जंग का प्रतिरोध और उष्मा का प्रतिरोध ये विशेषताएं पाने के लिए निकेल और क्रोमियम की उच्च मात्रा होने वाले मिश्रधातु विकसित किए गए। इनमें से अधिकांश मिश्रधातु, उष्णता प्रतिरोधक (हीट रेजिस्टंट) सुपर अलॉइ इस श्रेणी में होते हैं। इन्हें सामान्यतः HRSA इस संक्षिप्त नाम से जाना जाता है। HRSA के यंत्रण में आने वाली चुनौतियां, मशीन का चयन, यंत्रण हेतु आवश्यक कटिंग टूल आदि के बारे में विस्तारपूर्वक जानकारी देने वाला यह लेख।
पिछले शतक में तकनीक में आमूल बदलाव देखे गए। आज हमारे यहाँ खेती से विमान परियोजना (एरोस्पेस प्रोजेक्ट) तक नई तकनीक का इस्तेमाल बड़ी मात्रा में देखा जा सकता है। इस शतक में दो विश्वयुद्ध हुए, मानव चाँद पर पहुंचा और संगणक एवं संगणक विज्ञान का विकास आज के IoT और AI तक पहुंचा है। आज हम उत्पाद की विस्तृत श्रेणी और उनमें इस्तेमाल होने वाले, धातु तथा अधातु से बने विभिन्न पुर्जे देख सकते हैं।
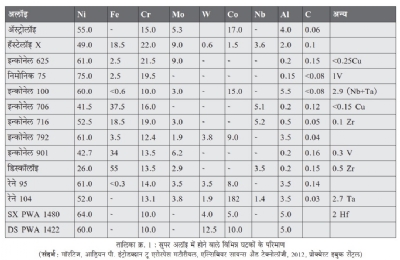
घटकों की मात्रा में थोड़े फर्क से बनाए गए, विभिन्न प्रकार के लोह तथा अलोह मिश्रधातुओं (तालिका क्र. 1) का इस्तेमाल किया जाने से उसके विभिन्न गुणों का बड़ा लाभ उत्पादकों को मिला है। इंजन के पुर्जे, चिकित्सा उपकरण, इंप्लांट तथा एरोस्पेस उपकरण आदि में भिन्न गुणों के मटीरीयल का इस्तेमाल करना पड़ता है। उष्मोपचार हेतु इस्तेमाल होने वाले यंत्र, बड़े टर्बो इंजन तथा एरोस्पेस में इस्तेमाल होने वाले पुर्जों के निर्माण में जंग प्रतिरोधक एवं उष्मा प्रतिरोधक गुणों से युक्त मटीरीयल की जरूरत बहुत पहले से ही थी। ऐसी जरूरतों को पूरा करने के लिए उच्च मात्रा में निकेल और क्रोमियम होने वाले मिश्रधातु विकसित किए गए। आगे चल कर निकेल, लोहा, कोबाल्ट, क्रोमियम के मिश्रण से 'सुपर अलॉइ' यह मिश्रधातु की श्रेणी विकसित हुई। इसमें उच्च तापमान पर भी बने रहने की शक्ति के साथ जंग प्रतिरोध के गुण थे। इसमें से कई सुपर अलॉइ उष्मा प्रतिरोधक (हीट रेजिस्टंट) श्रेणी में आते हैं। इन्हें सामान्यतः HRSA इस संक्षिप्त नाम से जाना जाता है। ये एरोस्पेस इंजन, गैस टर्बाइन, तेल एवं गैस उद्योग तथा मेडिकल इंप्लांट में इस्तेमाल होते हैं।
जेट इंजन बनाने में आवश्यक होने वाले मटीरीयल के कई गुण सुपर अलॉइ में होते हैं। जैसे कि उच्च तापमान में अपेक्षित शक्ति बनाई रखना, दरारें न पड़ने देना (फ्रैक्चर टफनेस), धीमे विरूपण (क्रीप) का तथा तनाव से टूटने (स्ट्रेस रप्चर) का प्रतिकार करना, दीर्घ फटीग आयु (तनाव पड़ना और तनाव से मुक्त हो जाना, इन आवर्तनों के कारण धातु में आई कमजोरी को फटीग कहते है।)। इसके अलावा, अन्य कई धातु उच्च तापमान में जंग और ज्वलन (ऑक्सिडेशन) से जल्दी कमजोर पड़ती हैं लेकिन सुपर अलॉइ उनका प्रतिकार करते हैं। सुपर अलॉइ 95º सें.-1300º सें. के तापमान में काम कर सकते हैं, इसलिए आधुनिक जेट इंजन में इस्तेमाल के लिए ये बेहद उचित मटीरीयल हैं।
