हर सी.एन.सी. मशीन टूल उसमें समाविष्ट प्रोग्रैमिंग के अनुसार काम करता है। प्रोग्रैम में दिए हुए निर्देशों के मुताबिक काम होने के लिए मशीन के संबंधी पुर्जों का संचलन अपेक्षित अचूकता से होना महत्वपूर्ण है। लेसर तंत्रज्ञान के उपयोग से, ISO:230-2 मानकों के अनुसार मशीन कैलिब्रेट करने की विस्तृत जानकारी इस लेख में दी गई है।
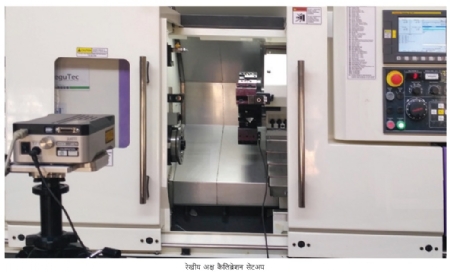
सामान्य रूप से किसी भी मापन साधन का कैलिब्रेशन करने का उद्देश्य यह होता है कि उस साधन द्वारा लिए गए रीडिंग की अचूकता की मानक (स्टैंडर्ड) के साथ पड़ताल की जाए और जरूरत हो तो उसमें सुधार किए जाए। सी.एन.सी. मशीन का उपयोग यंत्रण के लिए होता है। उसे इस्तेमाल करते हुए, प्रोग्रैम के अनुसार यंत्रण करने से बनने वाली कार्यवस्तु में प्रत्याशित व्यास, लंबाई या अन्य नाप पाए जा रहे हैं या नहीं यह सुनिश्चित करना जरूरी होता है। इसलिए इस मशीन का समय समय पर कैलिब्रेशन करना आवश्यक है। मशीन की घिसाई, वातावरणीय तापमान में होने वाले बदलाव आदि के कारण बनाई गई कार्यवस्तुओं के नाप में खामियाँ आ सकती हैं, जो प्रोग्रैम का ही एक हिस्सा बन जाती हैं। ऐसी खामियाँ दूर करने के लिए कैलिब्रेशन करवाना उपयोगी होता है।
सी.एन.सी. मशीन की अचूकता एवं पुनरावर्तन की क्षमता (रिपीटैबिलिटी) का नियंत्रण करने हेतु नियमित अवधि के बाद लेसर मापन प्रणाली (एल.एम.एस.) का प्रयोग कर के सी.एन.सी. मशीन की जांच की जाती है। इसका इस्तेमाल टाईप परीक्षा, स्वीकार परीक्षा, तुलनात्मक परीक्षा, नियमित सत्यापन (वेरिफिकेशन), मशीन कॉम्पेन्सेशन आदि के लिए किया जाता है। लेसर मापन प्रणाली की मदद से सी.एन.सी. मशीन के अक्षों का स्थान निर्धारण (पोजिशनिंग), अचूकता एवं पुनरावर्तन की क्षमता का परीक्षण और मूल्यांकन करने का तरीका खडज:230-2 मानक से पाया जाता है। ये तरीके रेखीय (लीनियर) एवं चक्रीय (रोटरी) दोनों अक्षों को समान रूप में लागू होते हैं किंतु जब एक साथ कई अक्षों की जांच की जाती है तब ये तरीके लागू नहीं होते।
कैलिब्रेशन करने के लिए इस्तेमाल किए जाने वाले उपकरण
लेसर मापन प्रणाली में लेसर हेड, ट्राइपॉड, डिस्प्ले यूनिट (एवं/या) कंप्यूटर, वातावरण क्षतिपूर्ती इकाई (कॉम्पेन्सेशन यूनिट), वायु का तापमान नापने वाला सेन्सर, मटीरीयल का तापमान नापने वाला सेन्सर और रेखीय अक्षों की अचूकता एवं पुनरावर्तन क्षमता नापने हेतु आवश्यक फिक्श्चर समेत प्रकाशीय (ऑप्टिकल) उपकरण शामिल होते हैं जो राष्ट्रीय/अंतर्राष्ट्रीय मानकों से संबद्ध किए जा सकते हैं।
