ड्रिलिंग प्रक्रिया में, यंत्रण कर के कार्यवस्तु में छिद्र तैयार किए जाते हैं। लेकिन छिद्र की गहराई अधिक होने पर, चिप नियंत्रण और उन्हें दूर ले जाने की दृष्टि से उसमें कुछ अलग बातों की जरूरत होती है। कार्य के आधार पर ड्रिलिंग का वर्गीकरण किया जाता है, शॉर्ट होल ड्रिलिंग और डीप होल ड्रिलिंग।
जब लंबाई और व्यास का अनुपात (L/D) 5 से कम होता है, तब उसे शॉर्ट होल ड्रिलिंग कहते हैं। जब यह अनुपात 5 से अधिक होता है, तब उसे लाँग होल ड्रिलिंग कहते हैं। यहाँ L का अर्थ छिद्र की गहराई और D छिद्र का व्यास होता है।
ड्रिलिंग के दो तरीकें है। सॉलिड ड्रिलिंग अर्थात ठोस पदार्थ पर किया गया ड्रिलिंग और ट्रिपैनिंग अर्थात कोर छिद्र या कास्ट किए छिद्र का आकार बढ़ाने के लिए किया गया काम। दूसरा तरीका आम तौर पर बड़े छिद्र के लिए इस्तेमाल किया जाता है।
छिद्र का ड्रिलिंग करने के लिए विभिन्न प्रकार के ड्रिल उपयोग में लाए जाते हैं। • टेपर और स्ट्रेट शैंक ड्रिल
• 2 फ्ल्यूट, 3 फ्ल्यूट और 4 फ्ल्यूट वाले ड्रिल
प्रायः सॉलिड ड्रिलिंग के दौरान, पहली बार छिद्र बनाने के लिए 2 फ्ल्यूट वाले ड्रिल का इस्तेमाल किया जाता है। पहले से किए छिद्र को बड़ा करने या फिनिश करने के लिए 3 फ्ल्यूट और 4 फ्ल्यूट वाले ड्रिल का इस्तेमाल किया जाता है।
छिद्र का उचित आकार तैयार करने में और कुल कार्यप्रदर्शन में ड्रिल टूल की ज्यामिति (चित्र क्र. 1) का योगदान महत्वपूर्ण होता है। ड्रिल निर्माण के दौरान आगे बताए गए ज्यामितीय मापदंड़ों का विचार किया जाता है।
1. बिंदु कोण (पॉइंट अैंगल) मटीरीयल के अनुसार स्टैंडर्ड ड्रिल टूल में साधारणतः 90º से 150º ये कोण और पहले किए छिद्र का आकार पूरा करने के लिए 160º से 180º तक बिंदु कोण (चित्र क्र. 3) इस्तेमाल करते हैं।
2. हेलिक्स कोणहेलिक्स कोण कम (10º से 20º के श्रेणी में) होने से चिप बाहर निकालना आसान होता है। डीप होल ड्रिलिंग में कम कोण का इस्तेमाल होता है। शॉर्ट ड्रिल होल के काम में उच्च हेलिक्स कोण (30º से 40º तक) का उपयोग किया जाता है।
3. ड्रिल का टेपर उचित और असरदार ड्रिलिंग के लिए यह बेहद महत्वपूर्ण मापदंड़ है। रीग्राइंडिंग की संख्या इस पर निर्भर होती है।
उचित ड्रिलिंग पाने हेतु ड्रिल का चयन करते समय हमें आगे बताए मापदंड़ जानना जरूरी हैं
अ. छिद्र का व्यास और गहराई
आ. पुर्जे का आकार
इ. व्यास का अपेक्षित टॉलरन्स
ई. कार्यवस्तु का मटीरीयल
उ. मशीन की शक्ति और स्थिरता
परिमाणों का उचित चयन करते समय उपरोक्त मापदंड़ों का विवरण
