पेचीदा पुर्जों के मामले में पारंपरिक तरीके से आयाम या दूरियां नापना चुनौतिभरा हो सकता है। ऐसे मापनों के लिए लेजर ( laser ) पर आधारित खास मापन तकनीक विकसित की गई है। यह लेख उसी के बारे में है।
उत्पादन क्षेत्र में गुणवत्ता नियंत्रण विभाग पर, अल्प समय में बड़े एवं जटिल उत्पादों की जांच कर के उनकी गुणवत्ता प्रमाणित करने की जिम्मेदारी होती है। निर्माण होने वाली हर वस्तु की अचूकता निश्चित करने हेतु उसे अगर गुणवत्ता आश्वासन परीक्षण से गुजरना हो, तो उत्पादन विभाग की क्षमता गुणवत्ता नियंत्रण विभाग के काम पर निर्भर होती है। इससे गुणवत्ता नियंत्रण विभाग पर काम का बोझ बढ़ता है। अगर एक ही कार्यवस्तु के कई हिस्सों की जांच करनी हो, जैसे कि छोर, वक्रता, ड्रिल किए छिद्र, ग्रूव आदि तब ये काम और भी मुश्किल होता है। इसके लिए प्रशिक्षित तथा कुशल कर्मियों की बड़ी जरूरत होती है। मांग के अनुसार उत्पादन की मात्रा में हमेशा चढ़ाव उतार होने के कारण गुणवत्ता जांचने वाले कर्मियों के कार्यभार पर उसका बुरा असर होता है। फलस्वरूप गुणवत्ता प्रभावित हो सकती है।
उद्योग क्षेत्र में गुणवत्ता नियंत्रण हेतु विभिन्न तकनीक/साधनों का उपयोग किया जाता है। तथापि, हर साधन की क्षमता के अनुसार उसके अचूक मापन के टॉलरन्स और फिट की मर्यादाएं, कुछ दशमलव में होती हैं। इससे भी, पुर्जे असेंब्ली में जाने के बाद अस्वीकृत होने की संभावना बढ़ती है। ऐसे अस्वीकृत पुर्जे उत्पादन विभाग में मरम्मत/पुनर्प्रक्रिया के लिए फिर से भेजे जाते हैं। उत्पादन/यंत्रण होने के बाद के छोटे-बड़े सुधार करने हेतु कोई कुशल कर्मी नियुक्त करना पड़ता है। इससे यंत्रण का समय तथा लागत दोनों बढ़ते हैं। अचूक यंत्रण से समस्या का समाधान हो सकता है, लेकिन इसमें मानवीय त्रुटियों को अनदेखा नहीं किया जा सकता। उत्पादन कार्य में पूर्णतया स्वचालन आपूर्ति हेतु, प्रथम श्रेणी की आश्वस्त गुणवत्ता जरूरी है।
गुणवत्ता नियंत्रण और जांच प्रणाली की आवश्यकता को ले कर अभियंताओं के एक समूह ने हमसे संपर्क किया। उन्हे सैकड़ों वस्तुओं की गुणवत्ता नियंत्रण के लिए एक शीघ्र प्रतिक्रिया देने वाली और माइक्रोमीटर स्तर पर अचूकता होने वाली प्रणाली आवश्यक थी।
उनकी मांग का गहन अध्ययन कर के हमने एक आसान उपाय खोज निकाला। हमनें उन्हें उनके गुणवत्ता नियंत्रण विभाग में लेजर स्कैनिंग की छोटी मशीन इस्तेमाल करने का सुझाव दिया।
लेजर प्रणाली कैसे काम करती है?