मापन उपकरण एवं साधन उचित तरह से ‘अर्थिंग’ कर के बिजली के मुख्य सप्लाई से जोड़े होने चाहिए। मशीन की धातुई बॉडी और बिजली की सप्लाई का ‘अर्थ’ पॉइंट इनके बीच का ए.सी. लीकेज वोल्टेज 0.2 V ए.सी. से कम होने की निश्चिति की जानी चाहिए। जांचना जरूरी है कि मशीन के साथ दिए गए इंटरफेस के जरिए, सामान्य स्थिति में, संगणक के साथ लेसर हेड में भी सारे कार्य ठीक से हो रहे हैं या नहीं।
साईट की वातावरणीय स्थिति का मापन
मापन करते समय यह जरूर देखें कि वातावरण का तापमान उत्पादक द्वारा सूचित सीमा से कम है। लेसर मापन प्रणाली के सप्लाइअर ने दिए निर्देशों के अनुसार, यदि वातावरण का तापमान 00 से 400 से. की सीमा में हो, तो ही प्रणाली की मदद से कैलिब्रेशन करें। यदि मापन के समय वातावरण का तापमान 200 से. से अलग हो तो अक्ष स्थिति निर्धारण प्रणाली एवं मशीन टूल बॉडी के प्रतिनिधिक हिस्से (जैसे कि मशीन टेबल) के बीच विस्तारण से पैदा हुई सूक्ष्म दूरी की मरम्मत कर के, 200 से. के लिए, सुधारित परिणाम दिए जाते हैं।
मशीन इन्स्टॉलेशन
कैलिब्रेशन आरंभ करने से पहले मशीन पूरा जोड़ कर सही बुनियाद पर क्लैम्प/ग्राउट किया होना आवश्यक है। साथ ही यह भी जरूरी है कि उत्पादक के निर्देशोंनुसार मशीन पूरी तरह से सक्रिय हो तथा उसका ज्यामितिक संरेखन एवं क्रियात्मक परीक्षण पूरा किया गया हो। सारे मापन तब ही करें जब मशीन पर कोई भार न हो यानि कि उस पर कार्यवस्तु बिठाई ना हो। मापन प्रणाली से मशीन जोड़ते वक्त वह सही तरह से ‘अर्थ’ किया हुआ हो। ध्यान में रखें कि मशीन का तापमान स्थिर करने हेतु मशीन वार्म अप किया हुआ हो।
मापन की शर्तें एवं लक्ष्य स्थान (टार्गेट पोजिशन)
सी.एन.सी. मशीन के रेखीय एवं चक्रीय ये दोनों अक्ष जितने परिशुद्ध हों, उतने ही उस मशीन के प्रोग्रैम द्वारा किए यंत्रण से बनी हुई कार्यवस्तु के नाप सटीक होंगे। इसलिए हर अक्ष पर अलग अलग दूरी पर कई बिंदु चुने जाते हैं और आरंभ बिंदु से उनकी दूरी नाप कर मानक के साथ पड़ताल की जाती है। इन विभिन्न बिंदुओं को ही लक्ष्य स्थान कहा जाता है। जिसका कैलिब्रेशन करना हो वह मशीन अक्ष उसके संचलन की सीमाओं में हिलाया जाता है। उस वक्त अन्य अक्ष, जितना हो सके, केंद्रस्थान पर रखे जाते हैं। मशीन में ऐसा प्रोग्रैम बनाया जाता है कि जांच होने वाला अक्ष, लक्ष्य स्थानों की एक मालिका में क्रमिक रूप से हिलाया जाए। प्रोग्रैम में यह सुविधा की जाती है कि इन लक्ष्य स्थानों पर पहुंच कर, नपाई करने के बाद उनका रीडिंग लिया जाने तक वह अक्ष उस स्थान पर स्थिर रहे। मापन के दोनों तरफ अक्ष को थोड़ा आगे या पीछे जाने के लिए (ओवरशूटिंग) जगह रख कर (अक्ष का थोड़ा आगे या थोड़ा पीछे के स्थान पर होना) लक्ष्य स्थानों पर विस्थापन (डिस्प्लेसमेंट) नापा जाता है। इन लक्ष्य स्थानों पर पहुंचने के लिए मशीन के प्रोग्रैम में मशीन उत्पादक तथा ऑपरेटर के बीच सहमती से निश्चित की हुई यंत्रण गति एवं सरकने की गति अपनाई जाती है, वरना अक्ष का रैपिड फीड रेट अपनाया जाता है।
