किसी भी उद्यम में शीट मेटलसंबंधि कामों में अधिक अचूकता आवश्यक हो, तो ऐसे काम लेजर कर्तन ( laser cutting ) द्वारा करना ही बेहतर होता है। लेजर एक उष्माधारित (थर्मल) प्रक्रिया होने पर भी, मूल मटीरीयल का विरूपण न्यूनतम रखते हुए आयामों की अचूकता प्राप्त करना इसमें आसानी से संभव है। लेजर तकनीक की यात्रा, प्रक्रिया, इस्तेमाल जैसे मुद्दों के बारे में इस लेख में विस्तारपूर्वक बताया गया है।
लगभग 60 के दशक के आरंभ में धातु के लिए लेजर कटिंग की तकनीक का उपयोग शुरू हुआ। शुरुआती दौर में यूरप में इसका इस्तेमाल बढ़ता गया। भारत में 1983-84 के आसपास इंदौर में एक मशीन आई, फिर टेल्को ने 1984-85 के आसपास प्रोटोटाइपिंग उत्पादन हेतु एक मशीन खरीदी। यहीं से सही मायने में भारतीय उद्योग क्षेत्र में लेजर तकनीक के इस्तेमाल का आरंभ हुआ।
उस समय वाहन निर्माण में, शीट मेटल काट कर उसके अपेक्षित कच्चे आकार (ब्लैंक) तैयार करने पड़ते थे। इसके बाद उसे उचित आकार दे कर (फॉर्मिंग), अतिरिक्त मटीरीयल काटना (ट्रिमिंग) पड़ता था। इसकी डाइ बनाने के लिए भी काफी समय लगता था। नमूना उत्पाद (प्रोटोटाइप) बनाने के लिए यह किफायती नहीं था। इसलिए वे सारी चद्दरें हाथों से काटी जाती थी। अल्प मात्रा में साफ्ट टूल विकसित कर के फॉर्मिंग किया जाता था, लेकिन उसके बाद मटीरीयल काटने की समस्या थी। इसी लिए टेल्को ने उस समय इंग्लैंड की एक कंपनी से 3D लेजर कटिंग मशीन खरीदी। उस मशीन में ब्लैंकिंग, ट्रिमिंग जैसे सारी प्रक्रियाएं की जाती थी।
टेल्को की नौकरी छोड़ कर मैंने अपना कारखाना शुरू करते समय सोचा कि सारी चीजें नई तकनीक वाली तथा समय के अनुरूप हो। 3D लेजर मशीन बेहद महंगी थी, इसलिए सारे मुद्दों का अध्ययन कर के हमने फ्लैट बेड 2D मशीन लाने पर विचार किया और वह मशीन (चित्र क्र. 1) आयात की।
उसी समय, एक बड़ी कंपनी के नए वाहन के भागों का ब्लैंकिंग करने का काम हमें मिला। तब हमनें 6 महीने कड़ी मेहनत कर के उस तकनीक को सिद्ध किया। प्रोटोटाइप हेतु इस्तेमाल होने वाले इस मशीन पर हमनें थोक उत्पादन लिया। उस वक्त हमारे कारखाने के दरवाजे पर ट्रक खड़े रहते थे, मटीरीयल पड़ा रहता था और हमारी मशीन 24 घंटे शुरू रहती थी। उस मशीन से हम ग्राहक की गाड़ी के एक मॉडल के 75 प्रकार के भाग तैयार करते थे। जैसे कि आउटर डोर पैनल, इनर डोर पैनल, B पिलर, C पिलर, टेल गेट इनर, टेल गेट आउटर, लोर पैनल, हूड का इनर और आउटर पार्ट आदि। प्रति महीना हर एक के हमने लगभग 100 सेट बनाए। हमने 5 महीने तक ये काम किया।
पुणे, मुंबई और बाद में पूरे देश में यह तकनीक कहाँ और कैसे उपयुक्त होगी इसका हमने धीरे धीरे अध्ययन किया। तब तक कई बहुराष्ट्रीय कंपनियां इस तकनीक से परिचित हो गई थी। इसलिए उनके कारखानों में जल्द ही इस तकनीक के इस्तेमाल का मौका हमें मिला। अन्य तकनीक की तुलना में लेजर तकनीक बेहद तेजी से स्थापित और कम समय में लोकप्रिय भी हुई। छोटे आकार के पुर्जे, प्रोटोटाइप आदि के लिए लेजर तकनीक की शुरुआत हो चुकी थी।
