आज के जमाने की यंत्रण प्रक्रिया में बहुत सी ज्यामितीय विशेषताएं, विशिष्ट सीमाओं में अचूकता से नियंत्रित करना जरूरी होता है। इनमें से एक विशेषता है समतलता यानि फ्लैटनेस। जब किसी पृष्ठ की समतलता के संदर्भ में कुछ अंकीय मूल्य बताए जाते हैं, तब उनका मतलब होता है संबंधि पृष्ठ पर स्थित सभी बिंदु जिन दो काल्पनिक प्रतलों (प्लेन) के बीच में होंगे, उन दोनों प्लेन के बीच की अधिकतम दूरी। मिसाल के तौर पर, किसी पृष्ठ की समतलता 20 माइक्रोन बताई जाए, तो उस पृष्ठ के सर्वोच्च बिंदु संबंधि पृष्ठ से समानांतर प्रतल और सबसे गहरे बिंदु संबंधि समानांतर प्रतल के बीच की दूरी 20 माइक्रोन (चित्र क्र. 1, 2, 3) होगी।
घटिया समतलता दर्शाने के दो प्रकार1. पहले प्रकार में, पृष्ठ पर आसानी से दिखते उंच नीच हिस्से नहीं होते। हाथों को तो पूरा पृष्ठ बिल्कुल चिकना प्रतीत होता है, लेकिन इस पृष्ठ की समतलता का मूल्य सी.एम.एम. पर नापा जाए, तो वह सीमा (टॉलरन्स) के बाहर होती है।
2. दूसरी तरह की घटिया समतलता, यंत्रण के दौरान पैदा हुए उतार-चढ़ावों के कारण होती है और वह दिखाई भी देती है।
इससे भी घटिया स्थिति में ऊपर दिए हुए दोनों का मिश्रण होता है।
हम पहले प्रकार की चर्चा करेंगे। कार्यवस्तु पर पड़ने वाले यंत्रण भार या कार्यवस्तु पकड़ने के लिए इस्तेमाल किए जाने वाले फिक्श्चर/क्लैंप के कारण पैदा हुए तनाव से कार्यवस्तु में आने वाले डीफॉर्मेशन की वजह से यह घटिया समतलता पैदा होती है। यहाँ ध्यान में रखना चाहिए कि पुर्जों में इस तरह आने वाला विरूपण (डिस्टॉर्शन) थोड़ा अस्थायी (इलैस्टिक) और थोड़ा स्थायी (प्लैस्टिक) होता है।
ऐसी स्थिति में, मिलिंग प्रक्रिया द्वारा समतलता नियंत्रित करते समय आगे दी गई बातों का ध्यान रखना जरूरी है।
1. क्लैंपिंग और यंत्रण भार से पुर्जा मुड़ने की संभावना धातु की बुनियादी ताकत और उसकी भौतिक संरचना पर, यंत्रण के दौरान होने वाला विरूपण निर्भर करता है। इन दो घटकों का विचार करते हुए कार्यवस्तु पकड़ने के लिए इस्तेमाल किए जाने वाले फिक्श्चर का डिजाइन और क्लैंपिंग का दबाव तय किया जाता है। कटिंग टूल और पैरामीटर का चुनाव भी इन्हीं दो घटकों पर निर्भर करता है। पुर्जों के विरूपण के संदर्भ में अैल्युमिनियम जैसी कमजोर धातु के मामले में हमें, कास्ट आयरन/फौलाद से ज्यादा संवेदनशील रहना होता है।
2. समतलता बनाई रखने के लिए फिक्श्चर के डिजाइन संबंधि महत्वपूर्ण मुद्देकिसी भी फिक्श्चर में पुर्जा ठीक से लगाना हो, तो सटने के लिए तीन, स्थाननिर्धारण हेतु दो और दिशानिर्देश के लिए एक, इतने बिंदु जरूरी होते हैं। सुनिश्चित करें कि सटने के बिंदुओं के ठीक ऊपर क्लैंप दिए हुए हैं। अगर क्लैंप, सटने वाले बिंदुओं के ठीक ऊपर ना हो, तो क्लैंपिंग बल के कारण विरूपण आ सकता है। कभी कभी पुर्जे के डिजाइन के कारण उसके ठीक ऊपर क्लैंप करने की संकल्पना अपनाना संभव नहीं होता। ऐसी स्थिति में, फिक्श्चर डिजाइन करते समय ही क्लैंपिंग भार का वितरण संतुलित करना जरूरी होता है।
