कई बार छिद्र तथा बाहरी व्यास के आरेखन के विवरण में, गोलाई ( circularity ) और बेलनाकार (सिलिंड्रिसिटी) पर डिजाइनर मर्यादा ड़ालते हैं। ये दोनों संज्ञाएं अलग अलग ज्यामितीय गुणधर्म दर्शाती हैं। लेकिन इन दोनों पर नियंत्रण हेतु की जाने वाली क्रियाएं समान होने के कारण हम इनके बारे में एकसाथ विचार करेंगे। सबसे पहले हम इन दोनों की परिभाषा और अर्थ समझते हैं।
गोलाई या वृत्ताकारिता
यह दोनों समान अर्थ के शब्द एक ही गुणविशेष दर्शाने के लिए इस्तेमाल (चित्र क्र. 1) किए जाते हैं। दो काल्पनिक संकेंद्रित वृत्त की त्रिज्या में होने वाला फर्क है गोलाई। इसमें उस कार्यवस्तु की परिधि (पेरिमीटर) पर होने वाले सारे बिंदु समाविष्ट होते हैं। इससे यह स्पष्ट होता है कि यह गुणविशेष बेलनाकार या छिद्र के पूरे पृष्ठ से संबंधित नहीं, बल्कि उनके केवल एक हिस्से से संबंधित होता है।
बेलनाकार (सिलिंड्रिसिटी)
एक बेलनाकार के सारे बिंदु जिन दो संकेंद्रित बेलनाकारों में होते हैं, उन दो बेलनाकारों की त्रिज्या में होने वाले फर्क को बेलनाकारिता (चित्र क्र. 2) कहते हैं। इससे यह स्पष्ट होता है कि यह गुणविशेष बेलनाकार के पूरे पृष्ठ से संबंधित है, किसी विशिष्ट हिस्से तक सीमित नहीं।
जरूरत के अनुसार या किसी विशेष कारण के लिए इस्तेमाल किए जाने वाले 'फिट' के मुताबिक, डिजाइनर द्वारा गोलाई या बेलनाकार पर मर्यादा निश्चित की जाती है।
बोरिंग में समस्या
अब हम समझ लेते हैं कि 'बोरिंग' प्रक्रिया में गोलाई और बेलनाकार पर कैसे असर होता है और उस पर नियंत्रण कैसे पाते हैं।
कार्यवस्तु पकड़ने वाले घटकों के असरकार्यवस्तु पकड़ने के बल से कार्यवस्तु का विरूपण (डिस्टॉर्शन) न हो, इस पर नियंत्रण करना महत्वपूर्ण होता है। जब टूल घुमा कर बोरिंग किया जाता है तब कार्यवस्तु के आकार में होने वाला बदलाव, कार्यवस्तु और फिक्श्चर इनके जोड़ पर निर्भर होता है। जब कार्यवस्तु घुमा कर बोरिंग किया जाता है तब कार्यवस्तु के आकार में होने वाला बदलाव, जॉ तथा कार्यवस्तु के बीच के पृष्ठीय संपर्क (इंटरफेस) पर निर्भर होता है। गोल घूमते टूल से यंत्रण करते समय एक आसान परीक्षण किया जा सकता है। कार्यवस्तु फिक्श्चर में बिठाने के बाद जिस भाग पर बोरिंग करना हो वहाँ एक डायल इंडिकेटर रखते हैं। रेस्ट पैड पर सेन्सर सटने जितना ही पकड़ का दबाव रख कर, डायल शून्य पर ला कर, पकड़ का दबाव जरूरत के हिसाब से बढ़ाते हैं। इस दौरान डायल की सुई हिली तो माना जाता है कि कार्यवस्तु का विरूपण हो रहा है। डायल 90° में घुमाने पर, विरूपण की दिशा जानी जा सकती है। यह परीक्षण उसी हिस्से पर करने से उसका गोलाई पर असर जान सकते हैं।
सिलिंड्रिसिटी पर सटीक नियंत्रण पाना हो और यदि छिद्र के आकार के अनुसार दो डायल गेज लगाना संभव हो तो छिद्र की शुरुआत में एक और अंत में एक, ऐसे दो गेज लगाने पर लंबाई की दिशा में होने वाला विरूपण पता चलेगा।