HRSA के यंत्रण में चुनौतियां
HRSA मटीरीयल की यंत्रण क्षमता खराब होती है। उच्च तापमान में अपनी विशेषताएं बनाई रखने का सुपर अलॉइ का गुण ही, उनकी खराब यंत्रण क्षमता के लिए जिम्मेदार है। आमतौर पर स्टेनलेस स्टील से विकसित किए लोह, निकेल बेस सुपर अलॉइ का यंत्रण करने का काम, समान प्रकार के उष्मोपचार किए निकेल बेस तथा कोबाल्ट बेस सुपर अलॉइ का यंत्रण करने से आसान है। फिर भी, मुख्यतः लोहाधारित होने वाले अलॉइ के चिप टूटने में समस्या होती है, इसके लिए कई बार विशेष ज्यामिती वाले टूल की जरूरत होती है। निकेल बेस तथा कोबाल्ट बेस अलॉइ में इस प्रकार की कई समान विशेषताएं होती हैं, जिनसे यंत्रण की लागत बढ़ती है। सुपर अलॉइ के यंत्रण गुण आगे दिए घटकों पर निर्भर होते हैं।
• उच्च तापमान पर (जहाँ सामान्य टूल स्टील नरम पड़ने लगते हैं) शक्ति बनाई रखना।
• उच्च गतिज शियर स्ट्रेंग्थ के कारण यंत्रण करना मुश्किल होता है।
• माइक्रोस्ट्रक्चर में कठोर कार्बाइड होने के कारण उसमें अपघर्षक गुण होते हैं।
• धातु काटते समय घर्षण से उत्पन्न होने वाली उष्मा से कठोरता आती है।
• उष्मा का बेहतर निष्कासन नहीं होता, जिससे कटिंग टूल के अग्र पर तापमान बढ़ता है।
• धातु काटते समय कठोर, आरी जैसी अखंड़ चिप तैयार होती हैं।
• ऐसे धातुओं के यंत्रण हेतु अधिक शक्तिमान स्पिंडल की जरूरत होती है।
यंत्रण
इस प्रकार के मटीरीयल का यंत्रण टर्निंग, मिलिंग, ड्रिलिंग, बोरिंग, ग्राइंडिंग, ब्रोचिंग, हॉबिंग आदि पारंपरिक यंत्रण प्रक्रियाओं द्वारा किया जा सकता है। ऐसे मटीरीयल पर प्रक्रिया करने के लिए उचित सी.एन.सी. लेथ, सी.एन.सी. मशीनिंग सेंटर और अन्य मशीन उपलब्ध हैं।
यंत्रण में सामान्यतः आगे दिए गए तीन चरण होते हैं।
• रफ यंत्रण (इसमें अधिक मटीरीयल हटाया जाता है।)
• मध्यम चरण का यंत्रण (कई बार उष्मोपचार के बाद किया जाता है और इसमें वाजिब मटीरीयल निकाला जाता है।)
• फिनिशिंग (इसमें कम मटीरीयल निकाला जाता है।)
पारंपरिक पद्धति से ग्राइंडिंग जैसी प्रक्रिया द्वारा भी फिनिशिंग किया जा सकता है। लेकिन अब यह काम टर्निंग या मिलिंग द्वारा भी किया जा सकता है।
टर्निंग प्रक्रिया
पहले हम HRSA की टर्निंग प्रक्रिया पर चर्चा करते हैं। व्यास, फेस, खांचे आदि के यंत्रण हेतु लेथ पर टर्निंग प्रक्रिया की जाती है। टर्निंग के लिए आमतौर पर एक अग्र वाले (सिंगल पॉइंट) यंत्रण टूल का इस्तेमाल होता है। टर्निंग करते समय कार्यवस्तु, एक चक में पकड़ कर खुद के अक्ष पर गोल घुमाई जाती है। इस परिवलन के अक्ष को समानांतर या चौरस (टेपर हो तो कोण में) टूल को संचालित कर के व्यास या फेस का यंत्रण किया जाता है।
टर्निंग प्रक्रिया के नियंत्रक घटक
यंत्रण गति : यह गति मीटर प्रति मिनट में दी जाती है। कार्यवस्तु के फेरे की वास्तविक गति इससे मिलती है। यंत्रण गति 'V' चिन्ह से दर्शाई जाती है। (V= -- मी./मि.)