किसी पुर्जे के बड़े पृष्ठ का मिलिंग करना हो, तो उसे स्थिर बिंदुओं के बीच आधार देना जरूरी है, वरना यंत्रण भार के कारण विरूपण आ सकता है। इस विरूपण का कुछ हिस्सा स्थायी होने की वजह से घटिया समतलता प्राप्त होती है। जहाँ आधार देना है, वह संदर्भ पृष्ठ (यानि मिलिंग किए जाने वाले पृष्ठ का विरुद्ध पृष्ठ) अगर असमतल या ऊबड़खाबड़ हो, तो समायोज्य (अैडजस्टेबल) आधार इस्तेमाल करने होते हैं। जब पुर्जे को प्राथमिक स्थिर बिंदु पर फिक्श्चर में लगाया जाता है, तब यह आधार उनसे नीचे होते हैं। पुर्जे को प्राथमिक बिंदुओं पर क्लैंप करने के बाद यह गौण आधार, पुर्जे को छूने के लिए ऊपर लाए जाते हैं और उसी स्थिति में लॉक किए जाते हैं। यंत्रण के बाद पुर्जे को फिक्श्चर में से बाहर निकालते समय ध्यान रखना पड़ता है। इन सहारों को उनकी जगह से पीछे हटाया जाता है और वहीं लॉक किया जाता है। यह आधार यांत्रिक, न्यूमैटिक या हैड्रोलिक प्रकार में उपलब्ध होते हैं। पुर्जे के महत्व और टूलिंग खर्च की सीमा के अनुसार विकल्प चुना जा सकता है। यंत्रण के कारण आने वाले विरूपण को काबू में रखने में इन समायोज्य सहारों (चित्र क्र. 4) की परिणामकारकता की बहुत बड़ी भूमिका होती है।
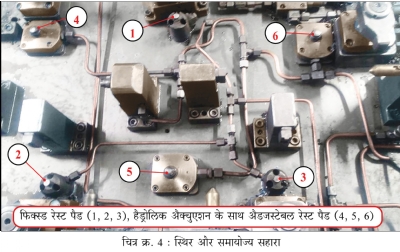
जब संदर्भ पृष्ठ को फिनिश कर के अच्छी तरह से समतल किया जाता है, तब हम समायोज्य आधारों की जगह 'स्थायी गौण रेस्टिंग पैड' देते हैं। यह पैड प्राथमिक रेस्टिंग पैड से 10 से 20 माइक्रोन निचले स्तर पर रखे जाते हैं। प्राथमिक रेस्टिंग पैड और क्लैंपिंग को बिल्कुल धक्का ना पहुंचाते हुए, यह पैड अस्थायी विरूपण क्षेत्र (इलैस्टिक डीफॉर्मेशन जोन) को आधार देते हैं।
3. क्लैंपिंग दबाव का चुनावऊपर बताए अनुसार फिक्श्चर में क्लैंपिंग करते समय पुर्जे में विरूपण आता है। इसमें कुछ विरूपण स्थायी होते हैं। इस वजह से जो पृष्ठ मिलिंग के बाद 'कार्यवस्तु क्लैंप की हुई स्थिति' के दौरान पूरी तरह से समतल होता है, वह 'कार्यवस्तु क्लैंप में से छूटने के बाद की स्थिति' के दौरान समतल नहीं रहता।
एक आसान जांच से यह सुनिश्चित किया जाता है कि पुर्जे में क्लैंपिंग के दौरान विरूपण आया है या नहीं। फिक्श्चर में क्लैंपिंग का दबाव बढ़ाते हुए मिलिंग करने के पृष्ठ पर एक डायल इंडिकेटर लगाएं। कोशिश करें कि डायल की सुई का विस्थापन, समतलता की सीमा के 20% से ज्यादा ना हो।
इस जांच के आधार पर क्लैंपिंग का दबाव तय करें। यांत्रिक फिक्श्चर हो, तो टॉर्क रेंच के इस्तेमाल से क्लैंपिंग नट कसें और उसका मूल्य तय करें।
