लघु, मध्यम उद्योगों में बड़ी संख्या में होने वाली मशीनों में प्रयोग किए जाने वाले उपयोगी एच.एस.एस. टूल का विस्तृत विवरण।
यंत्रण करने वाले किसी भी कारखाने का अविभाज्य भाग वहाँ इस्तेमाल किए जाने वाले टूल होते हैं। यह टूल महत्वपूर्ण होते हैं क्योंकि उनका सीधा असर कारखाने से बाहर भेजे जाने वाले उत्पादन की गुणवत्ता, लागत और उत्पादकता पर होता है। आजकल कटिंग टूल बनाने वाली कई कंपनियाँ बाजार में हैं। इनमें से कुछ गिनीचुनी तगड़ी हैं। अन्य कई कंपनियाँ स्थानीय हैं और खुद को टिका कर रखने की कोशिश में हैं।
इस लेख के द्वारा हम मशीन उद्योग में कई सालों से इस्तेमाल किए जाने वाले हाई स्पीड स्टील (एच.एस.एस.) टूलों की जानकारी लेने वाले हैं।
20 वीं सदी के प्रारंभ में हाई कार्बन स्टील मौजूद थे। पहले इसी स्टील से बने कटिंग टूल इस्तेमाल होते थे (जैसे कि, नॉन फेरस मेटल में काम करने वाले टैप)। उनकी कठोरता (हार्डनेस) ज्यादा थी, साथ ही उनकी भंगुरता (ब्रिटलनेस) भी ज्यादा थी। किसी मटीरीयल की कठोरता बढ़ने पर उसकी भंगुरता भी बढ़ सकती है। टूल बनाते समय मटीरीयल की कठोरता उसकी प्रधान भौतिक गुणवत्ता होती है। इसी वजह से हाई कार्बन स्टील के लिए हाई स्पीड स्टील का विकल्प खोजा गया। हाई कार्बन स्टील की तुलना में हाई स्पीड स्टील की भंगुरता कम होती है। इसके कारण अनिश्चित आकार के पुर्जे का यंत्रण करते समय एच.एस.एस. टूल के असमयिक टुकड़े नहीं होते हैं। धातु को काटते समय उष्मा निर्माण होने के कारण टूल का तापमान बढ़ता है। हाई कार्बन स्टील 180ॅ तापमान पर नर्म होने लगता है। इसके विपरित एच.एस.एस. मटीरीयल की कठोरता 5000 तापमान पर भी बनी रहती है। इसी वजह से एच.एस.एस. टूल के इस्तेमाल से काम अधिक तेजी से होता है। आजकल धातु काटने के लिए हाई कार्बन स्टील का इस्तेमाल कभीकभार ही किया जाता है।
आज भी भारतीय लघु और मध्यम कंपनियों में उच्च गति की नवीनतम मशीनों की संख्या कम है। इन मशीनों पर कार्बाइड टूल की आयु अच्छी होती है। लेकिन हमारे देश में पारंपरिक रीति से काम करने वाली कई छोटी-बड़ी कंपनियाँ मौजूद हैं। अधिकतर कंपनियाँ लेथ मशीन, ड्रिलिंग मशीन, युनिवर्सल मिलिंग मशीन जैसी पारंपरिक मशीन का इस्तेमाल करती हैं। एच.एस.एस. टूल का इस्तेमाल ऐसी ही मशीन पर ज्यादा होता है।
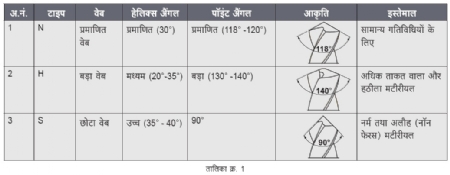
पुराने तंत्रज्ञान की लेथ मशीन, ड्रिलिंग मशीन, युनिवर्सल मिलिंग मशीन आज भी हमारे देश में इस्तेमाल होती हैं। इन मशीनों में बिजली का उपयोग कम होता है। लेकिन कुछ समय के बाद इन मशीनों में स्पिंडल प्ले या टेबल प्ले जैसे दोष निर्माण होते हैं। विदेश में मशीन की आयु उसके कार्यकाल या उत्पादन की तारीख के अनुसार निश्चित करते हैं। उसके बाद इन मशीनों को हटा कर बदल दिया जाता है। हमारे यहाँ ऐसा नहीं किया जाता। अगर कार्बाइड टूल का इस्तेमाल करना हो तो इस प्रकार का आचरण नहीं होना चाहिए। कार्बाइड की वजह से कटिंग टूल की आयु लंबी होने के बावजूद, पुरानी मशीन की इन खराबियों के सामने, कार्बाइड टूल बिलकुल टिकता नहीं है। टूल को धक्का लगने से उनके टूटने की संभावना अधिक होती है।
