1 मिमी. तक कम होता है जो टॉलरन्स में होता है। इसमें एक और समस्या है कि माइनर व्यास हमेशा उचित टॉलरन्स में अपेक्षित होता है। उपरोक्त मिसाल में यह 4.9 से 5.17 मिमी. की मर्यादा में होना चाहिए। यह फॉर्म टैपिंग के बाद मिलता है, जिसके बारे में चिंता करने की आवश्यकता नहीं है। क्योंकि इस चूड़ी पर बैठने वाले उस भाग से पिच डाइमीटर पर संपर्क होता है, जिससे स्ट्रिपिंग स्ट्रेंग्थ मिलती है। उसका माइनर व्यास से कोई संबंध नहीं होता। इसी सोच से, टूल की अधिकतम आयु प्राप्त करने के लिए उचित प्री टैपिंग होल साइज की तालिका टैप उत्पादक के पास उपलब्ध होती है।
टैप के प्रकार
फॉर्म टैप के लाभ
फॉर्म पद्धति से किए गए छिद्रों में 100% निरंतर अचूकता मिलती है, क्योंकि वहाँ चिप नहीं होती। कटिंग टैप में, 10 में से 4 चूड़ी पर बेल माउथिंग होने की संभावना होती है। क्योंकि टैप लौटते समय फंसी हुई चिप उसके साथ आने से चूड़ी ओवरसाइज हो जाती है या चिप में अटक कर टैप टूटता है। फॉर्म टैपिंग चिपरहित होने के कारण, सारी समस्याएं समाप्त होती हैं। यंत्रण के पैरामीटर बढ़ा कर उत्पादकता बढ़ाई जा सकती है। चूड़ी का फिनिश बेहतर मिलता है। थ्रेड की गुणवत्ता बढ़ती है, जिसमें स्ट्रिपिंग स्ट्रेंग्थ और अन्य बातों का समावेश होता है। अप्रत्यक्ष रूप से, प्रति कार्यवस्तु लागत कम होती है। जैसे, स्टेनलेस स्टील में 4 टैप का काम एक ही टैप में होता है।
फॉर्मिंग टैप खरीदते समय शायद लागत अधिक हो सकती है, लेकिन कटिंग टैप के कारण होने वाले अप्रत्यक्ष नुकसान (टैप टूटना, चूड़ी की गुणवत्ता, मटीरीयल की अस्वीकृति) के बारे में सोचे तो फॉर्मिंग टैप अंततः किफायती होता है। इसमें कटिंग ऑपरेशन न होने के कारण छिद्रों में टैप टूटने की समस्या उत्पन्न नहीं होती। टैप अगर अंदर टूटता है तो उसे बाहर निकालना मुश्किल होता है। क्योंकि इसमें कार्यवस्तु और टैप दोनों भी खराब हो जाते हैं।
फॉर्म टैपिंग में गेज से जांच करते समय, पहली कार्यवस्तु से अंतिम कार्यवस्तु तक या पहले छिद्र से अंतिम छिद्र तक 100% निरंतरता मिलती है। जिस पल टैपिंग की लंबाई अपेक्षा से कम मिलने लगे (जैसे, 10 मिमी. की लंबाई 9.5 मिमी. होने लगे), समझ जाएं कि यह टैप के घिसाव की शुरुआत है और टैप बदल दे। यह फॉर्मिंग टूल होने के कारण टैप को तेज नहीं बनाया जा सकता। रीशार्पनिंग करने पर उसका व्यास कम होता है।
फॉर्म टैपिंग की यंत्रण गति
फिलहाल मैन्युअल टैपिंग की मात्रा बहुत कम हो रही है। मशीन टैपिंग में गति अधिक मिलती है, लेकिन उसकी भी कुछ मर्यादाएं हैं। फोर्ज्ड् स्टील के लिए 15 मीटर प्रति मिनट से अधिक गति नहीं होनी चाहिए। कटिंग टैप में 8 - 10 मीटर प्रति मिनट से अधिक गति नहीं होनी चाहिए। अगर अधिकतम पैरामीटर पर काम किया जाए तो एक टैप पर काम होता है लेकिन अगले टैप में मुश्किले आती हैं। अैल्युमिनियम के मामले