हमने पिछले अंक में, वुडरफ की-वे यंत्रण हेतु बनाई एस.पी.एम. के बारे में जानकारी ली। इन लेखों के माध्यम से एस.एम.इ.डी. के साथ
पोकायोके जैसी लीन मैन्युफैक्चरिंग तकनीक का इस्तेमाल कर के, एस.पी.एम. का अधिक किफायती उपयोग करने के बारे में भी हमने जाना। इस लेख में हम, एक आसान यंत्रण हेतु, विशेष तरकीबों के इस्तेमाल से बनाई एस.पी.एम. के बारे में जानकारी लेंगे।
इस एस.पी.एम. में प्रमुख रूप से 'ट्यूब पार्टिंग' का काम किया जाता है। आम तौर पर बाजार में उपलब्ध ट्यूब या पाइप के व्यास भिन्न होते हैं लेकिन उनकी लंबाई मानकीकृत (स्टैंडर्डाइज्ड) होने के कारण वह 4 मीटर या 6 मीटर होती है। चित्र क्र. 1 और 2 देखें। उचित यंत्रण पद्धति द्वारा ग्राहक को अपेक्षित लंबाई में उस ट्यूब को काटा जाता है।
चूंकि ट्यूब पार्टिंग काम में प्रत्यक्ष यंत्रण बेहद कम होता है, यह प्रक्रिया अन्य यंत्रण प्रक्रियाओं की तुलना में छोटी और आसान होती है। लेकिन अगर पूरे काम की योजना ठीक से न करें तो इस काम के कुल आवर्तन समय (साइकिल टाइम) में, प्रत्यक्ष यंत्रण समय की तुलना में, अन्य बातों में जाने वाला समय अधिक हो सकता है। साथ ही, गुणवत्ता में अपेक्षित परिणाम न पाए जाने के कारण नुकसान हो कर दोहरी हानि हो सकती है।
हमारे एक ग्राहक ने हमें ट्यूब पार्टिंग ऑपरेशन के लिए एक एस.पी.एम. बनाने का अनुरोध किया। इस ग्राहक के काम का स्वरूप, चित्र क्र. 3 और तालिका क्र. 1 में संक्षेप में प्रस्तुत किया गया है।
चित्र क्र. 3
तालिका क्र. 1
हम एस.पी.एम. डिजाइन करने में कुशल एवं अनुभवी हैं। हमारे सामने की चुनौतियां और उन पर किए गए उपाय आगे दिए हैं।
1. लोडिंग तथा अनलोडिंग का समय बचाने हेतु ट्यूब फीडर की रचना करना। इसमें प्रत्यक्ष यंत्रण किए जाने वाली जगह की तुलना में, ट्यूब फीडर के लिए आवश्यक जगह कई गुना अधिक होती है।
2. अचूक और निरंतर लंबाई काटने के लिए स्टॉपर का उचित स्थान तय करना।
3. कार्यवस्तु के घूमते समय, बीच के हिस्से में आने वाला जंपआउट कम करने की सुविधा करना।
4. विभिन्न व्यास की ट्यूब पकड़ने हेतु आसान तथा न्यूनतम समय लेने वाला प्रावधान करना।
5. ट्यूब की दीवार की मोटाई (वॉल थिकनेस) कम होने के कारण, अपेक्षित उत्पादकता पाने के लिए स्पीड, फीड और क्लैंपिंग दबाव (प्रेशर) का उचित संतुलन करना।
6. चूंकि हर मानकीकृत लंबी ट्यूब का अंतिम टुकड़ा बेकार हो जाता है, उसकी लंबाई कम से कम रखने का प्रावधान करना।
हमने उपर दिए सभी मुद्दों का गहरा अध्ययन किया और हर चुनौती पर ठोस विकल्प प्रस्तुत कर के एस.पी.एम. की समस्त संकल्पना, एक मॉडल (चित्र क्र. 4) के तौर पर साकार की।
आम तौर पर, बार पार्टिंग या ट्यूब पार्टिंग ऑपरेशन हेतु ऑटो फीडिंग रचना (चित्र क्र. 5) का प्रावधान जितना उचित तथा समन्वित हो, उस ऑपरेशन का आवर्तन समय घटाया जा सकता है। हमारी एस.पी.एम. की डिजाइन में हमने, मुख्य मशीन में, अचूक एवं सुलभता से अलाइन्मेंट करने वाली रचना देने की प्राथमिक जरूरत पूरी की। और साथ ही आगे दी गई नई विशेषताओं को प्रत्यक्ष साकार किया।
1. काटी हुई ट्यूब की लंबाई अचूक पाने के लिए बॉल स्क्रू की रचना