मध्यम स्तर के यंत्रण पैरामीटर प्राप्त करने हेतु पर्याप्त दबाव देते समय अगर विरूपण टालना संभव ना हो, तो फिक्श्चर की डिजाइन पर फिर से ध्यान देना होगा और कुछ बदलाव करने पड़ेंगे।
4. मिलिंग कटर का चुनावसर्वश्रेष्ठ परिणाम चाहिए हो, तो जो पृष्ठ मिलिंग कर के समतल बनाना है, उसके लंबकोण में न्यूनतम यंत्रण भार देने वाले मिलिंग कटर का चुनाव करना चाहिए। सामान्य रूप से फेस मिल कटर (चित्र क्र. 5), एंड मिल कटर से अधिक भार पैदा करेगा। तथापि, फेस मिल कटर का प्रति नग टूल खर्चा कम हो सकता है। इस वजह से, इस बारे में पूरा सोच विचार कर के फैसला लेना हितकारी होता है। फिर भी, कोशिश करें कि फिनिशिंग के लिए इस्तेमाल किया जाने वाला कटर एंड मिल प्रकार का हो।
ऊपर दिए गए चारों मुद्दे देखते हुए, पहले प्रकार की घटिया समतलता का निराकरण किया जा सकता है।
अब हम समतलता की दूसरी स्थिति यानि मिलिंग किए हुए पृष्ठ पर दिखाई देने वाले उंच नीच हिस्सों पर ध्यान देते हैं। इसके लिए आगे दिए मुद्दों पर ध्यान देना जरूरी है।
1. मशीन के स्पिंडल की स्थितिअक्षीय बेरिंग में 'प्ले' होने के कारण ऐसी अनियमितताएं बन सकती हैं। इनकी जांच कर के उन्हें ठीक करना जरूरी है। स्पिंडल की खराब स्थिति के कारण बैक कटिंग हो सकता है, फलस्वरूप 'स्टेप्स' बन सकती हैं।
2. मशीन स्लाइड का घिसावअक्सर मिलिंग के काम में उंच नीच स्तर बनने की प्रमुख वजह होती है मशीन स्लाइड का घिसाव। कई बार जहाँ स्लाइड बहुत अधिक इस्तेमाल की जाती है, उस हिस्से में टर्साईट पट्टी का घिसाव होता है। मशीन की स्लाइड को चिकना बनाने वाली, टर्साइट यह सिंथेटिक पट्टी होती है। कार्यवस्तु के यंत्रण के दौरान, स्लाइड कम अधिक घिसाव वाले हिस्सों पर से घुमाई जाती है। ऐसे समय, कभी कभी स्लाइड काट की गहराई की दिशा में सरकती है, जिससे उंच नीच स्तर पैदा होते हैं। मशीन की अच्छी देखभाल और रखरखाव से ही इस समस्या का निराकरण होता है।
3. टूल के मार्ग के कारण अनियमित यंत्रण भारअगर टूल का मार्ग ऐसा हो कि उसके एक हिस्से में कटर का संपर्क क्षेत्र, दूसरे हिस्से से ज्यादा हो तो स्पिंडल पर पड़ने वाला अक्षीय भार कम ज्यादा हो कर अनियमितताएं पैदा होती हैं। मिसाल के लिए, 80 मिमी. व्यास का एक कटर, 120 मिमी. चौड़े X 300 मिमी. लंबे पृष्ठ का मिलिंग, लंबाई की दिशा में दो पास में करने हेतु इस्तेमाल किया गया है। पहले पास में टूल 70 मिमी., तो दूसरे पास में 50 मिमी. चौड़ाई की पट्टी का यंत्रण करता है। दोनों पास में अक्षीय अवरोध अलग अलग होगा और उसके कारण अक्षीय स्पिंडल विस्थापन भी भिन्न होगा। इसे टालने हेतु ऐसा रास्ता अपनाएं कि दोनों पास में संतुलित यंत्रण भार हो।
ऊपरलिखित विभिन्न स्थितियों में मिलिंग करते समय प्रक्रिया का नियंत्रण कर के समतलता सुनिश्चित करना संभव है।