में, टैपिंग की लागत में बड़ा फर्क नजर आता है। अत्यंत दर्जेदार कटिंग टैप की आयु भी उसमें 50 - 60 मीटर से अधिक नहीं मिलती। लेकिन फॉर्मिंग टैप की आयु कम से कम 110 - 130 मीटर तक मिलती है। अगर प्री टैपिंग होल उचित किया गया हो, तो इससे बेहतर आयु मिलती है। फेरस मटीरीयल पर टैपिंग करने के लिए अगर निरंतरता, आयु, गुणवत्ता आदि के बारे में मुश्किलें हो तब ही फॉर्म टैपिंग विकल्प चुनना उचित होता है।
टैपिंग लंबाई
चित्र क्र. 3 : विभिन्न प्रकार के कटिंग चैंफर
आम तौर पर छिद्र की कुल लंबाई में से 90 से 95% लंबाई चूड़ी की होना, यह टैपिंग की मुख्य समस्या होती है। फॉर्मिंग टैप अंदर जाने के लिए और मटीरीयल स्क्वीज करने के लिए एक टेपर होता है। कटिंग टैप में अंदर जाने के लिए और काटने के लिए चैंफर (चित्र क्र. 3) होता है। इस भाग में आधी चूड़ी होती है, जिसकी लंबाई सामान्यतः 2.5 पिच होती है। जैसे, अगर 6 X 1 का टैप हो, तो 2.5 से 3 मिमी. लंबाई होती है। 10 मिमी. लंबाई के छिद्र में 7 मिमी. का ही टैपिंग किया जा सकता है, इससे अधिक नहीं। कम से कम चैंफर 1.5 या कम से कम क्लियरन्स 1.5 पिच जितना होता है। इसमें L/D अनुपात से कोई फर्क नहीं पड़ता। अगर कटिंग टैप हो, तो अनुपात के अनुसार फ्ल्यूट की उचित लंबाई तय करनी पड़ती है। जहाँ से चिप और शीतलक बाहर निकलते हैं उस जगह को फ्ल्यूट कहते हैं। टैप अगर फ्ल्यूट की लंबाई से अधिक अंदर जाए तो मटीरीयल अंदर फंस जाएगा। जरूरत के अनुसार फ्ल्यूट की लंबाई बढ़ाई जाती है। गहरा छिद्र होने पर चिप ब्रेकर रखना पड़ता है। पृष्ठ के अंदर 40 से 50 मिमी. गहराई पर टैपिंग करने के लिए, टैप के फ्ल्यूट की लंबाई तुलना में अधिक रखनी पड़ती है। पृष्ठ से टैप अंदर जाने पर, चिप बाहर आने के लिए 5 से 10 मिमी. जगह होना आवश्यक है।
चिप ब्रेकर की मदद से चिप का आकार नियंत्रित किया जा सकता है। चिप ब्रेकिंग के परिणाम पाने के लिए, टैप को लेपन (कोटिंग) करने के बाद यंत्रण छोर पर थोड़ा मटीरीयल निकाल कर उसे समतल (फ्लैट) बनाया जाता है। लेपन किया गया हो, तो पृष्ठ बेहद चिकना होता है। किसी भी चिकने पृष्ठ पर दूसरी वस्तु अधिक गति से सरकती है। इससे कई बार दुर्घटना हो सकती है। यही बात चिप के संदर्भ में भी लागू होती है। अगर चिप अधिक चिकने पृष्ठ के संपर्क में आती हैं तब वे तेजी से सरकती हैं और तेजी से फंसती भी हैं। इससे बचने के लिए पृष्ठ से लेपन हटाया जाता है। इस कर्तन छोर से मटीरीयल काट कर चिप तैयार होती हो, तो वे दो पृष्ठों के बीच की चिकनाई में फर्क होने के कारण टूटती हैं और छोटी चिप तैयार होती हैं। चिप नियंत्रण के विभिन्न विकल्प उपलब्ध हैं।
स्टेनलेस स्टील पर टैपिंग