अ. जब छिद्र का व्यास 12.5 मिमी. से कम होता है, तब हम सॉलिड कार्बाइड ड्रिल चुन सकते हैं। यह चयन मशीन की क्षमता पर भी निर्भर होता है। मशीन की क्षमता सीमित हो तो एच.एस.एस. ड्रिल का चयन करना होगा। चिप फंसने से बचने के लिए हमेशा आर पार शीतक प्रवाहित कर सकने वाले ड्रिल चुनने चाहिए। एकदम छोटे आकार के छिद्र के लिए, आर पार शीतक प्रणाली न होने वाले ड्रिल के अलावा कोई विकल्प नहीं होता। 12.5 से 40 मिमी. व्यास तक की श्रेणी के लिए हम इंडेक्सेबल ड्रिल का चयन कर सकते हैं। हमें यहाँ छिद्र की अचूकता पर विचार करना आवश्यक होता है। यहाँ अधिक यंत्रण गति और सरकन गति के उपयोग की गुंजाइश होती है। जब सटीक टॉलरन्स जरूरी होता है और छिद्र की गहराई अधिक (L/D>4) मात्रा में होती है तब इंडेक्सेबल ड्रिल उचित नहीं होता।
आ. झुके पृष्ठ या क्रॉस होल ड्रिलिंग वाले उत्तल/अवतल पृष्ठ के काम में इंडेक्सेबल ड्रिल को पहले पसंद किया जाता है। पृष्ठ के नमूने चित्र क्र. 2 में दिए हैं। ऐसे कामों में सरकन गति हमेशा 30% कम रखनी चाहिए। दूसरे छिद्र के अक्ष को छेदने वाले छिद्र का ड्रिलिंग करना हो तब ड्रिल एक अवतल पृष्ठ से बाहर निकल कर दूसरे अवतल पृष्ठ में प्रवेश करता है। ऐसे काम में चिप बाहर निकालने की समस्या हमेशा रहती है। चित्र क्र. 4 में दर्शाएनुसार दोनों दिशाओं से ड्रिलिंग कर के इस समस्या से बचा जा सकता है। पहले सेटअप में क्रॉस होल में छिद्र खुलने तक ड्रिलिंग किया जाता है। ड्रिल अवतल पृष्ठ में प्रवेश करते समय सरकन गति 20% से 30% तक कम करें। चित्र क्र. 2 में दूसरे सेटअप में दर्शाएनुसार हमें नीचे से ड्रिल करना होगा। मान लिजिए अगर एक काम में हमें अलग अलग आकार के छिद्र बनाने हैं, तो उसके लिए ड्रिलिंग प्रक्रिया चित्र क्र. 5 में दर्शाई है। पहले हमें एक बड़ा छिद्र करना होगा और उसके बाद कम सरकन गति पर अगला छोटा छिद्र बनाना होगा। दूसरी तरफ से, जरूरी गहराई तक तीसरा ड्रिल करना होगा। इस ड्रिलिंग में भी टूट-फूट, अंड़ाकार (ओवैलिटी) और गलत आकार के छिद्रों से बचने के लिए सरकन गति कम रखना आवश्यक है।
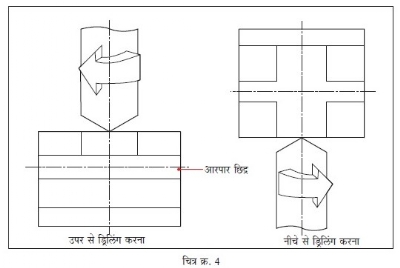
इ. 35 मिमी. से अधिक व्यास के बड़े छिद्रों के लिए हमें मशीन की क्षमता जांचना जरूरी है। ड्रिलिंग में अधिकतम कर्तन बल (कटिंग फोर्स) अक्षीय दिशा में होते हैं। थ्रस्ट लोड भी अधिक होता है। उसके लिए अधिक स्पिंडल उर्जा की आवश्यकता होती है। उच्च क्षमता की मशीन पर, इंडेक्सेबल ड्रिल के उपयोग से बड़े छिद्र करना मुमकिन है। चित्र क्र. 6 में टूल का फ्रंट व्यू दर्शाया है और उसमें अलग अलग प्लेन पर 4 इन्सर्ट बिठाए हैं। ये इन्सर्ट, ड्रिल पर विशिष्ट स्थान पर इस प्रकार बिठाए गए हैं कि उनका मटीरीयल में धीरे से प्रवेश हो कर, कर्तन भार कम होगा। ड्रिलिंग के लिए आवश्यक शक्ति का विश्लेषण करना हमेशा जरूरी होता है।
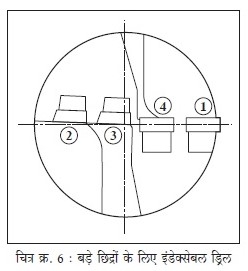
