प्रस्तुत लेख में हम ड्रिलिंग प्रक्रिया तथा उसके टूलिंगसंबंधि जानकारी लेंगे। ड्रिलिंग करते समय कौनसी गलतियां संभव हैं, उनका बोरिंग पर होने वाला असर तथा आम ड्रिलिंग करते समय आने वाली मुश्किलें आदि के बारे में हम इस लेख में जानेंगे।
ड्रिल (खास कर के इन्सर्ट या इंडेक्सेबल) डिजाइन करते समय निम्नलिखित प्राथमिक बातों को जांचना जरूरी होता है।
स्पिंडल
मशीन में 'थ्रू कूलंट स्पिंडल' है या सामान्य स्पिंडल है यह जांचना जरूरी है। अगर लंबाई एवं व्यास का अनुपात (L/D) 5 या उससे अधिक हो और मटीरीयल की टेन्साइल स्ट्रेंग्थ ज्यादा हो तो 'थ्रू कूलंट स्पिंडल' का इस्तेमाल जरूरी है। अैल्युमिनियम, कास्ट आयरन के यंत्रण के लिए थ्रू कूलंट स्पिंडल की आवश्यकता नहीं होती है। लेकिन स्टील, स्टेनलेस स्टील का यंत्रण करते समय थ्रू कूलंट स्पिंडल का उपयोग, यंत्रण की उत्पादकता बढ़ा सकता है तथा उत्पादन की लागत घटा सकता है।
ड्रिलिंग किए जाने वाले पृष्ठ का स्वरूप
इन्सर्ट प्रकार का ड्रिल डिजाइन करते समय, पुर्जे का पृष्ठ अवतल (कॉन्केव) है या उत्तल (कॉन्वेक्स) यह जांचना जरूरी होता है। ड्रिल के मुख पर केंद्र (सेंटर) में एक इन्सर्ट होता है तथा एक परिधीय (पेरिफेरल) इन्सर्ट (चित्र क्र. 1) होता है।
ड्रिलिंग के दौरान प्रथमतः केंद्र में स्थित इन्सर्ट का संपर्क पुर्जे से होना अपेक्षित है। इन्सर्ट का संपर्क पुर्जे से होने पर, उसका संदर्भ ले कर यंत्रण शुरु होता है। पृष्ठ उत्तल हो तो केंद्र का इन्सर्ट पहले संपर्क करता है लेकिन पृष्ठ अवतल हो तो यंत्रण के दौरान परिधीय इन्सर्ट प्रथम संपर्क में आता है। परिधीय इन्सर्ट का संपर्क पहले होने से टूल का अक्ष (अैक्सिस) सरकता है। अक्ष स्थानांतरित होने के कारण, यंत्रण शुरु होने से पहले ही, व्यास का विरूपण (डिस्टॉर्शन) होना संभव है। इससे अपेक्षित व्यास प्राप्त नहीं होता है। इन्सर्ट टूट जाते हैं। इसलिए यह पहले जांचना जरूरी है कि पुर्जे का पृष्ठ अवतल है या उत्तल। कास्टिंग प्रक्रिया से बनाई कार्यवस्तु में अगर छिद्र हो तो वहाँ कोर ड्रिल या फ्लैट सेंटर स्पॉट फेस किया जाता है।
मशीन की क्षमता
मशीन में अपेक्षित क्षमता की है या नहीं यह जांचना चाहिए। ड्रिलिंग के व्यास पर कई बातें निर्भर करती हैं। इंडेक्सेबल ड्रिल में, 12.5 मिमी. से अधिक व्यास के लिए इन्सर्ट प्रकार का ड्रिल इस्तेमाल किया जा सकता है। 12.3 मिमी. से कम व्यास का ड्रिल करना हो तो एच.एस. एस. या कार्बाइड स्टील के ड्रिल का उपयोग किया जाता है। 12.3 मिमी. से अधिक व्यास का ड्रिल इंडेक्सेबल टूल से करना हो तो, ड्रिल के व्यास के अनुसार पर्याप्त अश्वशक्ति(हॉर्सपावर HP) की मशीन चुनी जाती है। आगे दिए समीकरण से, मशीन की आवश्यक शक्ति पता कर सकते हैं।