इन परीक्षणों से, ऑपरेटर को विरूपण के स्वरूप का अनुमान होता है और यंत्रण की ट्रायल लेने से पहले जरूरी कार्यवाही कर के वह इस विरूपण पर नियंत्रण पा सकता है। फिक्श्चर मशीन पर बिठाने से पहले यह परीक्षण करने से मशीन का बर्बाद होने वाला समय बच सकता है।
अब जानेंगे कि लेथ मशीन पर (पारंपरिक या सी.एन.सी. मशीन) बोरिंग करते समय क्या होता है। आम तौर पर लेथ पर 3 जॉ चक (चित्र क्र. 3) का इस्तेमाल होता है। जॉ के इस्तेमाल से क्लैंपिंग करते समय, घर्षणात्मक बल से पकड़ने का बल मिलता है जो यंत्रण बल की विपरित दिशा में काम करता है। लेकिन जॉ ने, अपने संचलन की दिशा में लगाए बल से कार्यवस्तु का आकार बिगड़ सकता है। यहाँ स्थिर घर्षण का सरल सूत्र लागू होता है।
घर्षण बल = घर्षण का सहगुणांक (कोइफिशंट ऑफ फ्रिक्शन) x बल
कार्यवस्तु की मोटाई कम हो तो विरूपण टालना अधिक चुनौतिभरा होता है। ऐसे समय घर्षण का बल बढ़ा कर जॉ द्वारा लगाया बल कम रखना पड़ता है। जॉ का बल कम करने का एक विकल्प है, दबाव उतना ही रख कर संपर्क क्षेत्र बढ़ाना। कई बार, विशेष जॉ (चित्र क्र. 4) तैयार करने होते हैं ताकि यह संपर्क क्षेत्र, प्रति जॉ 100° से 110° मिले। ऐसे जॉ का, कार्यवस्तु के अनुरूप, अचूक बोरिंग करना पड़ता है। इससे कार्यवस्तु का विरूपण होने की संभावना कम होती है।
घर्षण का सहगुणांक बढ़ाने के लिए जॉ का पृष्ठ खुरदरा करना पड़ता है। उस पर सरेशन करने पड़ते हैं या उसे खरोचा जाता है। लेकिन सरेशन करें तो उनके चिन्ह, जॉ ने पकड़े पृष्ठ पर दिखते हैं। इसलिए जब पकड़े जाने वाले पृष्ठ का यंत्रण नहीं किया गया हो या इन चिन्हों से फर्क नहीं पड़ता हो तब ही सरेशन किए जॉ का इस्तेमाल किया जाता है। चक के कारण आकार में आने वाला विरूपण इन उपायों से घटाया जा सकता है।
स्पिंडल के 'डाइनैमिक्स' के असर
चूंकि स्पिंडल यह घूमने वाला हिस्सा होता है, कार्यवस्तु की गोलाई पर इसका असर होता है। कर्तन दबाव के कारण अच्छा स्पिंडल कभी भी धक्के या झटके नहीं देता, लेकिन बेरिंग में क्लियरन्स बढ़ने पर स्पिंडल धक्के दे सकता है। यंत्रण करते समय स्पिंडल हिलने पर कार्यवस्तु अपेक्षित गोलाई में न हो कर अंड़ाकार (ओवल) या अन्य आकार की बनेगी। ऐसे आकार के छिद्रों को अधिक अंड़ाकार के (एलिप्टिकल) कहलाते हैं। कई बार सिर्फ स्पिंडल घुमाने पर 'रनआउट' नहीं दर्शाया जाता, लेकिन उस पर भार (लोड) आने पर इस दोष का पता चलता है। इसलिए मशीन उत्पादक ने बताए प्रतिबंधात्मक एवं अनुमानित (प्रेडिक्टिव) तंत्र के इस्तेमाल से स्पिंडल का समय पर रखरखाव करना जरूरी होता है।
कार्यवस्तु या टूल की रचना अथवा वजन के गठन के कारण, उसे स्पिंडल पर लगाने से स्पिंडल का संतुलन बिगड़ता है। खास कर के स्पिंडल की गति (आर.पी.एम.) बढ़ने पर गतिशीलता में असंतुलन बढ़ता है, जिससे स्पिंडल झटके देता है। इससे गोलाई तो बिगड़ती ही है, साथ में टूल की आयु भी कम होती है। इस पर उपाय है, बोरिंग टूल का गतिशील संतुलन (डाइनैमिक बैलन्सिंग) करना या, लेथ के संदर्भ में, कार्यवस्तु चक में बिठाने के बाद संतुलन करना। घूमने वाले पूरे हिस्से का गतिशील संतुलन किया जाने पर गोलाई में सुधार आता है।
