सरफेस प्लेट, मापन संदर्भ उपकरण और मापनसंबंधि अन्य सहायक साधनों में इस्तेमाल करने हेतु ग्रेनाइट ( granite ) आदर्श माना जाता है। परिशुद्ध पृष्ठ नापने में संदर्भ के रूप में उपयोग करने के लिए ग्रेनाइट, स्टील या कास्ट आयरन से बेहतर होता है। ग्रेनाइट उत्पादों के विकसन में होने वाली चुनौतियां, ग्रेनाइट से बनाए मापन साधनों का इस्तेमाल तथा उनका रखरखाव आदि की जानकारी, मिसालों के साथ, इस लेख से पाई जाएगी।
ग्रेनाइट बेहद कठोर, स्फटिक जैसा, प्राकृतिक अग्निज पत्थर से बना होता है। इसमें मुख्य रूप से क्वार्टज और फेल्स्पार होते हैं। मापनशास्त्र (मेट्रोलॉजी) के कार्यों में इस पत्थर की कौनसी ग्रेड का इस्तेमाल करें यह निश्चित नहीं किया गया है। चूंकि यह पत्थर कई खनिज पदार्थों से युक्त होता है, यह विभिन्न रंगो में उपलब्ध होता है। इसका घनत्व भिन्न होने के कारण मापन कार्य में इस पत्थर की उपयुक्तता पर भी उसका असर होता है। काले रंग का पत्थर सबसे अच्छा माना जाता है लेकिन भूरे तथा हरे रंग के पत्थर भी बेहतर हो सकते हैं। इस्तेमाल करने से पहले काले रंग के अलावा अन्य पत्थरों का परीक्षण कर के उनके गुण जांचने पड़ते हैं। सरफेस प्लेट, प्रिजम जैसे मापन के संदर्भ उपकरण और मापन में सहायक होने वाले अन्य साधनों में ग्रेनाइट का इस्तेमाल आदर्श माना जाता है।
परिशुद्ध (प्रिसाइज) पृष्ठ मापन करने के संदर्भ में, स्टील या कास्ट आयरन से ग्रेनाइट बेहतर होता है। इसके कारण आगे दिए गए हैं।
· रासायनिक प्रतिरोधक शक्ति के कारण वह जंग नहीं पकड़ता या उसका घिसाव नहीं होता। इसलिए इसकी देखभाल करना आसान होता है।
· उष्मीय प्रसरण का गुणांक (हीट एक्स्पांशन कोइफिशंट) कम होने के कारण ग्रेनाइट विरूपित (वार्प) नहीं होता। ग्रेनाइट और कास्ट आयरन का रैखिक उष्मीय प्रसरण का गुणांक (CLTE)
काला : 2.2 K-1
हसन ग्रीन : 3.3 K-1
कास्ट आयरन : 10-12.5 K-1
· आयु लंबी होती है।
· पृष्ठ चिकना होने के कारण कार्यवस्तु का संचलन आसानी से होता है।
· गैर चुंबकीय (नॉन मैग्नेटिक)
· इसकी सरंध्रता (पोरोसिटी) कम (सिर्फ मापन श्रेणी में) है, इसलिए आसानी से इसका आकार नहीं बिगड़ता है या उस पर दाग नहीं पड़ते।
· इसका कंपन प्रतिरोध कास्ट आयरन से अधिक होता है।
· बेहतर अचूकता से फिनिश किया जा सकता है।
· इस्तेमाल करते समय अगर पृष्ठ पर खरोंच आए, तो प्रतिक्रियास्वरूप पुंज तैयार नहीं होते। स्टील पर खरोंच पड़ती है तो उस खरोंच की छोर का मटीरीयल बाहर धकेला जाता है और एक पुंज तैयार होता है। पुंज बड़ा हो तो स्टील प्लेट के पृष्ठ का दोबारा फिनिशिंग करना पड़ता है।
· ग्रेनाइट की बनावट में बड़े कण होते हैं जो सिर्फ टूट कर बाहर फेंके जाते हैं। इससे समतलता (फ्लैटनेस) पर कोई असर नहीं (कार्यवस्तु की तुलना में खरोंच का आकार छोटा हो तो) होता।