स्टेनलेस स्टील जैसे चुनौतीपूर्ण मटीरीयल पर काम करने वाले टैप विकसित करते समय कुछ विशेष बातों पर गौर किया जाता है। स्टेनलेस स्टील में, विशेष रूप से SS316 प्रकार के मटीरीयल में टैपिंग करना, उसमें मौजूद क्रोमियम के कारण अधिक चुनौतीपूर्ण होता है। इस कारण, कटिंग टैप की तुलना में फॉर्मिंग टैप प्रक्रिया सुलभ होती है। फॉर्मिंग टैप में आम तौर पर 5 से 10% कोबाल्ट होता है। कोबाल्ट का प्रतिशत जितना अधिक होगा, उतनी टैप की कठोरता और मजबूती अधिक होती है। इससे टूल की आयु बढ़ती है।
मटीरीयल के अनुसार फॉर्मिंग टैप का डिजाइन बदलता है। स्टैंडर्ड टैप को 4 हाइ पॉइंट होते हैं, स्टेनलेस स्टील या फोर्ज्ड् स्टील में इस्तेमाल होने वाले टैप (चित्र क्र. 4अ और 4ब) को अधिक हाइ पॉइंट होते हैं। इसके साथ अन्य ज्यामिति भी बदलती है। प्रत्येक मटीरीयल के अनुसार, त्रिज्या और फॉर्म में फर्क आता है।
चित्र क्र. 4 अ चित्र क्र. 4 ब
स्टेनलेस स्टील में फॉर्म टैपिंग करते समय आगे दी गई बातें महत्वपूर्ण होती हैं। पहली बात है स्टेनलेस स्टील की तन्यता (डक्टिलिटी), जो इस काम के लिए उपयुक्त होती है। दूसरी बात ध्यान में रखें कि व्यास और पिच के हिसाब से प्री टैपिंग होल साइज बदलें। तीसरी और सबसे महत्वपूर्ण बात स्नेहन की है। कटिंग टैप में इसकी दोहरी आवश्यकता होती है। एक, मटीरीयल ठंड़ा करना और दूसरी, चिप को प्रवाह के साथ बहा कर लाना। चूंकि फॉर्मिंग टैप में कटिंग न हो कर सिर्फ घर्षण होता है, उस जगह ठंड़ेपन से बेहतर स्नेहन क्षमता का होना अधिक आवश्यक है। इसी लिए उच्च कोटि के स्नेहन गुणों वाला शीतलक अथवा 'नीट कटिंग ऑईल' जरूरी होता है। नीट कटिंग ऑईल की स्नेहन क्षमता अधिक होने के कारण उसे प्राथमिकता दी जाती है। कटिंग टैप में निकलने वाला मटीरीयल टैप पर चिपकता (कोल्ड वेल्डिंग) है। इसे टालने के लिए शीतलक में ऑईल के बजाय पानी की मात्रा अधिक होना आवश्यक है। उसी के साथ दबाव (प्रेशर) भी अधिक जरूरी होगा। गुणवत्तापूर्ण शीतलक के साथ, उसकी दिशा भी उतनी ही महत्वपूर्ण होती है। फॉर्मिंग टैप में उसकी जरूरत नहीं होती। लेकिन कटिंग टैप में उसका अहम् स्थान होता है।
कई बार आर पार छिद्रों में टैपिंग करते समय अंदर से और बाहर से, दोनों तरफ से शीतलक दिया जाता है। फलस्वरूप, अंदरी शीतलक के कारण बाहर आया हुआ कूड़ा, बाहरी शीतलक द्वारा फिर से अंदर धकेला जाता है। इससे बचने के लिए हम एक विकल्प देते हैं। 4 छिद्र एक तरफ से बंद (ब्लाइंड) होगे और 6 छिद्र आर पार होगे, तो आर पार छिद्रों में सिर्फ बाह्य शीतलक शुरू रहता है और अंतर्गत शीतलक बंद रहता है। एक तरफ से बंद किए छिद्रों में इसके विपरित प्रक्रिया होती है। एक तरफ से बंद छिद्रों में टैपिंग करते समय, शीतलक की दिशा हमेशा टैप की अक्ष की दिशा में (चित्र क्र. 5अ) होनी चाहिए।
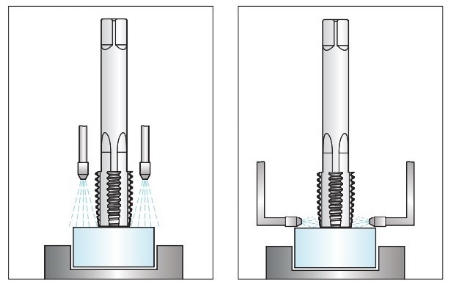
चित्र क्र. 5 अ : उचित पद्धति चित्र क्र. 5 ब : गलत पद्धति