लक्ष्य स्थान (Pi) का चयन
हर लक्ष्य स्थान का चयन निम्न सूत्र का प्रयोग करते हुए किया जाएगा
Pi = (i - 1) p + r, जहाँ
i = वर्तमान लक्ष्य स्थान का अनुक्रमांक,
p = अक्ष की यात्रा के मार्ग पर होने वाले लक्ष्य स्थानों के बीच की नियमित दूरी
r = ± 30 % p की सीमाओं के बीच का एक अंक ।
स्वीकार के अमल के लिए चयनित लक्ष्य स्थान, संबंधी अक्ष के स्थान निर्धारण में रही त्रुटियों की संख्यात्मक क्षतिपूर्ती हेतु इस्तेमाल होने वाले, नमूना बिंदुओं से अलग होते हैं।
2000 मिमी. तक की लंबाई के रेखीय अक्षों के लिए मापन
जैसे कि पहले बताया गया है, हर मीटर की लंबाई पर कम से कम पांच लक्ष्य स्थान चुनें। सभी लक्ष्य स्थानों पर मानक जांच आवर्तन के अनुसार मापन करने हैं (ISO : 230-2 के अनुसार, चित्र क्र. 1)। हर लक्ष्य स्थान पर, हर दिशा से, पांच बार पहुंचना है। इस तरह से पहुंचते हुए निश्चित की गई यंत्रण की गति एवं सरकने की गति प्राप्त करने हेतु (यानि कि मशीन सामान्य तरह से काम कर रहा है यह सुनिश्चित करने के लिए) दिशा बदलने का उचित स्थान चुनना जरूरी है।
2000 मिमी. से अधिक लंबाई के रेखीय अक्षों के लिए मापन
औसत 250 मिमी. की दूरी रखते हुए चुने गए लक्ष्य स्थानों पर, हर दिशा से एक एकदिशा मार्ग (युनिडाइरेक्शनल ऐप्रोच) रख कर अक्ष की पूरी लंबाई पर की यात्रा जांची जाती है। इसके अलावा, 2000 मिमी. तक की लंबाई के रेखीय अक्षों के लए बताई गई जांच भी की जाती है।
3600 तक के चक्रीय अक्षों का मापन
अन्य लक्ष्य स्थानों के साथ 00, 900, 1800 एवं 2700 के प्रधान स्थान भी शामिल करें। हर लक्ष्य स्थान पर हर दिशा से पांच बार पहुंचना जरूरी है। लक्ष्य स्थानों का चयन निम्न विधिनुसार करें
• ≤ 900 : कम से कम 3 लक्ष्य स्थान
• > 900 और ≤ 1800 : कम से कम 5 लक्ष्य स्थान
• > 1800 : कम से कम 8 लक्ष्य स्थान
3600 से अधिक चक्रीय अक्षों का मापन
हर परिक्रमा में कम से कम 8 लक्ष्य स्थान चुन कर हर दिशा से एक एकदिशा मार्ग रख कर अक्ष की कुल मापन यात्रा की 18000 में (पांच परिक्रमाएं) नपाई करें। इसके अलावा, 3600 तक के चक्रीय अक्षों के लिए बताई गई जांच भी करें।
लेसर संरेखन, मापन सेटअप एवं एकरेखन (अलाईनमेंट)