एच.एस.एस. टूल की ज्यामिति
टूल बनाते समय उसकी आयु बढ़ाने के लिए अलग अलग ज्यामितीय तरकीबें अपनाई जाती हैं। जैसे कि कास्टिंग के लिए ड्रिल का बिंदु कोण (पॉइंट ऐंगल) बदलना। उस समय ड्रिल को डबल ऐंगल पॉइंट ज्यामिति अर्थात 1180 से 900 पॉइंट ऐंगल रखते हैं। स्टेनलेस स्टील हो तो 1350 पॉइंट ऐंगल रखते हैं।
टूल का डिजाइन बनाते समय वे प्राय: N टाइप, S टाइप और H टाइप इन तीन प्रकार की ज्यामिति में बनाए जाते हैं। तालिका क्र. 1 देखें।
• N टाइप का मतलब है सामान्य (नार्मल)। यंत्रण क्षमता अच्छी होने वाले मटीरीयल के लिए इस टूल का इस्तेमाल होता है।
• H टाइप ज्यामिती के टूल, यंत्रण क्षमता कम होने वाले मटीरीयल के लिए इस्तेमाल करते हैं। इस प्रकार के मटीरीयल काटना मुश्किल होता है। इस टूल से इच्छित कार्य पाने के लिए क प्रकार की ज्यामिति में हेलिक्स ऐंगल कम रखा जाता है। रेक ऐंगल भी कम रखा जाता है। इससे उसके कटिंग एज को ताकत मिलती है और टूल की आयु बढ़ती है।
• S टाइप ज्यामिति का इस्तेमाल नर्म (साफ्ट) मटीरीयल के लिए किया जाता है। पिघलन तापमान (मेल्टिंग पाइंट) कम होने के कारण, टूल इस्तेमाल करते समय पैदा होने वाली उष्मा से, कटिंग एज पर कोल्ड वेल्डिंग (या उभरी किनार यानि बिल्टअप एज) होता है। इसे टालने के लिए मटीरीयल पर काम करते समय हाइ रेक ऐंगल रखना भी ठीक रहता है। उसका हेलिक्स ऐंगल ज्यादा रखा जाता है।
निरंतर इस्तेमाल करते रहने से एच.एस.एस. टूल की हानि होती है। उचित ज्यामिति का इस्तेमाल किया गया तो यह टूल सुचारू रूप से काम करते हैं।
एच.एस.एस. टूल पर की जाने वाली परत (कोटिंग) और उनकी श्रेणी
‘बिर्ला प्रिसिजन टेक्नो लिमिटेड (इंडियन टूल्स)’ इस कंपनी ने, एच.एस.एस. टूल के ग्राहकों के लिए महत्वपूर्ण
होने वाला, प्रति पुर्जा खर्चा घटाने की कोशिश की है। कार्बाइड के कटिंग टूल का प्रति पुर्जा खर्चा बहुत कम है क्योंकि उसकी आयु ज्यादा होती है। इस पर मात करने के लिए एच.एस.एस. कटिंग टूल पर विभिन्न प्रकार की परतें लगाई जाती हैं। TiN कोटिंग, TiCN कोटिंग, हार्ड क्रोम प्लेटिंग आदि प्रकार की परत की जाती हैं। कुछ ऐप्लिकेशन पर काम करते समय नाइट्राइडिंग, ब्ल्यू टेपरिंग जैसी प्रक्रिया कर के टूल की आयु बढ़ाई जाती है। उदाहरण के तौर पर मानिए कि किसी मटीरीयल पर ड्रिल से 100 छिद्र बनाने हैं। अगर उस पर आवश्यक परत दे कर इस्तेमाल करे तो उसकी आयु 35% से 50% से बढ़ेगी। टूल उत्पादक प्रत्येक मटीरीयल के लिए उसकी भौतिक गुणवत्ता के अनुसार अलग अलग परत का सुझाव देता है। किस परत का प्रयोग करना चाहिए यह बात टूल के इस्तेमाल पर निर्भर करती है। जैसे कि ऐल्युमिनिअम और हीट रेजिस्टेंट अलॉइ के लिए विभिन्न परत होती है।