इस प्रणाली का मूलाधार है लेजर विस्थापन पद्धति पर आधारित लेजर मापन तकनीक। जिस स्थान पर पारंपरिक पद्धति से दूरी या आयाम (डाइमेन्शन) का मापन करना बेहद मुश्किल होता है, ऐसे पेचीदा पृष्ठों के लिए लेजर पर आधारित यह मापन तकनीक विशेष रूप से विकसित की गई है। इस प्रणाली के दूसरे चरण पर, संबंधि भाग की मोटाई जांचने के काम में भी जरूरी सुधार किए गए हैं।
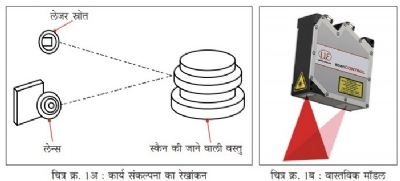
यह लेजर पर आधारित एक बेहद आसान स्कैनिंग मशीन है। इसमें वॉल्युम इल्युमिनेशन और फोटो डायोड रिसीवर के साथ हाइ रिजोल्युशन कैमरे भी (चित्र क्र. 1अ और 2अ) हैं। किसी भी प्रातिनिधिक प्रणाली में आगे दिए घटक होते हैं - ऑप्टिकल लेजर स्कैनर, एक डिटेक्शन यूनिट, एक डेटा प्रोसेसिंग यूनिट। रिसीवर के पहले (चित्र क्र. 2 ब) फिल्टर और लेन्स बिठाए जाते हैं। ये लेन्स, वाइड अैंगल अैडजस्टमेंट कर के वस्तु पर किरण केंद्रित (फोकस) करने हेतु दी जाती हैं। प्रकाश की जिन तरंग लंबाई (वेवलेंग्थ) से रूकावट हो सकती है, उन्हें फिल्टर द्वारा रोका जा सकता है। लेजर की वेवलेंग्थ के अनुसार फिल्टर का चयन किया जाता है। दूरी मापन के लिए (चित्र क्र. 1अ) जरूरत के हिसाब से सामान्य लेजर बिंदु या लेजर रेखा पर्याप्त होती है। लेजर स्कैनिंग प्रणाली में, जिस पृष्ठ की जांच/ निगरानी करनी हो, उसे लेजर किरण (बीम) द्वारा हर बिंदु पर से स्कैन किया जाता है। इससे पृष्ठ पर एक तेजस्वी बिंदु निर्माण होता है। जब फोकस की गई लेजर किरण किसी पृष्ठ पर गिरती है तब उत्सर्जित किरणों का फैलाव पृष्ठ के रूप तथा रचना पर निर्भर होता है। जब किसी भी वस्तु के पूरे पृष्ठ की जांच करनी हो तब बिना कोई जगह छोड़े, साफ प्रतिमा पाने हेतु लेन्स की रचना (फोकस) कर के लेजर किरण से पृष्ठ पर का हर बिंदु जांचना जरूरी होता है। प्रकाश अधिग्रहित करने वाले (लाइट रिसीविंग) यूनिट द्वारा इमेजिंग लेन्स में से, उपरोक्त तेजस्वी बिंदु के अवकाशीय स्थान, पी.सी.डी. या सी.सी.डी. जैसे प्रकाशबिंदु स्थान शोधक (पोजिशन डिटेक्टर) द्वारा दर्ज किए जाते हैं। मापन प्रणाली में होने वाला सिग्नल प्रोसेसिंग यूनिट, किसी प्रोब के समान काम कर के वस्तु विस्थापन में हुए बदलाव का गणन करता है। साथ ही इससे, मापन के समय पृष्ठ पर घूमने वाले तेजस्वी बिंदु का बदलता स्थान हर बार दर्ज किया जाता है।
प्रणाली, वस्तु के आदर्श नमूने (मास्टर) को त्रिमिति में स्कैन करती है और संदर्भ हेतु उस नमूने का एक नक्शा तैयार करती है। स्कैनिंग प्रक्रिया शुरू करने से पहले एक आरंभ बिंदु तय किया जाता है। इस आदर्श नमूने के पृष्ठ के लेजर प्रतिबिंब, हर स्कैनिंग के समय प्रणाली के मेमरी में संग्रहित किए जाते हैं। पृष्ठ का चयन क्रमवार किया जा सकता है और उसके अनुसार मशीन के नीचे उसका स्कैनिंग कर सकते