· इसकी कीमत कास्ट आयरन की कीमत से आधी होती है।
· कास्ट आयरन के इस्तेमाल में आकार एक प्रतिबंध हो सकता है, क्योंकि किसी भी काम के लिए कास्ट आयरन की ढ़लाई सफलतापूर्वक होने में आकार की और फिनिशिंग करते समय वित्तीय किफायत की मर्यादाएं होती हैं।
ग्रेनाइट उत्पादन के विकास में आई चुनौतियांपहले हमारे सारे मापन उपकरण कास्ट आयरन के थे। जैसे इस उद्योग के विकास के साथ अचूक पुर्जों की मांग बढ़ने लगी वैसे कास्ट आयरन का उष्मीय प्रसरण का गुणांक उच्च होने के नुकसान उभर कर दिखने लगे। ग्राहक को सटीकता चाहिए थी, इसलिए हमने ग्रेनाइट का इस्तेमाल शुरू किया। उच्च अचूकता वाली ग्रेनाइट सरफेस प्लेट, नियंत्रित तापमान में उपकरण और गेज के कैलिब्रेशन हेतु सबसे बेहतर होती है।
80 के दशक के आरंभ में विकसित देशों में ग्रेनाइट इस्तेमाल किया जाता था। ग्रेनाइट का उष्मीय प्रसरण का गुणांक कास्ट आयरन से कम होने के कारण वह एक स्थायी (स्टेबल) मटीरीयल था और उसकी लागत भी कम थी। विश्व में दक्षिण भारत के दख्खनी पहाड़ी मैदान (डेक्कन प्लेटू) से, उच्च दर्जे का ग्रेनाइट बड़ी मात्रा में मिल सकता है। गिंडी मशीन टूल्स लि. (GMT) ने एक खदान खरीदने का प्रबंध किया और होसूर में SIPCOT औद्योगिक संकुल में कारखाना स्थापित करने हेतु किराए पर जमीन भी ले ली।
खदानों से पत्थर निकालना एक अलग ही कहानी है। यह खदानें दुर्गम और पहाड़ी क्षेत्र में थी। वहाँ जंगली जानवरों और चोरों की तकलीफ थी। निकाला जाने वाला पत्थर मेट्रोलॉजी ग्रेड का है या नहीं, यह निश्चित करने हेतु हमारे कर्मचारियों को कच्चे पत्थर जांचने हेतु खदानों में जाना पड़ता था। सार्वजनिक परिवहन के अभाव में उन्हे कई मुश्किलों का सामना करना पड़ता था। कई बार उन्हें नजदीकी बस अड्डे से खदान तक की आखरी कुछ किलोमीटर की दूरी पैदल ही पार करनी होती थी। उसके बाद एक और समस्या खड़ी हुई। निर्माण उद्योगों के ग्रेनाइट मूल्य को ध्यान में रखते हुए राज्य सरकार ने सभी खदानों को अपने अधिकार में कर लिया, जिससे उपलब्धता अधिक मुश्किल हो गई।
80 के दशक के आरंभ में ग्रेनाइट काटने के लिए हथोड़े और लोहे की छिन्नी से ग्रेनाइट में कर्मी कई छिद्र करते थे और उनमें लकड़ी की पच्चर बिठा कर उस पर पानी ड़ालते थे। कुछ समय बाद लकड़ी फूलने से पत्थर टूटता था। विस्फोट से पंक्ति में छिद्र बनाने की तरकीब से भी खदान से पत्थर काटा जाता था। लेकिन इन पद्धतियों के कारण पत्थरों में अंदरूनी दरारें बनती थी जो फिनिशिंग के समय दिखाई देती थी। इसलिए इनसे बनी प्लेट अस्वीकार होती थी। यह एक बड़ी समस्या थी क्योंकि इसके कारण अंतिम कीमत भी बढ़ रही थी।