]
यंत्रण बल के असर
यंत्रण बल के अक्षीय भाग का असर, विरूपण पर और अंततः गोलाई पर पड़ता है। इस घटक का असर कम से कम हो तथा अचूक छिद्र बनाने हेतु पॉजिटिव रेक वाले टूल इस्तेमाल करें। इससे प्रति कार्यवस्तु टूल की लागत कभी कभी बढ़ती है, लेकिन कार्यवस्तु में न्यूनतम दोष रहने से रिजेक्शन से होने वाला नुकसान घटता है। प्रक्रिया बार बार रीसेट नहीं करनी पड़ती, इससे समय भी बचता है। इन मुद्दों पर विचार कर के उचित निर्णय लेना पड़ता है।
रेडियल यंत्रण के दौरान तैयार होने वाले बल पर, फिनिशिंग करते समय हटाए गए मटीरीयल का तथा टूल की नोज त्रिज्या का भी असर होता है। लेकिन पृष्ठ के खुरदरेपन पर नियंत्रण हेतु इसका अधिक विचार करना पड़ता है।
उष्मीय विरूपण से होने वाले असर
सूखे यंत्रण में पैदा होने वाली उष्मा से कार्यवस्तु का तापमान बढ़ता है। कर्तन के बाद कार्यवस्तु फिक्श्चर से निकाल कर खुले में ठंड़ी होने के लिए रखी जाने पर, छिद्र के पृष्ठ से निकलने वाली उष्मा छिद्र के आसपास के वजन के वितरण के अनुसार होती है। कार्यवस्तु की रचना के अनुसार, उष्मा अलग अलग हिस्सों से भिन्न मात्रा में बाहर फेंकी जाती है। इससे कार्यवस्तु का विरूपण हो सकता है, जिसका असर गोलाई एवं बेलनाकार पर होता है। ऐसे उष्मीय विरूपण से बचने के लिए, संभव हो तब यंत्रण में शीतक का इस्तेमाल करें।
छिद्र की लंबाई से होने वाले असर
छिद्र की लंबाई व्यास की तुलना में अधिक हो (L/D >5), तो गोलाई के बजाय बेलनाकार पर अधिक असर संभव होता है। जब अधिक लंबाई के बोरिंग बार इस्तेमाल किए जाते हैं और कार्यवस्तु की रचना या अन्य समस्याओं के कारण लंबाई/व्यास अनुपात उचित रखना मुमकिन नहीं होता तब लंबगोलाकारिता पर नियंत्रण कम पड़ सकता है। बोरिंग बार पर्याप्त मात्रा में सख्त (स्टिफ) ना हो तो, उस पर कर्तन बल के असर से होने वाले विचलन (चित्र क्र. 5) का अचूक अनुमान लगाना मुश्किल होता है। बोरिंग बार अधिक सख्त बनाने हेतु, उसके डिजाइन एवं उत्पादन में विभिन्न तकनीक इस्तेमाल होते हैं। बोरिंग बार अधिक सख्त बनाने के लिए उत्पादकों के पास कई तरह के उपाय होते हैं। कुल कीमत का विचार करने के बाद उचित उपाय चुना जाता है।
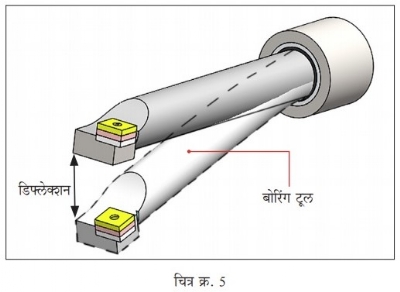
अलग अलग प्रकार के यंत्रण के समय, उपर बताए सारे घटकों का असर, कम या अधिक मात्रा में, गोलाई और बेलनाकार पर होता है। सारे घटकों का उचित मूल्यांकन कर के उन पर नियंत्रण पाने हेतु हर यंत्रण के मामले में उचित उपाय करने पड़ते हैं। कई बार उपरोक्त घटकों का असर होता भी नहीं, लेकिन वृत्ताकार या बेलनाकार कार्यवस्तु का उत्पादन करते समय इन्हें ध्यान में रखना आवश्यक है।