लेजर प्रक्रिया
लेजर, उष्मा पर आधारित (थर्मल) प्रक्रिया है। गैस कटिंग हो या प्लाज्मा कटिंग, कोई भी भाग काटने पर उस स्थान पर 'हीट अफेक्टेड जोन' तैयार होता है, जिससे फॉर्मिंग में कभी कभार मुश्किल हो सकती है। धातु थोड़ी कठोर (हार्ड) हो सकती है, लेकिन लेजर प्रक्रिया से हीट अफेक्टेड जोन न्यूनतम (मिनिमल) होने से, मटीरीयल के गुणधर्म (प्रॉपर्टी) बिल्कुल भी नहीं बदलते। 4-5 मिमी. मोटी शीट लेजर से काटने पर मिलने वाला हीट अफेक्टेड जोन 0.25 मिमी. चौड़ा होता है। प्लाज्मा कटिंग से काम करने पर यहीं जोन लगभग 5 से 7 मिमी. चौड़ा होता है, तो गैस कटिंग में यही जोन 10 से 15 मिमी. चौड़ा होता है। लेजर प्रक्रिया ठंड़े काट (कोल्ड कट) जितनी उत्कृष्ट होती है। लेजर प्रक्रिया के दौरान बर नहीं निकलती। ब्लैंकिंग डाइ के इस्तेमाल से तैयार भागों की अचूकता और लेजर से मिलने वाली अचूकता एकसमान होती है। लेजर द्वारा 1 मीटर में ± 0.25 मिमी. तक अचूकता मिलती है। गैस कटिंग या प्लाज्मा कटिंग से 1 मीटर में ±2 मिमी. तक अचूकता मिलती है। चूंकि लेजर की किरणें, उनका तय किया गया मार्ग नहीं बदलती, पुर्जों के आयामों में निरंतरता बनी रहती है। प्लाज्मा कटिंग में मटीरीयल अधिक मात्रा में जलता है, इसलिए लेजर की तुलना में उसकी अचूकता कम होती है। प्लाज्मा कटिंग में मटीरीयल काटते समय उसकी छोर (एज) पर ढ़ाल (टेपर) आता है। लेजर में इस टेपर की मात्रा कम होती है। 15 मिमी. मोटा मटीरीयल लेजर से काटने पर 1 मिमी. टेपर पैदा होता है। वहीं प्लाज्मा से काटने पर, सामान्यतः 4 मिमी. तक टेपर हो सकता है। कुछ पुर्जों का टॉलरन्स, गैस और प्लाज्मा कटिंग से नहीं प्राप्त किया जा सकता, उसके लिए लेजर का ही इस्तेमाल करना पड़ता है।
लेजर के दो प्रकार होते हैं। एक है CO2 लेजर, जो गैस से तैयार होता है, दूसरा है फाइबर लेजर, जो ठोस (सॉलिड) मटीरीयल से तैयार होता है। CO2 लेजर की तुलना में फाइबर लेजर मशीन (चित्र क्र. 2) चुस्त होती है।
मटीरीयल
लेजर कटिंग के लिए इस्तेमाल किया जाने वाला मटीरीयल विशेष गुणवत्ता का होना आवश्यक होता है। सही उष्मोपचार (हीट ट्रीटमेंट) दे कर इसमें से तनाव (स्ट्रेस) पूरी तरह से निकाल देना, इसकी प्राथमिक आवश्यकता होती है। अन्यथा मटीरीयल काटने के बाद वहाँ का तनाव निकल जाने से विरूपण (डिस्टॉर्शन) हो सकता है। पतले या महीन (थिन) मटीरीयल में इसकी संभावना अधिक होती है। सभी प्रकार के मटीरीयल में यह समस्या नहीं होती। आमतौर पर कोल्ड रोल्ड (CR) मटीरीयल को, बेहतर ट्रीटमेंट के कारण यह समस्या नहीं आती, हॉट रोल्ड (HR) मटीरीयल में यह समस्या आती है। 5-12 मिमी. मोटे मटीरीयल में अधिक समस्याएं आती हैं। स्टेनलेस स्टील बनाने की प्रक्रिया बेहतर होने के कारण इसमें कम समस्या होती है। वाहन उद्योग में अधिकतर पुर्जे या बॉडी 0.8, 1, 1.2 मिमी. मोटे होते हैं, उनमें यह समस्या नहीं होती। इससे मोटे मटीरीयल में समस्या होती है।