जरूरी शक्ति की मशीन उपलब्ध न होने के मामले में, यंत्रण करते समय टूल एक गहराई तक पहुंचता है और अपर्याप्त शक्ति के कारण स्पिंडल रुकता है। इससे ड्रिल टूट सकता है। यंत्रण की जरूरत के मुताबिक, विविध स्पिंडल शक्ति वाली मशीन उपलब्ध हैं।
मटीरीयल
पुर्जे का मटीरीयल कौनसा है यह देखना भी महत्वपूर्ण होता है क्योंकि अगर अैल्युमिनियम पुर्जे का L/D अनुपात 5 से अधिक हो तो भी टूल उत्पादक वह जोखिम उठा सकते हैं, लेकिन स्टील पुर्जे का L/D अनुपात 5 से अधिक नहीं होना चाहिए। इससे आगे ड्रिल करने के लिए डैंप्ड अडैप्टर (चित्र क्र. 2) का प्रयोग करना पड़ता है। लेकिन डैंप्ड अडैप्टर में, स्पिंडल के अंदर से कूलंट देना संभव नहीं है।
टूल की रचना
स्टील बॉडी में बिठाए हमारे कार्बाइड इन्सर्ट तक शीतक 2 प्रकारों से पहुंचाया जाता है। डैंप्ड बोरिंग बार को शीतक नहीं दिया जा सकता। इस मुश्किल से बचने के लिए कार्बाइड रॉड पर 2 चौकोर खांचे (स्क्वेयर स्लॉट) बनाए जाते हैं। कार्बाइड रॉड के बाहर ड्रिल बॉडी होती है। बॉडी को पीछे से छिद्र कर के उसमें कार्बाइड रॉड ड़ाला जाता है। कार्बाइड रॉड के लिए सेंटर थ्रू कूलंट वाला स्टैंडर्ड कार्बाइड रॉड इस्तेमाल किया जाता है।
•इसमें बीचोबीच एक छिद्र होता है।
•इसका व्यास कम हो तो शीतक का बहाव भी घटता है। लीटर प्रति मिनट में गिने जाने वाले इस बहाव की मात्रा उचित होना जरूरी होता है।
•शीतक को इन्सर्ट के टिप तक पहुंचाना हो तो इस स्थान पर वायरकट या इ.डी.एम. प्रकिया से खांचा बनाया जाता है।
•खांचा बनाने के बाद शीतक केंद्र में नहीं रहता है। इससे शीतक का उचित बहाव प्राप्त होता है तथा थ्रू कूलंट का काम यथायोग्य होता है।
इसका उपयोग ड्रिलिंग में किया जाता है। साथ ही सेमीफिनिश तथा फिनिश बोरिंग में इस्तेमाल किया जाता है।
ड्रिलिंग को बोरिंग का प्रथम चरण माना जाता है। समतल पृष्ठ से हमें अगर 40 ± 0.02 माइक्रोन फिनिश बोरिंग करना हो, तो फिनिश बोर के लिए 0.5 मिमी. व्यास से अधिक अलाउन्स नहीं होनी चाहिए। इससे 39.5 मिमी. व्यास पर सेमीफिनिशिंग होना अपेक्षित है। मानिए कि 5 हॉर्सपावर क्षमता वाली मशीन पर 38 मिमी. का ड्रिलिंग करना है। मशीन की अपर्याप्त क्षमता के कारण 25 मिमी. का ही ड्रिल संभव है, तो पहले 25 मिमी. का ड्रिल करें, बाद में कोर ड्रिल का उपयोग करें। कोर ड्रिल के उपयोग से 38 मिमी. व्यास प्राप्त करें। सेमीफिनिशिंग करते समय वह व्यास 39.5 मिमी. करें। इसके बाद फिनिश बोर में आपको अपेक्षित व्यास प्राप्त होगा।
अपेक्षित उत्पादन
आउटपुट कितनी क्षमता से होना चाहिए यह भी महत्वपूर्ण होता है। उच्च पैरामीटर का उपयोग करना हो तो चिप के बहाव के बारे में सोचना पड़ता है। ड्रिल बनाते समय चिप के बहाव हेतु फ्लूट को सुपर फिनिश अर्थात बफिंग किया जाता है। फिर भी वें फ्लूट और फिनिश करने पड़ते हैं। जितना बेहतर फिनिशिंग होगा उतना चिप का वहन अच्छा होगा। चिप का वहन उचित न होने से यंत्रण पैरामीटर प्रभावित होते हैं। शीतक का दबाव कम से कम 16 बार होना जरूरी हैं। शीतक उचित दबाव से न आने पर चिप के वहन में मुश्किलें आती हैं।