ई. काम की आवश्यकता के अनुसार ड्रिल का चयन कैसे करें, इसे तालिका क्र. 1 में दर्शाया है। ड्रिल की किसी विशिष्ट गहराई के लिए हम छिद्र के व्यास का टॉलरन्स किस मात्रा में प्राप्त कर सकते हैं, इसकी जानकारी इस तालिका से मिलती है। सीमित ड्रिल गहराई और छिद्र के टॉलरन्स हेतु इंडेक्सेबल या इन्सर्ट प्रकार के ड्रिल इस्तेमाल किए जाते हैं। जब ड्रिल की गहराई 5D से अधिक, 8D तक होती है, ऐसे काम में कर्तन भार सहने हेतु टूल का मटीरीयल पर्याप्त कठोर होना चाहिए। डीप होल ड्रिलिंग, ऑईल होल ऐसे कामों में आवश्यक गहराई के छिद्र करने हो, तो उसके लिए इस्तेमाल होने वाले टूल को गन ड्रिल कहा जाता है। ऐसे कामों में ड्रिल के अगले हिस्से पर ठोस कार्बाइड का टूल ब्रेजिंग कर के बिठाया होता है। इसमें सिंगल फ्ल्यूट होना जरूरी है। डीप होल ड्रिलिंग के काम में विशेष मशीन आवश्यक होती हैं।
वर्तमान प्रक्रिया की तुलना में, इंडेक्सेबल ड्रिल कितने किफायती होते हैं यह हम मिसाल के आधार पर समझ लेते हैं।
ड्रिलिंग के बाद हमें पता चलता है कि क्या छिद्रों के छोर नुकीलें हैं या वहाँ बर इकठ्ठा हुई है। इसके समाधान के लिए चैंफर किया जाता है या बर निकाली जाती है। टैपिंग जैसे अगले कामों के लिए चैंफर जरूरी होता है, या असेंब्ली के लिए भी वह उपयुक्त होता है।
इस स्थिति में ग्राहक चित्र क्र. 7 में दर्शाए काँबिनेशन टूलिंग का उपयोग करते हैं। चित्र में दर्शाए अनुसार कुछ उत्पादों में ड्रिलिंग के बाद फेसिंग, चैंफर जैसे काम आवश्यक होते हैं। चित्र क्र. 8 में दर्शाई कार्यवस्तु क्रैंकशाफ्ट है, जिसमें चैंफरिंग और स्पॉट फेसिंग जैसे काम हैं। काँबिनेशन टूल तीनों काम एक ही सेटअप में पूरा करते हैं। पहले ड्रिलिंग, उसके बाद चैंफर और अंत में स्पॉट फेस पूरा किया जाता है। ड्रिलिंग और चैंफरिंग के लिए उसी इन्सर्ट का उपयोग किया जाता है। स्पॉट फेसिंग के लिए अलग इन्सर्ट होता है। मापदंड़ों का विवरण तालिका क्र. 2 में दिया है।
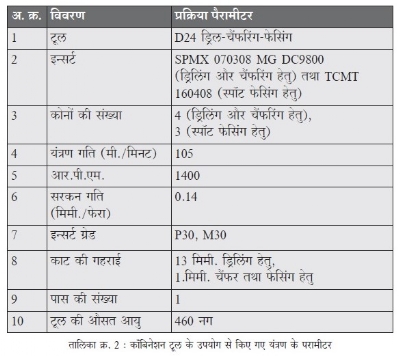
कई बार ग्राहक उनकी प्रक्रियाओं की लागत घटाने हेतु सस्ता टूलिंग इस्तेमाल करते हैं। लेकिन आम तौर पर उसका असर उनकी उत्पादनक्षमता पर होता है और बार बार टूल बदलने पड़ते हैं। बेहतर टूलिंग के अमल से कम लागत में उत्पादकता में सुधार करने हेतु हमें दीर्घावधि उपाय खोजने की जरूरत है। आगे एक मिसाल दी गई है, जिसमें एच.एस.एस. ड्रिल की जगह इंडेक्सेबल ड्रिल इस्तेमाल किया है। वर्तमान प्रक्रिया में कम मापदंड़ों पर एच.एस.एस. ड्रिल का उपयोग किया जाता था और टूल की आयु भी कम मिलती थी। यह ड्रिलिंग सी.एन.सी. लेथ मशीन पर शुरू था। नए और पुराने तरीकों के लिए प्रक्रिया के मापदंड़ों का विवरण तालिका क्र. 3 में दिया है।
पुर्जा : हैड्रोलिक पुर्जे की रिंग
ऑपरेशन : ड्रिलिंग
मटीरीयल : C45
(कठोरता 180 से 220 BHN)
मशीन : सी.एन.सी. लेथ
इंडेक्सेबल ड्रिल से प्रक्रिया करने पर ग्राहक को आगे दिए लाभ मिलें।
1. उत्पादकता में 100% से अधिक सुधार हुआ।
2. टूलिंग की लागत 87% से कम हुई।
3. आवर्तन समय कम (120 सेकंड से 30 सेकंड) हुआ।
4. छिद्र की गुणवत्ता में सुधार हुआ और निरंतरता बढ़ी।
प्रक्रिया में बदलाव करने से ग्राहक को अधिक लाभ मिले। अब शिफ्ट में, 200 पुर्जों की तुलना में 900 पुर्जें तैयार किए जाते हैं।