हैं। पूरे नमूने की स्कैनिंग प्रक्रिया पूरी होने के बाद ठोस प्रतिकृति (सॉलिड मॉडेलिंग) निर्मिति साफ्टवेयर से उसकी पुनर्रचना की जाती है। यह साफ्टवेयर हमारे लिए एक प्रीव्यू तैयार कर सकता है। इस चरण पर गुणवत्ता आश्वासन विभाग का समूह अपना योगदान दे कर आयामों में और भी सुधार कर सकता है। जिस क्षेत्र का विश्लेषण करना है, वह चाहे जितना विस्तृत हो सकता है और स्थानसंबंधि सूक्ष्मता माइक्रोमीटर से भी कम हो सकती है। लेजर के बिंदु का पृष्ठीय स्थान किसी भी चरण पर बेहद अचूकता से निश्चित किया जा सकता है, इसलिए यह मुमकिन होता है।
इस्तेमाल के मार्ग
विश्वसनीयता की उन्नत मांगें पूरी करने के लिए जानी पहचानी पुरानी गणितीय पद्धतियों और तकनीक (इंटरफेरोमैट्रिक, स्कैटरिंग, ट्रैंग्युलेशन, फ्रिंज प्रोजेक्शन आदि) का अध्ययन फिर से कर के उन्हें विकसित किया जा रहा है। विशेष रूप से त्रिकोणिकरण (ट्रैंग्युलेशन) पर आधारित पद्धतियों का उपयोग, व्याप्ति या पहुंच का संवेदन (रेंज सेन्सिंग), 3D आकार परीक्षण, स्थलाकृतिक (टोपोग्राफिक) मूल्यांकन और उबड़खाबड़ पृष्ठ के सूक्ष्म परीक्षण के लिए बड़े तौर पर किया जाता है। स्कैनिंग प्रक्रिया के दौरान जांचे जाने वाले पृष्ठ की तुलना, सेन्सर अपनी मेमरी में संग्रहित काल्पनिक संदर्भ प्रतल से नियमित करता है। इसके बाद इन दो पृष्ठों के सापेक्ष विस्थापन की दूरी गिन कर उसे दर्ज करता है। यह नक्शा उसकी मेमरी में संग्रहित किया जाता है, जिसका उपयोग उत्पादन विभाग में कार्यरत मशीन पर जरूरत के अनुसार किया जा सकता है। स्कैनिंग करते समय वस्तु तीनों अक्ष में, 360° में घुमाई जा सकती है। अगर गोल घुमाना संभव नहीं हो तो स्वचालन का कार्यभार घटाने हेतु स्कैनिंग यूनिट (चित्र क्र. 3अ और 3ब) की एक मालिका (अैरे) का नियोजन किया जा सकता है।
उपयोगकर्ता की आवश्यकतानुसार एक ही वस्तु की जांच कई बार कर सकते हैं। जैसा कि चित्र क्र. 3अ और 3ब में दर्शाया है, स्कैनिंग प्रणाली की मालिका का नियोजन किया जा सकता है। स्कैनिंग यूनिट की संख्या पर आधारित, वस्तु के भाग या खंड़ (सेक्शन) अलग किए जाते हैं। जब तक उससे कोई रुकावट नहीं आती तब तक, विभाग थोड़ी मात्रा में एक दूसरे पर अधिव्यापित (ओवरलैप) होने से भी कोई समस्या नहीं होती। लेकिन उससे कोई रुकावट आती है तब, विभिन्न तरंगलंबाई वाले लेजर (चित्र क्र. 4अ, 4ब) का इस्तेमाल कर सकते हैं। 2 या 3 स्कैनिंग यूनिट कार्यरत होने पर ये काम करना आसान होता है। लेकिन 3 से अधिक स्कैनिंग यूनिट का उपयोग किया जाता हो तो भिन्न क्षेत्र चिन्हित कर के, जरूरत के अनुसार स्कैनिंग मशीन का इंतजाम किया जा सकता है, क्योंकि उपलब्ध लेजर वेवलेंग्थ की संख्या मर्यादित होती है।
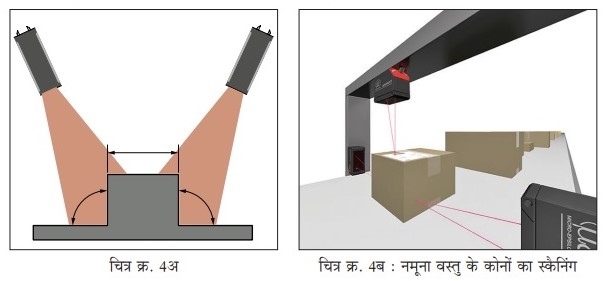