टूल का चयन
इन्सर्ट का चयन भी एक महत्वपूर्ण निर्णय होता है। इन्सर्ट का चयन कार्यवस्तु के मटीरीयल पर निर्भर करता है। सिंगल ड्रिल के निर्देश, मल्टिस्पिंडल ड्रिलिंग या गैंग ड्रिलिंग के निर्देशों से अलग होते हैं। गैंग ड्रिलिंग तथा मल्टिस्पिंडल ड्रिलिंग के लिए इंडेक्सेबल ड्रिल का उपयोग नहीं किया जाता, क्योंकि मल्टिस्पिंडल के लिए ड्रिल का व्यास 12 मिमी. से कम होता है। एक समय पर एक से अधिक छिद्र करने हो तो उसके लिए बहुत ज्यादा शक्ति भी आवश्यक होती है।
इसके बारे में हम और गहराई से जानेंगे। इंडेक्सेबल ड्रिल (चित्र क्र. 3) तथा आम एच.एस.एस. या कार्बाइड ड्रिल (तालिका क्र. 1) का प्राथमिक वर्गीकरण यंत्रण गति पर निर्भर करता है। एच.एस.एस. में 12, 15, 20 मीटर/मिनट की यंत्रण गति प्राप्त होती है। एच.एस.एस. के M35, M42 इन प्रकारों में यंत्रण गति 15, 20, 25 प्रतिशत तक बढ़ेगी। कार्बाइड के उपयोग से भी 50 से 70 मीटर/मिनट तक की गति प्राप्त होती है। इंडेक्सेबल में यही गति 100 मीटर/मिनट से शुरु होती है। इस ड्रिल के लिए न्यूनतम 100 से अधिकतम 400 मीटर/मिनट की यंत्रण गति जरूरी होती है। यह ध्यान में रख कर मटीरीयल तथा अन्य बातों का उपयोग किया जाए तो यंत्रण समय (मशीनिंग टाइम) तिगुना-चौगुना कम हो सकता है। इस संदर्भ में मशीन की शक्ति उचित होना आवश्यक है।
इंडेक्सेबल ड्रिल में रीशार्पनिंग नहीं होता, केवल इन्सर्ट का इंडेक्सिंग किया जाता है। एच.एस.एस. का उपयोग करना हो तो टूल किट में अधिक संख्या में ड्रिल रखने होंगे। इनका रीशार्पनिंग नियत समय पर करना जरूरी होता है। इससे इन्वेंटरी बढ़ती है। लेकिन कार्बाइड ड्रिल में इसकी आवश्यकता नहीं होती, एक ड्रिल मशीन पर तो एक ड्रिल स्टॉक में होता है।
इंडेक्सेबल ड्रिल की जो किनारें मटीरीयल के संपर्क में आती हैं उन्हीं किनारों से यंत्रण होता है। सॉलिड कार्बाइड या एच.एस.एस. ड्रिल के फ्लूट की किनार विशेष तरीके से तैयार की जाती है। इंडेक्सेबल इन्सर्ट में सिर्फ पॉइंट से यंत्रण होता है। इंडेक्सेबल में 56 मिमी. व्यास तक 2 इन्सर्ट का उपयोग किया जाएगा। व्यास 56 मिमी. से अधिक होने पर 3 इन्सर्ट इस्तेमाल किए जा सकते हैं। इससे अधिक इन्सर्ट का उपयोग संभव नहीं है क्योंकि 56 मिमी. का ड्रिल करने हेतु पर्याप्त (70 HP) क्षमता की मशीन जरूरी होती है। जब 56 मिमी. से अधिक व्यास का काम होता है तब अधिकतर 3 इन्सर्ट इस्तेमाल किए जाते हैं। इस स्थिति में एक इन्सर्ट बीच में तथा दो इन्सर्ट परिधि पर (पेरीफेरल) होते हैं। 4 इन्सर्ट भी लगाए जा सकते हैं, लेकिन इसके लिए अन्य डिजाइन का इस्तेमाल किया जाता है। चूंकि 76 मिमी. व्यास के लिए अधिक मटीरीयल निकालना पड़ता है, टूल में केवल इन्सर्ट लगाने के बजाय कार्ट्रिज (चित्र क्र. 4) लगा सकते है।