कई परीक्षणों के बाद हमने डाइमंड सॉ (हीरे की आरी) इस्तेमाल करने की ठानी। इससे पत्थरों में दरारें नहीं पड़ती और वह बेकार भी नहीं होता। बहुत गहराई में काम करना हो तब वायर कटिंग को प्राथमिकता दी जाती है।
ग्रेनाइट खरीदने के बाद उसे हाथों से लैप करने के लिए लैपिंग में कुशल कर्मियों की एक टीम तैयार करनी पड़ी। यह काफी तकलिफदेह और कड़ी मेहनत का काम है। प्लेट के पृष्ठ के लैपिंग में पूरा दिन निकल जाता था। प्लेट सूखने की प्रतीक्षा करनी पड़ती थी। हर पड़ाव पर, जांच करने से पहले पृष्ठ सामान्य तापमान पर होना चाहिए। संक्षेप में कहें तो इस काम में काफी मुश्किलें थी। आज लैपिंग मशीन के इस्तेमाल से 5 माइक्रोमीटर तक की समतलता पाई जा सकती है, लेकिन इससे अधिक अचूकता सिर्फ हाथों से मिल सकती है।
इस प्रकार, 'हाइ टेक' अैप्लिकेशन के लिए लगने वाले उच्चतम अचूकता के उत्पाद मानवीय हाथों से, 'नो टेक' प्राकृतिक शक्ति तथा संवेदनशीलता के उपयोग से विकसित किए गए।
विश्वसनीय परीक्षण प्रयोगशाला की स्थापना, हमारा अगला उद्देश्य था। ध्यान दें, यह सब 80 के दशक में हो रहा था। प्रयोगशाला के सभी अचूक साधन आयात करने पड़ते थे और आयात शुल्क 300% तक था। इससे हमारे बजट को गहरा धक्का लगा।
प्रिसिजन ग्रेनाइट उत्पाद बनाने के लिए खदान में अचूक पत्थर चुनने तथा उन्हें उचित तरह से काट कर बाहर निकालने से ले कर लैपिंग, ड्रिलिंग, इन्सर्ट बॉडिंग, पैकिंग और डिस्पैच करने तक कई समस्याएं थी। कई बार हमारे उत्पादों की जरूरत के अनुसार हमें मशीन बनवानी पड़ी। जैसे कि, शुरुआत में ग्रेनाइट में इन्सर्ट के लिए ड्रिलिंग करते समय हम रेडियल ड्रिलिंग मशीन का इस्तेमाल करते थे। कुछ दिनों बाद ग्राहकों ने थ्रेडेड इन्सर्ट में अधिक अचूकता की मांग की। ड्रिलिंग के लिए हम पानी का इस्तेमाल शीतक के रूप में करते थे। ऐसी मशीन आसानी से उपलब्ध नहीं थी। इसलिए हमने ग्रेनाइट गैंट्री की एक संरचना (चित्र क्र. 7) बनाई और उस पर एच.एम.टी. ड्रिलिंग हेड बिठाया। अब हम इन्सर्ट पर 50 माइक्रोमीटर पिच की अचूकता प्राप्त कर सकते हैं। मांग के अनुसार इससे भी अधिक अचूकता हासिल हो सकती है।
चमक और उससे पैदा होने वाली मापनसंबंधि समस्या से बचने के लिए प्रिसिजन ग्रेनाइट पृष्ठ कभी भी पॉलिश नहीं किया जाता।
अब हमारे पास ग्रेनाइट के कई स्रोत हैं। हर समय जब भी हम नई खदान का ग्रेनाइट इस्तेमाल करते हैं तब हम NABL मान्यताप्राप्त प्रयोगशाला में उसकी जांच करते हैं। तालिका क्र. 2 में प्रतिनिधिक परिणाम दर्शाए हैं।