कई बार टैप जिस दिशा में जाता है उसके 90° में शीतलक का प्रबंध (चित्र क्र. 5ब) किया जाता है। शीतलक टैप की अक्ष की दिशा में देना और उसके 90° में देना, इसमें काफी अंतर पड़ता है। टैप की अक्ष की दिशा में शीतलक देने पर वह टैप से लुढ़क जाता है, 90° में देने पर वह टैप पर गिर कर बाहर फेंका जाता है।
कट टैपिंग में टैप ठंड़ा करने के लिए शीतलक का इस्तेमाल किया जाता है। फॉर्म टैपिंग में टैप ठंड़ा करने की अनुमति नहीं होती। कट टैपिंग में, टैप अंदर जाते समय मटीरीयल काटते हुए जाता है। इससे गरम हुए टैप पर काटा गया मटीरीयल न चिपके, इसलिए उसे ठंड़ा करना जरूरी होता है। फॉर्म टैपिंग में चूड़ी बनाते समय, टैप पर चूड़ी के भीतर काफी मटीरीयल शेष होता है। अगर मटीरीयल ठंड़ा होने दिया जाए तब वह उधर ही इकठ्ठा हो जाता है। इसलिए फॉर्म टैपिंग में ऐसे शीतलक को चुनें जिसकी स्नेहनक्षमता, उसकी शीतनक्षमता से अधिक हो।
मिसाल
टैपिंग किया जाने वाला मटीरीयल : स्टेनलेस स्टील 316
टैप का आकार : M6 X 1
टैपिंग की गहराई : 15 मिमी.
मशीन : वी.एम.सी.
स्नेहन : इमल्सिफाइड
स्टेनलेस स्टील पर कट टैपिंग करते समय आने वाली मुश्किलें
1. चिप क्लॉगिंग के कारण टैप बार बार टूटना (चित्र क्र. 6)।
चित्र क्र. 6 : टूटा टैप
2. टैप की कर्तन छोर (चित्र क्र. 7) बार बार चिप ऑफ् होना।
चित्र क्र. 7 : यत्रण छोर बेकार हुआ टैप
3. चूड़ी पर मिलने वाला फिनिश (चित्र क्र. 8) अच्छा नहीं होना (थ्रेड टॉर्न ऑफ्)
चित्र क्र. 8 : बेकार हुई चूड़ी
4. टैपिंग करते समय लंबे चिप तैयार होने से वे उलझ (चित्र क्र. 9) जाना।
चित्र क्र. 9 : टैप के इर्द गिर्द उलझी चिप
तालिका क्र. 1
कट टैपिंग के बजाय फॉर्म टैपिंग के इस्तेमाल से हुए लाभ तालिका क्र. 1 में दिए हैं। फॉर्म टैपिंग में तैयार की गई चूड़ी चित्र क्र. 10 में दर्शाई है।
चित्र क्र. 10 : फॉर्म टैपिंग से बनाई चूड़ी
स्पिंडल लोड नियंत्रण
पारंपरिक मशीन हो या सी.एन.सी. मशीन, स्टेनलेस स्टील मटीरीयल पर फॉर्मिंग टैप इस्तेमाल किए जा सकते हैं। हम पारंपरिक या सी.एन.सी. मशीन पर, ग्राहक को रिजिड टैपिंग का सुझाव देते हैं। आम तौर पर रेडियल तथा अैक्शियल इन दोनों दिशाओं में फ्लोट होने वाली अटैचमेंट, टैप के साथ आती है। पारंपारिक अटैचमेंट में अैक्शियल फ्लोट को क्लच होता है। अटैचमेंट पर होने वाला टॉर्क विशिष्ट मर्यादा तक जाने पर क्लच डिसएंगेज होता है और टैप का पहला फीड रूकता है। टैपिंग का निरंतर काम शुरू हो, तब 25-30 कार्यवस्तु होने के बाद टैपिंग की लंबाई कम होती दिखाई देती है। टैप ठीक होता है लेकिन कुछ निश्चित उपयोग के बाद उसकी टॉर्क की आवश्यकता बढ़ जाती है, जिससे अटैचमेंट पर लोड बढ़ता है। उसके बढ़ते ही, क्लच डिसएंगेज हो कर फीड रूकता है। लेकिन मॉनिटर में काम शुरू दिखाई देता है। यही काम रिजिड टैप पर करने से, इस प्रकार कोई रचना न होने के कारण अपेक्षित लंबाई मिलती है। टैप का आवश्यक अधिकतम टॉर्क, मशीन की मर्यादा के बाहर नहीं होता। कार्यवस्तु पर मर्यादा से कम लंबाई मिलती हो, तो टैप बदलना पड़ता है।