एल.एम.एस. ऑप्टिक्स का दिशादर्शन अनुकूल बना लिया जाता है और लेसर मापन प्रणाली की निर्देशपुस्तिका में दिए गए निर्देशों के अनुसार ऑप्टिकल उपकरण जगह पर रखा जाता है। मशीन के हिलते हिस्से पर परावर्तक (रिफ्लेक्टर) बिठा कर स्थिर हिस्से पर इंटरफेरोमीटर बिठाया जाता है (संचलनक्षम स्लाईड होना और भी अच्छा है)। ट्राइपॉड की माउंटिंग प्लेट पर लेसर हेड रख कर वह इंटरफेस द्वारा संगणक से जोड़ा जाता है। लेसर बीम का संरेखन हिलने वाली स्लाईड के पूरे स्ट्रोक के साथ किया जाता है। लेसर मापन प्रणाली की निर्देशपुस्तिका में बताएनुसार वातावरण कॉम्पेन्सेशन यूनिट, वायु के तापमान का सेन्सर एवं मटीरीयल के तापमान का सेन्सर मापन प्रणाली से जोड़े जाते हैं (चित्र क्र. 2)।
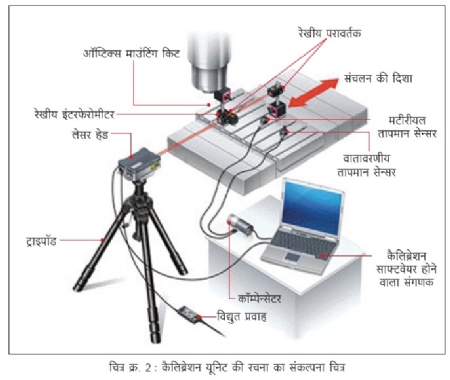
कोई भी मापन आरंभ करने से पहले मापन के चिह्नों के संकेत जान लेना आवश्यक है। जब इंटरफेरोमीटर को जांच किए जाने वाले अक्ष की दिशा में रखा हो और वह स्थायी स्थिति में हो तो धनात्मक त्रुटि (पॉजिटिव एरर) की दिशा से इंटरफेरोमीटर को हल्का धक्का दे कर लेसर डिस्प्ले धनात्मक (+ve) होने की निश्चिति की जाती है। विस्थापन की धनात्मक दिशा, संबंधी अक्ष की धनात्मक दशा में होनी चाहिए। स्वचालित वातावरण कॉम्पेन्सेशन क्रियान्वित किया जाता है और साफ्टवेयर में उचित मटीरीयल विस्तार गुणांक शामिल होने की निश्चिति की जाती है। रेखीय मापन में वातावरण क्षतिपूर्ति शामिल करने की सिफारिश काफी जोर दे कर की जाती है। मशीन की फीडबैक प्रणाली का विस्तार गुणांक सामान्यतः साफ्टवेयर में डाला जाता है (स्टील रैक, पिनियन ड्राईव एवं बॉल स्क्रू के लिए 11.7 पी.पी.एम./मी., ग्लास स्केल रेखीय एनकोडर के लिए 8 पी.पी.एम./मी.)। लक्ष्य स्थान, रन की संख्या और इन लक्ष्य स्थानों में से गुजरने का फीड रेट ऊपरलिखित तरीके से निश्चित कर के सेटअप किया जाता है।
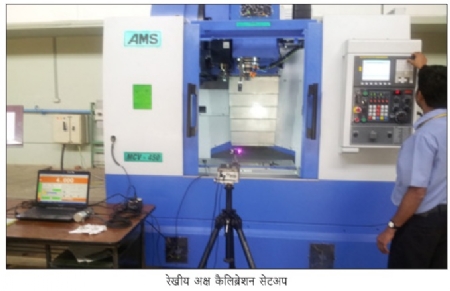
अक्ष को उसके आरंभ से अंत तक हिला कर, आखरी लक्ष्य स्थान तक रीडिंग में होने वाली क्रमिक वृद्धि पर ध्यान दिया जाता है। बड़ा स्लोप, रिफ्लेक्टर टेढ़ा कर के निकाला जाता है और बचा हुआ छोटा स्लोप, प्रणाली की निर्देशपुस्तिका में शामिल निर्देशों के मुताबिक, साफ्टवेयर द्वारा दूर किया जाता है। एकक एवं लेसर मापन डिस्प्ले तथा त्रुटि मूल्य के रीडिंग निश्चित किए जाते हैं। लेसर प्रणाली की दिशा जांच के अंतर्गत रही मशीन समान रखी जाती है। रेखीय मापन के लिए लेसर डिस्प्ले के चिह्न का मेल, मशीन के अक्ष के चिह्न से होना जरूरी है।
मापन कार्यविधि
मापन दो चरणों में किया जाता है।