सरकन गति : टूल के इस संचलन को f चिन्ह से दर्शाया जाता है तथा उसे मिमी./फेरे में दिया जाता है। (f = -- मिमी./फेरा)
काट की गहराई : यह d चिन्ह से दर्शाई जाती है और मिमी. में प्रस्तुत की जाती है। (d = -- मिमी.)
धातु हटाने का दर :
टूल जब कार्यवस्तु से मटीरीयल निकालना शुरू करता है तब उसे शक्ति की जरूरत होती है। यंत्रण बिंदु पर की शक्ति Pc चिन्ह से दर्शाई जाती है। शक्ति का गणन HP या kW में किया जाता है (अश्वशक्ति या किलोवैट)।
यंत्रण टूल बिंदु पर जरूरी होने वाली शक्ति Pc, यह धातु निकालने का दर Q, शक्ति स्थिरांक Kp, शक्ति स्थिरांक हेतु सरकन गति (फीड) घटक C और टूल घिसाव घटक W पर निर्भर होता है। यंत्रण टूल बिंदु पर लगने वाली शक्ति
Pc = KpCQW
मशीन पर जरूरी होने वाली शक्ति, आमतौर पर Pm = Pc/E होती है। यहाँ E शक्ति पारेषण की कार्यक्षमता होती है जो मुख्य स्पिंडल मोटर और लेथ की वर्क स्पिंडल के बीच की ड्राइव यंत्ररचना पर निर्भर होती है।
ये सारे विवरण, HRSA के टर्निंग हेतु मशीन तथा टूल निश्चित करते समय बेहद महत्वपूर्ण होते हैं। इस मटीरीयल के लिए उच्च यंत्रण बल की जरूरत होती है। इसी प्रकार कार्यवस्तु पकड़ने के लिए इस्तेमाल होने वाले चक, कटिंग टूल तथा टूल पकड़ने हेतु बिठाए टूल होल्डर की संरचना भी मजबूत होना आवश्यक होता है। HRSA के यंत्रण में कटिंग टूल के लिए विशेष मटीरीयल का इस्तेमाल इष्ट होता है। साथ ही यंत्रण प्रक्रिया की किफायत और खास कर के टूल जैसी, नियमित इस्तेमाल होने वाली वस्तुओं की, लागत पर भी विचार करना चाहिए। ऐसे टूल का चयन करना जटिल होता है। आर्थिक रूप से टूल का किफायती होना, यंत्रण गति तथा सरकन गति पर आधारित होता है। तालिका क्र. 2 में दिए प्रारूप में प्रक्रिया के विभिन्न घटक, यंत्रण गति तथा सरकन गति के सहसंबंध दर्शाए हैं।
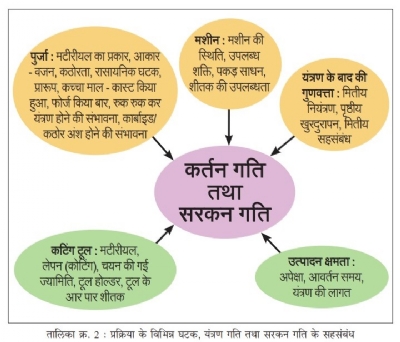
सुपर अलॉइ अपना अधिकतर सामर्थ्य यंत्रण के तापमान पर बनाए रखते हैं। इससे शियर जोन में अधिक उष्मा तैयार होती है तथा दी गई यंत्रण गति पर, अन्य धातुओं के मुकाबले इसमें टूल का घिसाव अधिक होता है। इसके अलावा सुपर अलॉइ काटने के लिए अधिक शक्ति की आवश्यकता होती है यानि मध्यम कार्बन अलॉइ स्टील के टर्निंग में काटने हेतु आवश्यक शक्ति से दोगुनी। इसके साथ टूल ज्यामिति, टूल का सामर्थ्य एवं/अथवा टूल होल्डर की मजबूती भी महत्वपूर्ण होती है।