रिजिड टैपिंग में टैप भोंथरा होने पर भी उसे इस्तेमाल करने पर, पॉवर मीटर पर स्पिंडल द्वारा उपयोग की जाने वाली शक्ति दर्शाई जाती है। कटिंग टैप इस्तेमाल करते समय स्पिंडल लोड 10-12% अधिक होने पर, भले ही गेज जांच में कार्यवस्तु स्वीकृत हो, हम टैप हटाने का सुझाव देते हैं। क्योंकि उसके बाद वह किसी भी पल टूट सकता है। यह स्थिति फॉर्मिंग टैप में देखी जा सकती है। स्पिंडल लोड बढ़ने पर हम टैप बदलने का सुझाव देते हैं।
प्री टैपिंग होल साइज
टैपिंग में, प्री टैपिंग होल साइज इस घटक की अहम् भूमिका होती है। प्री टैपिंग होल साइज जितना बड़ा होगा (टॉलरन्स की अधिकतम मर्यादा में), टैप को उतना ही टॉर्क कम आवश्यक होगा। टैप की आयु बेहतर मिलेगी। जब कम आकार के छिद्र बनाए जाते हैं तब घर्षण बढ़ता है और टैप पर कोल्ड वेल्डिंग भी होता है। टैप पूरी तरह से बेकार होता है। और तो और, बनाई हुई चूड़ी भी खराब हो जाती है।
हाथ से (मैन्युअली) टैपिंग करते समय टैप फॉर्वर्ड और रिवर्स, इन दोनों पद्धतियों से घुमाए जाते हैं। लेकिन मशीन पर एक ही दिशा में काम किया जाता है। हाथ से टैपिंग करते समय, काम की अचूकता व्यक्ति के कौशल पर निर्भर होती है। ब्रोचिंग में विशिष्ट टेपर से ब्रोच का व्यास बढ़ता है। लेकिन टैपिंग में तत्व भले ही समान हो फिर भी टैपिंग की पहली पूरी चूड़ी को अपेक्षित व्यास और फिनिश मिलता है। अगली सभी चूड़ी सिर्फ आधार के लिए होती हैं। टैपिंग में L/D का अनुपात जब 2 से बढ़ता हो, तो कट टैपिंग के बजाय फॉर्म टैपिंग प्रक्रिया अधिक सुलभ होती है। चूंकि इस प्रक्रिया में कहीं भी चिप तैयार नहीं होती, टैपिंग कितना भी गहरा होने से प्रक्रिया पर असर नहीं होता। आर पार छिद्रों के लिए फॉर्म टैपिंग अत्यंत सरल होता है। आर पार छिद्रों के लिए विशेष ज्यामिति वाले कटिंग टैप भी इस्तेमाल किए जा सकते हैं। इसमें 'गैश' (चित्र क्र. 11) वाले राइट हैंड कटिंग टैप को, लेफ्ट हैंड हेलिक्स होता है। कटिंग के दौरान इस हेलिक्स के कारण चिप नीचे जाती हैं। अर्थात जब टैप घूमता हो, तो वह चिप से मुक्त रहता है। इससे आर पार छिद्रों के टैपिंग में मुश्किलें नहीं आती।
चित्र क्र. 11
शुरुआती दौर में, माइनर व्यास उचित न आने जैसे कारणों से फॉर्म टैपिंग का स्वीकार नहीं होता था। वास्तव में जहाँ रिसाव प्रतिरोधक (लीकेज प्रूफ) जोड़ की आवश्यकता न हो और चूड़ी द्वारा सिर्फ निर्धारित भार सहा जाना अपेक्षित हो वहाँ माइनर व्यास की अचूकता कोई मायने नहीं रखती। ये तथा अन्य मुद्दे जब लोग मानने लगे, तब से फॉर्मिंग टैप को स्वीकृती मिलने लगी। अब इसके लाभ जानने के बाद इसका इस्तेमाल बढ़ने लगा है।
9823019238
[email protected]
सौरभ सोनटक्के एमके टूल्स में विभागीय प्रबंधक हैं। आपको इस क्षेत्र का 27 से अधिक वर्षों का अनुभव है।