एच.एस.एस. टूल की M2, M35, M42 यह तीन प्रकार की श्रेणियां बाजार में उपलब्ध हैं। M2 में कोबाल्ट नहीं होता है। M35 में 5% कोबाल्ट तथा M42 में 8% कोबाल्ट मिलाया होता है। कोबाल्ट का प्रधान गुण है रेड हॉट हार्डनेस बढ़ाना (काटने के दौरान कभी कभी टूल गर्म हो कर लाल हो जाता है लेकिन टूटता नहीं है)। काम की जरूरत के मुताबिक योग्य टूल चुनने के लिए यह वर्गीकरण किया गया है। किसी स्थान में M2 ठीक तरह से काम नहीं करते हैं। उसकी धार घिस (ब्लंट) जाती है। उदाहरण के तौर पर उष्मारोधी मिश्रधातु (हीट रेजिस्टंट अलॉइ) तथा कुछ खास किस्म के स्टेनलेस स्टील आदि पर M2 के बदले M35 का इस्तेमाल किया गया, तो टूल की लंबी आयु मिलती है। M35 पर TiN या TiCN की परत की गई हो तो कटिंग टूल को 30% से 35% तक अधिक आयु मिलती है। जैसे जैसे कोबाल्ट बढ़ता है वैसे ही कठोरता बढ़ती है। उसमें स्थित भंगुरता के बारे में सोच कर उसकी कठोरता की एक निश्चित व्याप्ति (रेंज) चुनी जाती है। M2 की कठोरता 63-64 HRC तक और M35 की कठोरता 64-65 HRC जितनी होती है। M42 की कठोरता 65-66 HRC तक होती है।
एच.एस.एस. टूल की हीट ट्रीटमेंट में, कठोरता के साथ साथ, उनकी मजबूती (टफनेस) बढ़ाने की कोशिश की जाती है। आघात सहने की उसकी ताकत कार्बाइड से ज्यादा अच्छी होती है। कार्बाइड की कठोरता 80 से 85 HRC अर्थात उच्च क्षमता की होती है। एच.एस.एस. टूल की कठोरता 63 से 66 HRC तक होने के कारण उसकी भंगुरता कार्बाइड से कम होती है। साथ ही उसकी मजबूती कार्बाइड से ज्यादा होने के कारण एच.एस.एस. के कटिंग टूल जल्दी नहीं टूटते हैं।
एच.एस.एस. और कार्बाइड के टूल के बीच के फर्क
1. कार्बाइड के टूल एच.एस.एस. से ज्यादा महंगे होते हैं। अत: जब वे टूटते हैं, तब बहुत बड़ा आर्थिक नुकसान होता है। बिर्ला प्रिसिजन टेक्नो लिमिटेड (इंडियन टूल्स) कंपनी ने एक एच.एस.एस. ड्रिल बनाया था जिसका व्यास 90 मिमी. और लंबाई 2000 मिमी. थी। इस ड्रिल का इस्तेमाल इकएङ कंपनी की अर्थमूविंग इक्विपमेंट में होने वाला था। यह ड्रिल अखंडित एच.एस.एस. में या EN का शैंक लगा कर बाईमेटालिक भी कर सकते हैं। लेकिन ग्राहक की जरूरत के अनुसार उसकी रचना निश्चित की जाती है। इसका अगला हिस्सा ब्रेज्ड कार्बाइड में बनाना संभव होता है। लेकिन जिस काम के लिए इस ड्रिल को बनाया गया था, उसके लिए इसका इस्तेमाल उचित हो नहीं सकता था। साथ ही इतने बड़े आकार का कार्बाइड टूल बनाना हो तो उसकी कीमत लाखों रुपयों में होती है। फिर भी उसे बनाया गया तो वह मशीन पर इस्तेमाल नहीं हो सकता है। क्योंकि वह थोड़ा सा भी आघात सह नहीं सकता है, वह तुरंत टूटता है। इसके कारण खर्चा बढ़ जाता है। आजकल इसके बदले मीडिअम कार्बन स्टील का ढ़ाँचा बना कर उस पर कार्बाइड इन्सर्ट बिठा सकते हैं लेकिन वे टिप भी जल्दी टूट जाते हैं।