शुरुआत में ऐसी समस्याएं आने पर हमने एक जर्मन कंपनी से पूछा। उनसे पता चला की वहाँ विरूपण की कोई भी समस्या नहीं है। गौर करने पर हमें पता चला कि उनके कारखाने में ऊंची गुणवत्ता के उष्मोपचार से मटीरीयल तनावरहित किया जाता है। इस संदर्भ में स्टील उत्पादक जिंदाल या अन्य बहुराष्ट्रीय कंपनियों के साथ भी हम चर्चा कर रहें थे। हमनें उनसे 'लेजरेबल मटीरीयल' की मांग की, क्योंकि यूरप में इस प्रकार का मटीरीयल इस्तेमाल किया जाता था। कुछ समय प्रयास करने के बाद हमारे स्टील उत्पादक सारी जरूरी प्रक्रियाओं को विकसित कर के 'लेजरेबल मटीरीयल' की आपूर्ति करने लगे।
हम ज्यादातर स्टील का कर्तन करते हैं। ब्रास, स्टेनलेस स्टील के लिए लेजर का उपयोग किया जा सकता है। कॉपर, अैल्युमिनियम भी काटे जा सकते हैं, लेकिन लेजर से अैल्युमिनियम काटना मुश्किल होता है। इसके दो मुख्य कारण हैं, पहला है मटीरीयल की परावर्तन क्षमता (रिफ्लेक्टिविटी)। लेजर प्रकाश की किरणें होती हैं, जो परावर्तित (रिफ्लेक्ट) होती हैं। दूसरा कारण है कॉपर और अैल्युमिनियम द्वारा उष्मा वहन बहुत तेजी से होना। इससे ये धातु काटते समय अधिक उष्मा लगती है। जिस लेजर पॉवर से 20 मिमी. स्टेनलेस स्टील काटा जाता है, उतनी ही पॉवर से सिर्फ 5 मिमी. अैल्युमिनियम काटा जा सकता है। अधातु भी लेजर से काटे जा सकते हैं, लेकिन इन्हें काटते समय बड़ी मात्रा में विषैली भाप (टॉक्जिक फ्यूम) तैयार होने की समस्या होती है। ऐसे स्थान पर दर्जेदार एक्जॉस्ट प्रणाली आवश्यक होती है, जो बड़े पैमाने पर इस्तेमाल करनी पड़ती है।
मशीन की क्षमता
1994 में हमनें पहली मशीन लाई। तब उस मशीन से 10 मिमी. तक मोटी धातु काट सकते थे। आज हमारी नई मशीन से हम 25 मिमी. मोटाई की धातु काट सकते हैं।
मशीन की क्षमता के अनुसार उसमें 8 मिमी. से 20 मिमी. तक की मोटाई का मटीरीयल काटा जा सकता है। लेकिन उसकी अचूकता, मशीन उत्पादक द्वारा दी गई मर्यादा के अनुसार प्राप्त की जा सकती है। फिलहाल उपलब्ध मशीन 1 मी. x 1 मी. से 2.5 मी. x 16 मी. तक आकार के बेड वाली हो सकती हैं। इसके साथ लेजर की पॉवर यह भी महत्वपूर्ण पैरामीटर होता है। आम तौर पर इंडस्ट्री के लिए 1kW से 12kW तक शक्ती की मशीन का इस्तेमाल किया जाता है। 1kW की मशीन, 5 मिमी. तक मोटा मटीरीयल काटती है, 12kW की मशीन 35 मिमी. से 40 मिमी. तक मोटा मटीरीयल काट सकती है। 1 मी. x 1 मी. यह मशीन अधिक अचूक होती है। मशीन जितनी बड़ी, उसकी अचूकता उतनी ही कम होती जाती है।