HRSA मटीरीयल के यंत्रण हेतु उच्च यंत्रण पैरामीटर इस्तेमाल नहीं किए जा सकते लेकिन उच्च सरकन गति इस्तेमाल हो सकती है। विभिन्न यंत्रण प्रक्रियाओं के लिए आमतौर पर इस्तेमाल होने वाली यंत्रण गति की जानकारी तालिका क्र. 3 में दी है। फिर भी वास्तव में उपयोग किए जाने वाले यंत्रण पैरामीटर मटीरीयल की कठोरता, अंतिम गुणवत्ता की आवश्यकता, मशीन तथा टूल की अवस्था पर निर्भर होते हैं।
HRSA यंत्रण हेतु टर्निंग मशीन का चयन
किसी भी यंत्रण प्रक्रिया हेतु आवश्यक शक्ति, धातु हटाने के दर पर निर्भर होती है। यह दर मटीरीयल की कठोरता, यंत्रण क्षमता, यंत्रण गति, सरकन गति, काट की गहराई और टूल के छोर की स्थिति पर निर्भर होता है। ये सारी बातें HRSA यंत्रण के संदर्भ में प्रतिकूल है। इसलिए मशीन स्पिंडल में अधिक शक्ति होना बहुत जरूरी है और मशीन के स्लाइड, ड्राइव जैसे हिस्सों पर काफी तनाव पड़ने के कारण, उनका भी मजबूत तथा शक्तिमान होना जरूरी होता है। बड़े क्रॉस सेक्शन के टूल होल्डर और बहुत मजबूत बेस पर बिठाए, मजबूत कपलिंग वाले टरेट जरूरी होते हैं। मशीन स्पिंडल पर चक और फिक्श्चर जैसे पकड़ साधन भी मजबूत तथा पॉवर क्लैंपिंग व्यवस्था के साथ होने चाहिए। इसके अलावा, आवश्यक शक्ति मिलना सुनिश्चित करने हेतु कम गति पर ड्राइव मोटर की टॉर्क/गति विशेषताएं (चित्र क्र. 1) जांचना भी जरूरी है।
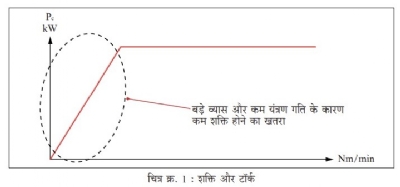
यंत्रण की जाने वाली कार्यवस्तु के आकार पर टर्निंग मशीन का आकार अवश्य निर्भर करता है। लेकिन टर्निंग मशीन का चयन करने से पहले उपरोक्त विशेषताओं का ध्यान से परीक्षण करना आवश्यक है। अब बाजार में सी.एन.सी. लेथ के कई प्रकार उपलब्ध हैं और हम अपनी जरूरत के हिसाब से चयन कर सकते हैं। शीतक की सुविधा होना कभी भी लाभदायक होता है। पिच की त्रुटि की भरपाई, तापमान भरपाई, टूल बदलने हेतु अलार्म आदि स्वयं सुधार सुविधाएं होने वाले सी.एन.सी. नियंत्रक, मशीन की अचूकता पर बेहतर नियंत्रण रख सकते हैं।
HRSA हेतु कटिंग टूल : ज्यामिति तथा मटीरीयल
सभी पारंपरिक टर्निंग टूल में, आमतौर पर यंत्रण के विभिन्न काम करने के लिए विशेष ज्यामिति होती है। जैसा कि ऊपर बताया गया है, टर्निंग टूल में प्रायः एक अग्र होता है, जिसकी ज्यामिति चित्र क्र. 2 में दर्शाई है। किसी भी टर्निंग टूल की मुख्य ज्यामिति में आगे बताई मूलभूत बातों का समावेश होता है।