मापन उपकरणों की जांचआयामी (डाइमेन्शनल) मेट्रोलॉजी उपकरण प्रमाणित करने हेतु कई यांत्रिकी तथा इलेक्ट्रॉनिक गेज हैं। शुरुआत के समय में हमने ऑप्टिकल गेज का भी इस्तेमाल किया था। जैसे, सीधापन स्ट्रेटनेस) प्रमाणित करने के लिए ऑटोकॉलीमीटर। ऐसी जांच करने वाला व्यक्ति कुशल होना आवश्यक होता है। 80 के दशक के उत्तरार्ध में समतलता के मापन हेतु इलेक्ट्रॉनिक लेवल उपकरणों का उपयोग आरंभ हुआ। उन्हें बिठाना और उनकी देखभाल करना हमारे लिए चुनौती से कम न था। क्योंकि उस समय भारत में कोई भी इस प्रकार के उपकरणों के बारे में ज्यादा नहीं जानता था। मैन्युअल जांच में, प्लेट के पृष्ठ पर पेन्सिल से चौखाने (ग्रिड) खींचने पड़ते थे। उनके हर हिस्से पर स्पिरिट लेवल ध्यान से सरका कर स्तरदर्शक तालिका (आलेख क्र. 1) हाथ से बनानी पड़ती है।
ग्राहक की जरूरतों को संबोधित करने में तकनीकी एवं व्यवसायिक (टेक्नो-कमर्शियल) चुनौतियां
मिसाल 1 हमने एक ग्राहक के लिए 12 मीटर लंबा T खांचा (स्लॉट) होने वाली, 12 मीटर X 1.5 मीटर आकार की एक प्लेट बनाई थी। T खांचे की सीधाई 150 माइक्रोमीटर/12 मीटर लंबाई पर देने का हमने वादा किया था। हम वो 80 माइक्रोमीटर में दे सके। T खांचे के इन्सर्ट के संरेखण के लिए संदर्भ पाने हेतु, प्लेट के उपरी पृष्ठ से 100 मिमी. की दूरी पर प्लेट की एक बाजू (साइड) पर एक और खांचा (चित्र क्र. 9) काटा। प्लेट की लंबाई पर इस 100 मिमी. पृष्ठ की सीधाई की अचूकता 30 माइक्रोमीटर/12 मीटर थी। T खांचे की अचूकता, 12 मीटर लंबाई पर 80 माइक्रोमीटर (चित्र क्र. 10) थी।
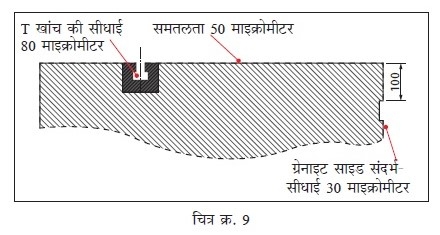
तीन बार प्रयास करने के बाद, इस आकार का एक पत्थर खदान के एक अच्छे कोटर से काटने में हमें सफलता मिली। खदान से 30 टन वजन की प्लेट कारखाने में लाना, अनलोड करना, उचित जगह पर रखना और विशेष विवरण के अनुसार (स्पेसिफिकेशन) फिनिश करना, इसमें हर मुद्दा एक आहवान था। इसके साथ ही, जांच प्रक्रिया के लिए प्लेट के आसपास हमें एक नियंत्रित परिवेश तैयार करना पड़ा। उसके बाद प्लेट को पैक तथा लोड कर के ट्रक पर चढ़ा कर ग्राहक तक पहुंचाना, अनलोड एवं अनपैक करना तथा उसका कार्यप्रदर्शन सिद्ध करना ये सभी चरण भी बेहद मुश्किल थे।
मिसाल 2 5 अक्षीय मशीन कैलिब्रेट करने के लिए सरफेस प्लेट
उंचे दर्जे की अचूकता होने वाले पुर्जों के उत्पादन में, बहु अक्षीय मशीन का इस्तेमाल बढ़ता जा रहा है। इन मशीनों को स्थिर तापमान के परिवेश में रखा जाता है। एक बार मशीन स्थापित करने पर उत्पादक मशीन पर 'जीरो सेटिंग' करते हैं। इस्तेमाल के बाद मशीन की जीरो सेटिंग दुबारा करने के लिए, उपयोगकर्ता को मशीन उत्पादक पर निर्भर रहना पड़ता है। क्योंकि 5 अक्षीय मशीन के कैलिब्रेशन करने हेतु कोई भी प्रयोगशाला फिलहाल सज्जित नहीं है। यह काफी महंगा पड़ता है। इसके अलावा, उन्हें उत्पादकों से सेवा की प्रतीक्षा करनी होती है, जिससे लागत और भी बढ़ जाती है। एक ग्राहक ने हमसे कैलिब्रेशन मास्टर (चित्र क्र. 12) विकसित करने की बिनती की और हम उसमें कामयाब रहे।