आम तौर पर इस प्रकार के पारंपरिक कामों में, काटी गई ट्यूब की लंबाई नियंत्रित करने हेतु स्पिंडल की अगली बाजू पर स्टॉपर की रचना की जाती थी। निवेश घटाने हेतु, डेड वेट की रचना कर के ट्यूब आगे सरकाने के लिए सुविधा की जाती थी। लेकिन इसमें स्पिंडल के अगले हिस्से में कार्यवस्तु, स्टॉपर, टूलपोस्ट, पार्टिंग होते समय निकलने वाले धातु की बर के छल्ले इकठ्ठा होने से भीड़ जम जाती थी और साथ में गुणवत्ता की अचूकता और निरंतरता में भी अपेक्षित परिणाम नहीं दिखाई देते थे। हमारे एस.पी.एम. ट्यूब फीडिंग मेकैनिजम पर
बॉल स्क्रू की व्यवस्था कर के उसका संचलन एक नियंत्रक (कंट्रोलर) से किया। इससे शुरुआत में ट्यूब चक में पकड़ी जाने पर, प्रोग्रैम द्वारा पार्टिंग की दूरी अचूकता से तय की जाने लगी। फलस्वरूप इसमें मेकैनिकल स्टॉपर की आवश्यकता नहीं रही।
2. कार्यवस्तु घूमते समय, बीच के हिस्से में आने वाला जंपआउट कम करने के लिए स्टेडी रेस्ट की रचना
कोई भी बेलनाकार कार्यवस्तु के आयाम असंगत अनुपात में (यानि व्यास कम और लंबाई अधिक) हो, तब उसे चक में कस कर तेजी से घुमाते समय उसका बीच का हिस्सा हिलता (जंप करता) हुआ दिखता है। इसे जंपआउट कहते हैं। इस स्थिति में कार्यवस्तु घूमती रख कर यंत्रण करने से कार्यवस्तु की गुणवत्ता घटती है। इसके साथ शोर होना या पृष्ठ पर घिसने से खरोच आना आदि दोष दिखाई देते हैं। ऐसे समय दुर्घटना की भी संभावना होती है।
हमने हमारे एस.पी.एम. पर स्वकेंद्रित हो सकने वाले पॉवर स्टेडी रेस्ट का प्रावधान किया। विभिन्न कार्यवस्तुओं पर लागू किए जाने वाले दबाव के कई विकल्प इससे उपलब्ध हुए। साथ ही, भिन्न कार्यवस्तुओं के व्यास के फर्क का सेटिंग बदलते समय आसानी हुई। इस रचना से उपर लिखी गई पहली तीन चुनौतियों पर उचित उपाय मिले।
ट्यूब बेलनाकार होने के कारण उसे कम से कम समय में सटीकता से समकेंद्री पकड़ना हो, तो स्प्रिंग कॉलेट के अलावा अन्य आसान विकल्प नहीं हो सकता। इसलिए हमने हेडस्टॉक का डिजाइन करते समय उसमें ग्राहक के उत्पादन की व्याप्ति (प्रॉडक्ट रेंज) के अनुसार विभिन्न कॉलेट के इस्तेमाल से (चित्र क्र. 6) ट्यूब पकड़ने की सुविधा की। इस प्रकार, चौथी चुनौती पर हमने उचित उपाय दिया।
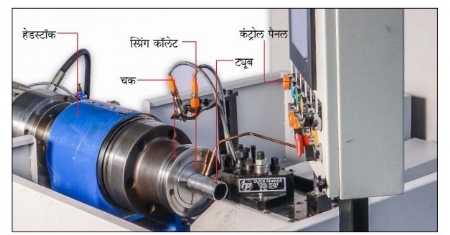
इस एस.पी.एम. पर की हुई ट्यूब फीडिंग की विशेष रचना के कारण, स्पिंडल के आगे स्टॉपर की आवश्यकता नहीं रही जिससे वहाँ अतिरिक्त जगह मिली। इससे बेहद संकीर्ण टूलपोस्ट पर संकीर्ण टूल बिठाने से कॉलेट के समीप ट्यूब पार्टिंग (चित्र क्र. 7) करना मुमकिन हुआ। इसका अप्रत्यक्ष लाभ यह है कि ट्यूब पर किसी भी प्रकार का विरूपण (डिस्टॉर्शन) नहीं हुआ और गुणवत्ता पर समझौता किए बिना एस.पी.एम. पर अधिक स्पीड, फीड (कटिंग पैरामीटर) का इस्तेमाल कर सके। उत्पादकता बढ़ाने में भी सफलता मिली। इस विशेषता से हमने पांचवी चुनौती पर मात की। इस प्रकार के यंत्रण में एक हानिकारक बात है, प्रत्येक बार या ट्यूब का बेकार होने वाला आखरी टुकड़ा (एंड पीस)। इस टुकड़े का इस्तेमाल स्वतंत्र यंत्रण कर के किया जा सकता है, लेकिन यह स्वचालित आवर्तन (ऑटो साइकिल) में न करते हुए मैन्युअली करना पड़ता है और इसे बनाने की लागत भी अधिक आती है जो किफायती नहीं होती। न्यूनतम लंबाई का टुकड़ा बचा रहने की व्यवस्था करना, यही एकमात्र लाभदायक मार्ग होता है। बेकार होने वाले टुकड़े की लंबाई, बार या ट्यूब पकड़ने की रचना पर निर्भर होती है।