रिलीफ कोण : एंड रिलीफ कोण और साइड रिलीफ कोण का प्रभाव, यंत्रण छोर के काम पर पड़ता है। रिलीफ कोण काफी बड़े हो, तो यंत्रण छोर कमजोर होती है और कठोर धातु काटते समय या रूक रूक कर (जिस यंत्रण में टूल कार्यवस्तु के निरंतर संपर्क में नहीं होता) किए यंत्रण जैसी, अधिक भार की स्थिति में छोर टूट सकती है। फिर भी बड़े रिलीफ कोण बेहतर पृष्ठीय फिनिश देते हैं। कठोर मटीरीयल काटते समय, कार्बाइड टूल के लिए 5º से 7º तक रिलीफ कोण होने चाहिए।
रेक कोण : ये कोण कार्यवस्तु के यंत्रण के दौरान बाहर निकलने वाली चिप को सरकने की दिशा देते हैं। रेक कोण +ve हो, तो टूल के फेस का झुकाव (इन्क्लिनेशन) यंत्रण छोर पतली करता है, या शून्य रेक कोण की तुलना में, अधिक तेज (शार्प) बनाता है। -ve रेक कोण, +ve रेक कोण की उल्टी दिशा में होता है और वह यंत्रण छोर मोटी एवं मजबूत बनाता है। उच्च +ve रेक कोण कम यंत्रण शक्ति देता है और यंत्रण छोर पर तापमान कम रखता है। -ve रेक कोण छोर मजबूत बनाता है लेकिन इससे अधिक यंत्रण शक्ति की जरूरत होती है जिससे यंत्रण छोर पर तापमान बढ़ता है।
साइड कटिंग एज और लीड कोण : ये कोण चिप पतली और लंबी होने में मदद करते हैं। यंत्रण छोर की आयु पर भी इसका प्रभाव होता है।
एंड कटिंग एज कोण : प्रोफाइल बनाते समय बड़े एंड कटिंग एज कोण की सिफारिश की जाती है। यह कोण यंत्रण छोर पर गड्ढे तैयार होने पर नियंत्रण
रखता है।
नोज त्रिज्या : टूल नोज, यह टूल का बेहद महत्वपूर्ण हिस्सा है। क्योंकि टूल के इसी भाग से वास्तव में कार्यवस्तु का पृष्ठ काटा जाता है। यंत्रण के बाद मिलने वाला पृष्ठीय फिनिश और टूल आयु, नोज त्रिज्या से निर्धारित होते हैं। टूल नोज की त्रिज्या बड़ी होना हमेशा बेहतर माना जाता है क्योंकि इससे अधिक अच्छी टूल आयु अथवा उच्च यंत्रण गति मिलती है। फिर भी पृष्ठीय फिनिश, मशीन पर उपलब्ध शक्ति जैसी अन्य बातों पर गौर करना भी जरूरी है।
HRSA हेतु कटिंग टूल
अन्य लोहयुक्त और अलोह मटीरीयल के यंत्रण हेतु इस्तेमाल किए टूल और तकनीक की वजह से HRSA का यंत्रण करते समय यंत्रण क्षमता के संदर्भ में टूल आयु, प्रक्रिया को लगने वाला समय, विश्वसनीयता, पुर्जों की गुणवत्ता जैसी समस्याएं पैदा हो सकती हैं।
पिछले कई वर्षों में HRSA का यंत्रण करने हेतु नए नए टूल विकसित किए गए। ये टूल पारंपरिक टूल के मुकाबले लाभदायक होते हैं। इन्हें भिन्न मटीरीयल से बनाया जाता है। टर्निंग के काफी सारे काम आसानी से करने के लिए इसमें कई प्रकार की ज्यामिति दी जाती है।
