पुराना तरीका
हमारे एक ग्राहक थर्मोकपल का उत्पादन करते हैं। इस थर्मोकपल में एक तरफ तांबे (कॉपर) का तार और दूसरी तरफ मिश्रधातु का तार होती है। इन तारों का व्यास 0.8 मिमी. होता है। कॉपर वेल्डिंग बहुत ही जटिल प्रक्रिया है। ग्राहक ने वह प्रक्रिया विकसित की थी जिसमें ऑपरेटर एक प्रकार के, 80 मिमी. लंबाई का तार काट लेता था और उतनी ही लंबाई के दूसरे प्रकार के तार काटता था। 80 मिमी. के दोनों टुकड़े एक बाएं और एक दाहिने हाथ में पकड़ कर, आँखों से देख कर जितनी अचूकता से आमने सामने ला कर, ऑपरेटर उनका स्पॉट वेल्डिंग करता था। चूंकि यह पूरी प्रक्रिया हाथ से यानि मैन्युअली होती थी, प्रत्याशित उत्पादकता एवं गुणवत्ता नहीं मिलती थी।
प्रक्रिया में रही समस्याएं
1. दोनों तार एक दूसरे में फंस जाना।
2. वेल्ड पूरा ना होना।
3. वेल्डिंग के दौरान तार बहुत ही गर्म होना और इस कारण उत्पादकता ना मिलना, यह प्रधान समस्या थी।
4. तार हाथ से काटा जाने के कारण टुकड़ों की लंबाई में फर्क आना।
5. ऑपरेटर के हाथ जल जाना। ये तार बहुत ही छोटे होने के कारण हैंडग्लव पहन कर काम करना मुश्किल था। ग्राहक ने यह समस्या सुलझाने के लिए हमारे पास स्वचालन की मांग की।
नया तरीका
आरंभ में हमने वेल्डिंग मशीन में स्वचालन करने की कोशिश की किंतु उसमें रही समस्याएं जल्द ही नजर आईं। इसलिए हमने तय किया कि ग्राहक जिस वेल्डिंग मशीन का इस्तेमाल तथा जिस वेल्डिंग प्रक्रिया का पालन कर रहा है, उसमें बदलाव ना किया जाए। इसमें मुख्य कठिनाई थी ग्राहक के पास वर्टिकल टाइप स्पॉट वेल्डिंग मशीन था। उसमें नीचे एक इलेक्ट्रोड और ऊपर एक इलेक्ट्रोड था। तार बनने के बाद वें नीचे गिर जाना भी जरूरी था, इसलिए हम मशीन की खड़ी रचना नहीं चाहते थे। इसलिए हमने मशीन का खड़ा रूप बदल कर आड़ा (हॉरिजोन्टल) कर दिया। स्वचालन की यह एक महत्वपूर्ण जरूरत थी।
नई रचना के परीक्षण किए गए और वे कामयाब भी रहे। इसके पश्चात हमने 2 कटर विकसित किए और केंद्र से बाईं एवं दाईं तरफ 80 मिमी. की दूरी पर लगा दिए। परंतु अब असली समस्या हमारे सामने आ गई। पुराने तरीके में जब ऑपरेटर खुद वेल्डिंग करता था तब तार थोड़ा टेढ़ा मेढ़ा होने के बावजूद वह अपनी आँखों से देख कर वेल्डिंग कर पाता था। लेकिन मशीन वेल्डिंग के लिए पूरी तरह सीधे तार की जरूरत थी। इसके लिए हमने कटर के पीछे दो दिशाओं में तार सीधे करने वाले साधन (वायर स्ट्रेटनर) भी निर्माण किए।
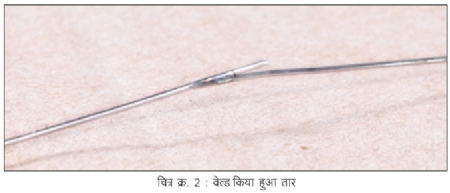
चूंकि तार तांबे जैसी नर्म धातु से बना था, उसको सीधा करना मुश्किल था। लेकिन थोड़े प्रयास के बाद हम वह कर पाए। तार सीधा करने के लिए हमने रोलर का एक सेट इस्तेमाल किया। 5 रोलर का एक सेट खड़ा और एक आड़ा, इस तरह 2 सेट का प्रयोग हमने किया। 80 मिमी. लंबे तार फीड करने हेतु हमने सामान्य रोलर फीडर इस्तेमाल करने की कोशिश की। मगर, चूंकि यह तार 0.8 मिमी. तक लघु व्यास का और तांबे जैसे लचीले मटीरीयल का बना था, रोलर प्रकार का फीडर काम नहीं कर रहा था। इसके लिए हमने एक न्यूमैटिक फीडर बनाया जिसमें 80 मिमी. आगे पीछे होने वाली स्लाइड है और उस पर एक ग्रिपर असेम्ब्ली है। इस तरह दो असेम्ब्ली मिला कर फीडर बनाया गया। तांबे का तार चाहे जितना सीधा किया जाने पर भी, कटर से 80 मिमी. की दूरी पर उनके केंद्र मिलने तथा दोनों तार एक दूसरे पर आ कर जुड़ जाने की नई चुनौती हमारे सामने खड़ी हुई। दोनों तार ठीक आमने सामने होने पर भी 50% बार उचित जोड़ नहीं मिल पाता था। क्योंकि तार एक दूसरे पर जब तक नहीं आते तब तक वेल्डिंग नहीं होता था। इसलिए 50 का कोण दिया गया, फिर दोनों तार एक दूसरे के ठीक सामने न आ कर, कुछ मात्रा में तिरछे (क्रॉस) आने लगे। एक तार से दूसरे तार में विद्युत प्रवाह जाने के बाद ही वेल्डिंग होता है। यह ‘बट वेल्डिंग’ नहीं है। 0.8 मिमी. की तार का बट वेल्डिंग करना नामुमकिन है, इसलिए हमें यह रास्ता अपनाना पड़ा। तार सीधा रख कर केंद्र तक पकड़ कर रखना महत्वपूर्ण बन गया। इसके लिए एक होल्डर असेम्ब्ली विकसित की गई, जिसमें वेल्ड होने तक तार होल्डर में पकड़ा जाता हैं। यह होल्डर खड़ी दिशा में दो हिस्सों में विभाजित किया होता है। वेल्डिंग खत्म होने के बाद यह खुलता है और वेल्ड हुआ तथा काटा गया तार नीचे गिरता है।
लाभ
1. उत्पादन 1000 जोड़ से 2400 जोड़ों तक बढ़ गया, यानि उत्पादकता बढ़ गई।
2. बनाए गए जोड़ एकसमान होने के कारण, पुरानी विधि में बेकार जाने वाला 10 -12% मटीरीयल बच गया।
3. गुणवत्ता में वृद्धि हुई।
4. बनने वाले जोड़ मशीन से एक ही दिशा में (ओरिएंटेड) आना शुरु हुआ, जिससे पैकिंग से पहले वें सही तरीके में रखने में व्यय होने वाला समय बच गया।
5. कुल प्रक्रिया अधिक सुरक्षित बन गई।
0 9422086165
prasannafabex@gmail.com
प्रसन्न अक्कलकोटकरजी यांत्रिकी अभियंता हैं। आप ‘फैबेक्स इंजीनीयर्स’ के संचालक हैं और आप को स्वचालन क्षेत्र का 25 सालों से अधिक अनुभव है ।