धातुकार्य के पिछले एक अंक में हमने एक छोटे वर्कशॉप में वी.एम.सी. का उचित इस्तेमाल करने के बारे में जानकारी प्राप्त की थी। आज हम देखेंगे कि विभिन्न प्रकार के अनेक वी.एम.सी. होने वाले एक नामचीन कारखाने में उनका इस्तेमाल कैसे किया जाता है।
इस कारखाने में एक पुर्जा (चित्र क्र. 1) बनाया जा रहा था। पुर्जे के आकार के कारण Ø150 मिमी. + Ø186 मिमी. का छेद, चैंफर के साथ प्लंज टूल की सहायता से करना संभव नहीं हो रहा था क्योंकि वी.एम.सी. का पिकअप आर्म इतने बड़े कटर को उठा नहीं पा रहा था। बाहर से हाथ से कटर लगा कर काम करने की कोशिश की, लेकिन उसमें बहुत समय जा रहा था, इसलिए उत्पादकता कम थी। एकदम हल्के, कम वजन के कटर से भी यह काम नहीं हो रहा था। इसी लिए इस Ø150 मिमी. + Ø186 मिमी. चैंफर ऑपरेशन के साथ, फिक्श्चर पर कार्यवस्तु को पकड़ कर लेथ मशीन पर किया जा रहा था और अन्य छेद वी.एम.सी. पर बनाए जा रहे थे। उसी प्रकार, Ø110.6 मिमी. पर का टैपिंग भी उसी समय वी.एम.सी. पर किया जा रहा था। पिछली ओर का फेस (चित्र क्र. 2) अलग सेटिंग में हो रहा था और सेटिंग बढ़ने के कारण उत्पादन की मनचाही मात्रा नहीं मिल रही थी।
उत्पादन बढ़ाने के लिए हमने बहुत से काम एकत्र किए और एक ही सेटिंग में पूरी कार्यवस्तु बाहर कैसे निकलेगी, इस मुद्दे पर विचार किया। ऐसा विचार करने पर इसकी सीमाएं हमारे ध्यान में आई और हमने टर्निंग बंद करने का फैसला किया।
तब हमने इंटरपोलेशन करने का प्रस्ताव रखा। शुरुआत में यह काम सॉलिड कार्बाइड एंड मिल द्वारा किया गया। काट की लंबाई और चौड़ाई काफी होने के कारण एंड मिल की आयु कम हो रही थी और इसके अलावा खंडि़त काट के कारण टूल भी टूट रहा था।
इसलिए हमने इन्सर्ट वाली एंड मिल इस्तेमाल करने का फैसला किया। इसकी सफलता के बाद हमने एक ऐसा मिश्र कटर विकसित किया जिसके द्वारा Ø150 मिमी. और Ø186 मिमी. व्यास और चैंफर एक ही काट में किए जा सकते थे। चित्र क्र. 3 और 4 देखें। इंटरपोलेशन द्वारा यह काम करना तय किया।
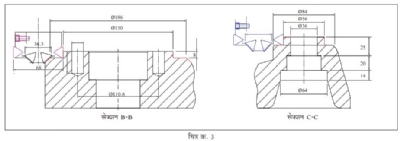
चैंफर पर आकार का नियंत्रण महत्वपूर्ण होता है और इसी लिए हमने कटर में इन्सर्ट के लिए अैक्सियल अैडजस्टमेंट रखी। इस कटर को सब तरफ से घुमाना संभव होने के लिए उसका बाहरी व्यास 68 मिमी. तक सीमित किया गया और उसी के साथ इन्सर्ट भी इस तरीके से बिठाया गया कि उसी समय चैंफर बन सके। यह भी देखा गया कि Ø150 मिमी. होते वक्त ही बाहरी चैंफर भी बन जाए। जब यह ठीक से होने लगा तब अगले चरण में एक तरफ के Ø56 मिमी. के तीनों छिद्र इसी कटर से बनाना शुरू किया। एक ही कटर की सहायता से इंटरपोलेशन ने सारा काम किया। यहॉँ Ø56 मिमी. की सीमा थी इसलिए वहां इंटरपोलेशन द्वारा रफिंग किया और बाद में एक बोरिंग बार से फिनिशिंग किया। इस तरह, काम पूरा होने की स्थिति में आने पर उसी सेटअप में उल्टी दिशा का फेस मिलिंग करने का प्रबंध किया। उसके लिए आकार में बड़ा लेकिन वजन में हल्का कटर बनाया गया। उसने अपने आकार के कारण ATC के तरफ दो टूल की जगह लेने पर भी सभी टूल ATC की बाकी जगहों पर लगा कर, पूरी कार्यवस्तु एक ही सेटअप में बनाई गई। तालिका क्र. 1 देखें।
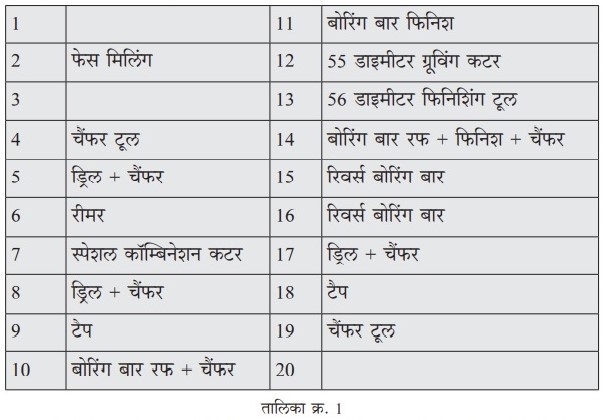
कार्यवस्तु के दो नग टेबल पर पास-पास सेट कर के दोनों पर एक ही सेटअप में पूरा काम किया जाने लगा। इसी काम के लिए पहले एक लेथ और दो वी.एम.सी. के सेटअप की जरूरत पड़ती थी।
यह कार्यपद्धति प्रस्थापित हो जाने पर, उसी तरह के कामों में बढ़ोतरी हुई। तीन तरह की कार्यवस्तु में हमने ड्रिलिंग टैपिंग जैसे बहुत समय लेने वाले काम, ड्रिल टैप सेंटर पर करना आरंभ किया। सभी तीन तरह के कामों से संबंधित अन्य काम वी.एम.सी. पर ही चलने दिए।
विभिन्न मशीनों का इस्तेमाल ना करने का और ऑपरेशन का संयोजन कर के वस्तुओं का इस्तेमाल घटाने का यह एक उत्तम उदाहरण है। अंत में, उपलब्ध मशीन यानि ड्रिल टैप सेंटर का इस्तेमाल कर के उत्पादन प्रक्रिया को संतुलित किया गया, यह एक अतिरिक्त लाभ माना जा सकता है।
इसी काम में पहले इस्तेमाल होने वाले सी.एन.एन. लेथ को इस काम से मुक्त करना एक बड़ी सफलता थी और एक ही सेटअप में काम पूरा करने से उत्पादन में अधिक आसानी भी पाई गई।
दत्ता घोलबा पिछले 44 सालों से कटिंग टूल्स से संबंधित काम कर रहे हैं।
आप विविध कंपनियों को टूलिंग विषयक समस्याओं पर मार्गदर्शन करते हैं।
9822881939