• पिच एरर/ बैकलैश एरर कॉम्पेन्सेशन : स्थान त्रुटि का मापन कर के अक्ष में पाए जाने वाले पिच एवं बैकलैश एरर का अंदाजा लगाया जाता है।
• मशीन कैलिब्रेशन: स्थान त्रुटि का मापन कर के, जांच किए जा रहे अक्ष की संपूर्ण अचूकता एवं पुनरावर्तन क्षमता का अंदाजा ISO:230-2 मानक के अनुसार लगाया जाता है।
पिच एरर/बैकलैश एरर कॉम्पेन्सेशन
मशीन अक्ष का कैलिब्रेशन करने से पहले समान दूरी पर रहे लक्ष्य स्थानों की त्रुटियों का मापन कर के रेखीय पिच एरर का कॉम्पेन्सेशन किया जाता है। अक्ष की यात्रा की लंबाईनुसार प्रोग्रैम में 20 मिमी. या 50 मिमी. का अंतराल (इंटर्वल) ड़ाल कर शुरुआती त्रुटि निश्चित की जाती है। मशीन की सी.एन.सी. कंट्रोल सिस्टम की विशेषताओं का इस्तेमाल कर के पिच एरर कॉम्पेन्सेशन के लिए जरूरी सुधार किए जाते हैं। जांच हो रहा अक्ष आरंभ स्थान से थोड़ा आगे हिला कर फिर आरंभ स्थान पर वापस लाया जाता है और लेसर डिस्प्ले पर दिखने वाला रीडिंग शून्य पर सेट किया जाता है। लेसर संगणक में अक्ष प्रोग्रैम चलाया जाता है और, सरकने की चयनित गति पर मशीन की सी.एन.सी. प्रणाली में प्रोग्रैम का एक आवर्तन चलाया जाता है। निश्चित किए हुए हर लक्ष्य स्थान पर जानकारी (डाटा) इकट्ठा की जाती है, उसे जतन (सेव) किया जाता है और उसका विश्लेषण भी किया जाता है।
प्रणाली द्वारा निर्धारित किए गए त्रुटि क्षतिपूर्ती मूल्यों के प्रयोग से रेखीय त्रुटियों में सुधार किए जाते हैं। रेखीय त्रुटि एवं बैकलैश इन दोनों के लिए त्रुटि क्षतिपूर्ती मूल्य मशीन के नियंत्रक में ड़ाले जाते हैं। कंट्रोल सिस्टम की विशेषताओं के अनुसार इस त्रुटि क्षतिपूर्ती का समावेश, आवश्यकतानुसार, एकदिशा/द्विदिशा (बाइडाइरेक्शनल) क्षतिपूर्ती में किया जाता है। संतोषजनक मूल्य पाए जाने तक (प्रस्तावित स्वीकार्य मूल्यों के 50-60%) कैलिब्रेशन आवर्तन एवं त्रुटि मापन दोहराए जाते हैं। मापन में पिच एरर क्षतिपूर्ती शामिल करने से पहले और पश्चात एवं ISO:230-2 के अनुसार, मूल्यांकन किए हुए अक्षों की अचूकता का उदाहरण तालिका क्र. 1 और 2 में दर्शाया है।
मशीन कैलिब्रेशन
कुछ उद्देश्यों को सामने रख कर प्रोग्रैम आवर्तन का चयन किया जाता है। यात्रा के दोनों तरफ ओवरशूट एवं, लक्ष्यों की ओर द्विदिशा मार्ग के साथ, पांच आवर्तों के लिए मापन दोहराया जाता है। निश्चित किए हुए हर लक्ष्य स्थान पर जानकारी ले कर वह जतन की जाती है और उसका विश्लेषण किया जाता है।