2. कुछ निश्चित कामों के लिए कार्बाइड की आयु ज्यादा होती है। उदाहरण के लिए, टर्निंग, बोरिंग, फेस मिलिंग इन कामों में कार्बाइड की बढ़िया जीवनी दिखाई देती है। इन क्षेत्रों में कार्बाइड ने एच.एस.एस. को बहुत खूब चुनौती दी है। लेकिन बड़े आकार के ड्रिल, टैप, मिलिंग कटर उदाहरण के लिए, स्लैब मिलिंग कटर, हॉबिंग कटर, जैसे कार्य के लिए कोई अन्य विकल्प नहीं मिला है। उस समय एच.एस.एस. पर ही निर्भर रहना पड़ता है।
3. एच.एस.एस. के ड्रिल, रीमर, मल्टिपल पॉइंट फॉर्म टूल, ब्रोच, गिअर हॉब, गिअर शेपिंग टूल, स्लैब मिलिंग कटर, सर्क्युलर स्लिटिंग सॉ आदि टूल कार्बाइड की तुलना में अधिक सस्ते हैं। साथ में, इन कामों के लिए वे उचित साबित होने के कारण, अच्छे कार्यप्रदर्शन के विचार से उनके दाम कार्बाइड से अधिक सही हैं।
4. एच.एस.एस. टूल को धार लगाना, कार्बाइड टूल को धार लगाने की अपेक्षा, अधिक सस्ता है। एच.एस.एस. टूल को धार लगाने के लिए सिर्फ ऐल्युमिनिअम ऑक्साइड के ग्राइंडिंग वील की जरूरत होती है जो साधारण टूल ऐंड कटर ग्राइंडर पर लगाया होता है। किसी एच.एस.एस. ड्रिल को साधारण पेडस्टल ग्राइंडर पर धार लगाने से भी काम चल सकता है। कार्बाइड टूल की ज्यामिति धार लगाते समय पूर्ण नहीं हुई हो तो वह मशीन पर टूट सकता है। अत: कार्बाइड टूल को धार लगाने के लिए सी.एन.सी. टूल ऐंड कटर जैसे आधुनिक मशीन और डाईमंड वील, उइछ की जरूरत होती है। इसके कारण उसकी धार लगाने की कीमत भी ज्यादा होती है।
बिर्ला प्रिसिजन टेक्नो लिमिटेड (इंडियन टूल्स) की विशेषता
ग्राहक की जरूरत के मुताबिक 0.75 से 135 मिमी. व्यास के, टेपर या समानांतर तथा 2000 मिमी. तक की लंबाई के (L/D के अनुसार) ड्रिल तैयार करना इस कंपनी की खासियत है। यह ड्रिल डीप होल ड्रिलिंग में इस्तेमाल किए जाते हैं। डीप होल ड्रिलिंग में ड्रिल टूटने की संभावना बहुत अधिक होती है। इसकी वजह से बहुत ही परेशानी होती है क्योंकि ऐसे ड्रिल के टुकड़े बाहर निकालना बहुत कष्टदायक होता है। इसलिए वहाँ एच.एस.एस. टूल का व्यापक रूप से इस्तेमाल किया जाता है।
ग्राहक सेवा
यह कंपनी स्लैब मिलिंग कटर का भी उत्पादन करती है। गन मेटल, तांबा, पितल जैसे नॉन फेरस कास्टिंग की मिलिंग के लिए स्लैब मिलिंग कटर का इस्तेमाल किया जाता है। इसके लिए बनाए गए खास एस.पी.एम. पर इस प्रकार के दो कटर के बीच में से नॉन फेरस धातु का तख्ता (स्लैब) पार किया जाता है और इस प्रकार दोनों पृष्ठों का यंत्रण एक ही समय किया जाता है। इसका व्यास 205 मिमी. और लंबाई 550 मिमी. है। इंटरप्टेड कटिंग का यह काम, अपेक्षा के अनुसार, कार्बाइड का कटर नहीं कर सका। इसलिए वह एच.एस.