लेजर प्रक्रिया में माप की अचूकता, काट का फिनिश, टेपर तथा विरूपण ये 4 अहम् बातें होती हैं। लेजर प्रक्रिया में हीट अफेक्टेड जोन कम होने के कारण मटीरीयल का विरूपण न्यूनतम होता है। लेजर प्रक्रिया में सामान्यतः टेपर नहीं आता, लेकिन अधिक मोटे मटीरीयल के लिए थोड़ी मात्रा में टेपर हो सकता है। बेहद सूक्ष्म किरणों द्वारा मटीरीयल काटने से अचूकता और फिनिश बेहतर मिलते हैं।
विभिन्न उपयोग
लेजर तकनीक मुख्य रूप से प्रोटोटाइपिंग के लिए उभर आई थी। विभिन्न क्षेत्रों में विभिन्न अैप्लिकेशन के अनुसार (चित्र क्र. 3, 4 और 5) इसे अपनाया गया।
हमारे उद्योग काफी हद तक कस्टमाइजेशन की ओर बढ़ रहे हैं। हमारे उद्योग कम बैच साइज क्वांटिटी के उत्पादन पर जोर दे रहें हैं। प्रेसिंग काम में कस्टमाइजेशन न होने के कारण लेजर का इस्तेमाल बढ़ रहा है। चूंकि हर लॉट अलग होता है, उसके लिए मशीन फ्लेक्जिबल होनी जरूरी होती है। इसमें कारखानेदार कई प्रकार के प्रयोग भी कर सकते हैं। इसमें सिर्फ पुर्जों का डिजाइन सही होना अपेक्षित है। वाहन उद्योग को छोड़ कर अन्य उद्योगों में अगर शीट मेटल की आवश्यकता पड़ती है तो उस पर लेजर कटिंग से ही काम किया जाता है।
कई कारखानेदार प्लाज्मा कटिंग या गैस कटिंग से अपग्रेड हो कर लेजर को अपना रहे हैं, क्योंकि अब समय के साथ लेजर प्रक्रिया की लागत भी काफी कम हुई है। पहले यह गैस कटिंग से कई गुना महंगी थी। तकनीक के विकास के साथ ये सारी कीमतें कम होती गई।
प्रोटोटाइपिंग और स्मॉल बैच क्वांटिटी के लिए लेजर तकनीक की शुरुआत हुई। समय के साथ लेजर तकनीक में कई बदलाव आए। अब लेजर एक प्रॉडक्शन टूल के रूप में प्रचलित होते नजर आ रहा है।
गैस कटिंग प्रक्रिया काफी समय लेती है क्योंकि वास्तव में, कटिंग होने के बाद फिनिशिंग के लिए संबंधि कार्यवस्तु पर कई प्रक्रियाएं करनी पड़ती हैं। लेकिन लेजर प्रक्रिया करने के बाद कोई अन्य प्रक्रिया की आवश्यकता नहीं होती, यह लेजर प्रक्रिया से बहुत बड़ा लाभ है। इसके बाद डीबरिंग करने की जरूरत नहीं होती। चित्र क्र. 5 में दर्शाया भाग लेजर से काटने पर उसे लगने वाला समय और लागत दोनों में बचत हुई है।
मिसाल
हम स्लाइडर (चित्र क्र. 6) नाम का पुर्जा तैयार करते हैं। ग्राहक को उस पुर्जे के उत्पाद की लागत कम करनी थी। इस बारे में शुरुआत से यानि डिजाइन बनाने से ग्राहक हमसे लगातार चर्चा कर रहे थे। इस स्लाइडर की असेंब्ली बेहद पेचीदा थी। प्रचलित तरीके में फैब्रिकेशन के बाद, उस पर काफी यंत्रण किया जाता था और यही उनकी लागत बढ़ा रहा था। इसी काम से यानि फैब्रिकेशन के बाद किए जाने वाले यंत्रण टालने के बारे में उनसे चर्चा हुई। इसमें विरूपण की बहुत बड़ी समस्या थी। मटीरीयल काटना, मोड़ना और बाद में उसे वेल्ड करना इन सभी में विरूपण होता है। इस विरूपण को घटाना एक चुनौती थी। इसके लिए सबसे पहले मटीरीयल दर्जेदार होना चाहिए तथा उसकी समतलता उत्कृष्ट होनी चाहिए। पहले गैस कटिंग या प्लाज्मा कटिंग से मटीरीयल काटा जाता था, उसके बजाय हमने लेजर प्रक्रिया को अपनाया। इससे कम से कम हीट अफेक्टेड जोन पैदा होते हैं और न्यूनतम विरूपण होता है।