मिसाल 3ग्राहक की आवाज हम तक पहुंचने का सबसे अच्छा मार्ग होता है उनसे पाए गए प्रशंसा पत्र! मे. नैनोटॉम टेक्नोलॉजी प्रा. लि. बंगलुरु, हमारे ग्राहक हैं। इन्होंने नैनो मिलिंग मशीन के लिए हमसे ग्रेनाइट बेस और गैंट्री खरीदे थे। नैनोटॉम के सतीश कुमार कहते हैं, "ग्रेनाइट बेस तथा कॉलम की सख्तता (स्टिफनेस) हमारे ग्राहक की अपेक्षा के अनुसार थी, चुने गए ग्रेनाइट के गुण भी मानक के अनुसार थे। अमरीका के हमारे ग्राहक, ग्रेनाइट की सख्तता से बेहद संतुष्ट हैं।"
ढ़ांचे की आवश्यक सख्तता वाला ग्रेनाइट बेस और कॉलम मिलने के कारण ग्राहक खुश हुए।
ग्रेनाइट मापन उत्पादों का इस्तेमाल और निगरानी 1. इंस्टॉलेशन के दौरान प्लेट को उचित आधार दें। सरफेस प्लेट के संदर्भ में, लेवलिंग स्क्रू समेत एक स्टैंड दिया जाता है। सरफेस प्लेट को, प्लेट की छोर से लंबाई के 20% से कम दूरी पर 3 बिंदुओं पर आधार देना आदर्श माना जाता है। इनमें से दो आधार, प्लेट की लंबी बाजू से चौड़ाई के 20% से कम दूरी पर और बचा हुआ आधार मध्य भाग में होना चाहिए। उत्पादन के दौरान यहीं आधारबिंदु का उपयोग किया जाता है।
2. प्लेट के इस्तेमाल से पहले उसे, परिवेश के तापमान पर आने के लिए कम से कम आधे घंटे का समय दें। जैसे, टूल रूम में पूरे समय के लिए वातानुकूलन यंत्रणा शुरू रखना व्यावहारिक नहीं होता। उसे कई बार बंद करना पड़ता है। उसे शुरू करने पर प्लेट के पूरे क्रॉस सेक्शन में एकसमान स्थिर तापमान आना जरूरी होता है।
3. उत्पाद साफ रखें। दिन में कम से कम दो बार साबुन के पानी से पोछें। बेहतर परिणाम पाने हेतु, सफाई के बाद सूखने और आसपास के तापमान पर पहुंचने हेतु उसे पर्याप्त समय दें। मापन के लिए जरूरी वस्तुओं के अलावा, उत्पाद पर चाय की प्यालियां जैसी अन्य कोई भी वस्तु न रखें।
4. पृष्ठ की चिप निकलना, नुकसान दर्शाने वाली आम बात है। प्लेट इस्तेमाल में न हो तब उसका उपरी पृष्ठ ढ़क कर रखें। प्लेट के पृष्ठ की सुरक्षा हेतु, लकड़ी से बना आवरण GMT आपूर्त कर सकती है। आम तौर पर प्लेट के घिसाव का सबसे बड़ा कारण अपघर्षक धूल ही होता है।
5. अपनी प्लेट नियमित रूप से कैलिब्रेट करें। कैलिब्रेशन करने की अवधि, प्लेट की देखभाल और उसके इस्तेमाल पर निर्भर होती है। प्लेट स्थिर तापमान पर रखी गई हो, धूल और कूड़े से संरक्षित हो तो वह लंबे समय तक सेवा देगी।
6. कैलिब्रेशन, अैप्लिकेशन पर भी निर्भर होता है। सामान्यतः, साल में कम से कम एक बार उपकरणों को कैलिब्रेट करने का सुझाव हम देते हैं। कैलिब्रेशन करने के लिए ग्राहक अपने निर्माता से या NABL प्रमाणित प्रयोगशालाओं से संपर्क करें।
सहलेखक : वी. सेकर,
(जनरल मैनेजर, मेट्रोलॉजी विभाग, गिंडी मशीन टूल्स लि.)