उपयोगकर्ता को ऑनलाइन पद्धति में परिणाम प्रस्तुत किए जाते हैं और सामान्य उत्पादन से मेल न रखने वाले उत्पाद तुरंत अलग (चित्र क्र. 5) किए जाते हैं। जिस गति से उत्पादन हो रहा हो उसी गति से यह प्रणाली काम कर सकती है। हर वस्तु स्कैन करने के लिए कम से कम 3 सेकंड का समय लग सकता है लेकिन यह, उस वस्तु की जटिलता एवं आकार पर निर्भर होता है। आसान उत्पादों के लिए यह समय कम हो सकता है। इसके साथ जुड़े साफ्टवेयर पैनल के अनुसार उत्पाद का अंतिम विवरण होता है। साफ्टवेयर रंगीन नक्शे के रूप में आउटपुट देता है। इससे दोषपूर्ण भाग पहचाने जा सकते हैं और उनमें आसानी से सुधार किए जा सकते हैं।
मिसाल
हम स्पॉक्रेट वील के दांत की जांच की एक पेचीदा मिसाल देखते हैं। चित्र क्र. 6अ में दर्शाएनुसार लेजर स्कैनिंग मशीन पर स्पॉक्रेट टूथ का स्कैनिंग करने के बाद, चित्र क्र. 6ब और 6क के अनुसार नक्शा तैयार होगा। दो दांतो के बीच का कोण, दो दांतों के बीच के खांचे की दूरी, दांत की गहराई, वक्रता या प्रोफाइल, पिच और सबसे महत्वपूर्ण बात वील के पृष्ठ का फिनिश ये पैरामीटर जांचे जाएंगे। इसके अलावा वस्तु पर कटाव के निशान, दांतो का बिगड़ा आकार या समतलता, दांतो की वील पर अलाइन्मेंट भी यह प्रणाली जांच सकती है।
लेजर का विविध कामों में इस्तेमाल
इस तकनीक के इस्तेमाल से वस्तु की गुणवत्ता जांचने और प्रमाणित करने के लिए एक व्यक्ति काफी है। कास्टिंग उद्योग क्षेत्र में यंत्रणपूर्व आयामों की मर्यादाएं सटीक नहीं होती। इसलिए परिणामों की जांच तेज गति से की जा सकती है। अनुचित कास्टिंग से उत्पन्न होने वाले दोष या वात छिद्र (ब्लो होल), माइक्रोमीटर के स्तर पर खोजना मुमकिन है। इसलिए जरूरत पड़ने पर इसका इस्तेमाल पृष्ठ परीक्षक साधन के रूप में किया जा सकता है। इसके विपरित, प्लास्टिक मोल्डिंग उद्योग क्षेत्र में जब डाइ द्वारा दबाव से निर्मित वस्तु का अंदरूनी भाग दांतेदार होता है या मोल्ड की गई वस्तु टॉलरन्स के बाहर होती है, तब ऐसे दोष खोजना बेहद आसान होता है। इन दोषों को अपनी आंखों से नहीं देखा जा सकता, वें दृश्यता पर आधारित जांच से छूट जाते हैं। रबड़ उद्योग क्षेत्र में रिंग या बुशिंग जैसी, बाद में कठोर की जाने वाली वस्तुओं में सरल फिट पाने के लिए उच्चस्तरीय अचूकता जरूरी होती है। इस प्रणाली से जांच में लगने वाले समय में काफी बचत हो सकती है।
समतल पृष्ठ के स्कैनिंग हेतु यह प्रणाली कोई भी गड्ढ़ा, कटाव, पुंज, कोने, समतलता और वस्तु के आयाम जांच सकती है।
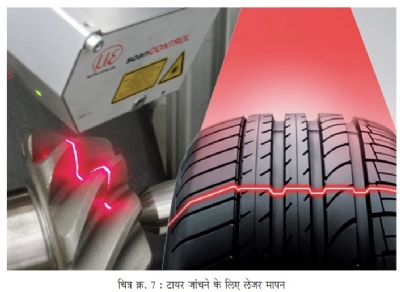
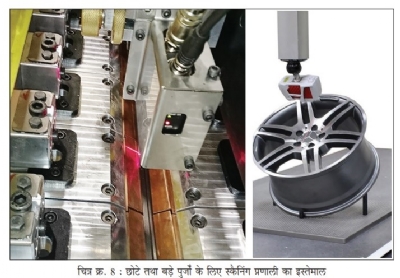