एस.पी.एम. का डिजाइन करते समय ट्यूब फीडिंग की रचना में ट्यूब पकड़ने हेतु बेहद चुस्त (कॉम्पैक्ट) चक का चयन किया। इस चक को एक बेलनाकार एक्स्टेंशन पर बिठाया। हेडस्टॉक का डिजाइन करते समय उसका पिछला भाग, चक और एक्स्टेंशन से अधिक व्यास का एवं खोखला बनाया। ट्यूब के आखरी हिस्से के टुकड़े करते समय, चक समेत एक्स्टेंशन खोखली जगह में आसानी से जा सके (चित्र क्र. 8) ऐसी सुविधा की। इससे, पकड़ी गई ट्यूब का आखरी हिस्सा कॉलेट के एकदम समीप पहुंचने के कारण उसकी लंबाई कम रहती है और अल्प लंबाई का आखरी टुकड़ा शेष रहता है। ऐसा करने से ट्यूब का अधिकतम भाग इस्तेमाल होता है, जो फायदेमंद है। बेकार होने वाले टुकड़े की लंबाई अत्यधिक न होने के कारण, नुकसान कम होता है।
यह एस.पी.एम., सी.एन.सी. द्वारा नियंत्रित होने के कारण उस पर विभिन्न प्रोग्रैम बना कर मनचाही लंबाई की कार्यवस्तुएं आसानी से संचालित की जा सकती हैं। नई ट्यूब लगा कर आवर्तन आरंभ करने पर, शुरुआत में टूल और चक दोनों 'होम पोजिशन' पर जाते हैं। एक बार शुरुआती संदर्भ (रेफरन्स) लेने पर मशीन का नियंत्रक अगला काम करता है। इसमें मानवी कुशलता की आवश्यकता नहीं होती। पाठकों को आकलन में आसानी हो, इसलिए हमेशा की तरह इस एस.पी.एम. पर स्वचालित आवर्तन में किए एक प्रातिनिधिक यंत्रण का विडियो बनाया गया है। इसे देखने के लिए यहाँ दिए गए QR कोड को मोबाइल फोन पर स्कैन करें।
ऐसी कई नई विशेषताओं के साथ डिजाइन की हुई एस.पी.एम. (चित्र क्र. 9) का सफल परीक्षण, ग्राहक के प्रतिनिधी के सामने ही कर के वह ग्राहक के पास भेजा गया। इसी ग्राहक के पास हमारे और दो एस.पी.एम. कार्यरत हैं।
कीमत के मामले में, ग्राहक की आवश्यकता के अनुसार बनाई एस.पी.एम. की तुलना पारंपरिक यांत्रिक पद्धति की बार फीडिंग की रचना वाली ट्रॉब या तत्सम मशीन के साथ करें, तो ये एस.पी.एम. कई गुना (लगभग 4 से 7 गुना) अधिक महंगी होगी। लेकिन यह तुलना भ्रमकारी हो सकती है। क्योंकि शुरुआत में भले ही अधिक कीमत चुकानी पड़ती हो लेकिन हम दावे के साथ कहते हैं कि आने वाले समय में विभिन्न मानदंड़ों पर इससे मिलने वाले लाभ निश्चित रूप से कई गुना अधिक होंगे। इसलिए प्रति पुर्जा यंत्रण की लागत काफी कम होती है।
इस तुलना में मिलने वाले लाभों का वर्गीकरण, तालिका क्र. 2 में पाठकों की जानकारी के लिए संक्षेप में दिया गया है।
कई गुना मिलने वाले इन लाभों की गारंटी होने के कारण ही, हमारे ग्राहक ने पहले एस.पी.एम. के सफल कार्यप्रदर्शन पर और दो एस.पी.एम. की मांग की है।
9822031792
vivek.pitke@gmail.com
विवेक पिटके ने मेटलर्जी में डिप्लोमा करने के बाद अभियांत्रिकी की शिक्षा समाप्त कर के वर्ष 1990 में 'स्पेपरमैक' कंपनी की स्थापना की है। आपकी कंपनी में कैम मिलिंग, डोम ग्राइंडिग जैसे कई जटिल यंत्रण हेतु एस.पी.एम. निर्माण को प्राथमिकता दी जाती है।