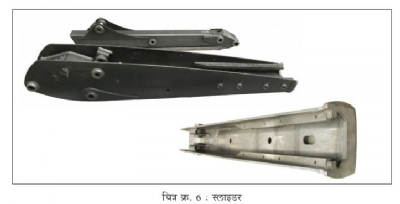
यह पुर्जा पतला और लंबा है। पुर्जा जितना लंबा और पतला होगा, विरूपण की संभावना उतनी ही बढ़ती है। इसलिए लेजर प्रक्रिया कर के उसके पैरामीटर इस तरह से स्थापित किए जिससे कम से कम विरूपण हो। उसके बाद सी.एन.सी. बेंडिंग मशीन पर मोड़ने की प्रक्रिया की, जिससे बेंडिंग के बाद मिलने वाली अचूकता अपेक्षा के अनुरूप होती है। ±30 मिनट टॉलरन्स में उसका बेंडिंग होता है। इस पुर्जे में कई छिद्र हैं और उसे कई स्थानों पर बुश वेल्ड किए गए हैं। हर छिद्र के संदर्भ केंद्र की दूरी, लेजर द्वारा बेहद अचूकता से नियंत्रित की गई। फैब्रिकेशन के बाद, बुश के बीच की दूरियां 0.5 मिमी. में नियंत्रित हुई। न्यूनतम विरूपण, केंद्र की अचूक दूरी और छिद्र की अचूकता इन तीनों पर नियंत्रण पाया गया। सी.एन.सी. बेंडिंग प्रक्रिया से बेंडिंग की अचूकता में निरंतरता रखी गई। इस पुर्जे के लिए हमनें कुछ फिक्श्चर (चित्र क्र. 7) तैयार किए। इससे उस पर वेल्डिंग करते समय, हम कार्यवस्तु सही स्थिति में रख पाए।
वेल्डिंग प्रक्रिया के बाद का विरूपण टालने हेतु हमने वेल्डिंग का अनुक्रम तय किया। एक भाग वेल्ड करने के बाद अगला भाग वेल्ड करने से पहले निश्चित समयावधि के लिए रूकना पड़ता है, ताकि वह ठंड़ा हो जाए। इस प्रकार उस पूरे पुर्जे की निर्माण प्रक्रिया तय की, जिससे यह सिद्ध हुआ कि यंत्रण के बिना भी इस पुर्जे को तैयार किया जा सकता है। इस पुर्जे के अंदर 2 फ्लैट वेल्ड किए हैं, जिनमें से तीसरा पुर्जा सरकता (स्लाइड) है। इसलिए इसे स्लाइडर या कैरियर नाम दिया गया है। यह सारी बातें प्रक्रिया में सुधार और डिजाइन में बदलाव कर के हासिल की गई। जैसे, कुछ स्थानों पर मोटाई बढ़ानी पड़ी, वेल्डिंग से बचने के उपाय खोजे गए। ऐसे सारे सुधार करते हुए उस पुर्जे पर लगभग 20% आर्थिक बचत की गई। इस प्रक्रिया को हमने पहले इस पुर्जे पर स्थापित किया और अब कई अन्य पुर्जों के लिए इसे इस्तेमाल कर रहे हैं। इन सारी प्रक्रियाओं में कहीं भी हीट ट्रीटमेंट या स्ट्रेस रीलीविंग प्रक्रियाएं शामिल नहीं हैं। कोई भी यंत्रण किए बिना, सिर्फ लेजर प्रक्रिया से उस असेंब्ली को हमनें तैयार किया।
सुरक्षित इस्तेमाल