HRSA जैसे कठोर मटीरीयल का यंत्रण करने वाले टूल, उससे अधिक कठोर मटीरीयल से बनाए जाने चाहिए और धातु काटने की मुश्किल स्थिति में वे आसानी से टिके रहने चाहिए। ऐसे कठोर मटीरीयल हैं सिरैमिक और हीरा (डाइमंड)। सिरैमिक टूल तथा हीरों की, पॉलीक्रिस्टलाइन हीरे और क्युबिक बोरॉन डाइमंड टूल की एक विस्तृत श्रेणी HRSA के यंत्रण हेतु अब उपलब्ध है।
ऐसे टूल के उपयोग से हमें कई उच्च यंत्रण पैरामीटर पर इच्छित यंत्रण शक्ति मिलती है। कार्बाइड श्रेणी, लेपन (कोटिंग) तथा ज्यामिति के उचित उपयोग से, HRSA यंत्रण में इष्टतम उत्पादकता प्राप्त करने के लिए इस टूल को विकसित किया गया है। यंत्रण के विशेष काम के लिए उचित बदलाव किए गए सिरैमिक टूल भी अब विभिन्न प्रकार में उपलब्ध हैं। विभिन्न ज्यामिति के सिरैमिक इन्सर्ट भी उपलब्ध हैं। इनमें ऑक्साइड सिरैमिक, ऑक्साइड/कार्बाइड सिरैमिक, सिलिकॉन नाइट्राइड बेस और विस्कर रीइनफोर्स किए सिरैमिक हैं। इसमें हमारे बालों जितने पतले तंतु (विस्कर) होते हैं जिनसे बेहद कठिन स्थिति में टूल की आयु में सुधार आता है।
आजकल विभिन्न आकार के पॉलिक्रिस्टलाइन सिंथेटिक डाइमंड (PCD) तथा क्युबिक बोरॉन नाइट्राइड (CBN) जैसे मूलतः कृत्रिम हीरे, कार्बाइड इन्सर्ट पर बिठाए (एंबेड किए) जाते हैं। इस टूल के इस्तेमाल से उच्च यंत्रण पैरामीटर पर यंत्रण किया जा सकता है। पहले ये महंगा लगता है लेकिन HRSA यंत्रण के लिए किफायती होता है।
शीतक (कूलंट)
HRSA मटीरीयल यंत्रण के लिए कठोर होता है। अन्य हर यंत्रण प्रक्रिया के समान, यंत्रण के दौरान शीतक का उपयोग यंत्रण के लिए सुलभ हो सकता है। कटिंग टूल के छोर के घिसाव से बचाने के लिए शीतक से पर्याप्त स्नेहन मिलता है और यंत्रण के दौरान पैदा हुई उष्मा कम करने में मदद होती है। कर्तन बिंदु पर, पानी पर आधारित शीतक बड़ी मात्रा में बहाना आवश्यक होता है। शीतक के कई प्रकार उपलब्ध हैं। HRSA का प्रकार तथा मशीन के अनुसार इसका चयन किया जाता है। कर्तन बिंदु पर शीतक की आपूर्ति आश्वस्त करने हेतु थ्रू कूलंट टूल होल्डर का इस्तेमाल होता है। पानी में घुलने वाले ऑईल, पानी पर आधारित रासायनिक इमल्शन, सल्फर युक्त या क्लोरिन युक्त कटिंग ऑईल आदि विभिन्न प्रकार के शीतक उपलब्ध हैं। यंत्रण के दौरान शीतक का उपयोग किया हो, तो पुर्जे पर उष्मोपचार करने से पहले वह पूरी तरह से साफ है यह सुनिश्चित करें।