एस. में ही बनाना पड़ा। कटर ग्राहक के पास जाने के कुछ समय बाद शिकायत आई कि कंपनी ने दिया हुआ कटर अपेक्षानुसार काम नहीं कर रहा है। टूल ‘चिप ऑफ’ हो गया है। ग्राहक के पास जा कर देखने पर मालूम हुआ कि उस कटर पर कोल्ड वेल्डिंग हुआ है। बहुत सोचने पर समझ में आया कि कोल्ड वेल्डिंग होने का मतलब है ज्यादा घर्षण। मटीरीयल ज्यादा चिकना होगा या शीतक (कूलंट) का चुनाव योग्य नहीं होगा। इसलिए हर घटक की जाँच की गई। शीतक तथा मटीरीयल की जाँच की गई, टूल की ज्यामिति परखी गई। “क्या आपने टूल को फिर से धार लगाई है?” ग्राहक से यह पूछने पर उन्होंने यह बात मान ली। हम ऑपरेटर के साथ रीग्राइंडिंग मशीन देखने गए तब ध्यान में आया कि उस मशीन पर ‘फिंगर’ नहीं था। (रीग्राइंडिंग करते समय मशीन पर ‘फिंगर’ न हो तो हर टिप का रेक ऐंगल एकसमान नहीं आता है। जिसके कारण ऐसे टूल के साथ काम करते समय, असमान बल उत्पन्न हो कर, कार्यवस्तु का फिनिश बिगड़ सकता है। साथ ही टूल की आयु भी कम हो जाती है।) हमने जब निरीक्षण किया तब कटर पर फ्लूटिंग का काम चल रहा था। लेकिन वहाँ कोई रेफरन्स नहीं था जिसके अलावा कटर की ज्यामिति बनाना संभव नहीं था। इसके बाद मशीन पर एक पट्टी लगा कर कटर का रीग्राइंडिंग करने पर समस्या सुलझ गई।
‘फिंगर’, टूल ऐंड कटर ग्राइंडिंग मशीन का एक महत्वपूर्ण भाग होता है। पहले इसे बिना लगाए कटर फ्लूट ग्राइंडिंग किया जाता था। जिसकी वजह से ‘इंडेक्सिंग एरर’ तैयार होते थे। ‘इंडेक्सिंग एरर’ के कारण हर कटिंग एज पर एकसमान भार नहीं रहता है, जिसके कारण वे टूटते हैं या मटीरीयल न कटते हुए कोल्ड वेल्डिंग हो सकता है। ‘इंडेक्सिंग एरर’ तैयार होने पर यंत्रण करते समय झटका (जर्क) लगता है। जिसके कारण टूल की आयु कम हो जाती है। फिंगर लगाने से कटर की एकरूपता (युनिफॉर्मिटी) तथा रेक ऐंगल एकसमान रखने में मदद हुई।
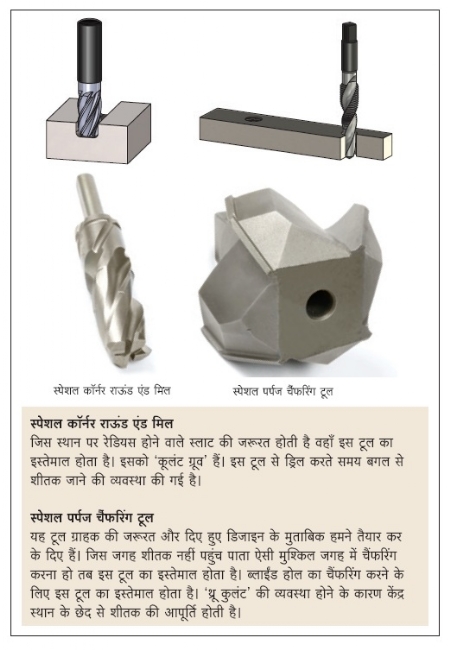
इसके अलावा यह कंपनी कॉम्बिनेशन टूल भी बनाती है। इससे ड्रिलिंग, रिमिंग, काउंटर बोरिंग और चैंफरिंग में से कोई भी एक से अधिक काम, एक ही समय हो सकते हैं। एक ही सेटअप में ड्रिलिंग कर के थ्रेडिंग भी कर सकते हैं। इस प्रकार के उत्पादन विशेष जरूरतों के अनुसार तैयार कर के दिए जाते हैं। इसकी वजह से मशीन सेटअप करने में जाने वाला और ऑपरेटर का भी समय बचता है। एक ही सेटअप में सभी ऑपरेशन होते हैं। फलस्वरूप मशीन और व्यक्ति की उत्पादकता बढ़ती है। इसकी वजह से ग्राहक के (मटीरीयल हैंडलिंग जैसे) अनदेखे व्यय घटते हैं। जिसके कारण उत्पादन की कीमत कम हो सकती है। आज की तीव्र प्रतिस्पर्धा की दुनिया में बने रहने के लिए कॉम्बिनेशन टूल का इस्तेमाल अनिवार्य है। इसमें ड्रिल कम रीमर, स्टेप ड्रिल, ड्रिल कम टैप, सबलैंड ड्रिल जैसे कई टूल शामिल हैं। ये कॉम्बिनेशन टूल कार्बाइड में बनाना मुश्किल होने के कारण एच.एस.एस. अच्छा विकल्प है। जब तक पुरानी मशीन का उपयोग होने वाला है तब तक ऐसे टूल की माँग होती ही रहेगी और एच.एस.एस. का मार्केट अखंडित रहेगा।
0 9960200268
aniltidke@indiantool.com
अनिल त्र्यंबक तिडकेजी पिछले 23 सालों से एच.एस.एस. कटिंग टूल के क्षेत्र में कार्यरत है। उत्पादन, ऐप्लिकेशन इंजीनीयरिंग तथा अनुसंधान एवं विकास इन तीनों क्षेत्रों में आपका तजुर्बा रहा है।