इस प्रकार में कार्ट्रिज में इन्सर्ट बिठाए जाते हैं। सेंटर कटिंग में एक, बाजू में एक तथा पेरीफेरल में एक, ऐसे 3 कार्ट्रिज हो सकते हैं। मान लें इन्सर्ट खराब हुआ है, तो केवल कार्ट्रिज फेंकना पड़ता है, पूरी बॉडी बेकार नहीं जाती। अन्यथा, आम ड्रिल में इन्सर्ट खराब होने तथा टूटने पर ड्रिल का आकार बिगड़ता है। इस कारण पूरी बॉडी फेंकनी पड़ती है। अधिक व्यास के काम के लिए आम ड्रिल के बजाय कार्ट्रिज का उपयोग सुविधाजनक होता है।
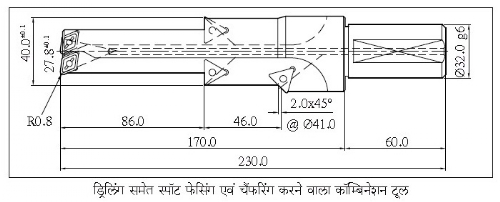
कार्ट्रिज से ड्रिल की बॉडी अमर्यादित समय तक चल सकती हैं। बॉडी की कठोरता (हार्डनेस) उचित होनी चाहिए, वह ज्यादा ही कठोर होने से टिप/यंत्रण बिंदु (कटिंग पॉइंट) पर भार (लोड) आता है। यह भार बॉडी पर प्रक्षेपित होता है। बॉडी पर भार आने से घिसाव होता है तथा पॉकेट विरूपित (डीफॉर्म) होते हैं। 2, 3 या 5 पुर्जों के बाद, आकार में बिल्कुल ही निरंतरता ना पाई जाने के कारण यंत्रण बंद करना पड़ता है। कठोरता 50 HRC से अधिक होने पर बॉडी अतिरिक्त भार सह नहीं सकती। इससे कंपन (वाइब्रेशन) तथा चैटर पैदा होते हैं। इसीलिए बॉडी की कठोरता 40-48 HRC के बीच होना जरूरी है। कठोरता 40 HRC से कम होने पर ड्रिल अधिक समय तक नहीं चलता। इसलिए N19, N24 अर्थात अलॉय स्टील मटीरीयल इस्तेमाल किया जाता है। N47 का भी इस्तेमाल किया जाता है, जो स्प्रिंग स्टील होता है। इसमें अल्प मात्रा में सिलिकॉन होने से यह स्प्रिंग जैसा लचीला होता है। मरोड़ने की क्षमता (टॉर्शन स्ट्रेंग्थ) भी बेहतर होती है। इसलिए घूमने वाले (रोटेटिंग) टूल के लिए N47 मटीरीयल का सुझाव दिया जाता है। कुछ मटीरीयल की कठोरता 40-44 HRC के बीच होती है। इसके लिए P20 मटीरीयल का इस्तेमाल करने पर P20 को 48 HRC तक कठोरता मिलती है। कठोरता जब 45 HRC से अधिक होती है तब इसकी यंत्रण क्षमता बहुत कम होती है। इस वजह से, हार्डनिंग के बाद ही पॉकेटिंग करना उचित होता है।
छोटे वर्कशॉप में इन्सर्ट का भी रीशार्पनिंग किया जाता है। ड्रिलिंग के लिए रीशार्पनिंग किए गए इन्सर्ट का उपयोग नहीं किया जाता क्योंकि रीशार्पनिंग करते समय उनकी ज्यामिती बनाई रखने पर ठीक से ध्यान नहीं दिया जाता। फलस्वरूप इन्सर्ट का आकार कम होता है, जिससे ऑफसेट कम होता है। रीशार्पनिंग होने के बाद इन्सर्ट की सेंटर हाइट की गारंटी नहीं रहती। इसलिए उसका ड्रिलिंग में इस्तेमाल नहीं किया जा सकता।
गिरीश फडके
संचालक, गौरव इंजीनीयर्स
9225641450
girish.phadke@gauravengineers.com
गिरीश फडके यांत्रिकी अभियंता हैं। आपने 6 साल टाटा मोटर्स में काम किया है। पिछले 26 सालों से आप औरंगाबाद स्थित गौरव इंजीनीयर्स के संचालक हैं।