मापन जानकारी का विश्लेषण एवं मूल्यांकन ISO:230-2:2014 (मशीन टूल के लिए टेस्ट कोड : संख्यात्मक तरीके से नियंत्रित अक्षों की अचूकता एवं पुनरावर्तन की क्षमता का निर्धारण) के अनुसार किया जाता है। जरूरी हो तो इस जानकारी का मूल्यांकन VDI/DGQ : 3441 (मशीन टूल की परिचालनात्मक एवं स्थान निर्धारण अचूकता का संख्यात्मक परीक्षण) के अनुसार भी कर सकते हैं।
इकट्ठा की हुई जानकारी का मूल्यांकन लेसर प्रणाली से जुड़े संगणक द्वारा किया जाता है। परिणाम प्रस्तुति के संदर्भ में तालिका क्र. 3 में दिए गए आलेख के अनुसार होने वाली विधि को प्रधानता दी जाती है। इसमें मापन और मशीन का संपूर्ण विवरण दिया जाता है।
कैलिब्रेशन मापन से आगे दिए गए पैरामीटर निश्चित हो सकते हैं। मानक के अनुसार स्वीकार्य मूल्य तालिका क्र. 4 और 5 में दर्शाए हैं।
अ) 2000 मिमी. तक की लंबाई के रेखीय अक्षों के लिए पैरामीटर
1. अक्ष के द्विदिशा स्थान निर्धारण में त्रुटि (A)
2. अक्ष के एकदिशा स्थान निर्धारण में त्रुटि (A↑ और A↓)
3. अक्ष के द्विदिशा पद्धतिबद्ध (सिस्टमैटिक) स्थान निर्धारण में त्रुटि (E)
4. अक्ष के मध्य द्विदिशा स्थान निर्धारण की त्रुटियों की व्याप्ति (M)
5. अक्ष के एकदिशा स्थान निर्धारण में रही पुनरावर्तन की क्षमता (R↑ और R↓)
6. अक्ष की व्युत्क्रम (रिवर्सल) त्रुटि (B)
आ) 2000 मिमी. से अधिक लंबे रेखीय अक्षों के लिए पैरामीटर
1. अक्ष की द्विदिशा पद्धतिबद्ध (सिस्टमैटिक) स्थान निर्धारण में त्रुटि (E)
2. अक्ष के एकदिशा पद्धतिबद्ध (सिस्टमैटिक) स्थान निर्धारण में त्रुटि (E↑ और E↓)
3. अक्ष के मध्य द्विदिशा स्थान निर्धारण की त्रुटियों की व्याप्ति (M)
4. अक्ष की व्युत्क्रम त्रुटि (B)
दर्ज की हुई मापन जानकारी में तारीख, समय, मशीन, इस्तेमाल किया हुआ उपकरण एवं मापन की रेखा का स्थान, विश्लेषण पद्धति, ऑपरेशन मोड, ड्वेल टाईम, जांच ना होने वाले अक्षों की स्थिति, इस्तेमाल की हुई क्षतिपूर्ती, इस्तेमाल किए चिह्न संकेत एवं फीड की दिशा आदि मुद्दे शामिल होते हैं।
संदर्भ दस्तावेज
• ISO 230-2:2014 या JIS 6192-2:1999 मशीन टूल के टेस्ट कोड - भाग 2 : संख्यात्मक तरीके से नियंत्रित अक्षों की अचूकता एवं पुनरावर्तन की क्षमता का निर्धारण
• VDI/DGQ : 3441, मशीन टूल की परिचालनात्मक एवं स्थान निर्धारण अचूकता का संख्यात्मक परीक्षण
0 9448709859
director@amttf.in
मशीन टूल टेस्टिंग, असेम्ब्ली, डिजाइन एवं उत्पाद अभियांत्रिकी में 40 से अधिक साल का अनुभव रखने वाले वाय. बालरामैय्याजी पिछले 7 साल ‘ऐडव्हान्स्ड् मशिन टूल टेस्टिंग फॅसिलिटी (AMTTF)’ के संचालक हैं। BIS के PGD-35 और MED-40 विभागों की कमिटी में आप IMTMA का प्रतिनिधित्व करते हैं।