लेजर का संचलन उचित पद्धति से न किया जाए तो वह एक अत्यंत घातक टूल हो सकता है। क्योंकि लेजर को आंखो से नहीं देखा जा सकता, उसकी पॉवर भी बहुत अधिक होती है। जिस लेजर को हम देख पाते हैं, उसकी पॉवर 1 या 2 वैट होती है। आज हमारे पास 12,000 वैट की मशीन है। लेजर के बारे में खास बात ये भी है कि लेजर किरणें, सीधी रेखा में कितनी भी दूरी पार कर सकती हैं। उनकी तीव्रता कम नहीं होती। लेजर के गुणधर्म भी नहीं बदलते, वे स्थायी होते हैं। इसलिए इस प्रक्रिया को निरंतर माना जाता है। इसी लिए लेजर मशीन में सारी सुरक्षा विशेषताओं का समावेश किया जाता है। लेजर मशीन के बाहरी बाजू पर फ्लेक्सि ग्लास नामक विशेष कांच की दीवार (चित्र क्र. 8) होती है। इस कांच से लेजर बीम विरूपित होते समय उसकी तीव्रता में कमी आती है।
लेजर किरणों को किसी भी एक जगह पर स्थिर नहीं रखा जा सकता। उन्हें निरंतर घूमता रखना पड़ता है। अगर लेजर को किसी एक जगह पर स्थिर किया जाए तो उस बिंदु के नीचे रखी कार्यवस्तु के साथ अन्य सारा मटीरीयल खराब होता है।
लेजर का हेड और कार्यवस्तु इनके बीच की दूरी बेहद महत्वपूर्ण होती है। कटिंग करना है या नहीं, अगर करना है तो उसकी गुणवत्ता किस दर्जे की होगी ऐसी सारी बातें इस दूरी पर निर्भर होती हैं। इसलिए यह दूरी हमेशा बनाई रखने हेतु मशीन में ऊंचे दर्जे की इलेक्ट्रॉनिक संवेदक (सेन्सर) तकनीक को शामिल किया जाता है। जैसे, 2 मिमी. की दूरी रखनी हो तब पूरी प्रक्रिया के दौरान उतनी ही दूरी रखी जाती है।
बड़ी शीट से विभिन्न आकार के भाग काटने हो तब नेस्टिंग तकनीक (चित्र क्र. 9) का इस्तेमाल किया जाता है। एक ही प्लेट से विभिन्न आकार के भाग काटने के लिए विशेष रचना करने से कम से कम मटीरीयल बेकार होता है। वहाँ कुछ खास टेस्टर होते हैं। दो नजदीकी भागों में काट रखने हेतु उन्हें इस्तेमाल किया जाता है। दो काट के बीच विशिष्ट रिक्ती छोड़नी पड़ती है, जो मटीरीयल की मोटाई पर निर्भर होती है। सारे मापन के बाद एक सीमा रेखा खींची जाती है। उसके बाहर का मटीरीयल बेकार जाता है।
वित्तीय घटक
लागत की दृष्टि से गैस कटिंग मशीन और लेजर कटिंग मशीन में तुलना करें तो लेजर कटिंग मशीन 8-10 गुना महंगी होती हैं। उसकी प्रक्रिया की लागत 4 गुना होती हैं। जहाँ गैस कटिंग से काम किया जा सकता है यकीनन वहाँ लेजर किफायती नहीं होता। भले ही लेजर की कीमतें कम हुई हो, उसकी प्रक्रिया महंगी होती है। यह केवल मशीन के संदर्भ में ही नहीं बल्कि उसके सारे कन्जूमेबल के बारे में भी सच है। लेकिन कुल उत्पादकता और गुणवत्ता की दृष्टि से देखें तो यह कीमतें कम लगती हैं। वैसे भी, लेजर से घटने वाली उत्पादन की लागत इस फर्क को कम करती है। साथ ही, कर्तन के बाद की जाने वाली प्रक्रियाएं न होने के कारण उनकी लागत में भी बचत होती है। इसी लिए लेजर इतने कम समय में काफी लोकप्रिय हुआ है। काम का समय कम करने हेतु यह एक प्रभावशाली प्रक्रिया है।
जब किसी पुर्जे का डिजाइन किया जाता है, तभी तय करना पड़ता है कि, क्या उसे लेजर प्रक्रिया से बनाना है? उसके अनुरूप डिजाइन में जरूरी सारी विशेषताएं शामिल करनी पड़ती हैं। कुल मिला कर तेज और अचूक उत्पादन पाने हेतु लेजर प्रक्रिया असरदार है, इसमें कोई संदेह नहीं।