अचूकता के स्तर के साथ इस प्रणाली का एक और लाभ यह है कि यह प्रणाली छोटे से बड़े तक किसी भी वस्तु के लिए प्रभावी रूप से उपयोगी है। यह प्रणाली ऑटोमेटिव उद्योगक्षेत्र में छोटे स्क्रू से ले कर चैसी जैसे विशाल भागों तक, सादे बार से पेचीदा दरवाजे के डिजाइन तक, सब कुछ स्कैन कर के जांच (चित्र क्र. 7 और 8) का काम कर सकती है। इसके लिए इसे विभिन्न उत्पादन कक्षों में आसानी से ले जाना संभव है। इस प्रणाली के केवल एक यूनिट के इस्तेमाल से एक प्लांट के सारे उत्पाद आसानी से जांचे जा सकते हैं। हर स्थान पर इस यूनिट को सिर्फ प्लग-इन कर के काम शुरू किया जा सकता है। यह प्रणाली पूरी तरह से सुरक्षित है क्योंकि इस प्रणाली में दूसरे श्रेणी के लेजर का उपयोग किया है। चूंकि इसमें कोई भी यांत्रिक भाग नहीं हैं, इसमें किसी भी प्रकार के सेफ्टी स्विच नहीं हैं। साथ ही, मशीनसंबंधि देरी के कारण प्रणाली धीरे से शुरू होना आदि घटनाएं नहीं होती। हाइ रेजोल्युशन, गतिमान स्कैनिंग, लेजर स्कैनिंग और उच्च कॉन्ट्रास्ट वाली प्रतिमाओं की उपलब्धता ये लेजर स्कैनिंग प्रणाली के महत्वपूर्ण लाभ हैं।
प्रणाली इस्तेमाल करते समय बरती जाने वाली सावधानियां
यह प्रणाली, उत्पादन विभाग द्वारा निर्मित सारे उत्पाद अस्वीकार कर के बड़ा झटका दे सकती है। मानवीय गलती के कारण दोषपूर्ण वस्तु आदर्श नमूने (मास्टर) के तौर पर चुनी गई हो तो इस प्रकार की गड़बड़ हो सकती है। इससे बचने के लिए उपयोगकर्ता ने बड़ी सावधानी के साथ आदर्श नमूना विकसित करना चाहिए। बेहद अचूक मास्टर बनाने के लिए अधिक प्रयास करने से, गुणवत्ता नियंत्रण यूनिट में श्रम और समय की बचत हो सकती है। यह प्रणाली किसी भी परिवेश में काम कर सकती है। आसपास के प्रकाश के कारण अंतिम परिणामों में कोई भी अतिरिक्त दोष नहीं होता। इसी लिए यह प्रणाली धूप में या अंधेरे में उतनी ही अचूकता से काम करती है। तापमान में होने वाले बदलावों का, मापन पर कोई असर नहीं होता। लेकिन जो वस्तु जांचनी है उसके तापमान का असर होता है, क्योंकि वस्तु के तापमान के अनुसार उसके आयाम बदलते हैं। मोटाई और आकारमान के अलावा यह प्रणाली आकार, समतलता, लंबाई, आड़ा-टेढ़ापन, वेवीनेस, को-प्लेनैरिटी के मामले में बेहतर काम करती है। इसके देखभाल की लागत बहुत कम होती है।
तापमान में बदलाव, प्रतिमासंबंधि प्रक्रिया में त्रुटि और गणितीय प्रतिमान की मर्यादा से मापन में होने वाली गलतियां आदि मर्यादाएं पहले थी। नई तकनीक के कारण अब ये लगभग सारी ही लुप्त हो चुकी हैं। अब अधिकांश गलतियां, पृष्ठ पर जमे कूड़े या अन्य बाहरी वस्तुओं (फॉरेन बॉडीज्) से हो सकती हैं।
इस प्रणाली की कीमत, उससे अपेक्षित काम और अचूकता पर आधारित होती है। उच्च रिजोल्युशन वाली कोई सरल 1D स्कैनिंग प्रणाली, कम रिजोल्युशन की 3D प्रणाली से महंगी हो सकती है।
सुधारित गुणवत्ता परीक्षण दर से, उत्पादन विभाग पर होने वाला तनाव कम हो सकता है। गुणवत्ता नियंत्रण प्रक्रिया के तनाव की जो वृथा प्रशंसा करते हैं उनके चेहरे पर हम खुशी देख सकते हैं।